CUSTOMER LOGIN
How to choose the right CNC tool for the job/material
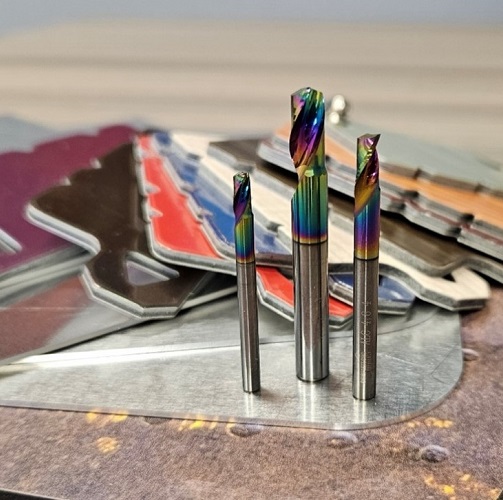
How to choose the right CNC tool for the job/material
PUBLISHED by EYE ON DESIGN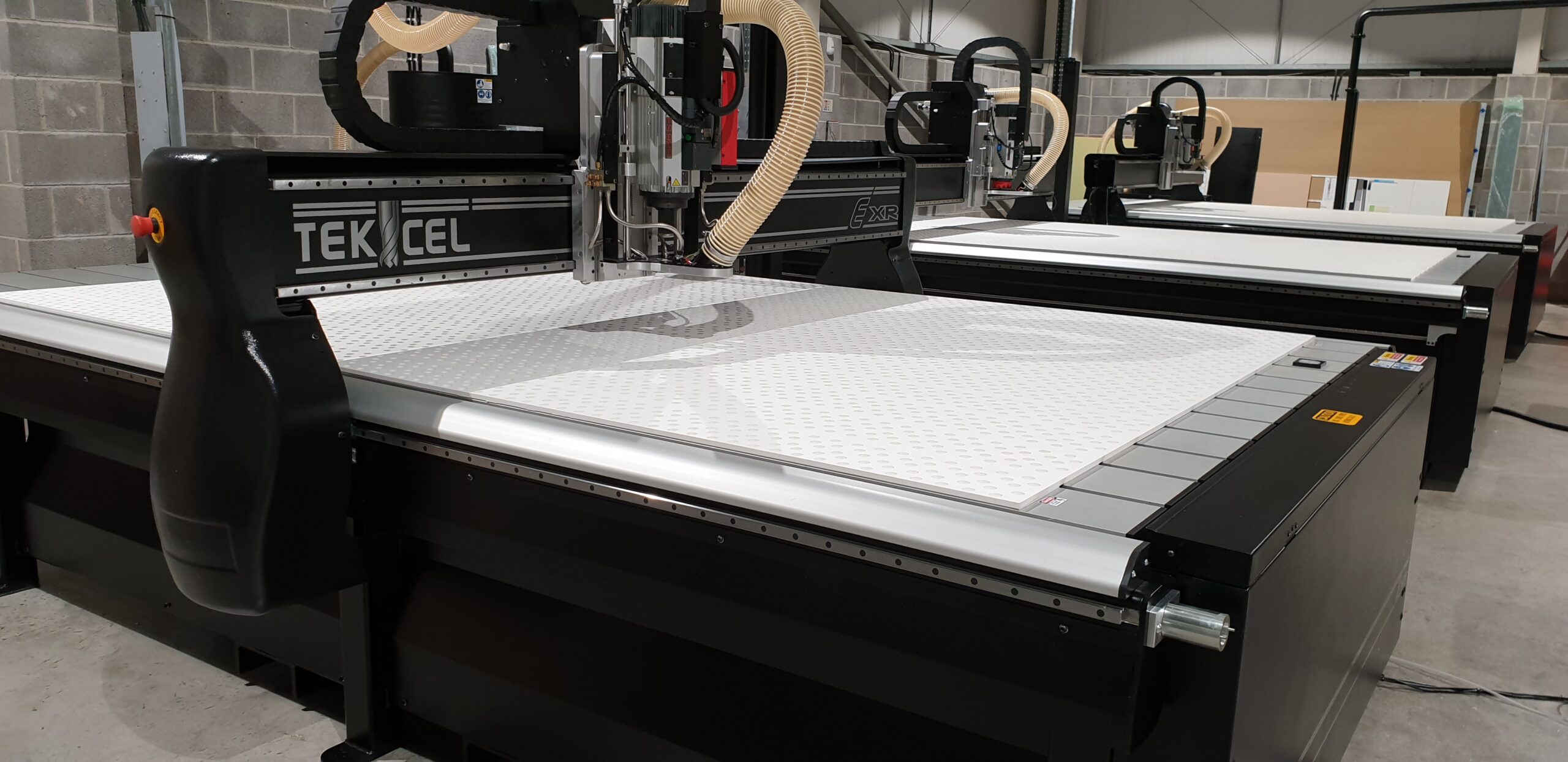
Evolving & adapting over many years, the Sign and Display industry now covers a vast spectrum of services, products & applications. These include internal & external shop signage, Point of Sale & Graphic Display, Exhibition Stand Build, Shopfitting & Joinery, Print Finishing & Packaging, Film & TV Prop Making to name just a few.
Each project usually comes with its own set of unique requirements and specifications, from material choice, application, cutting techniques and inevitably tight deadlines. As a leading supplier for many years of Tekcel CNC Routers & CNC Router tooling, Complete CNC Solutions Ltd fully understand customers cutting needs & requirements when using the most common & demanding materials for sign & display CNC work.
Typical materials range from Plastics & Acrylics, rigid Foam PVC’s, Recycled boards, Aluminium Composite Material (ACM), Aluminium, Brass & Copper, MDF, Plywood, Hard & Soft Woods, Cards and Display boards to really any CNC machinable materials on the market today.
At Complete CNC Solutions Ltd, we recognise the importance of getting the best performance, production & yield from your CNC Router, so choosing the correct CNC tooling in your machine is paramount in achieving the right edge quality, performance and longevity whilst producing the desired results for eye-catching and dynamic signage & display applications.
Whatever your application, having the right CNC tooling, properly specified and well made from the finest micro carbide tooling material is crucial, so here’s a few pointers to help make the right choice.
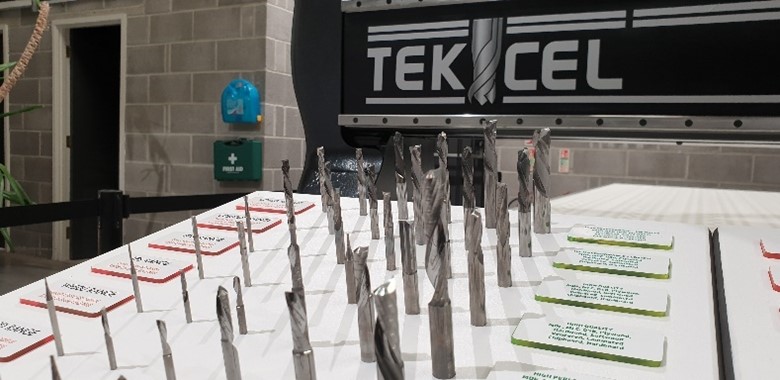
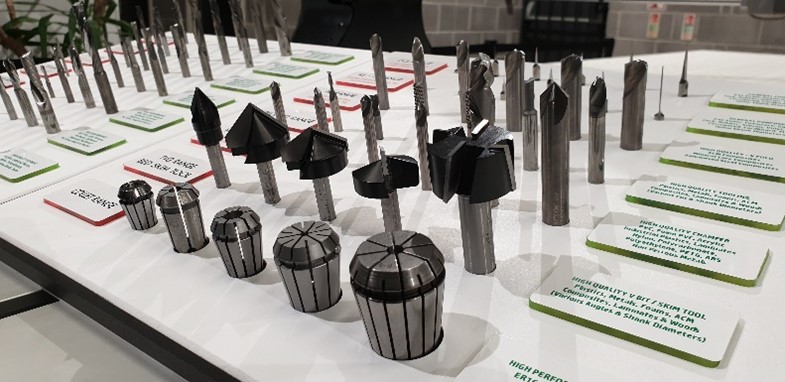
Plastics & Acrylics:
We would always recommend that single flute up spiral cutters are used on this style material. One cutting side offers less friction during the tool’s full rotation, creating a cleaner, smoother chip removal and therefore cleaner edge finish cut. There are many different diameters & cut lengths to choose from and different styles for the optimum edge quality too. Cutting in multiple passes is always advised when machining thicker material.
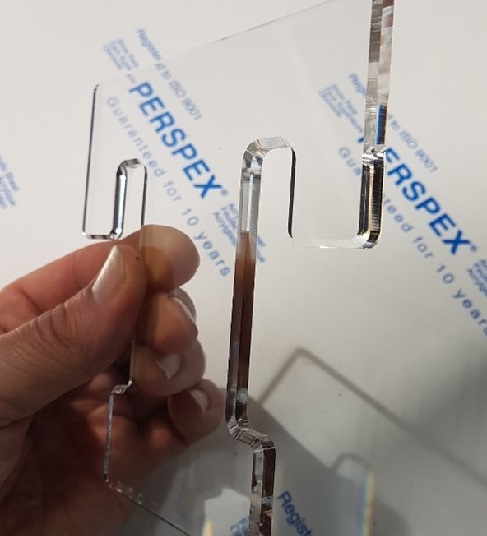
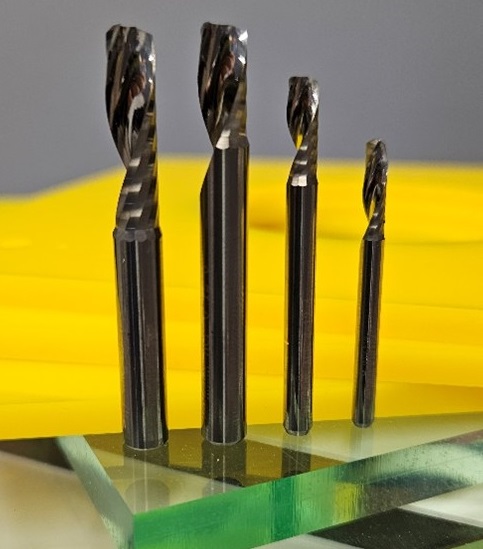
Rigid PVC’s Foam:
We would always recommend that single flute up spiral cutters are used on this style material from 5mm thickness and above. Thicknesses below 5mm thick are usually best cut with a twin flute up spiral style cutter, as the thinner materials sometimes needs more cutting to produce a better edge. Again, there are many different diameters & cut lengths to choose from and different styles for the optimum edge quality too. Cutting in multiple passes is always advised when machining thicker PVC material, so as to remove the swarf more easily.
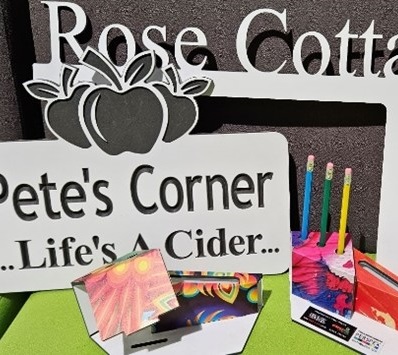
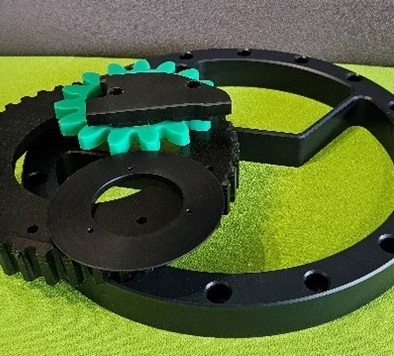
Aluminium Composite material (ACM) :
We would always recommend that single flute up spiral cutters are used to cut this style material. 3mm, 4mm or 6mm diameter and again with a shorter cut length is advised. For the best cut quality, experiment with direction of cut to check the edge finish (clockwise or counter clockwise) Although some aluminium can be cut dry, to get the best tool life, we would always recommend cutting this material wet, using a dedicated mist coolant fluid system.
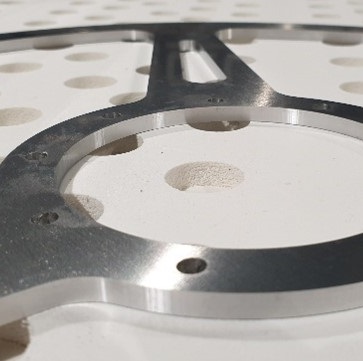
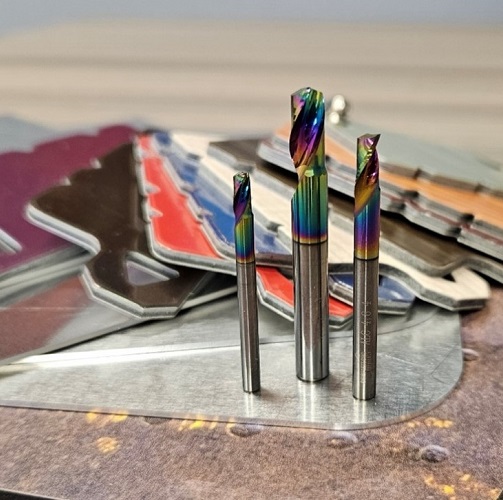
MDF, Ply & Woods :
Compression Cutter which offer both up-cut and down-cut capabilities within the same tool are perfect for achieving chip & burr-free top and bottom finishes. Used on all wood product sheet materials, especially those that can splinter easily on the surfaces. Available in many diameters and supplied with a non or heat resistant coating, Melamine-faced, MDF, Plywood, Hard and Soft woods are all machined to perfection using our CC800 Compression cutter range. Ask for cutting advice & techniques for these tools and we’ll be happy to help.
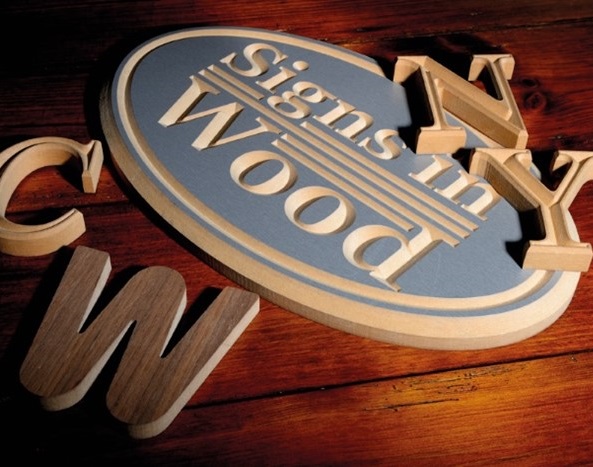
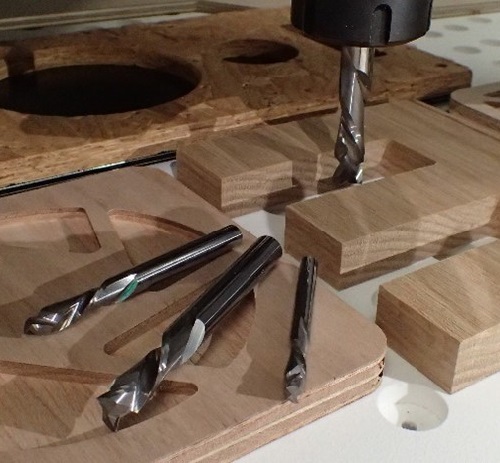
Folded Sign Tray Fabrication :
In the world of Sign makers, this is a very common product manufactured on a CNC Router on a daily basis in Sign shops. Produced by creating groove or fold lines in ACM, using a dedicated folding tool with 45 degree angle cutting sides with a 3mm flat tip, to create the perfect 45 degree angle folds
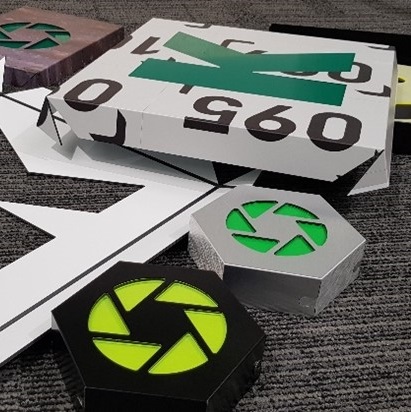
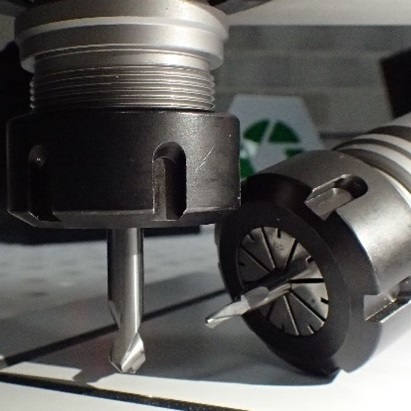
Important Factors & Guidelines to Consider When Choosing CNC Router Tools and to maximise the efficiency of your CNC router, keep these key points in mind:
Your CNC Tooling Supplier: Making the right choice of CNC Tooling supplier is the most important decision you need to make. There are many CNC tooling suppliers out there, but not all are the same. Here at Complete CNC, we actually use, test & trial all our CNC tooling ranges on all our in-house Tekcel CNC Routing machines, so as we can offer the very best advice and knowledge to all CNC customers. We have over 30 years of experience in CNC tooling & cutting, so any CNC tooling supplier who doesn’t use, own or fully understand CNC machines, shouldn’t sell you tooling. Please ask us for advice and recommendations for all CNC tooling and material machining applications and we’ll endeavour to help you get the best out of your CNC system.
Choice of Tool: Your correct choice of tooling geometry, style and profile will solely depend on the material you’re working with, giving you the best & most efficient edge quality and overall look & feel of the finished product. Please ask us for advice and recommendations as we have many years of tooling application and CNC cutting experience under our belts.
Feed and Speed Rates: Using the correct and recommended feeds & speeds along with the correct RPM for your spindle motor will enhance the performance and extend the lifespan of your CNC Tooling. Ask us for recommendations and advice anytime.
Never Cross Pollinate Tooling: Always use the recommended CNC Tooling for that specific type of material. Cutting say aluminium first and then using the same tool to cut acrylic is very bad practice. It will cut both, but the edge quality will suffer, so keep CNC tooling specific to material types and therefore never cross pollinate your tools
Collets: Probably just as important as your tool itself and very often over looked and neglected. Your collet plays a massively important role when getting the best performance and life out of your CNC Tooling. If it’s old & worn, it won’t clamp around the tool properly to hold it steady and therefore could get dragged out and damage your materials and even you CNC router table. Regularly check and replace your collets ever 3 to 4 months. View Collets.
Coolant and Lubrication: When working with metal materials like aluminium, copper, brass and even stainless steel on Tekcel CNC Routers, heat will be generated during the cutting process, so using dedicated and recommended cutting coolant is essential for stress free cutting, great edge quality and prolonged tooling life. View Coolant.
Quality Over Cost: Recognising the importance of using premium CNC router tooling by investing in quality product lines really does pay off. All our tooling is crafted from the best micro grain solid carbide to our specification, providing fully balanced tooling, giving the optimum longevity and professional results, every time. Choosing the appropriate CNC tool bit is paramount, as an ill-suited tool can lead to subpar edge finishes and potential distortion of the part, resulting in the need for additional material, unwanted mistakes & wasted time—time that equates to money in the world of expensive materials and precision cutting.
Together, we can help your business thrive in the signage and display industry, so contact us now and see how we can move your business forward.
Further Blog Posts
Is Your CNC Router Holding Your Business Back?
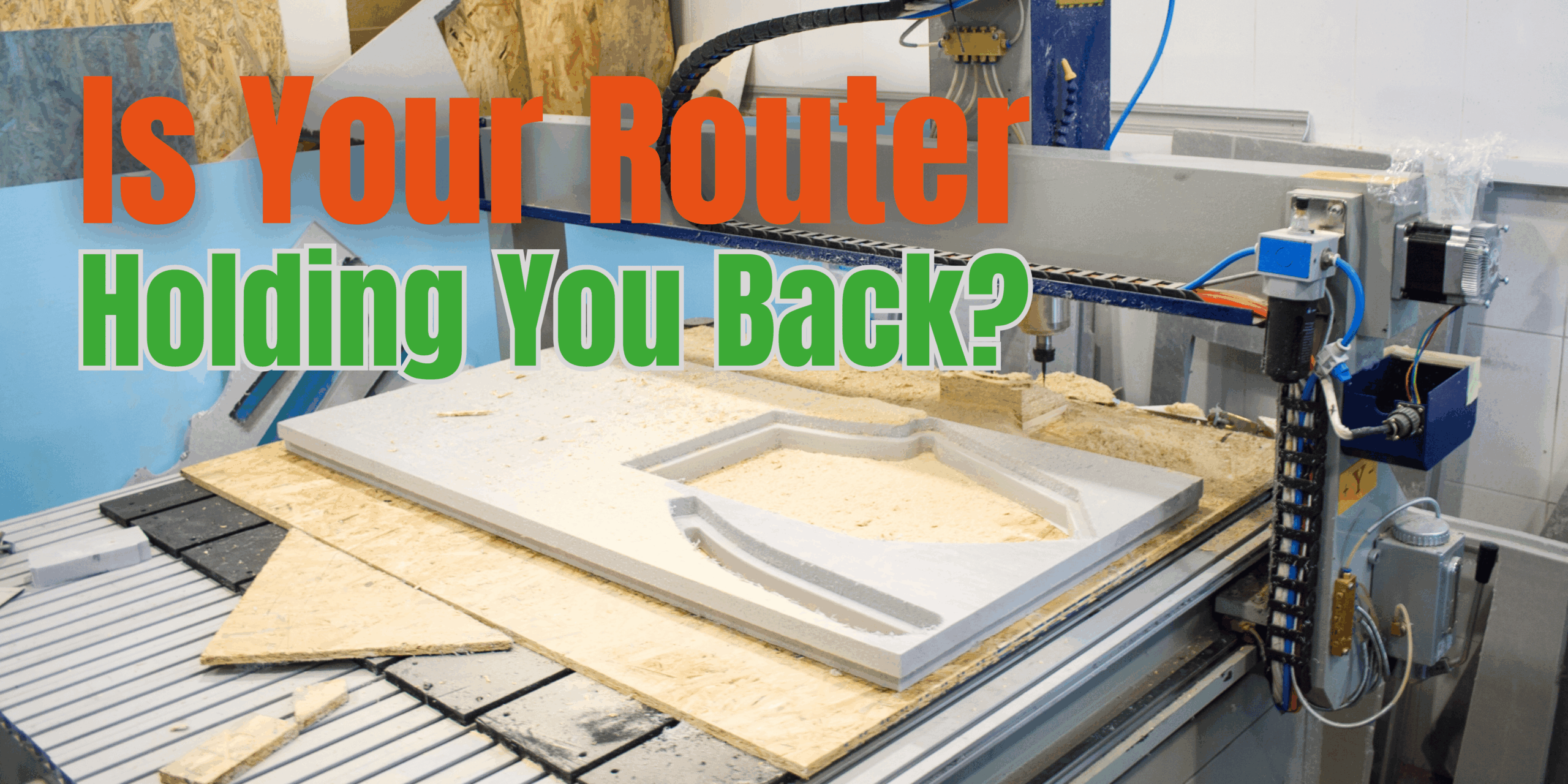
Can a CNC Router Cover Lots of Different Industries?
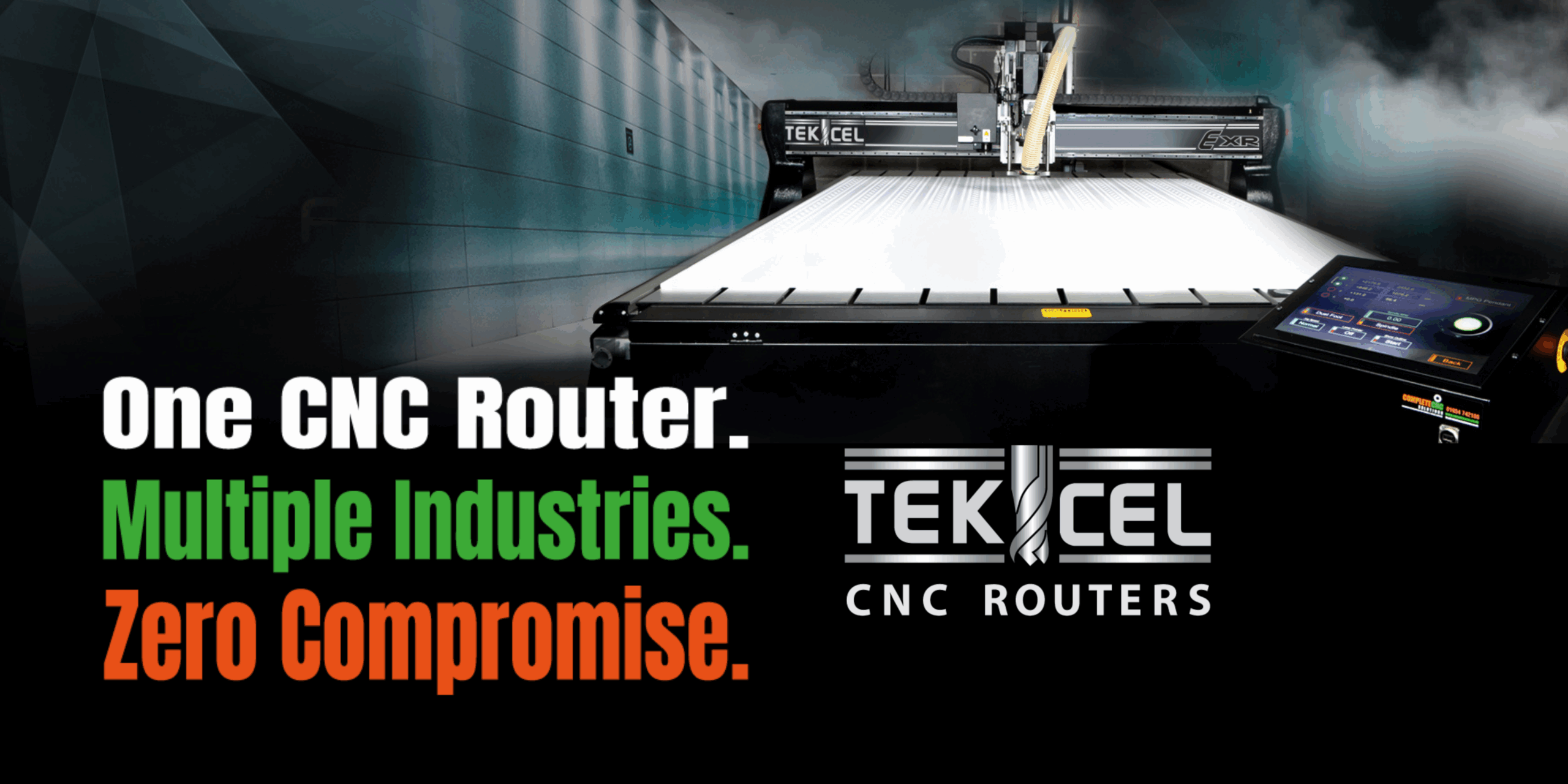
Why Case Makers Should Be Cutting Foam In-House With a CNC Router
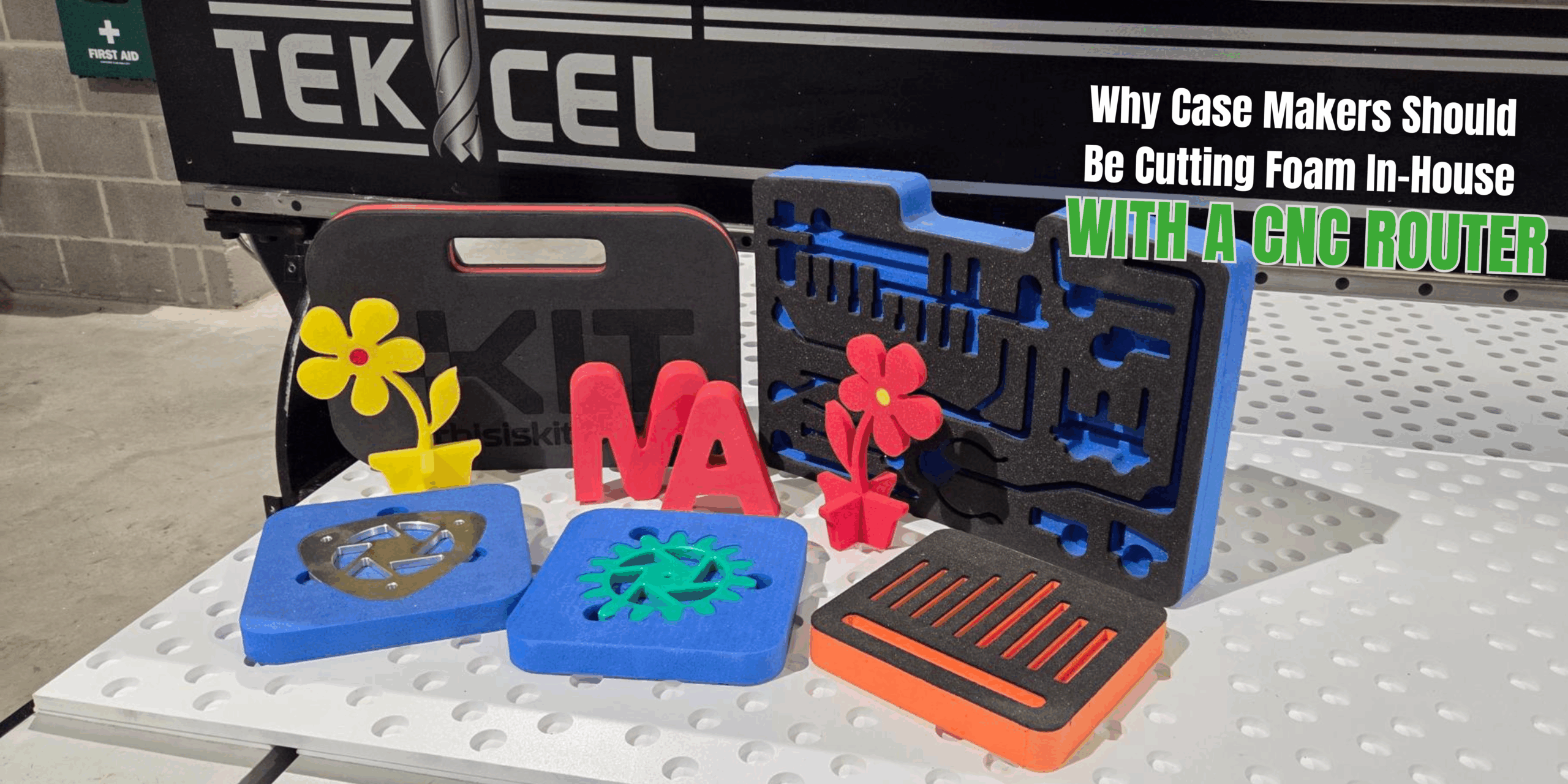
FAQ: What Tips Do You Have For Cutting MDF?
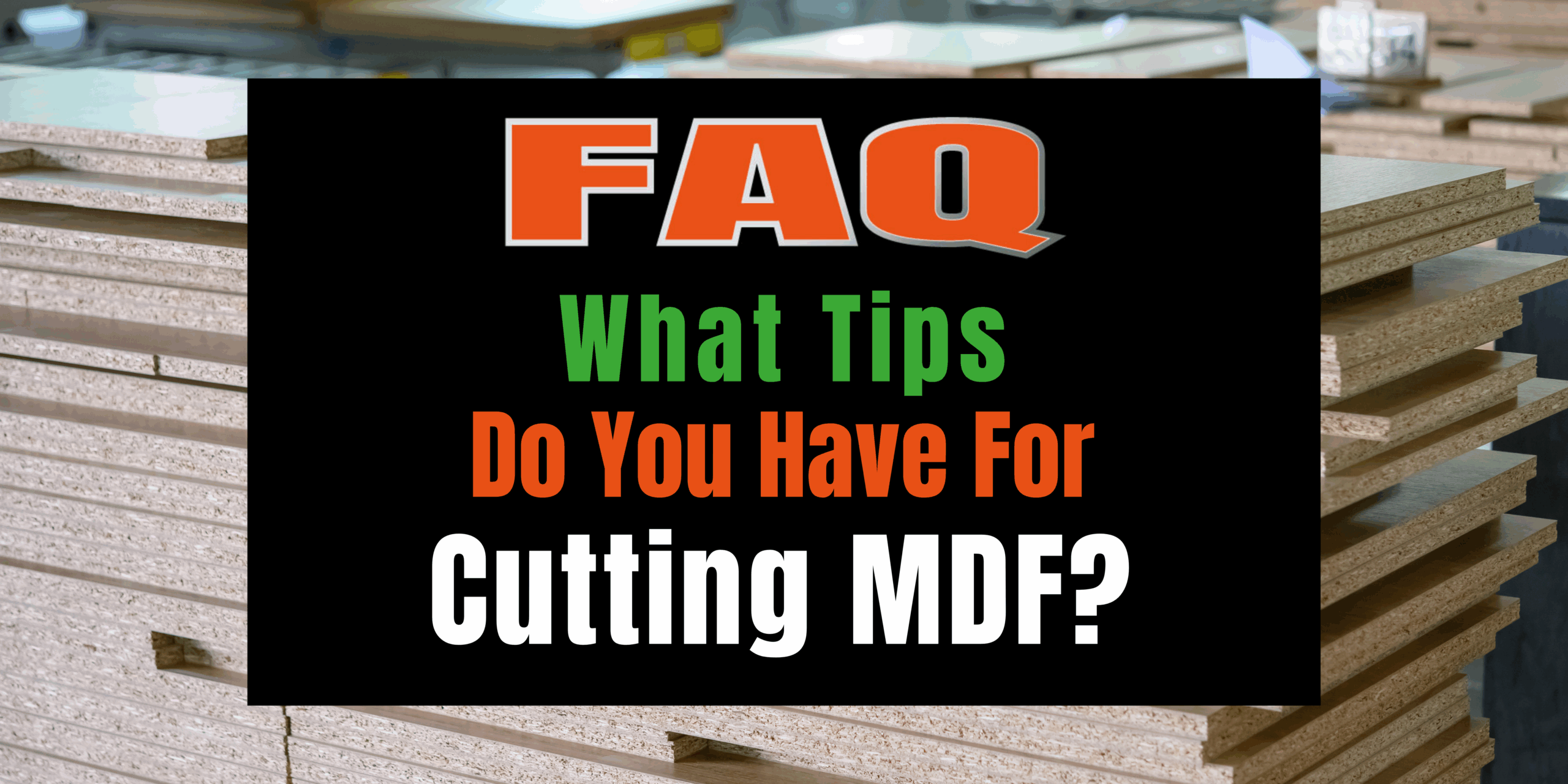
Thinking About Investing in a CNC Router?
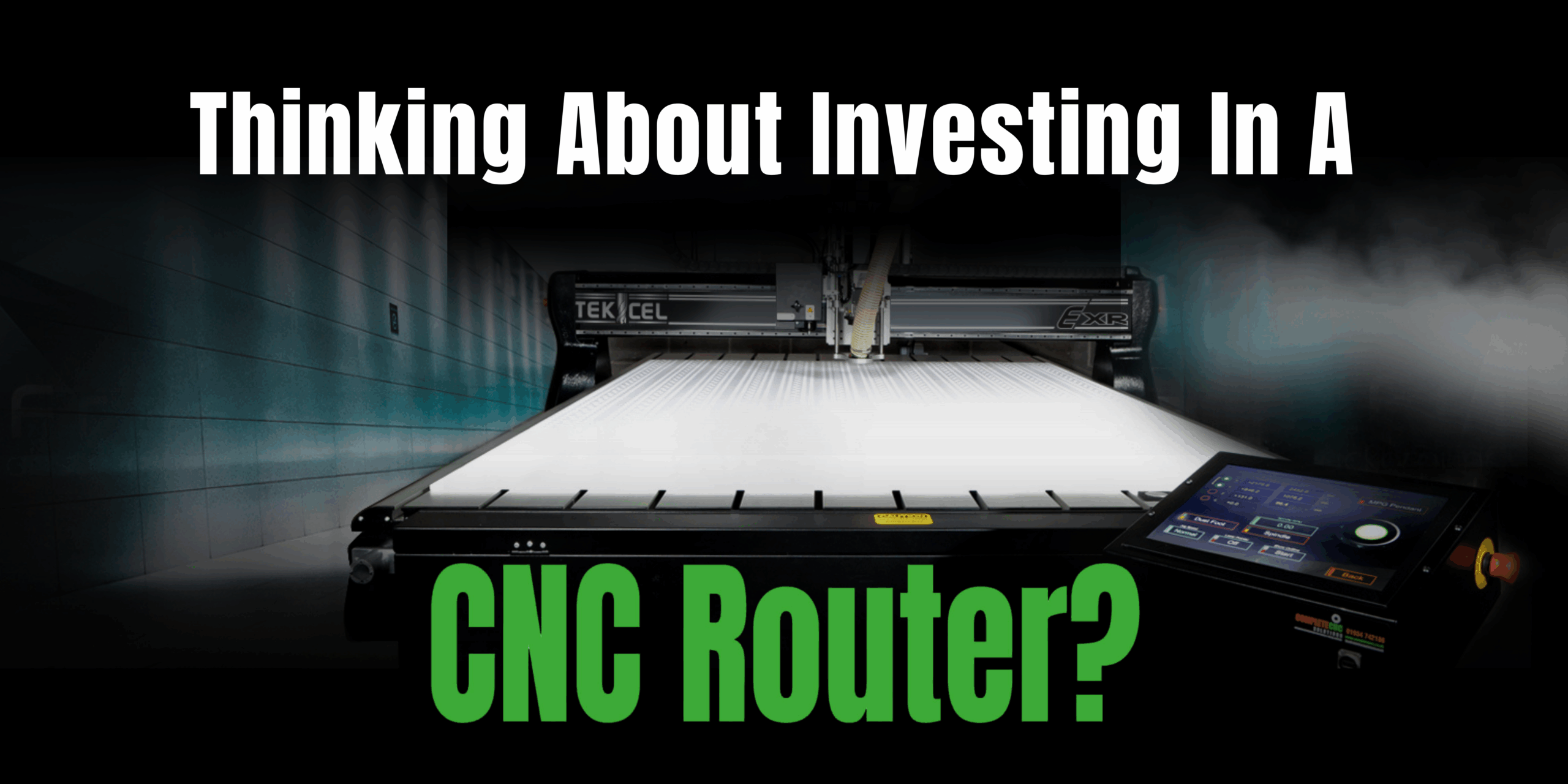
Why Tekcel EXR is the CNC Router You Need
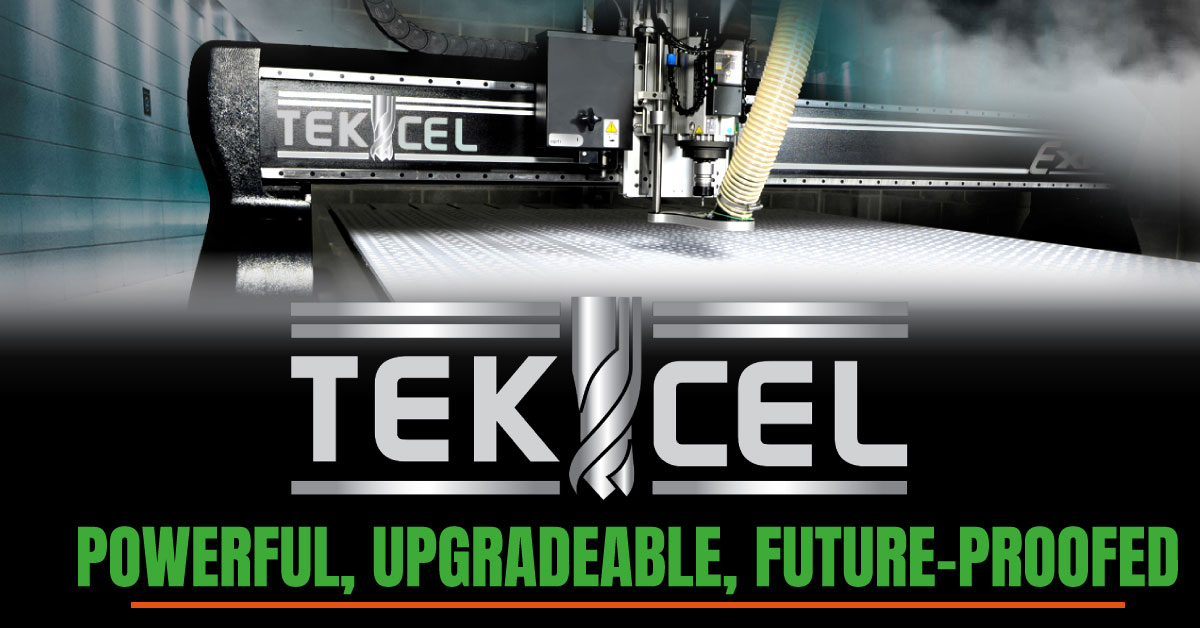
CNC Woodworking Without The Headaches
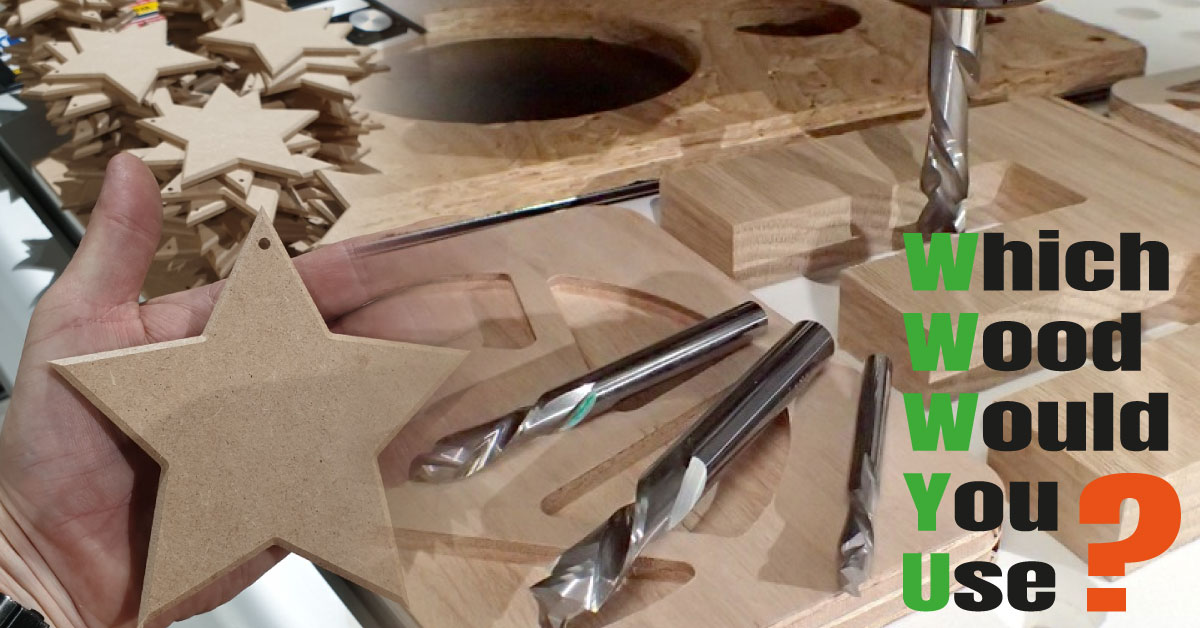
No More Botched Cuts on Plastics & Acrylics!
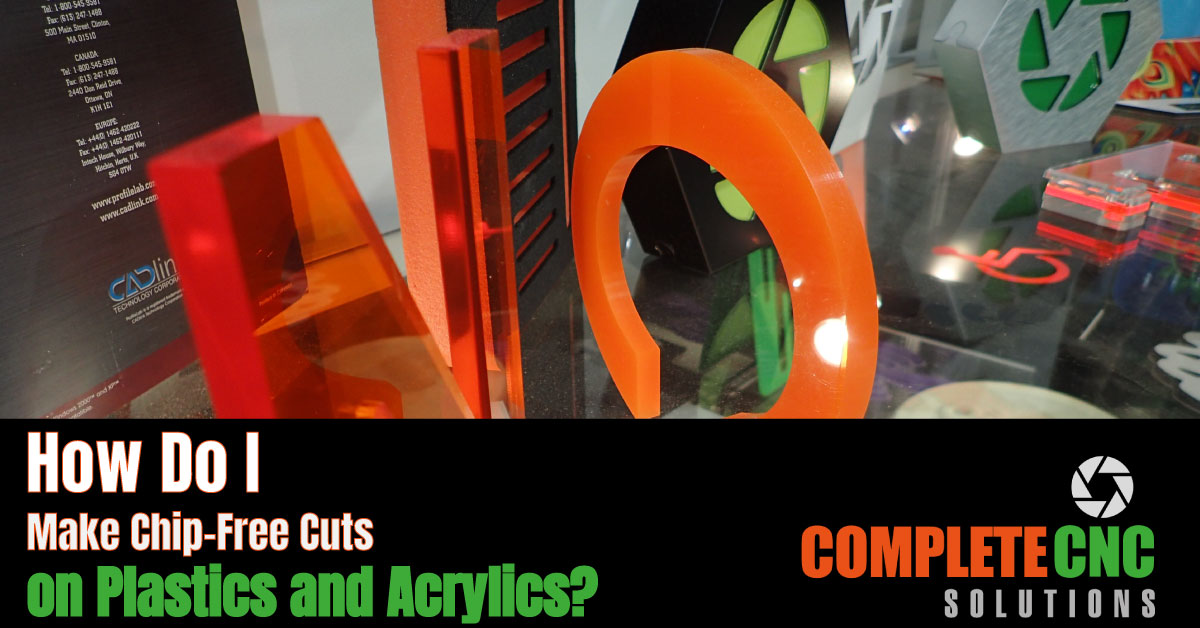
Struggling with Tool Wear?
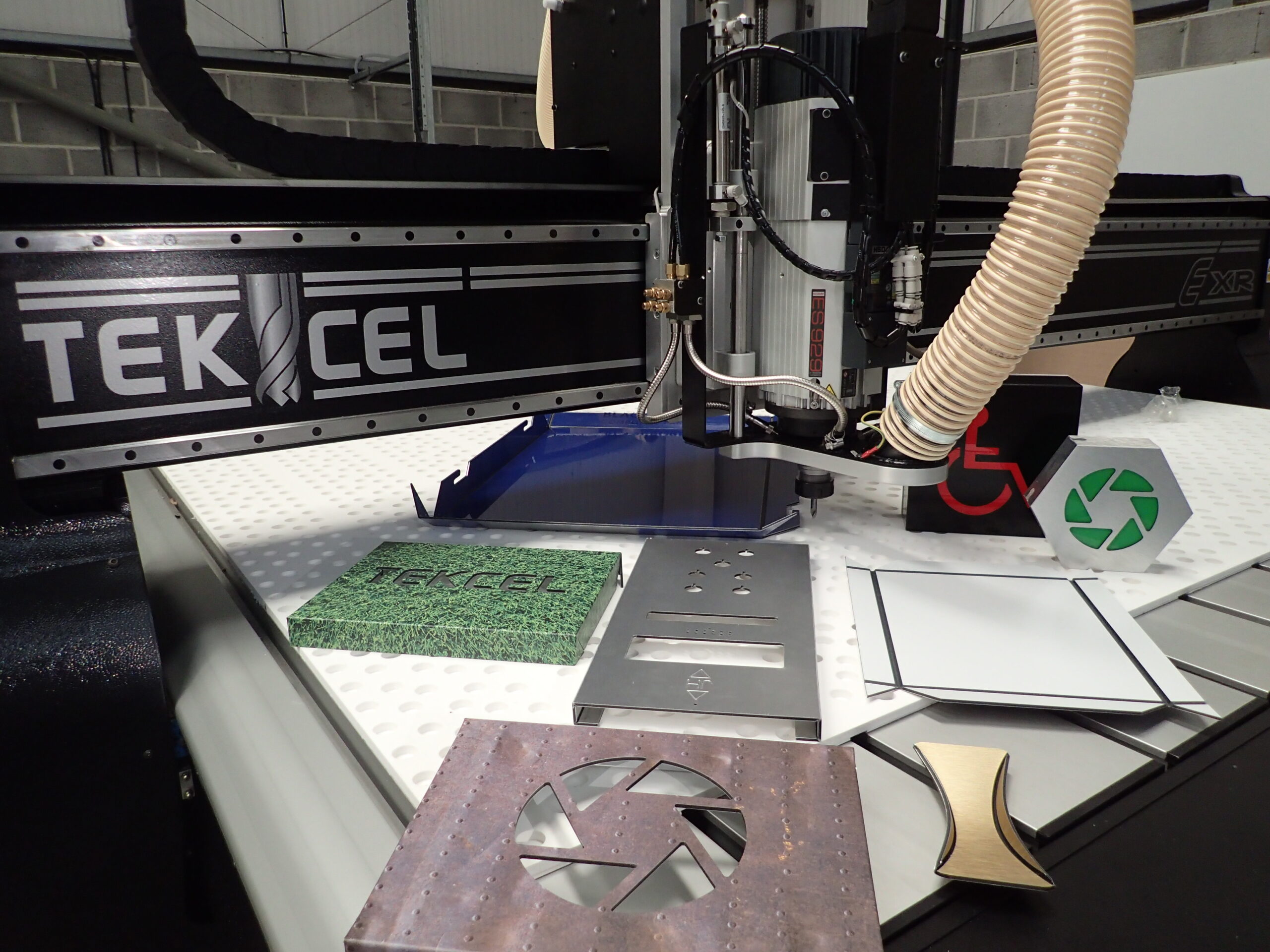
How to Successfully Cut Small Shapes Without Them Moving
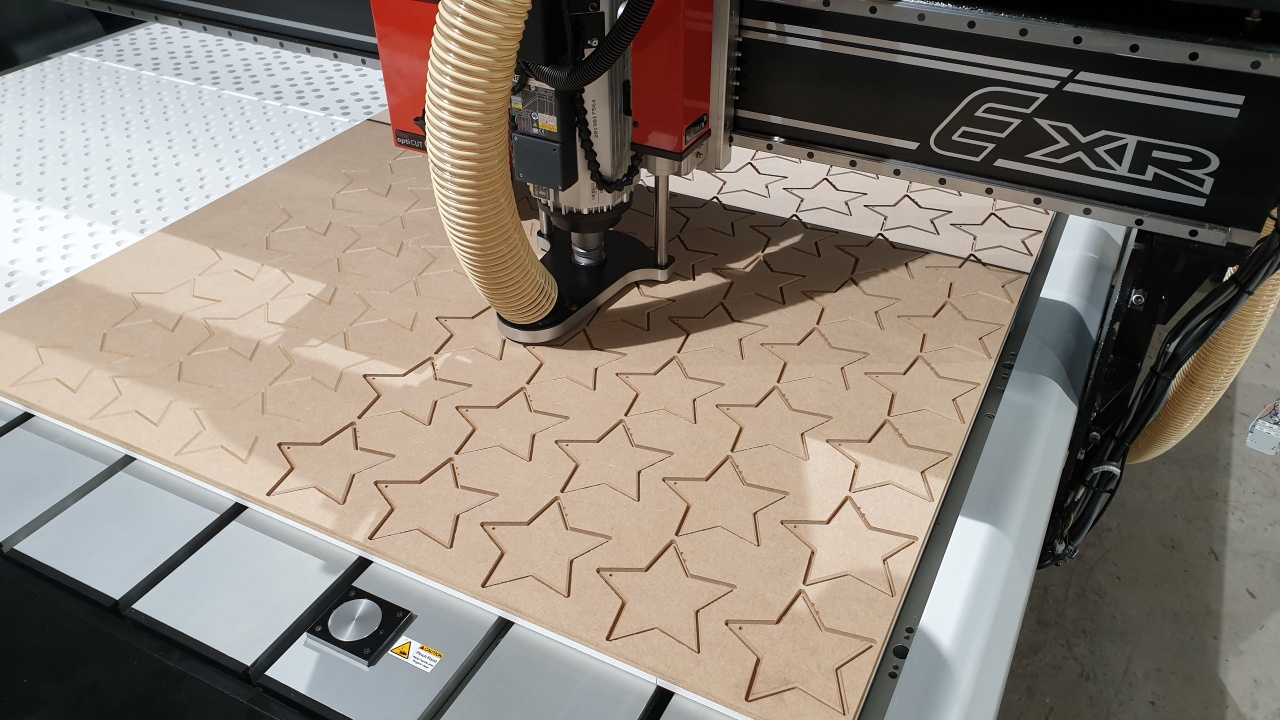
Documenting CNC Router Settings and Processes for Future Success
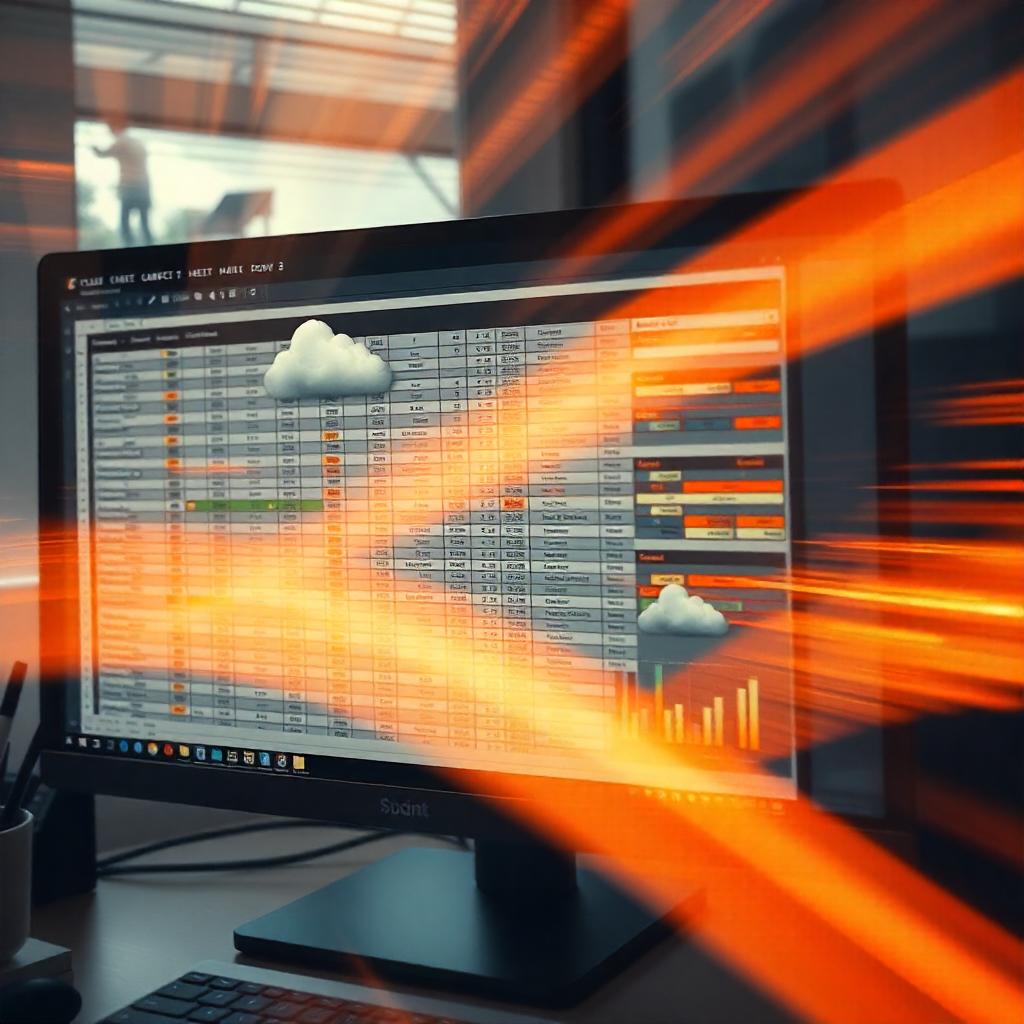
Training Tailored For Success With Your Tekcel CNC Router
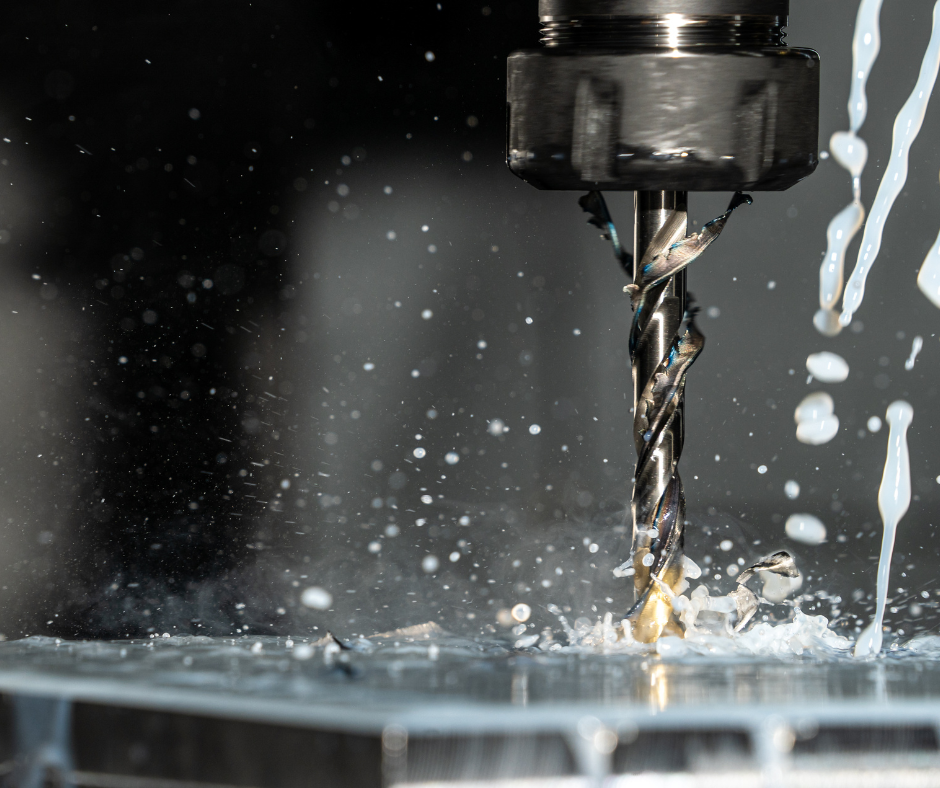
Stay Ahead with Software Updates for Your Tekcel CNC Router
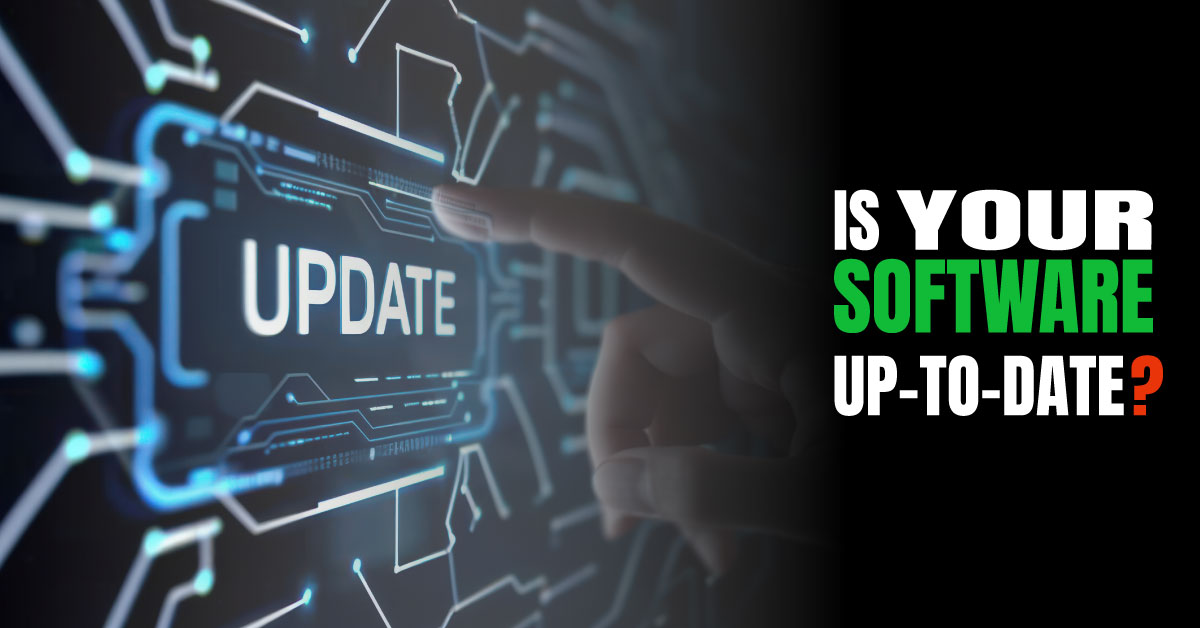
Revolutionise Signage with Tekcel CNC and Precision ACM Tooling
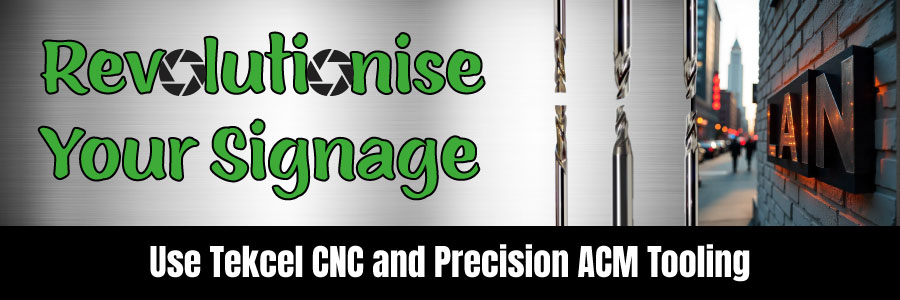
Cutting it Close? Know When to Change Your Collet for Safe, Sharp Results
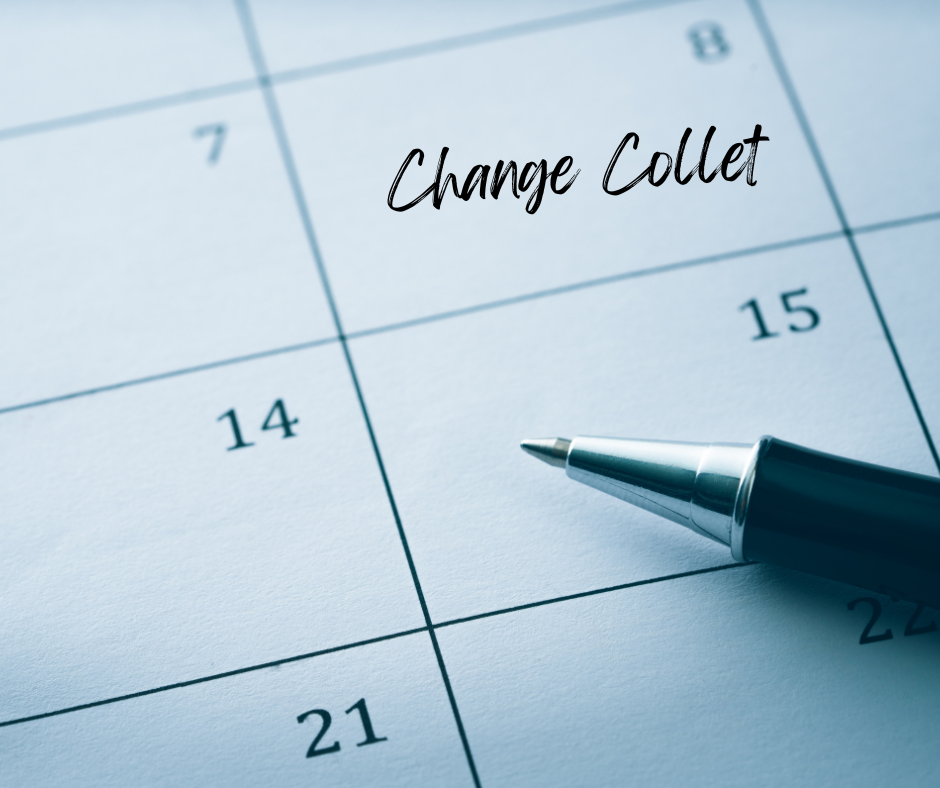
How to Avoid Burning and Furring When Cutting Wood with a CNC Router
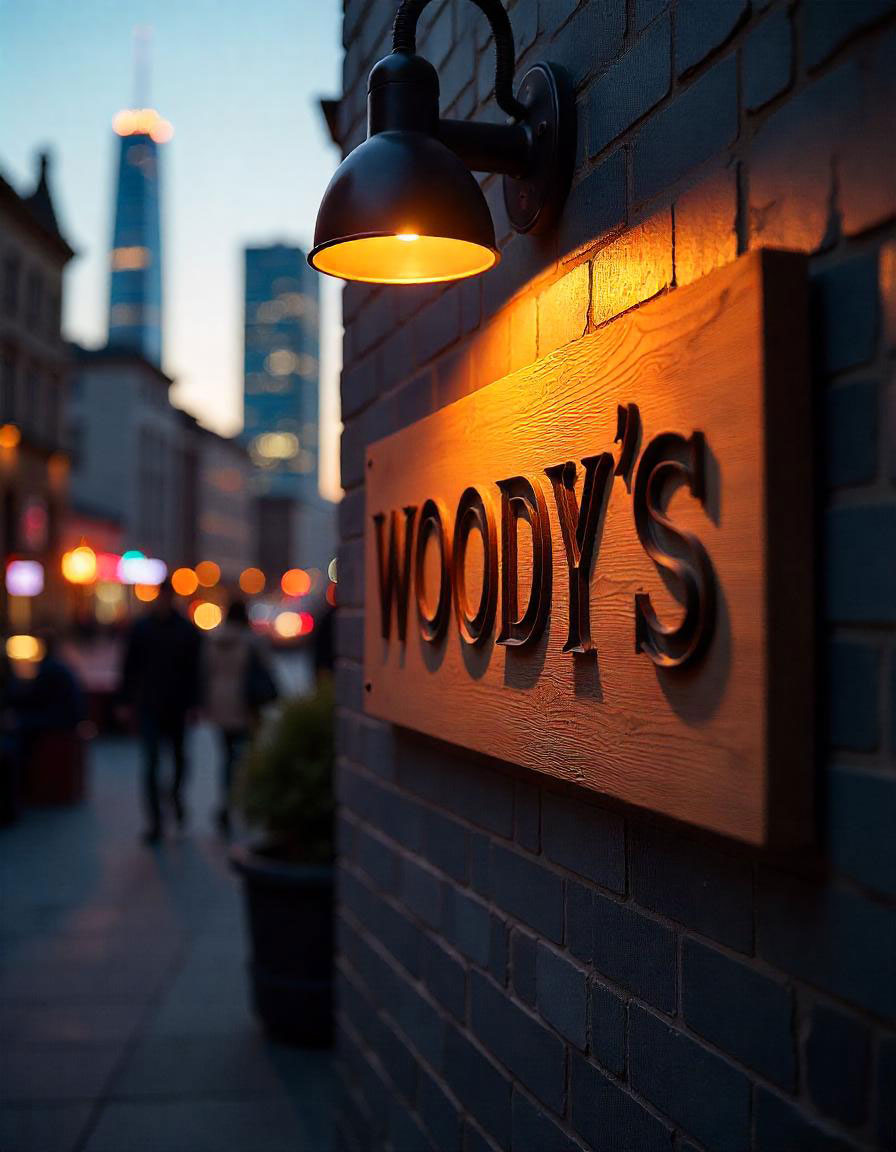
How to choose the right CNC tool for the job/material
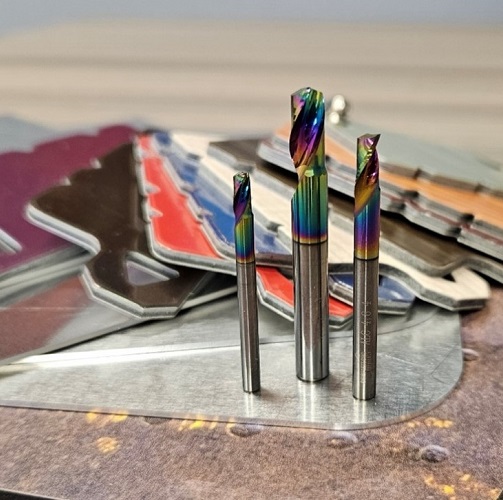
Which CNC Router covers all the bases for a signage manufacturer?
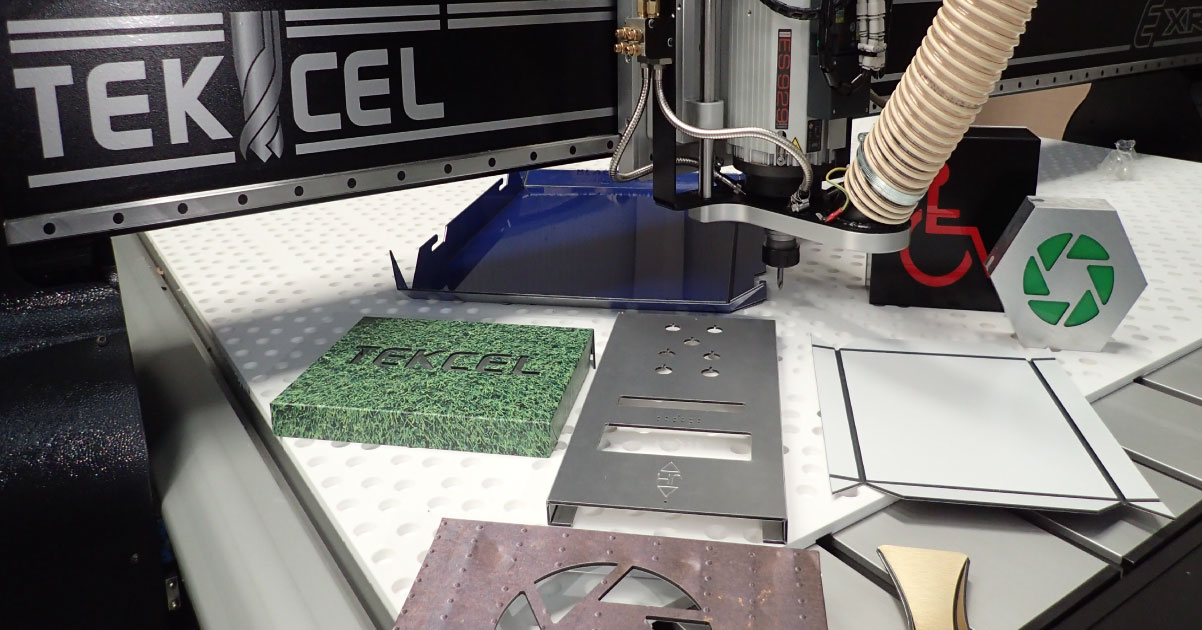
The Tekcel – High Pressure Mist Coolant System for Metal Cutting
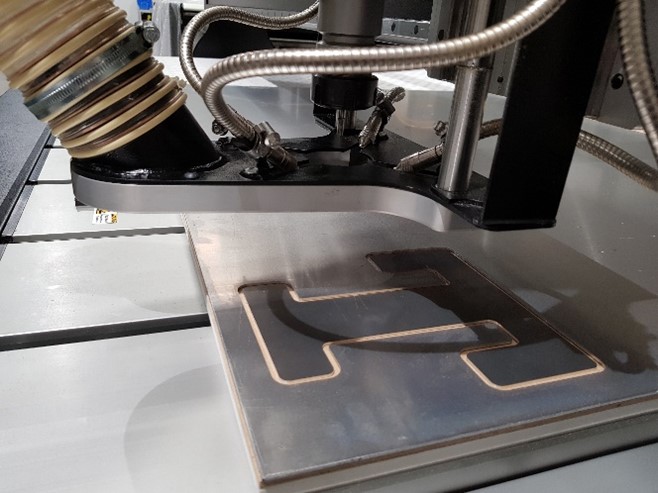
Tekcel CNC Routers – Furniture & Woodworkers dream machine
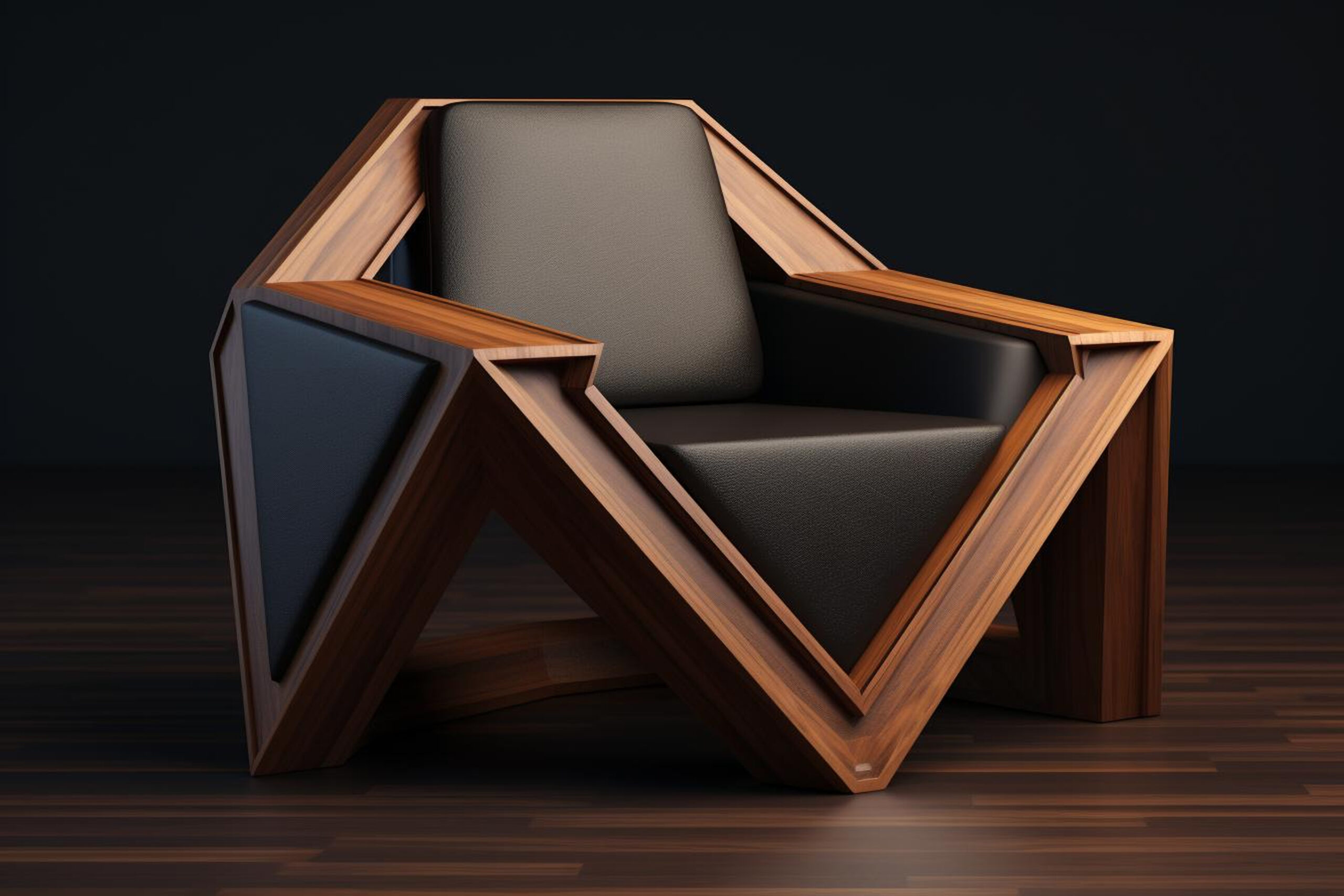
Start with a “Tekcel CNC” for the best finish…
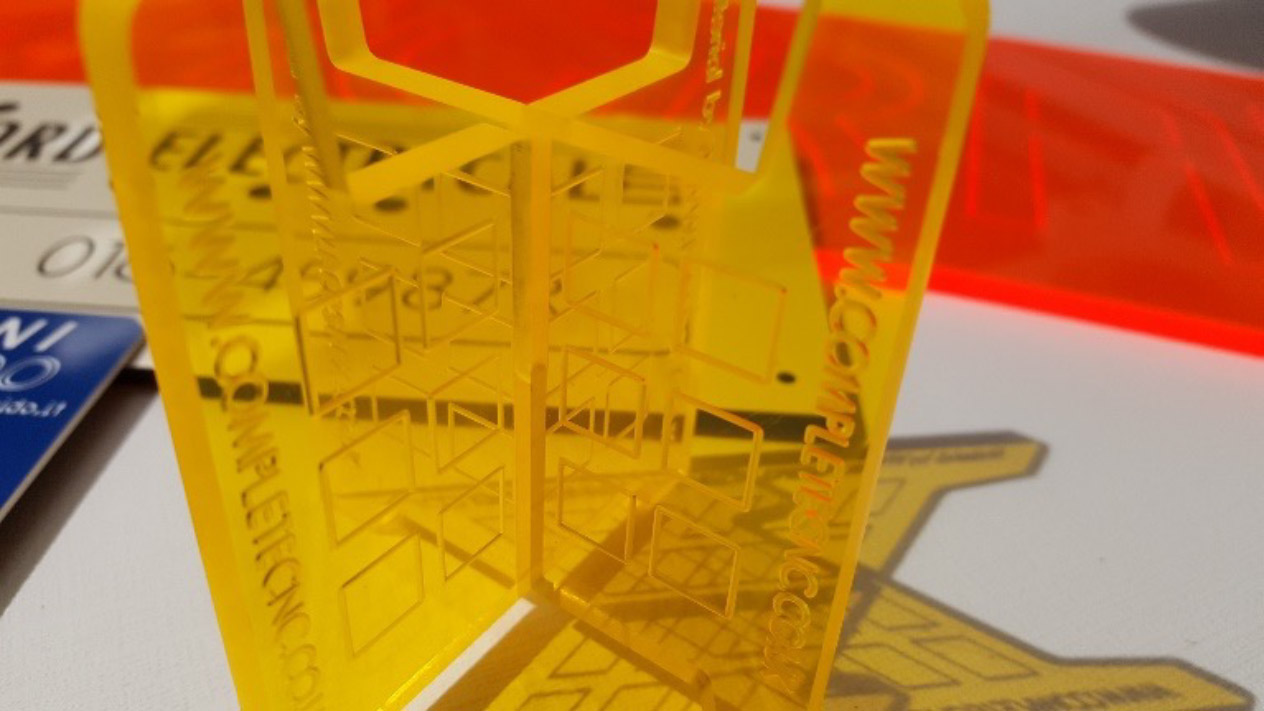
Under the Bonnet of a Tekcel EXR CNC Router
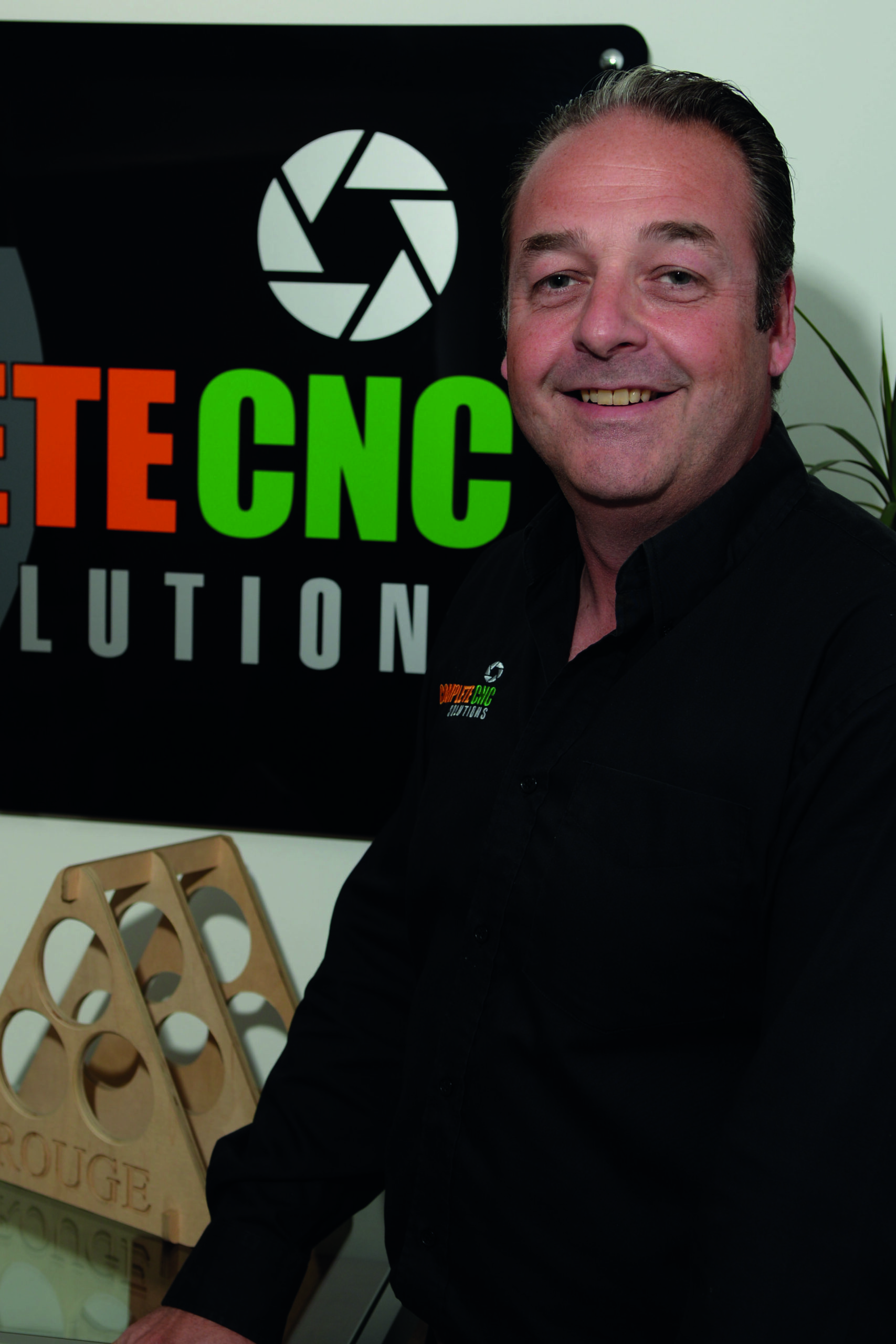
How to Skim the MDF Sacrificial Bed on your Tekcel CNC Router: A Step-by-Step Guide
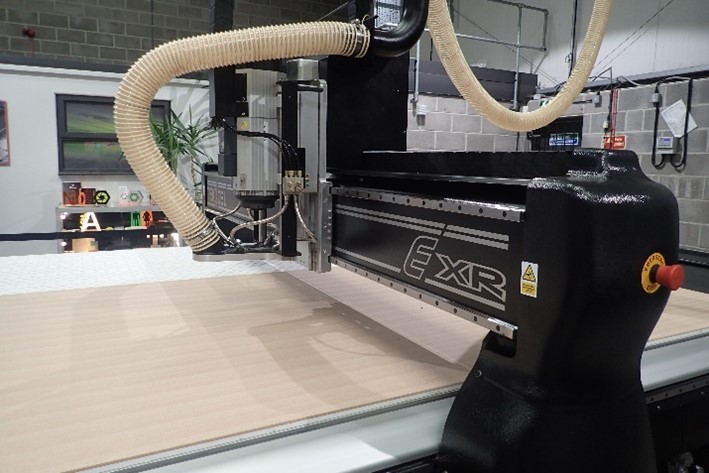
What is an ATC and why do I need one?
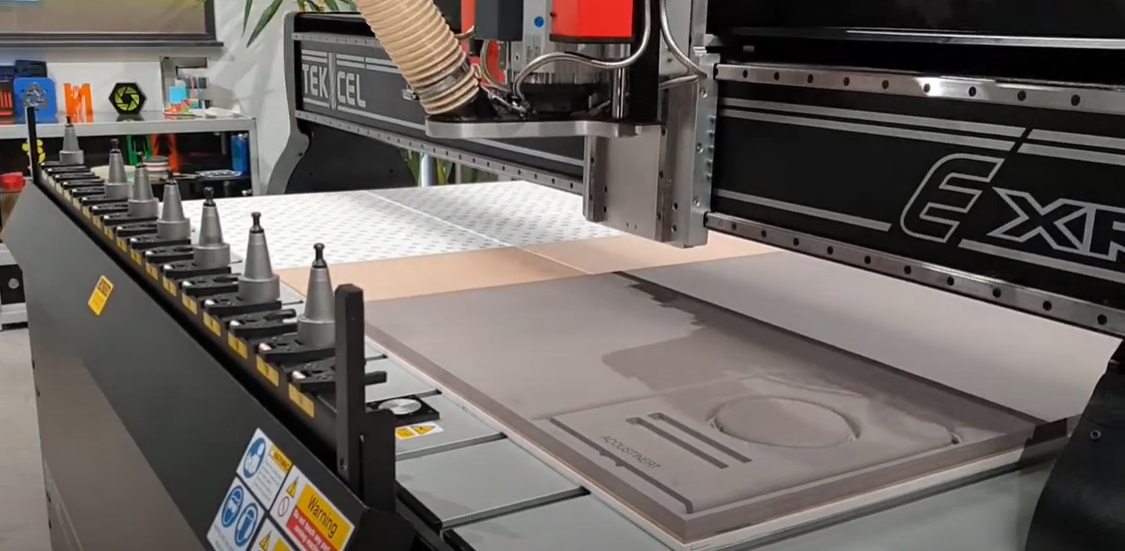
Tekcel CNC for ACM (Aluminium Composite Material) Signage:
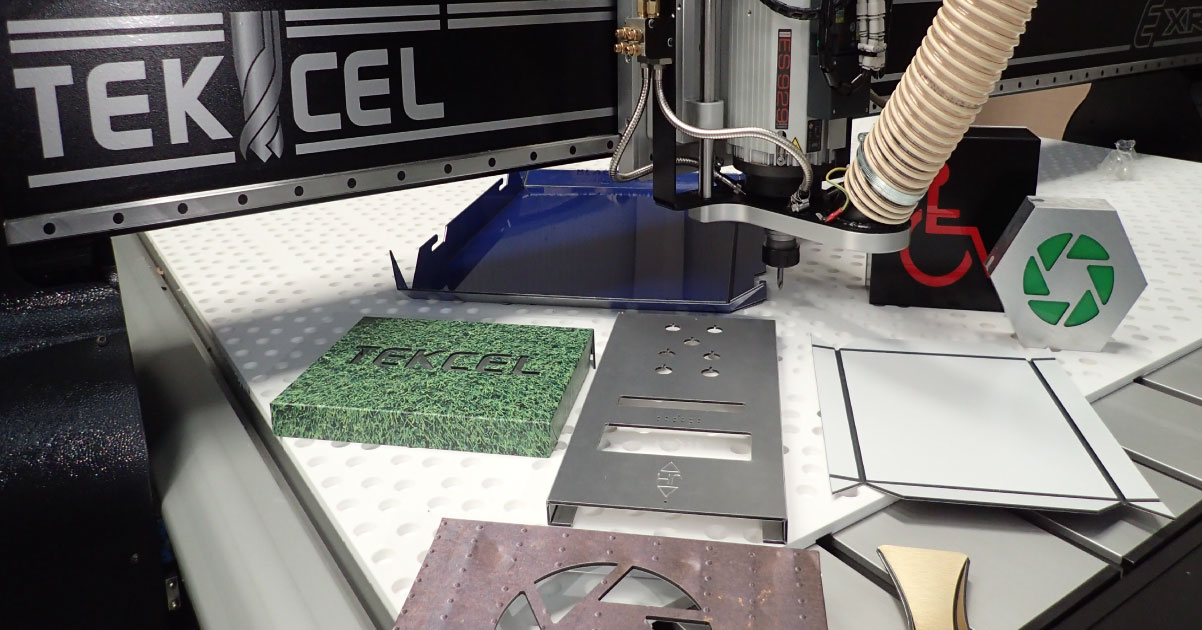
The Benefits of Acrylic
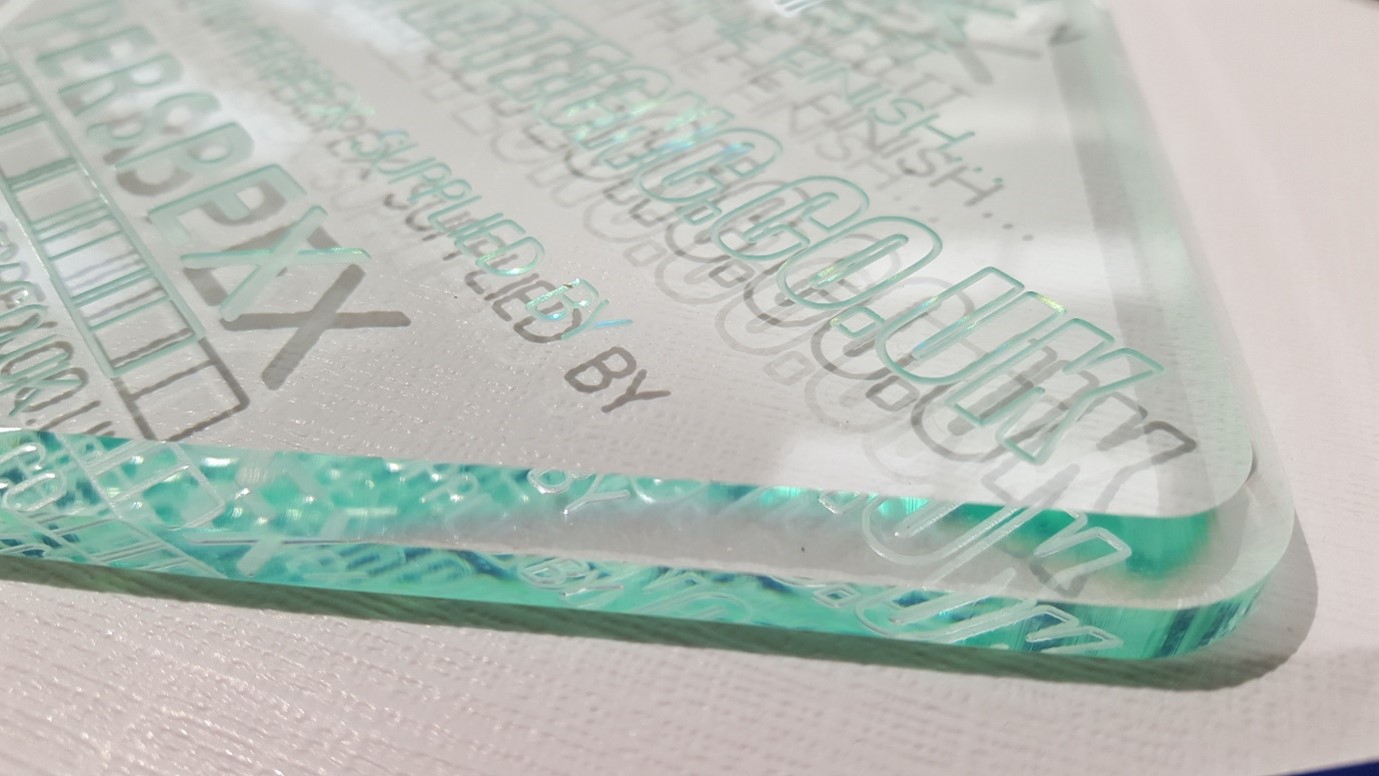
CNC for DFM
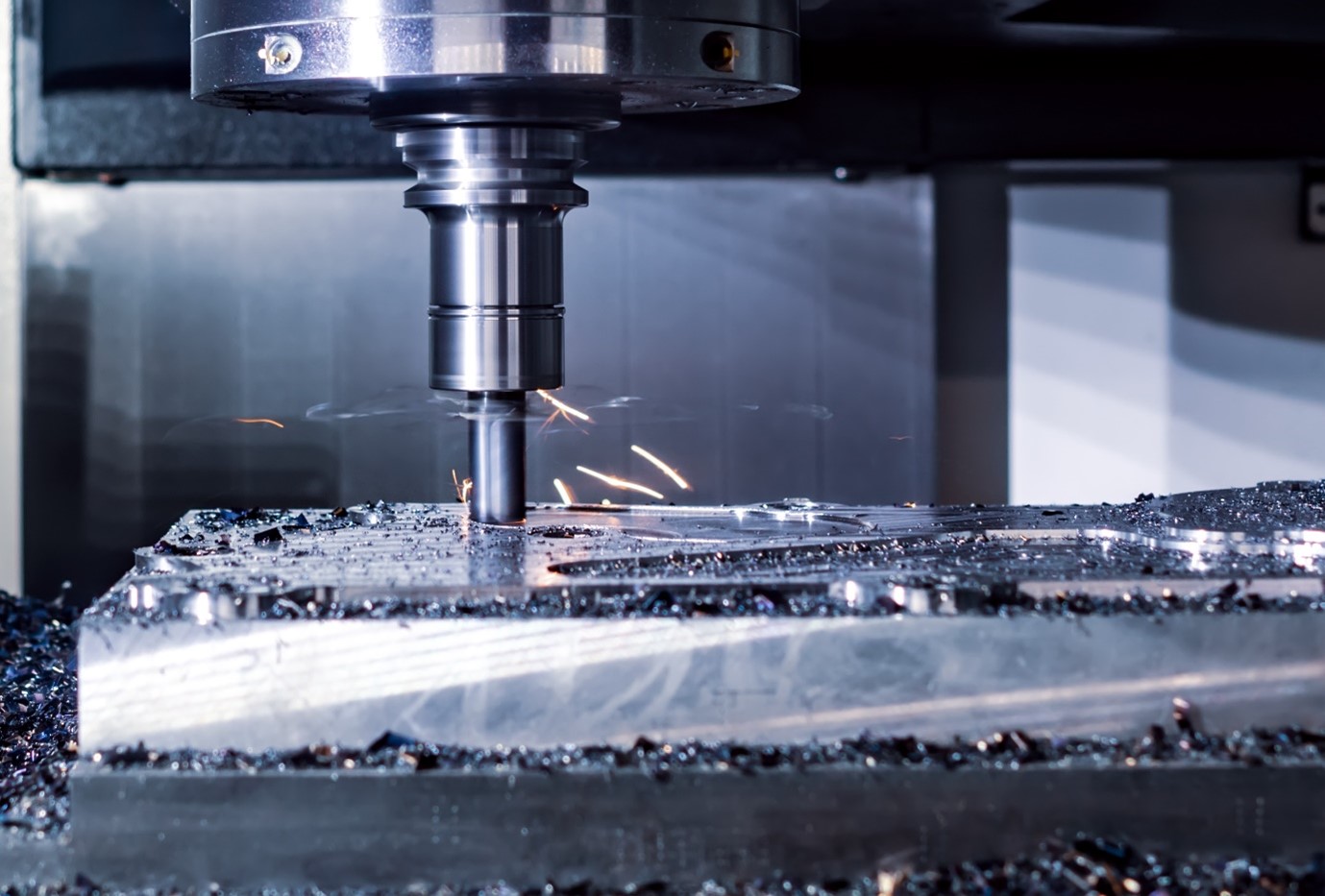
The Unbreakable Rules!
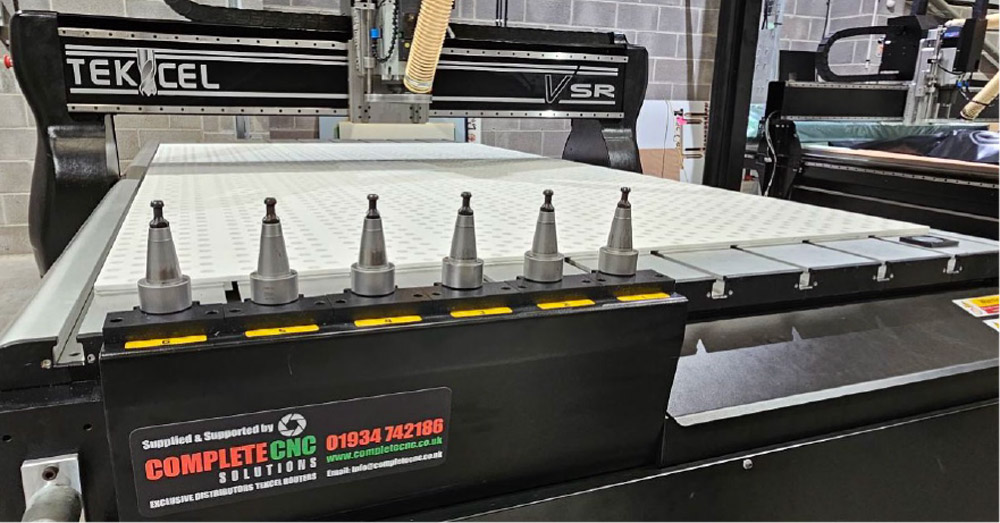
Welcome to the world of CAD/CAM
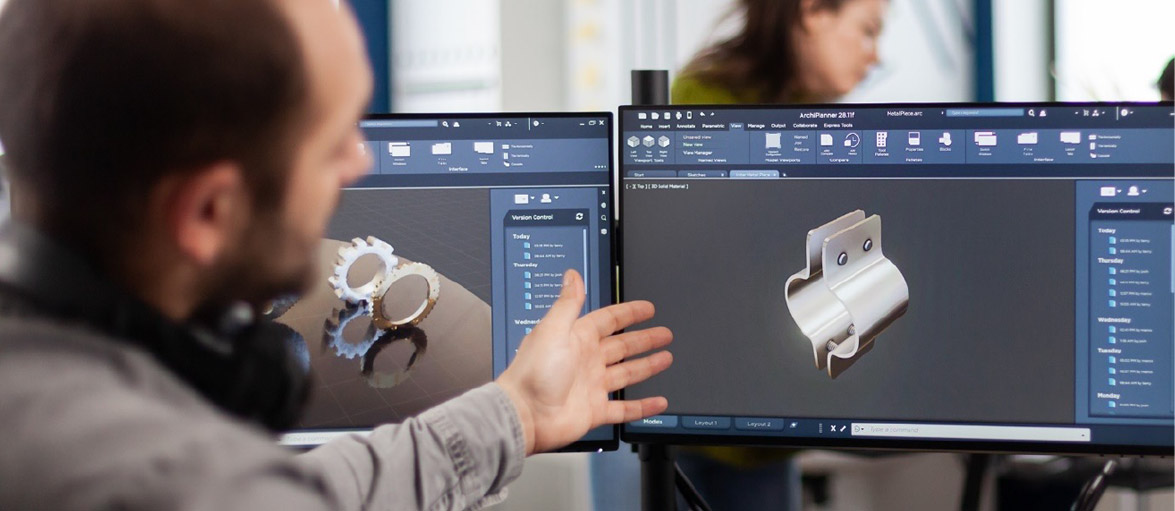
10 Tips for Successful Aluminium Cutting with CNC Routers
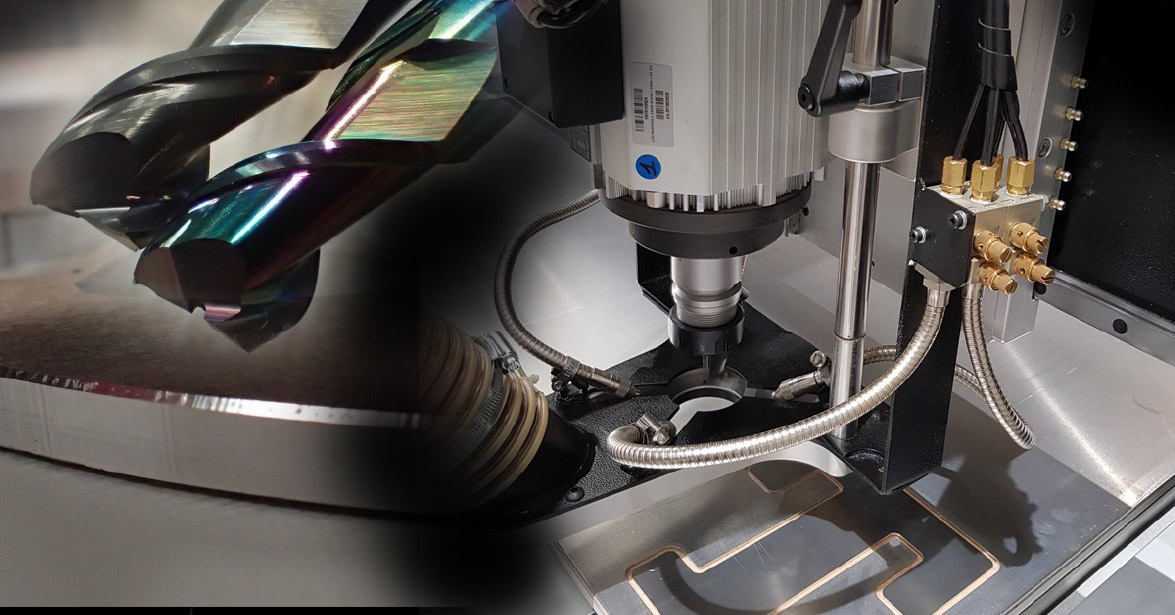
Mastering the Art of Tekcel CNC Router Speeds and Feeds: A Comprehensive Guide
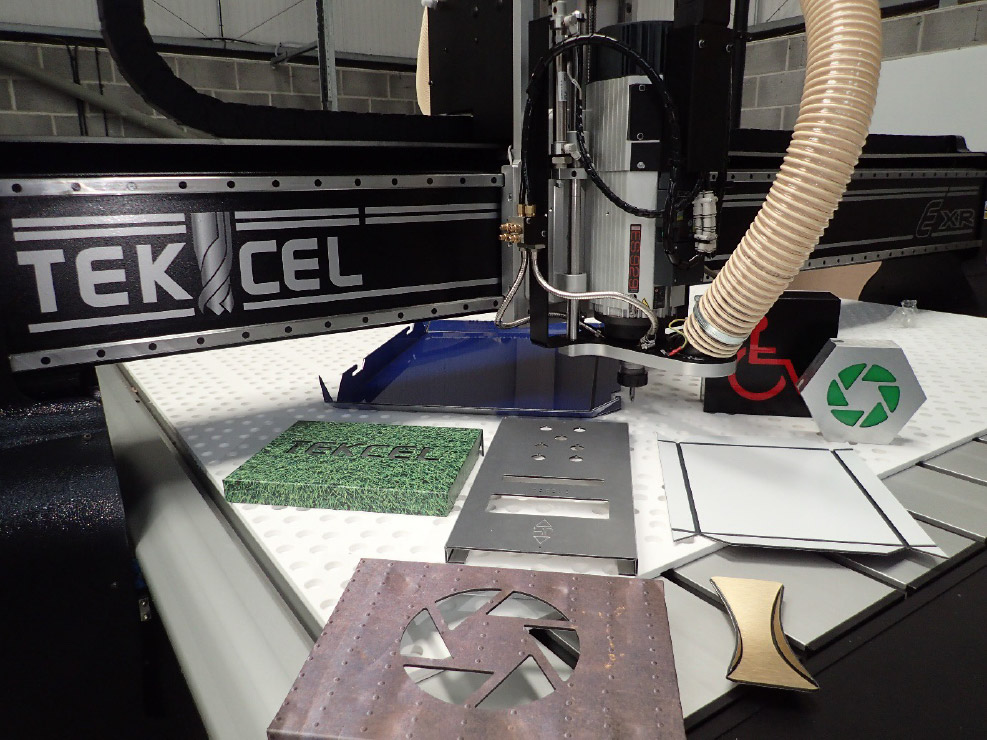
CNC Routers For Sign Making
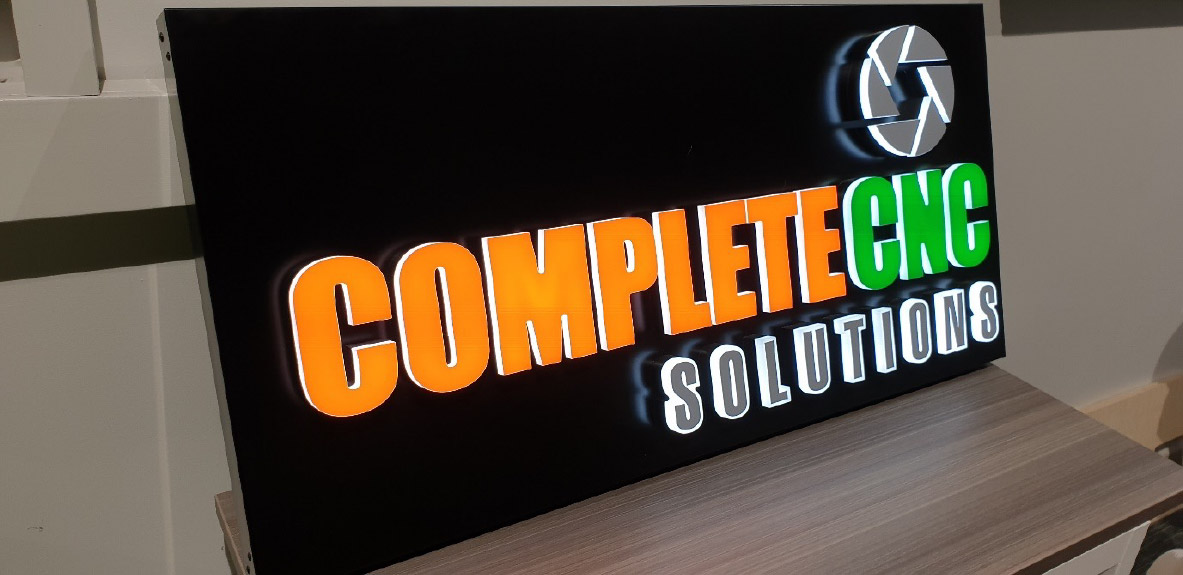
Cutting Acrylic With Your CNC Router
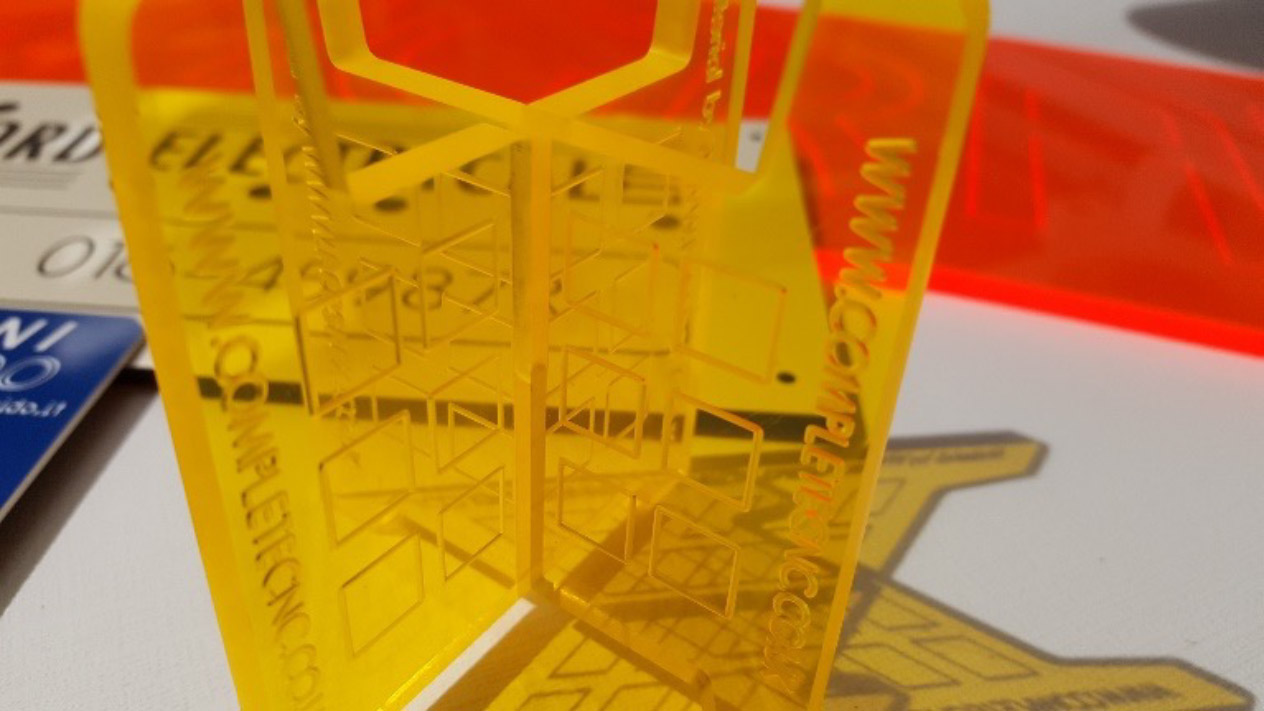
Collets: An Essential Tool
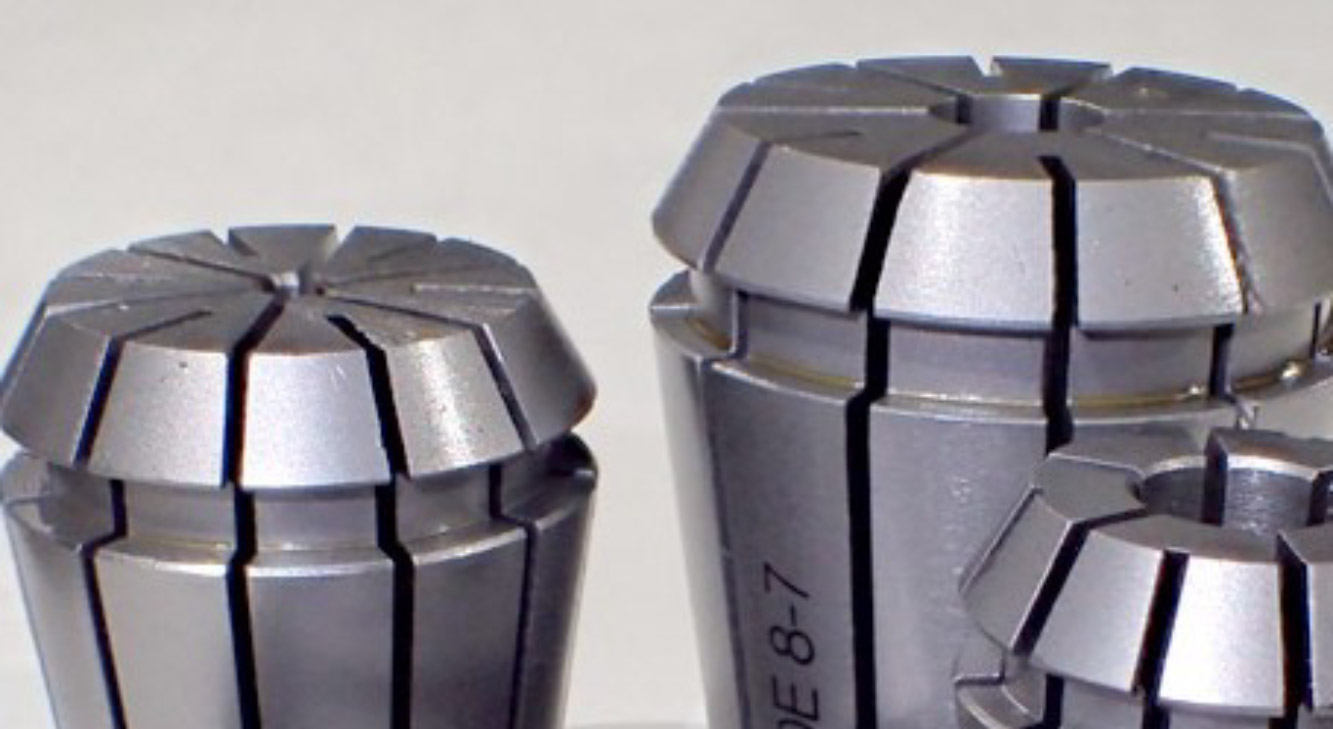
Calling all converters: How CNC Routers Elevate Vehicle Conversions
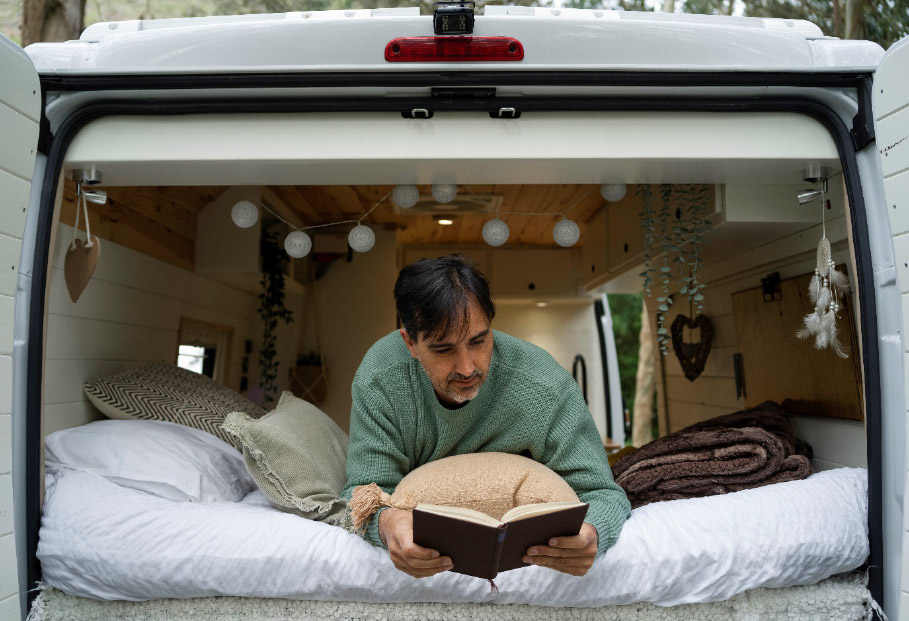
The Right tool for the job
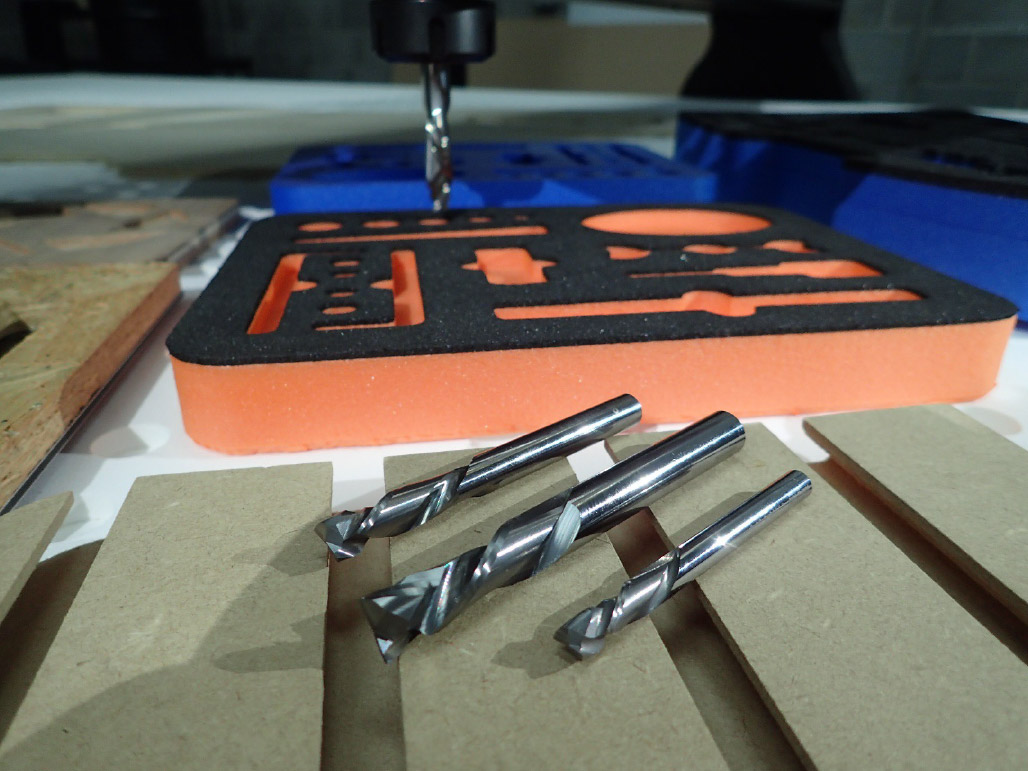
What is the cutting speed of a CNC router?
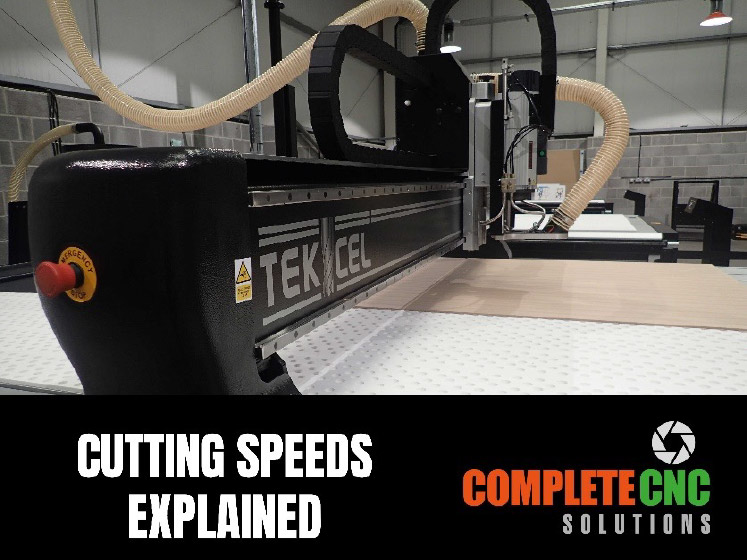
Unravelling the Mystery: Common themes overlooked with CNC Routers
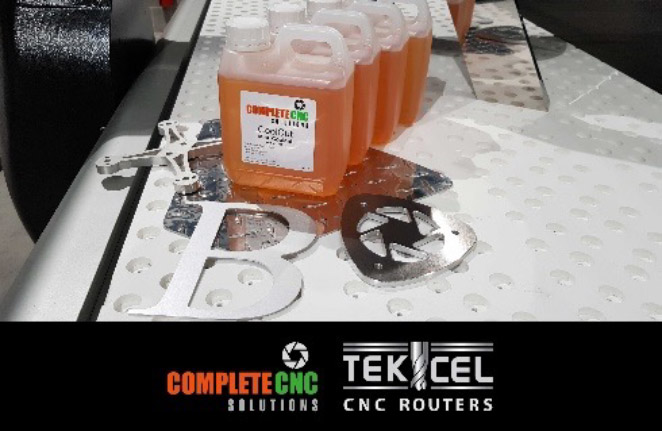
CNC Router Maintenance Guide for Longevity and Efficiency
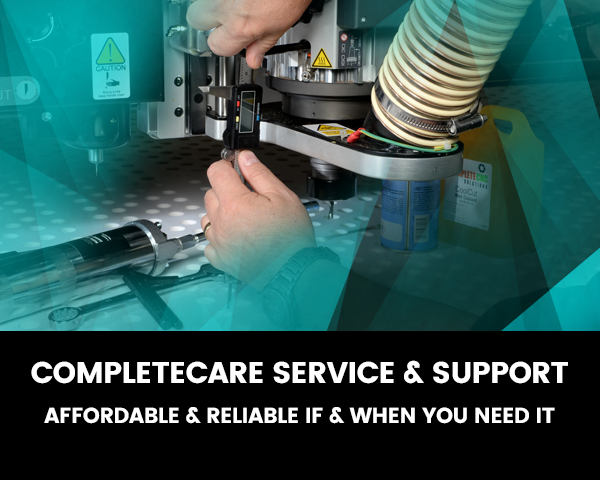
Tekcel Graphical User Interface
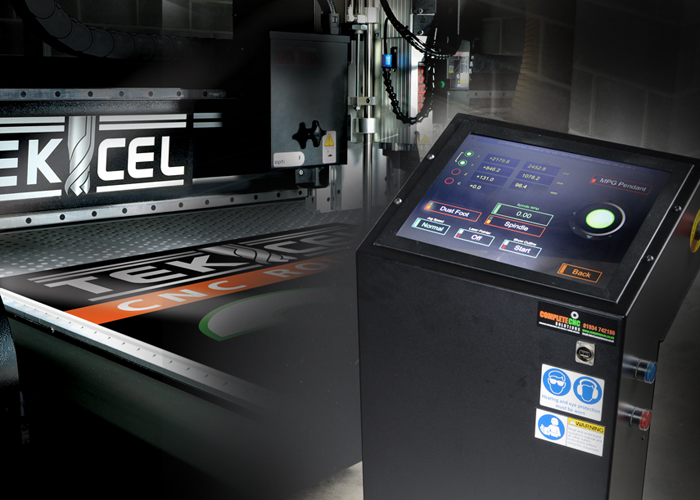
Unlock the World of Carving with CNC Routers!
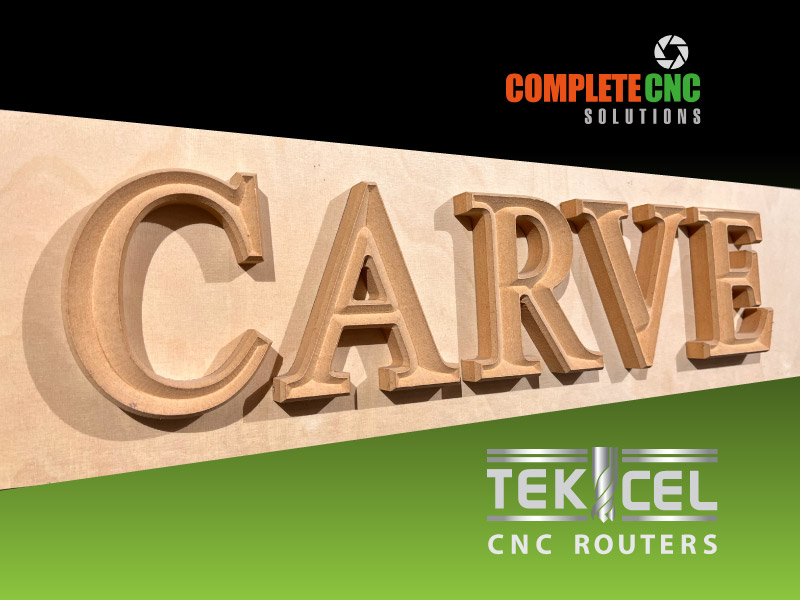
Can a CNC Router Carve Intricate Details? Yes!
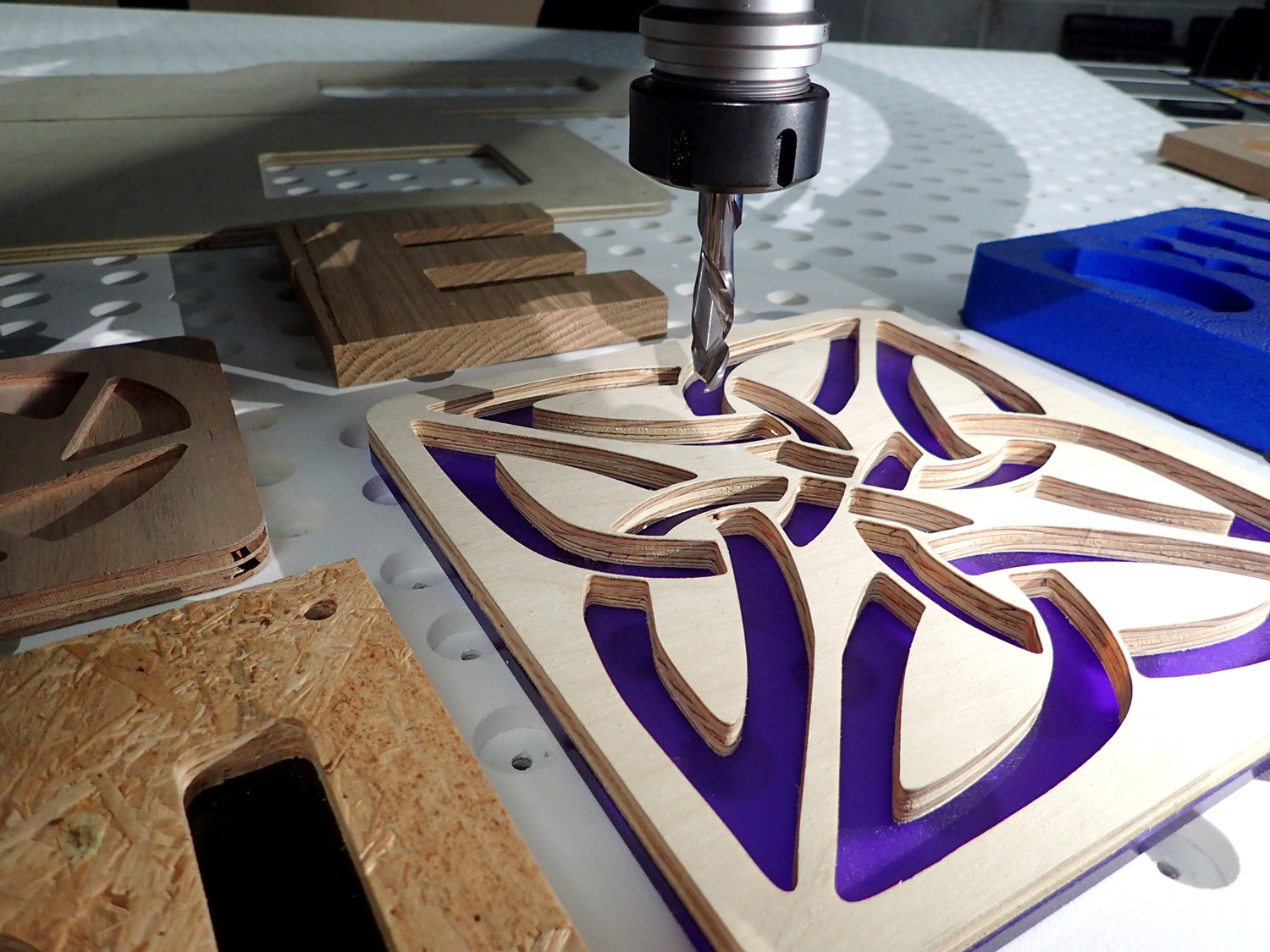
How a Tekcel CNC machine can provide value for your business
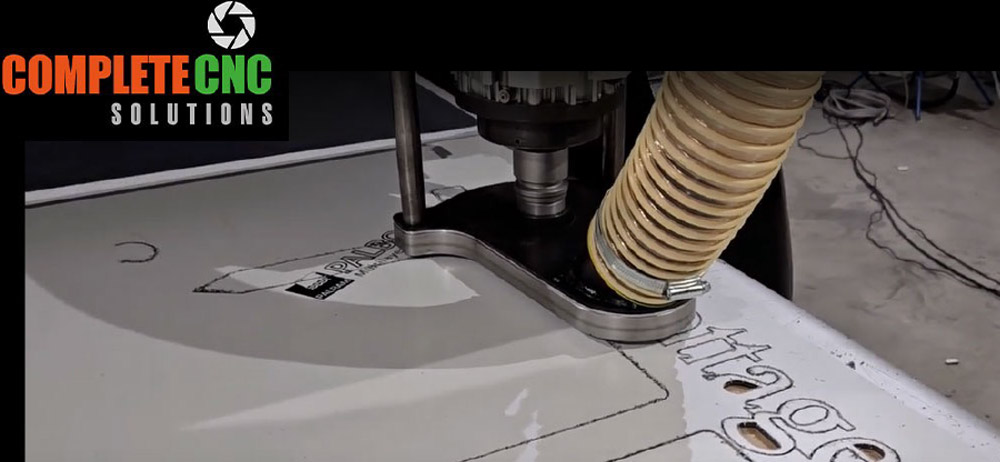
Elevating Point of Sale Production with CNC Machines
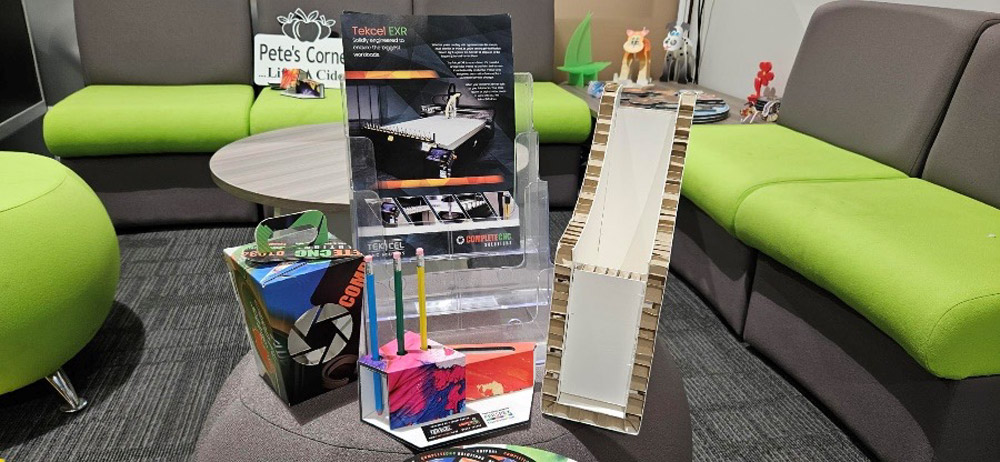
Why Sign Makers are Upgrading to CNC Cutting Machines
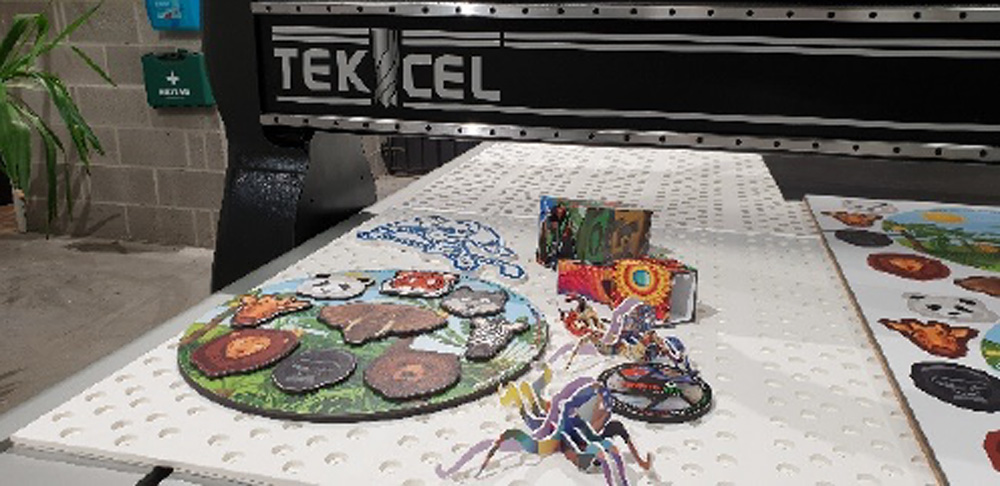
Hibernating Your CNC System During Lockdown.
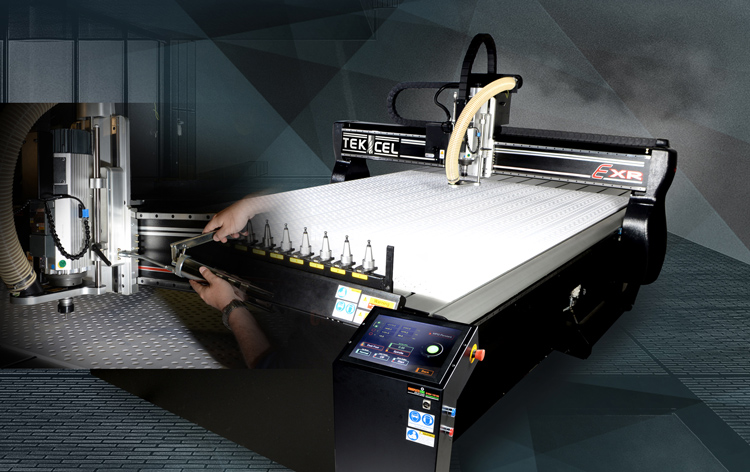
START BIG. GET BIGGER.
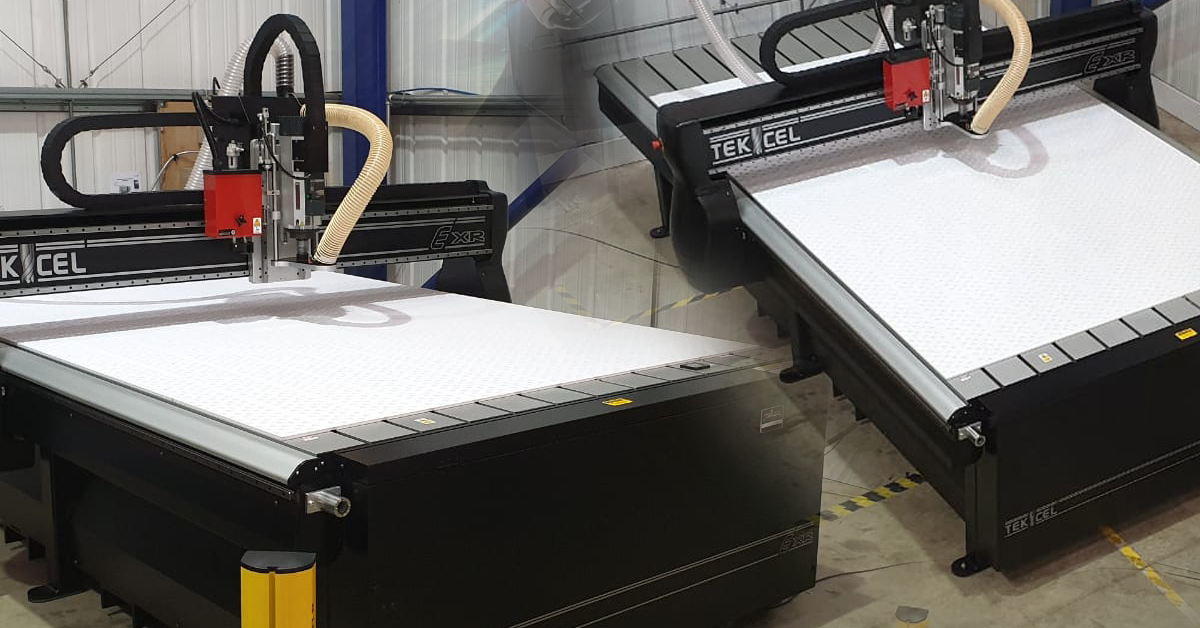
START WITH THE FINISH. FINISH WITH A PROFIT.
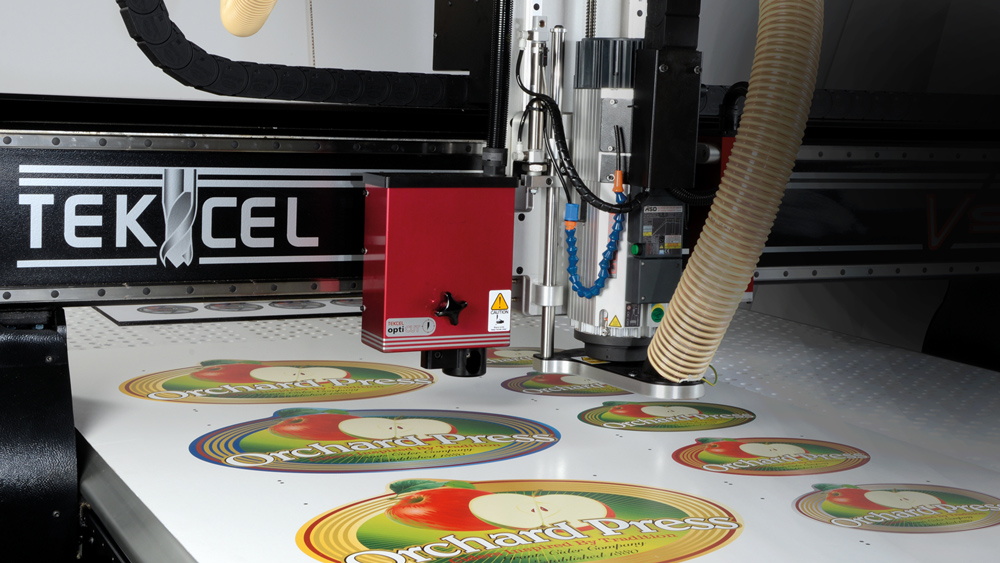
HEAVY METAL. LIGHT WORK.
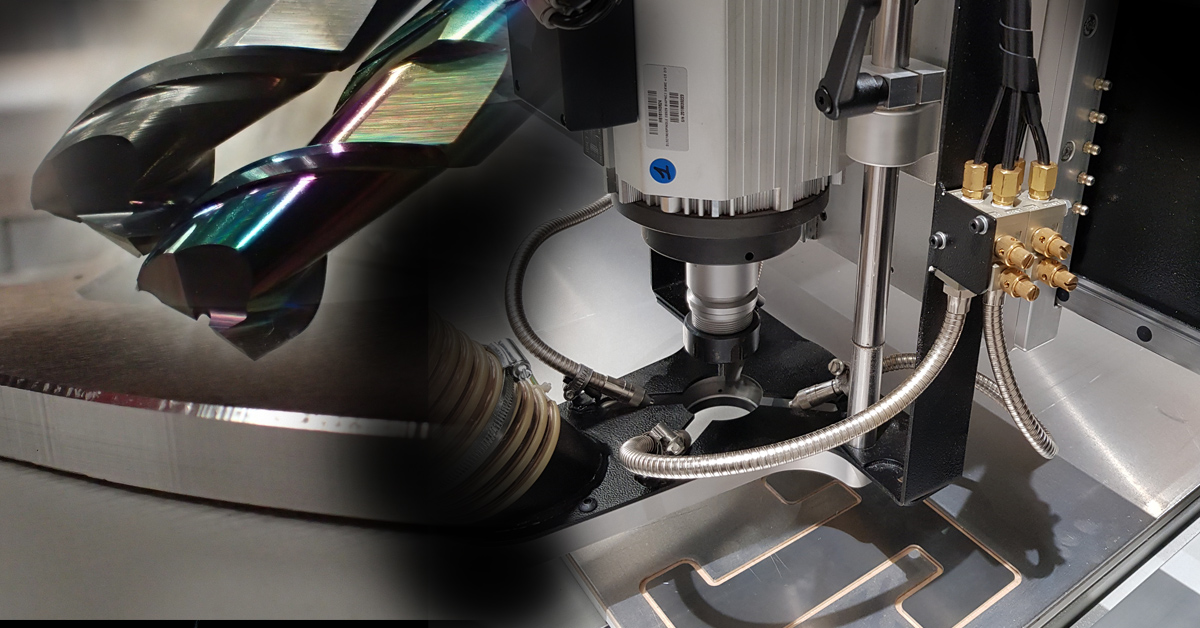
MAKE MORE WITH CORREX
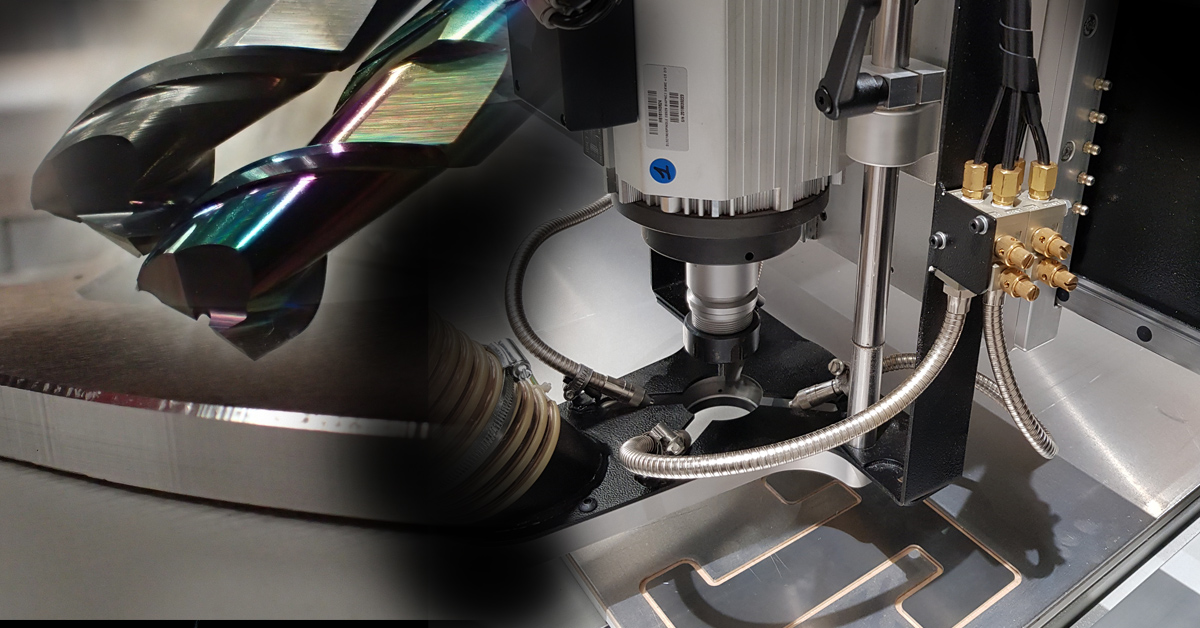
HOW SHOULD I APPROACH CUTTING OF SOLID SURFACE MATERIALS, CORIAN, AVONITE, THAT KIND OF THING?
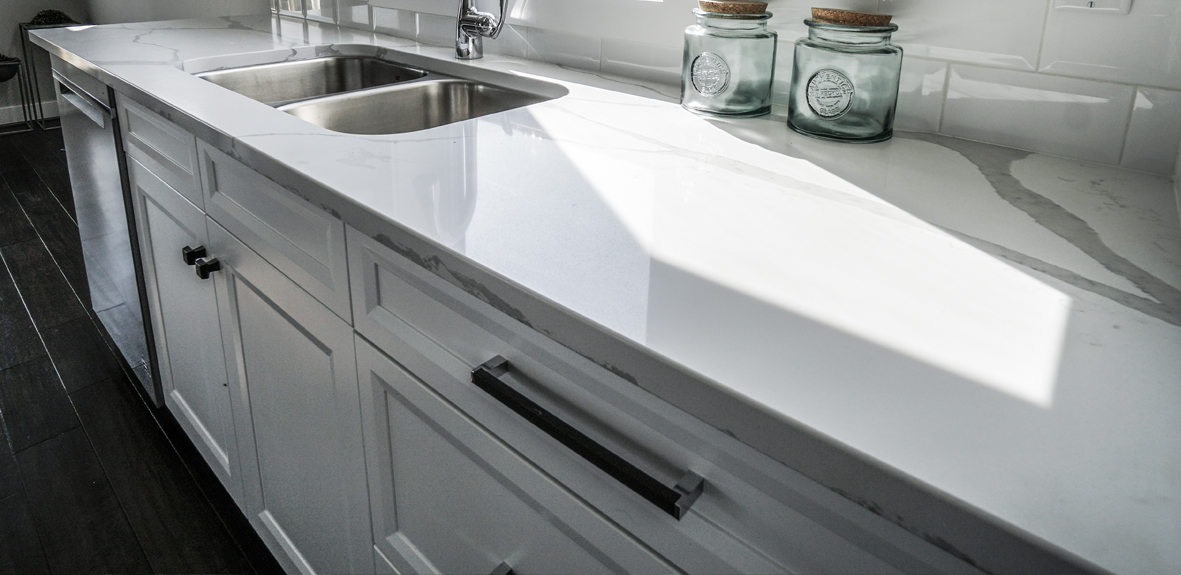
Achieving good results when you’re routing Woods, MDF, Laminates or Ply

HOW DO I GET THE BEST RESULTS POSSIBLE WHEN I’M CUTTING ACM ON MY CNC ROUTER?
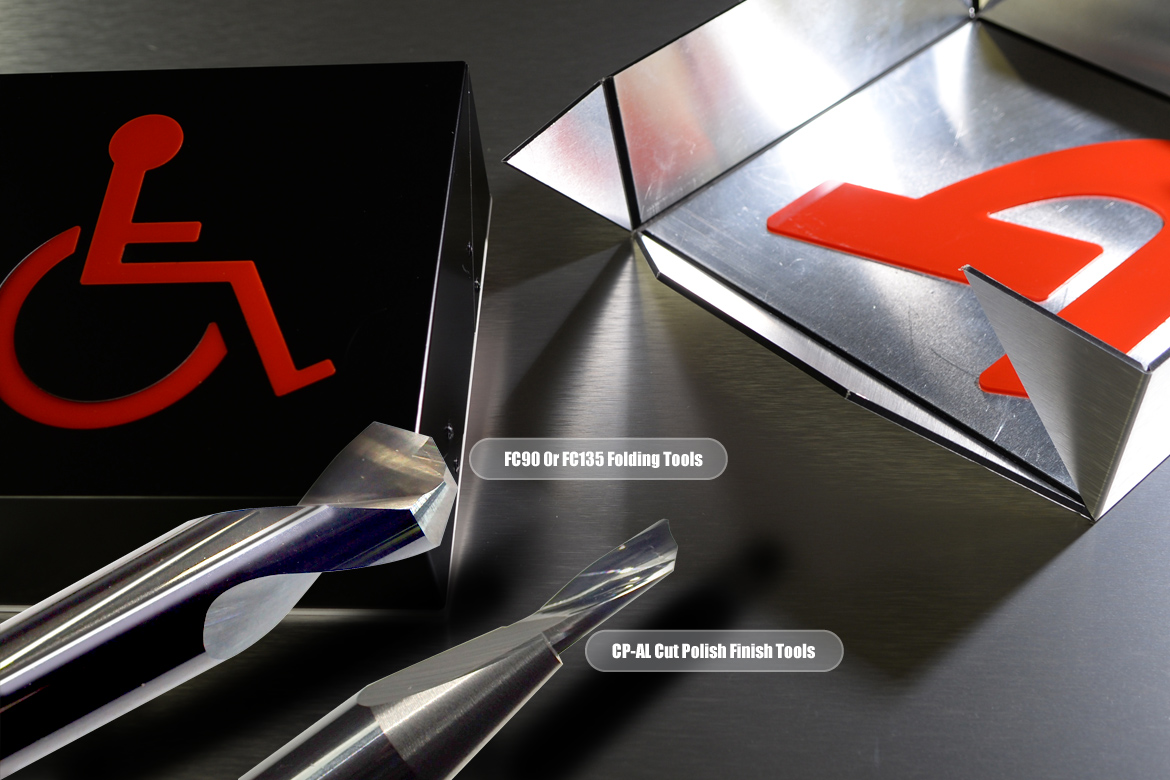
HOW CAN I GROW MY SIGNAGE AND GRAPHICS BUSINESS?
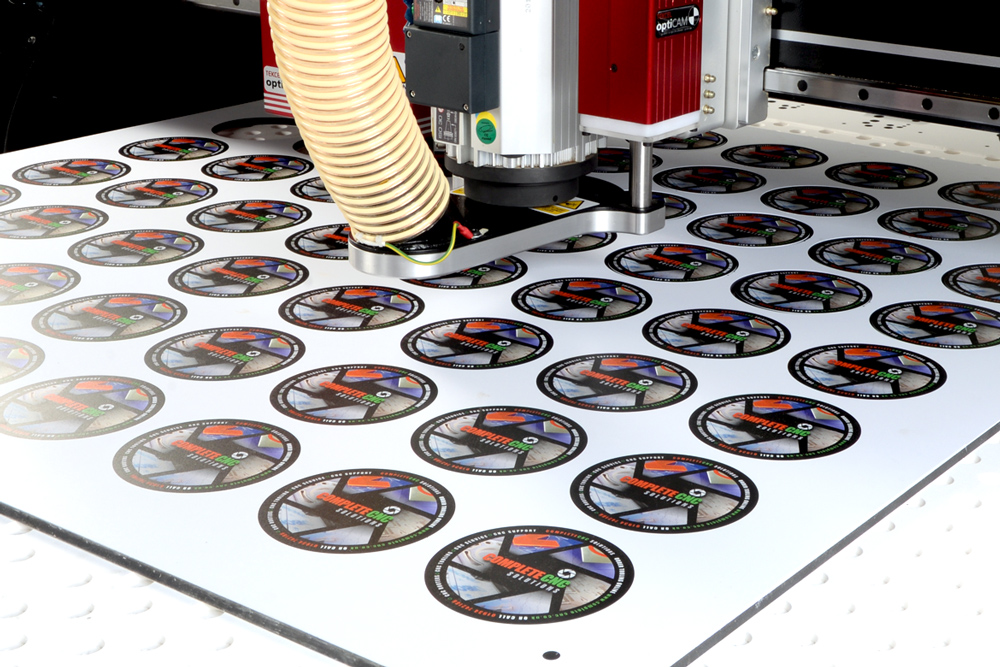
HOW CAN I REDUCE THE TIME I SPEND POLISHING THE EDGE ON THE OUTPUT FROM MY CNC ROUTER?
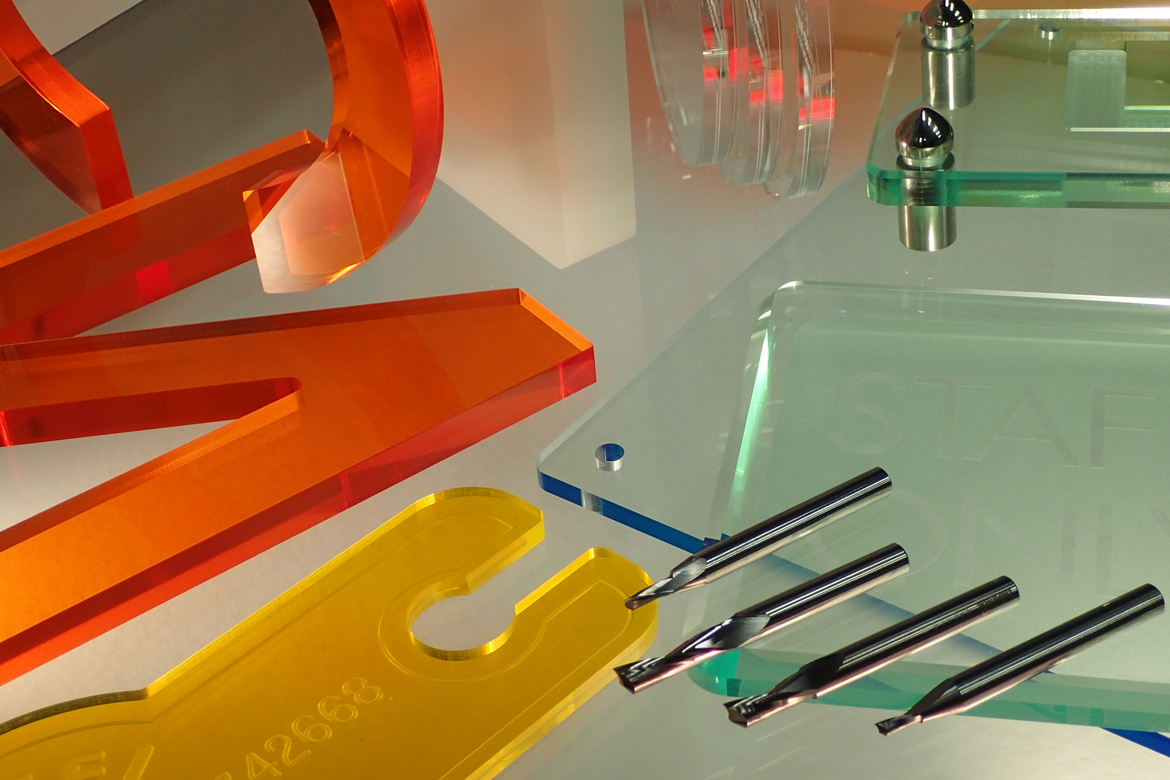
THE FLATTER THE BETTER
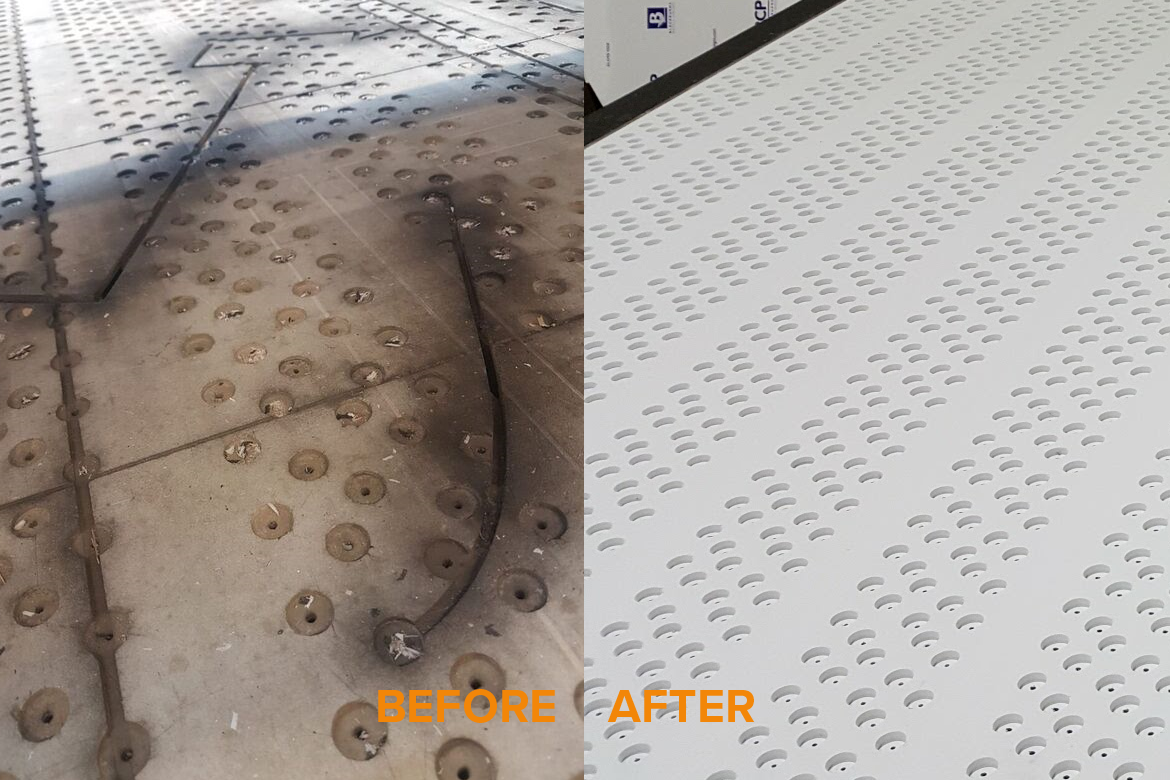
IS MY BUSINESS READY TO BUY A CNC ROUTER?
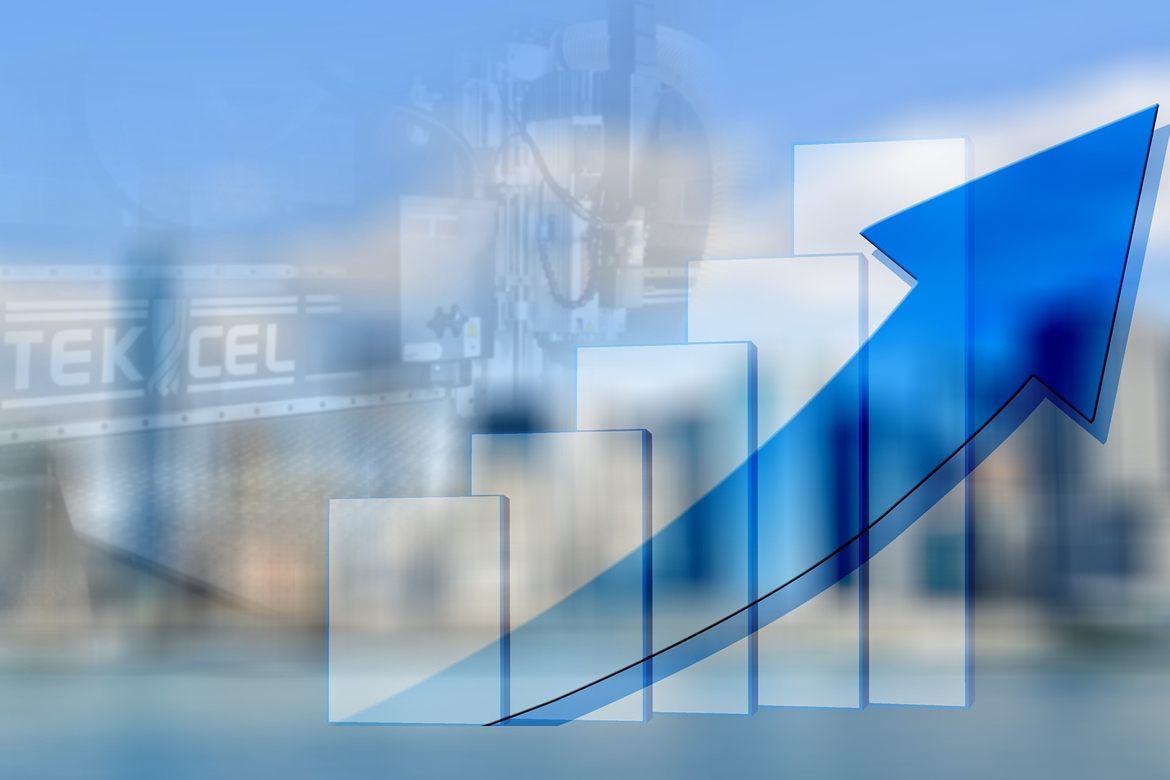
HEARD AT A TRADE SHOW
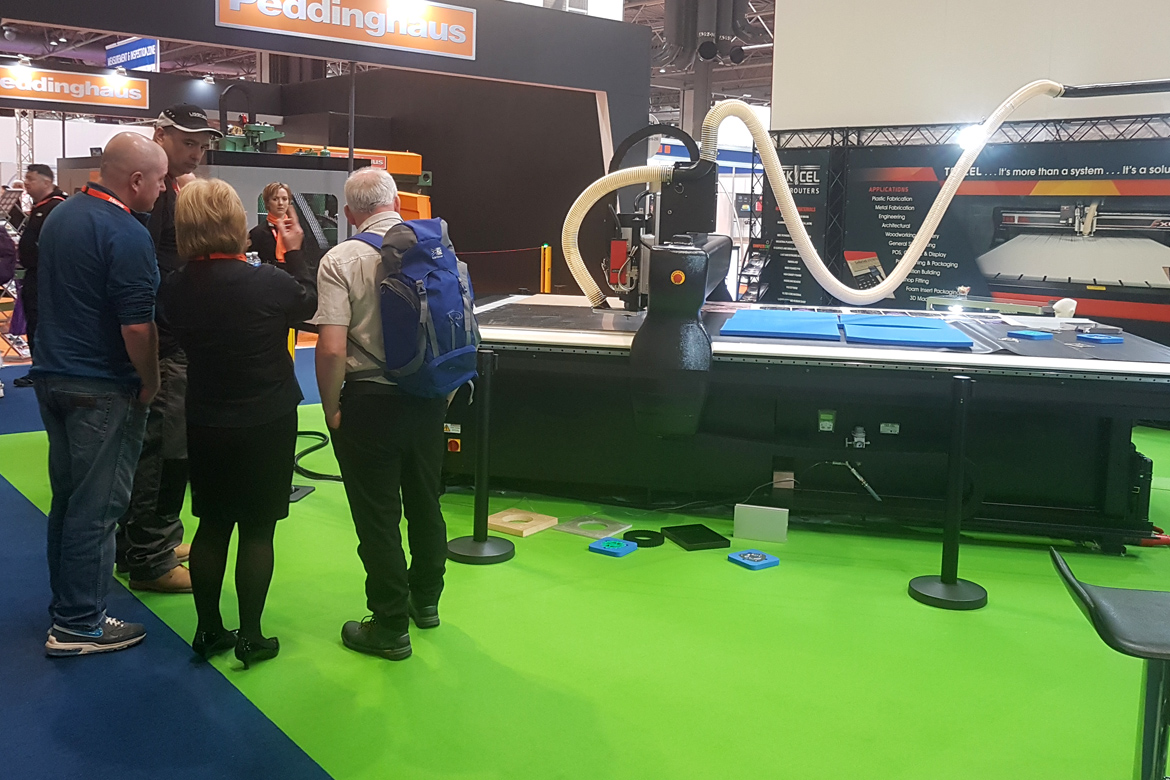
THE IMPORTANCE OF CHANGING CNC ROUTER COLLETS REGULARLY
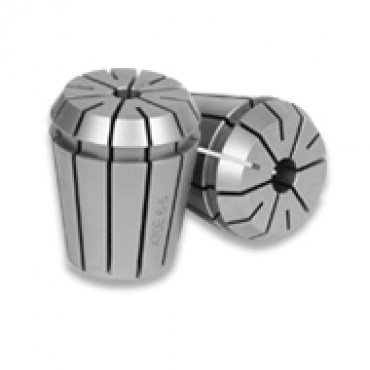
WITH YOU ALL THE WAY
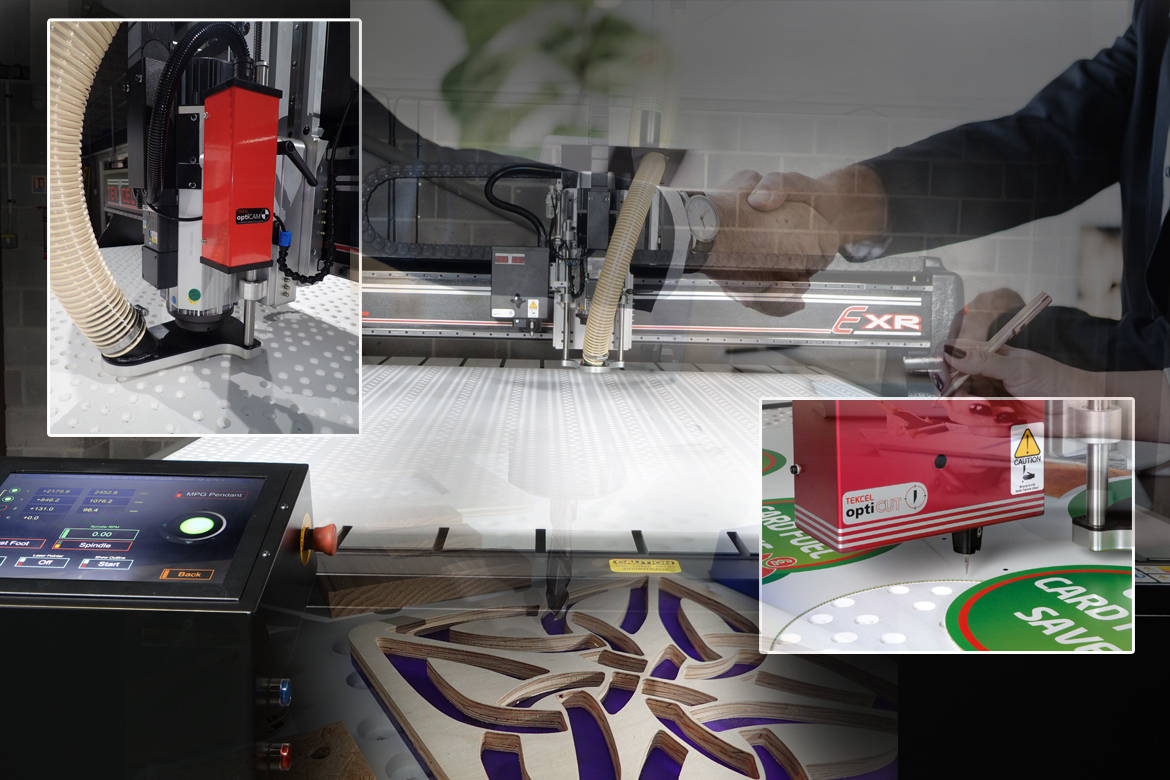