CUSTOMER LOGIN
What is an ATC and why do I need one?
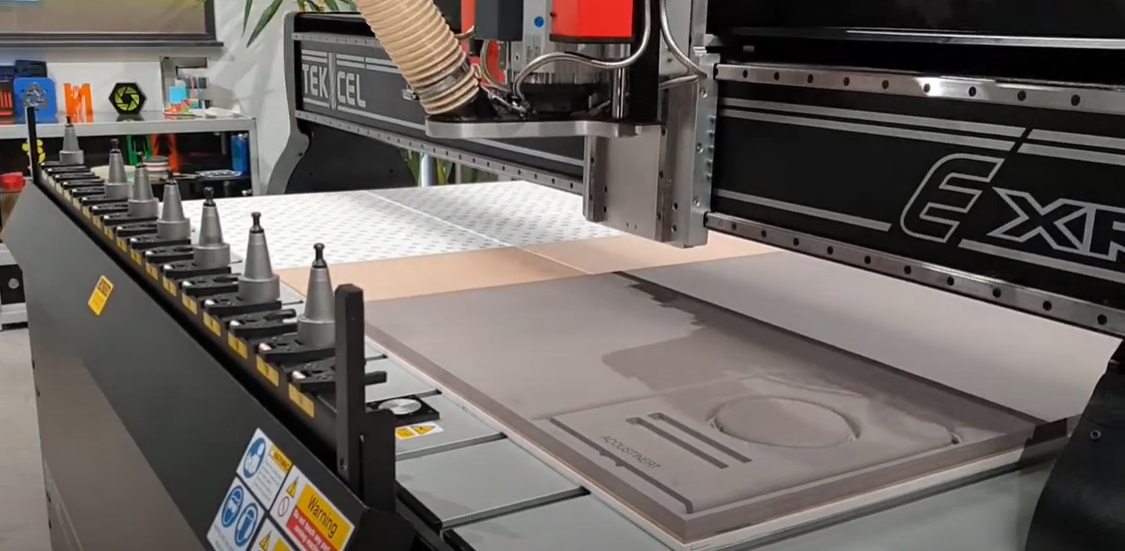
What is an ATC and why do I need one?
In today's fast-paced manufacturing environment, efficiency and productivity are paramount. One innovation that significantly contributes to these goals is the Automatic Tool Changer (ATC). By streamlining the process of switching tools during machining operations, ATCs save valuable time, reduce labour costs, and increase the overall output.
The Tekcel ATC is integrated into all their CNC (Computer Numerical Control) machines, allowing for the rapid and automatic switching of cutting tools. These tools can range from drills and mills to grinders and lathes, depending on the specific needs of the machining process.
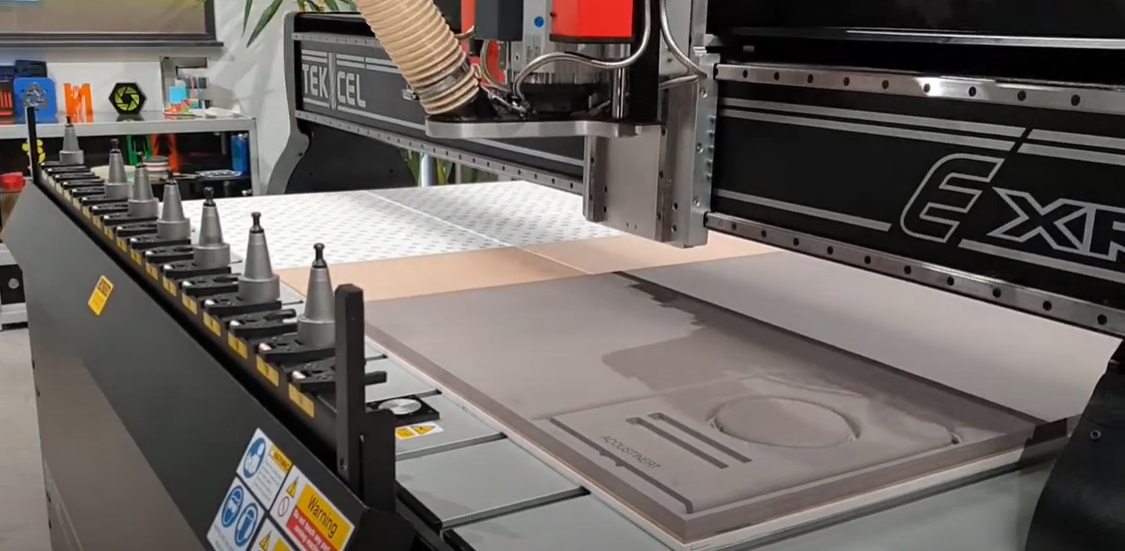
How Does an Automatic Tool Changer Work?
ATCs operate through a sophisticated sequence of mechanical and software-driven actions. Here's a simplified breakdown of the process:
1.Tool Storage: Tools are best stored in a linear Pop Up Pop Down tool rack, each in a specific numbered bay.
2.Tool Selection: When a new tool is needed, the CNC machine sends a command to the ATC, which generates a precise move to the position for the required tool.
3.Tool Exchange: The ATC retrieves the current tool from the spindle, places it back into its bay, and then selects the new tool.
4.Tool Placement: The new tool is securely fixed into the spindle, ready for the next machining operation.
Reasons to Use an Automatic Tool Changer
- Increased Productivity - One of the most compelling reasons to invest in an ATC is the significant boost in productivity. Manual tool changes are time-consuming and interrupt the workflow. ATCs can perform these changes in seconds, minimising downtime and keeping the machine running continuously.
- Enhanced Precision and Consistency - Manual tool changes can introduce errors due to human intervention. ATCs, being automated, ensure that each tool change is executed with high precision, maintaining the consistency and quality of the machining process.
- Versatility - Modern ATCs can handle a wide variety of tools, making them highly versatile. This adaptability allows manufacturers to take on more complex and varied projects without needing to manually switch tools frequently.
- Improved Safety - By automating the tool-changing process, ATCs reduce the need for manual intervention, thereby decreasing the risk of accidents and injuries on the shop floor.
Conclusion
Automatic Tool Changers are a powerful asset in any machining setup. They significantly increase productivity by reducing downtime, enhance precision by minimizing human error, offer substantial cost savings, and improve overall safety in the workplace.
Incorporating an Automatic Tool Changer into your CNC operations is a strategic move that can lead to significant improvements in productivity, precision, cost efficiency, versatility, and safety. As technology continues to advance, the role of ATCs in manufacturing will only become more vital, making any Tekcel CNC Router a sound investment for forward-thinking businesses.
Further Blog Posts
Avoid These CNC Pitfalls in Illuminated Signmaking
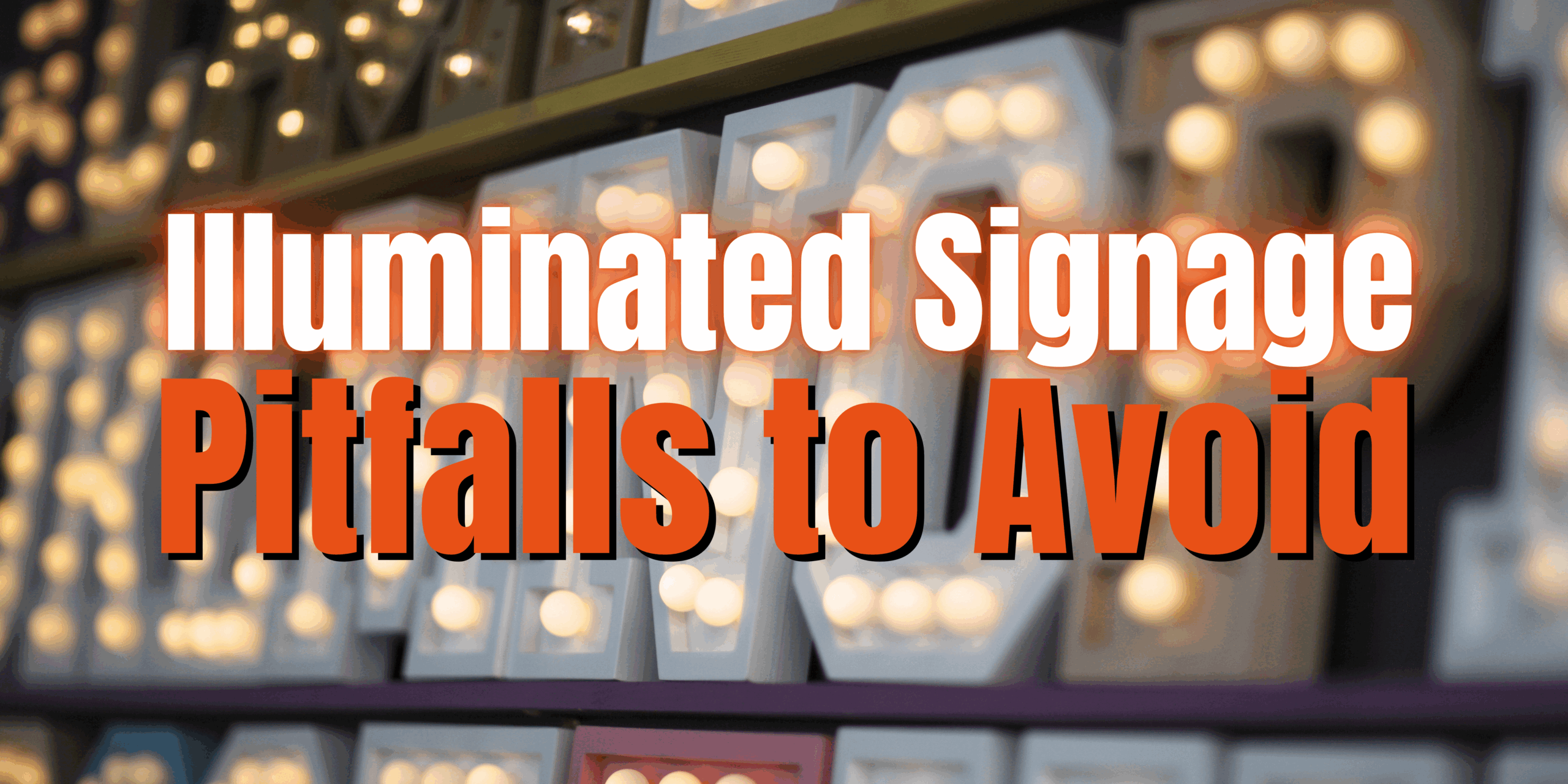
Essential CNC Router Tips for Cutting Acrylic
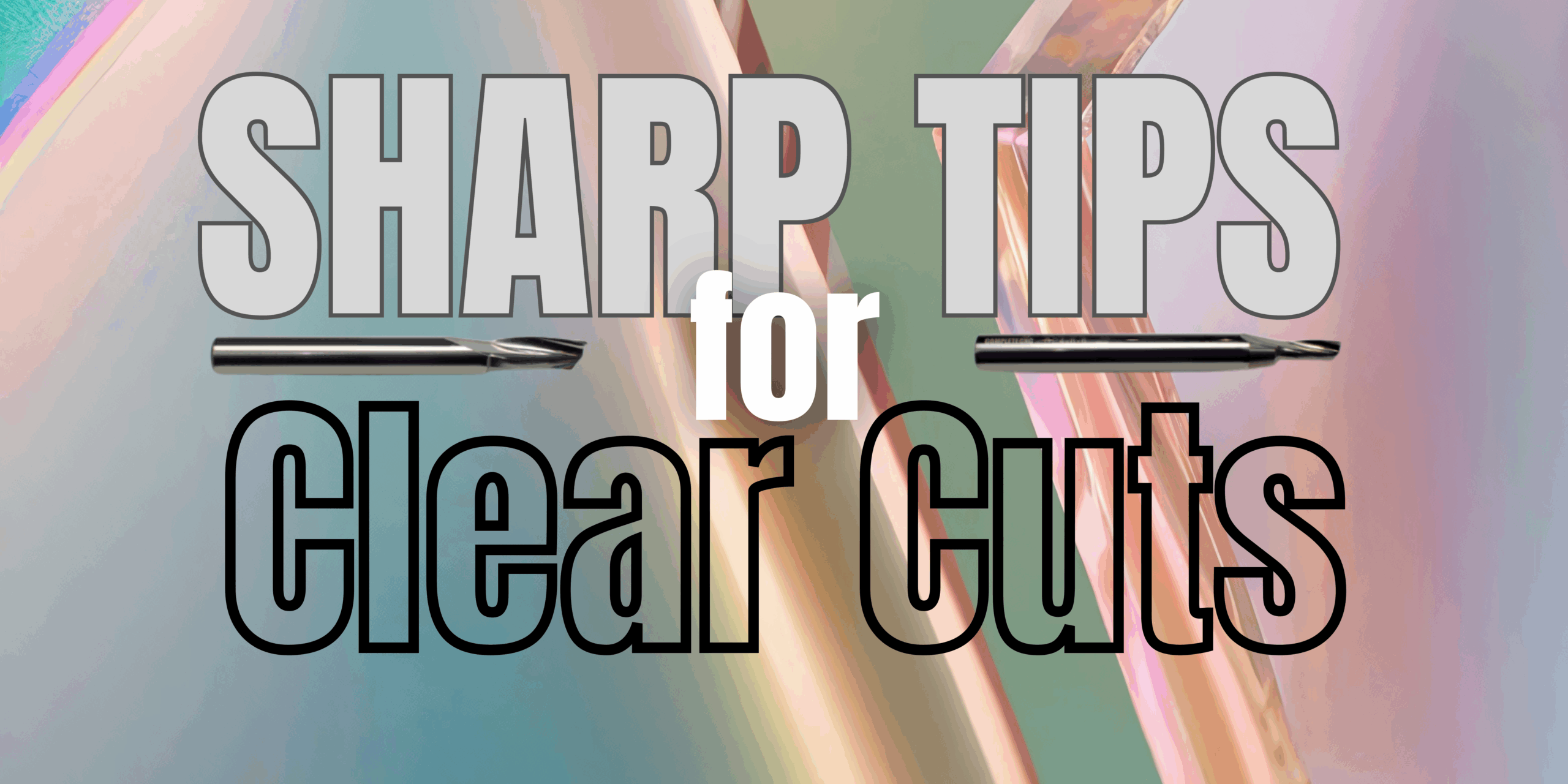
Nesting Your Way to Better Margins in Joinery
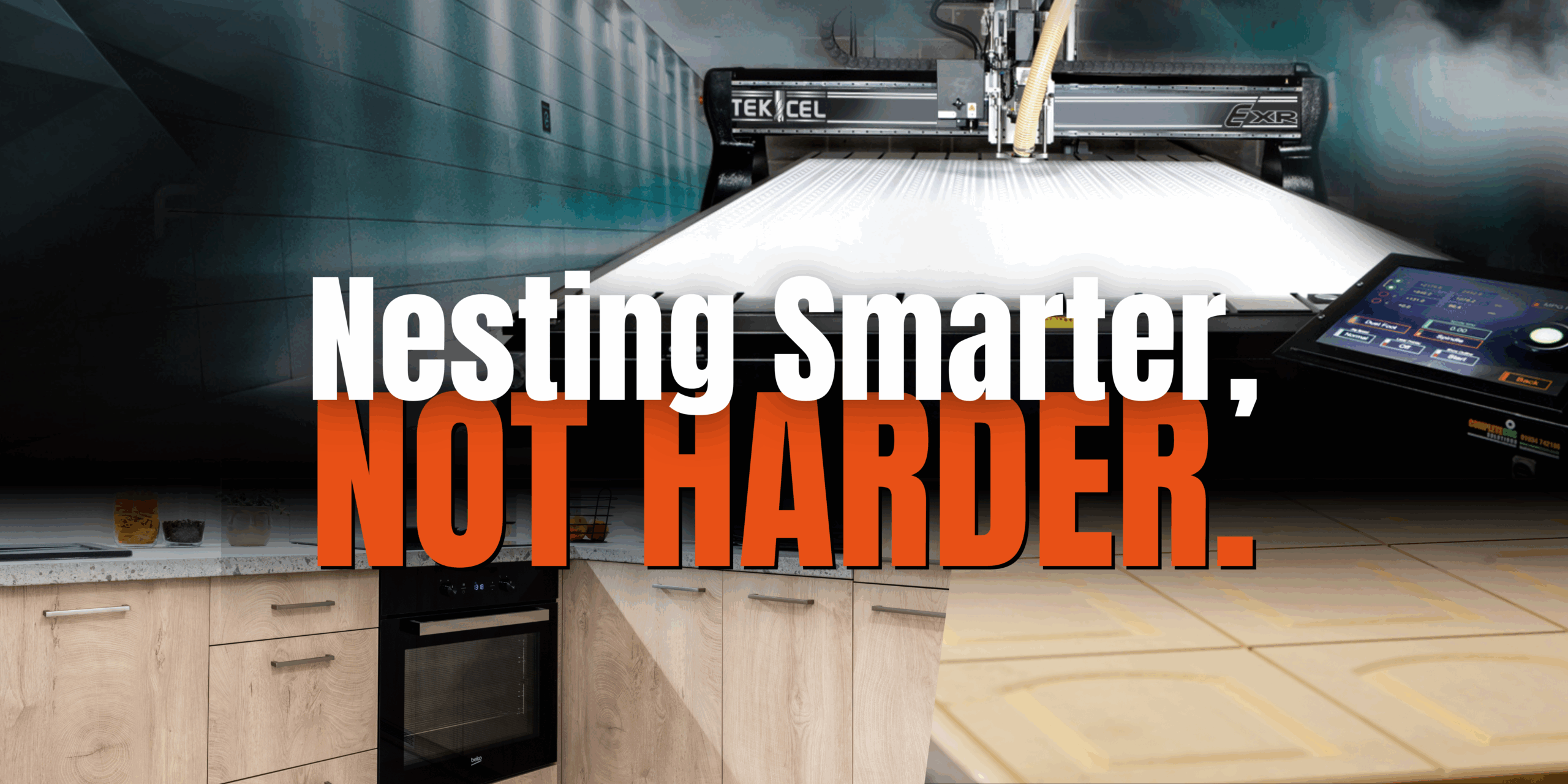
Is Your CNC Router Holding Your Business Back?
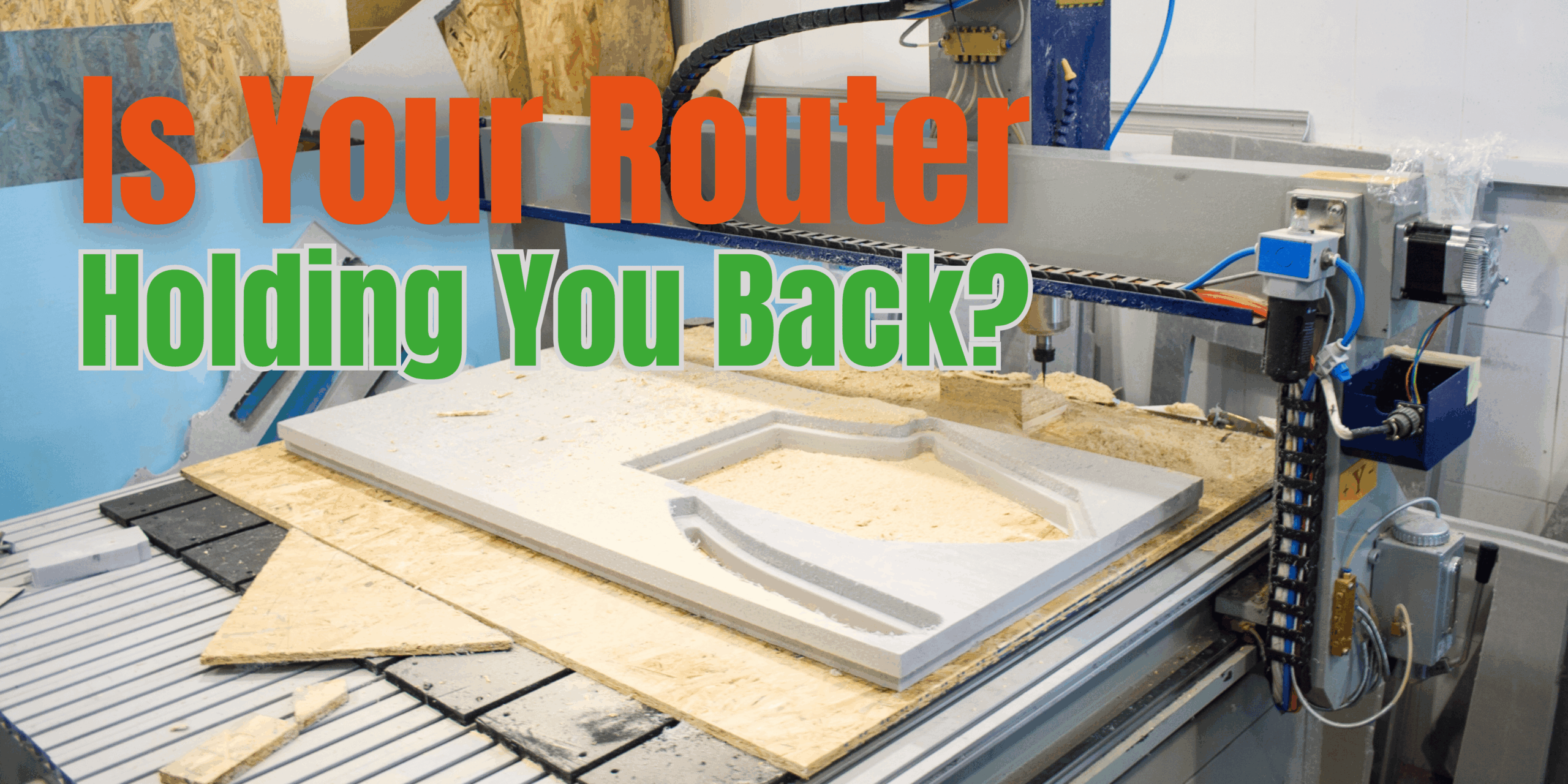
Can a CNC Router Cover Lots of Different Industries?
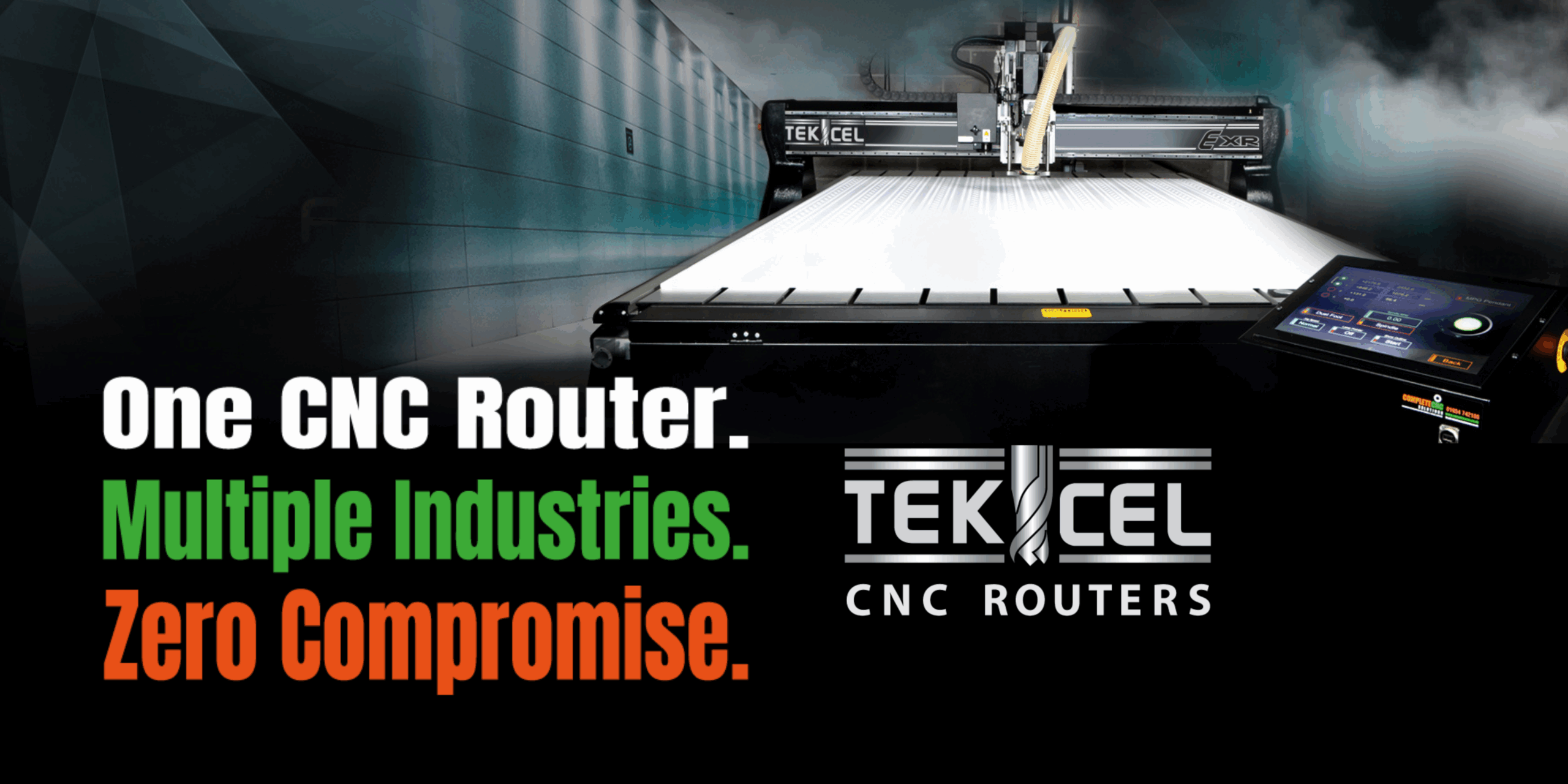
Why Case Makers Should Be Cutting Foam In-House With a CNC Router
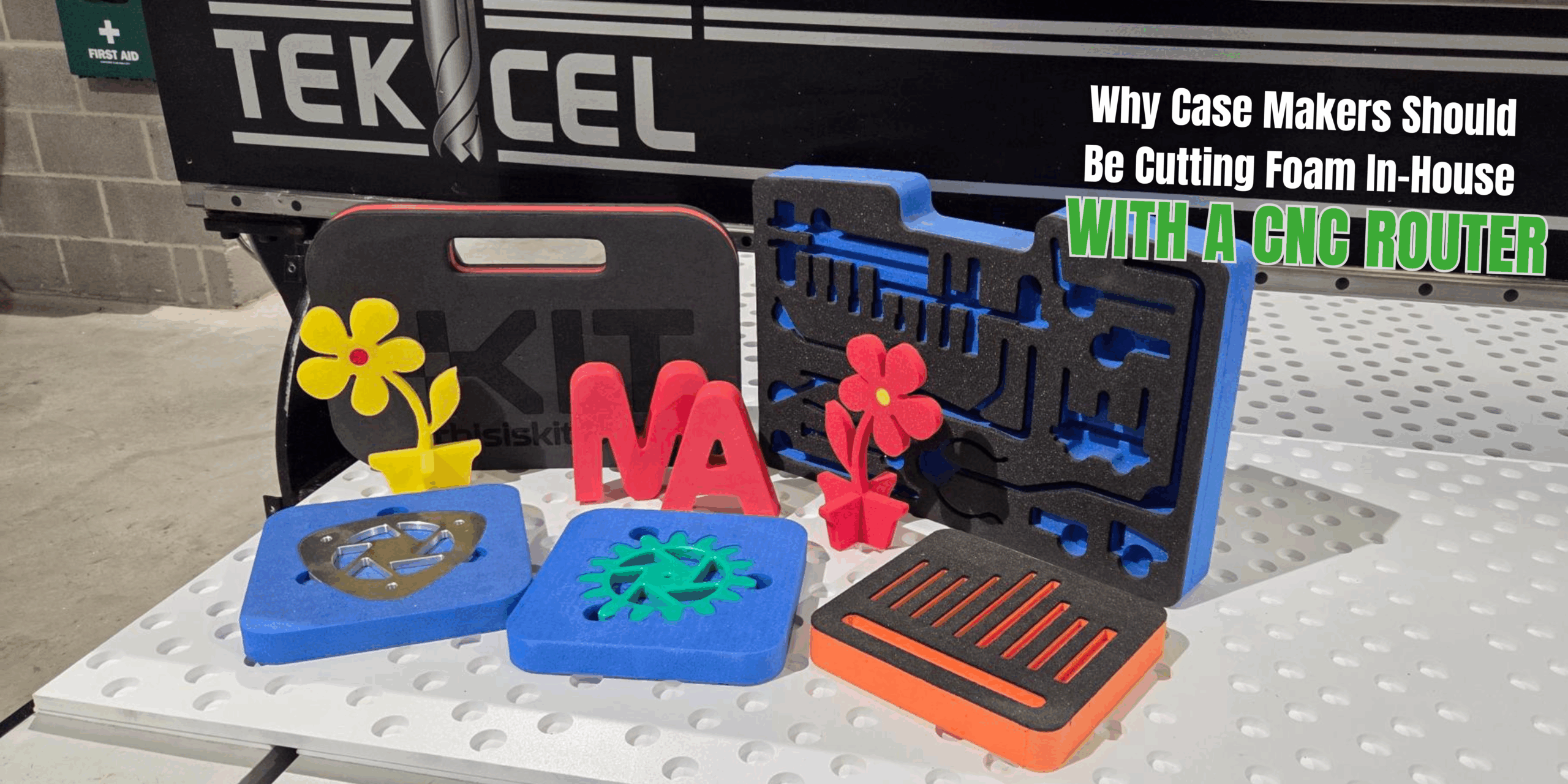
FAQ: What Tips Do You Have For Cutting MDF?
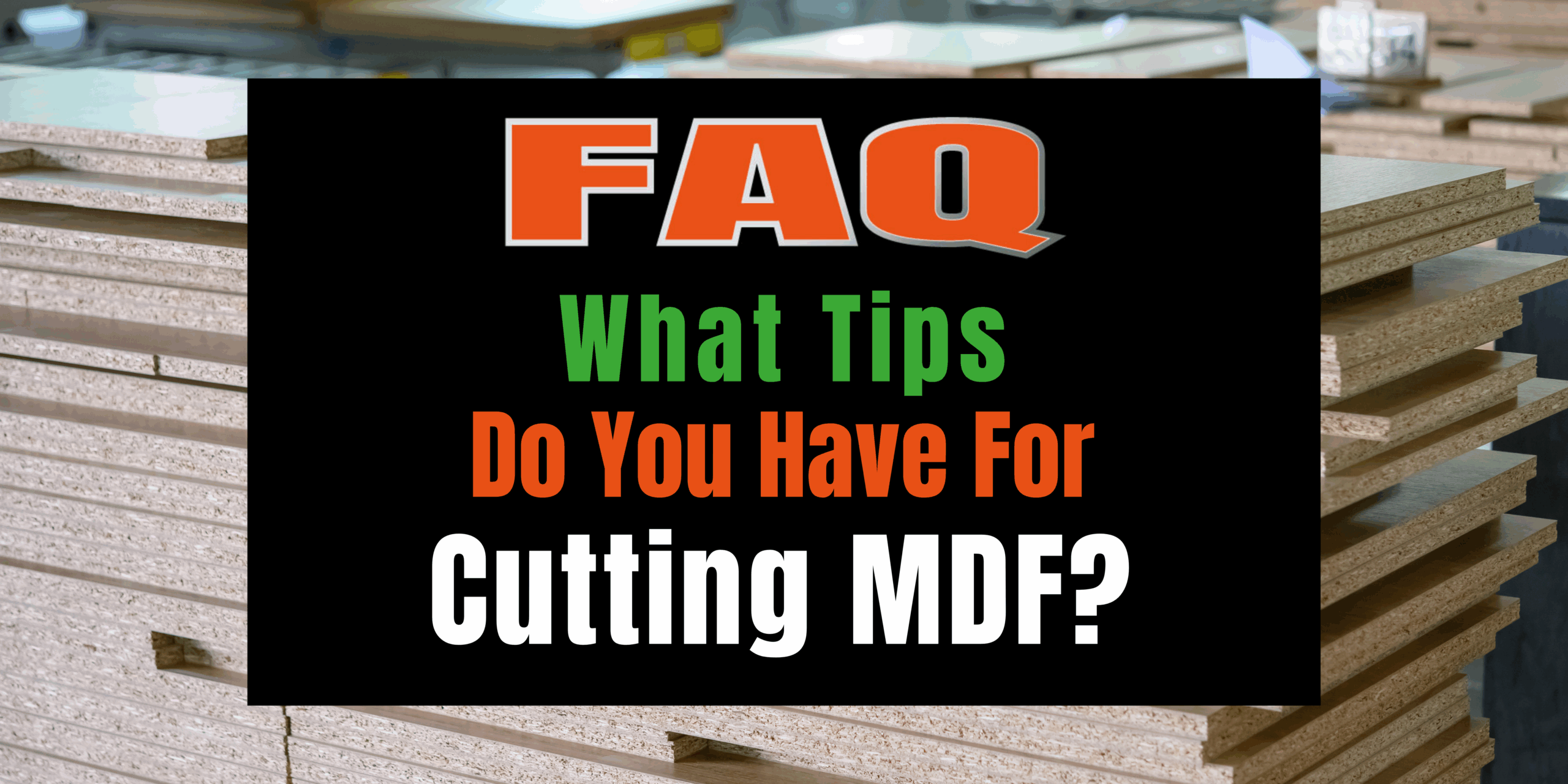
Thinking About Investing in a CNC Router?
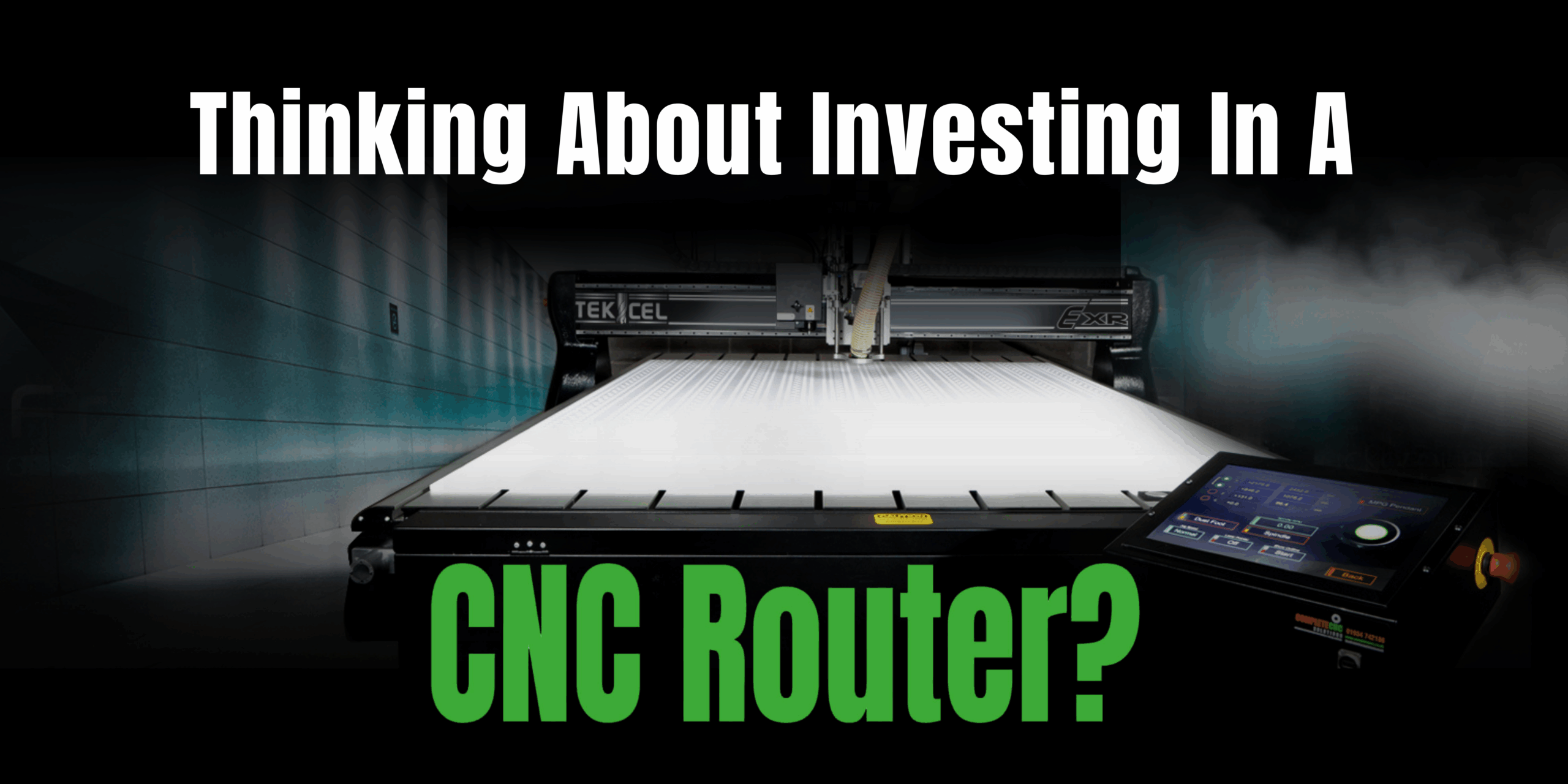
Why Tekcel EXR is the CNC Router You Need
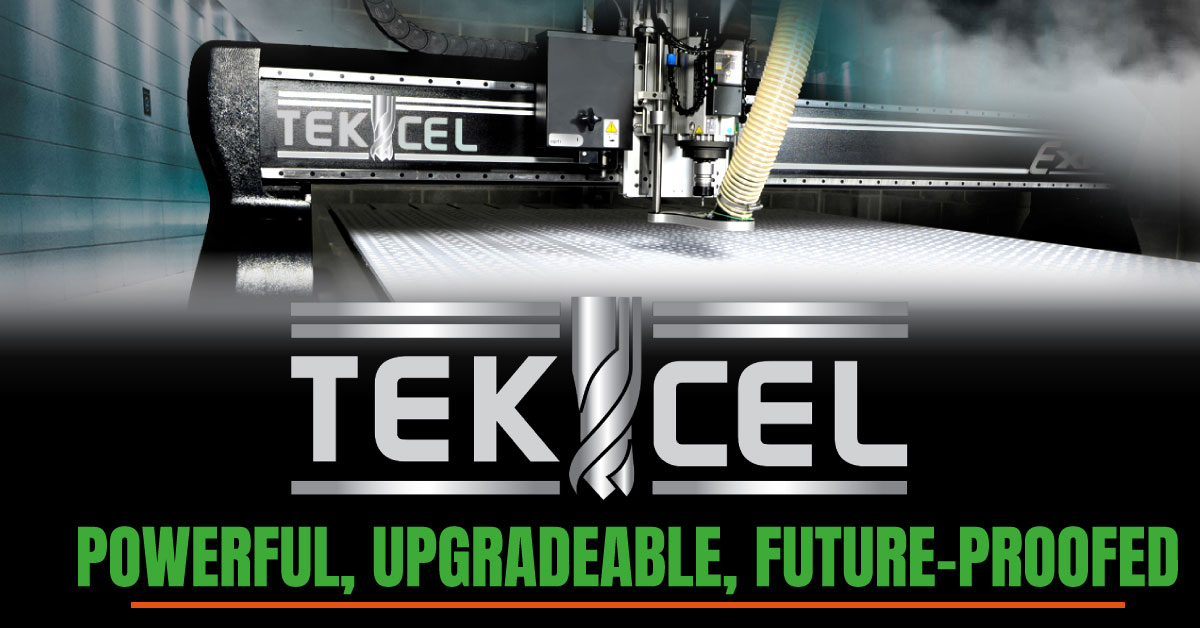
CNC Woodworking Without The Headaches
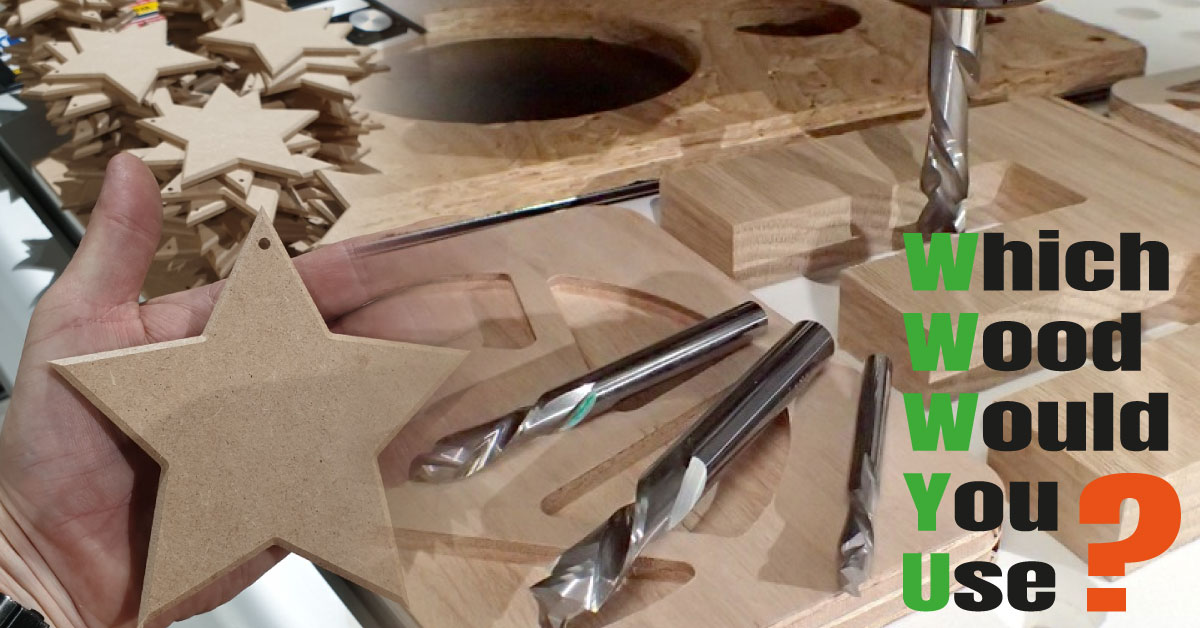
No More Botched Cuts on Plastics & Acrylics!
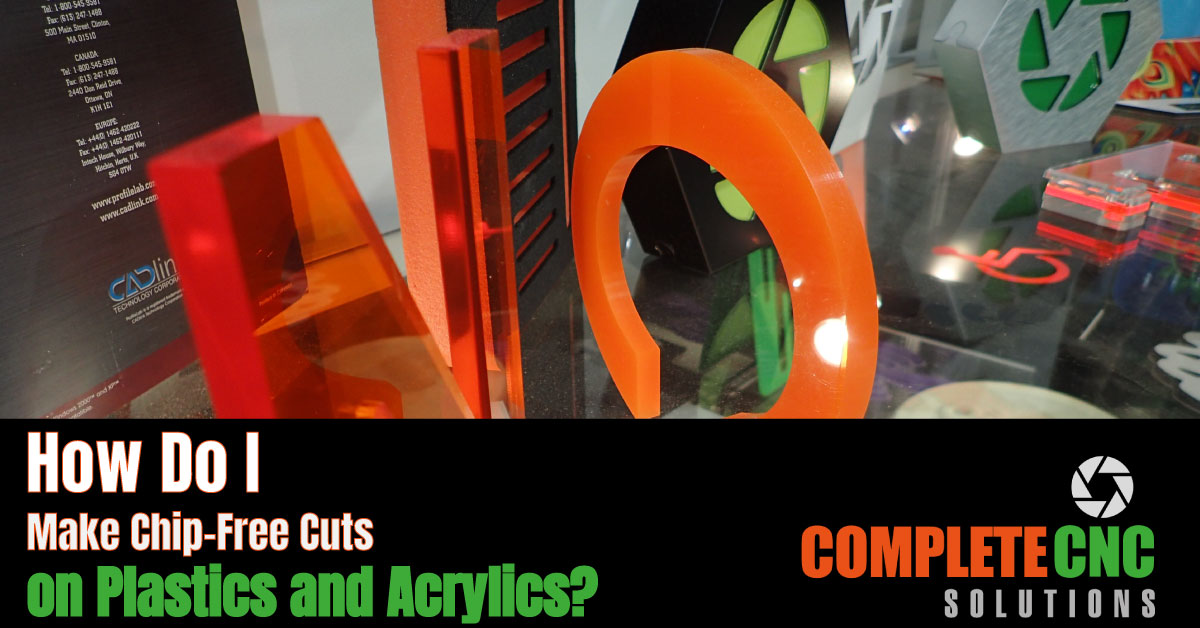
Struggling with Tool Wear?
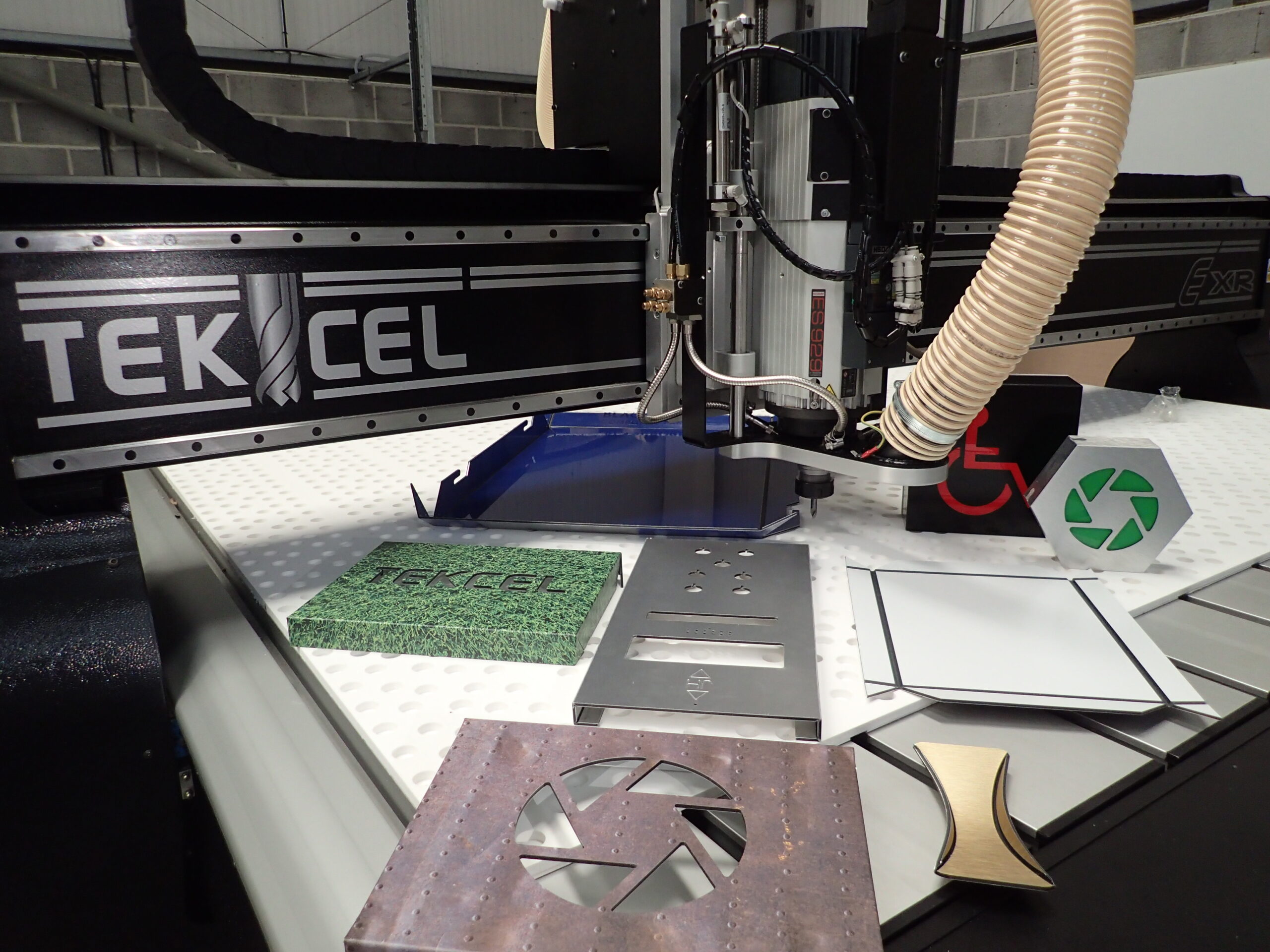
How to Successfully Cut Small Shapes Without Them Moving
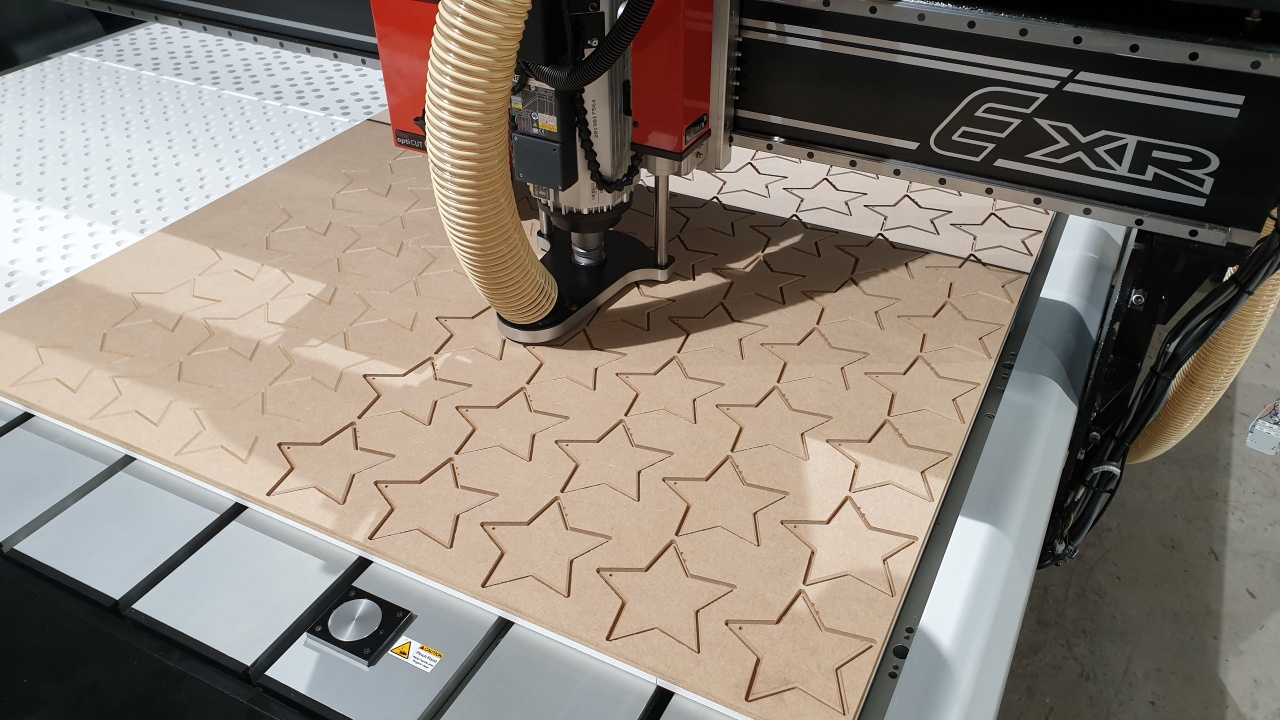
Documenting CNC Router Settings and Processes for Future Success
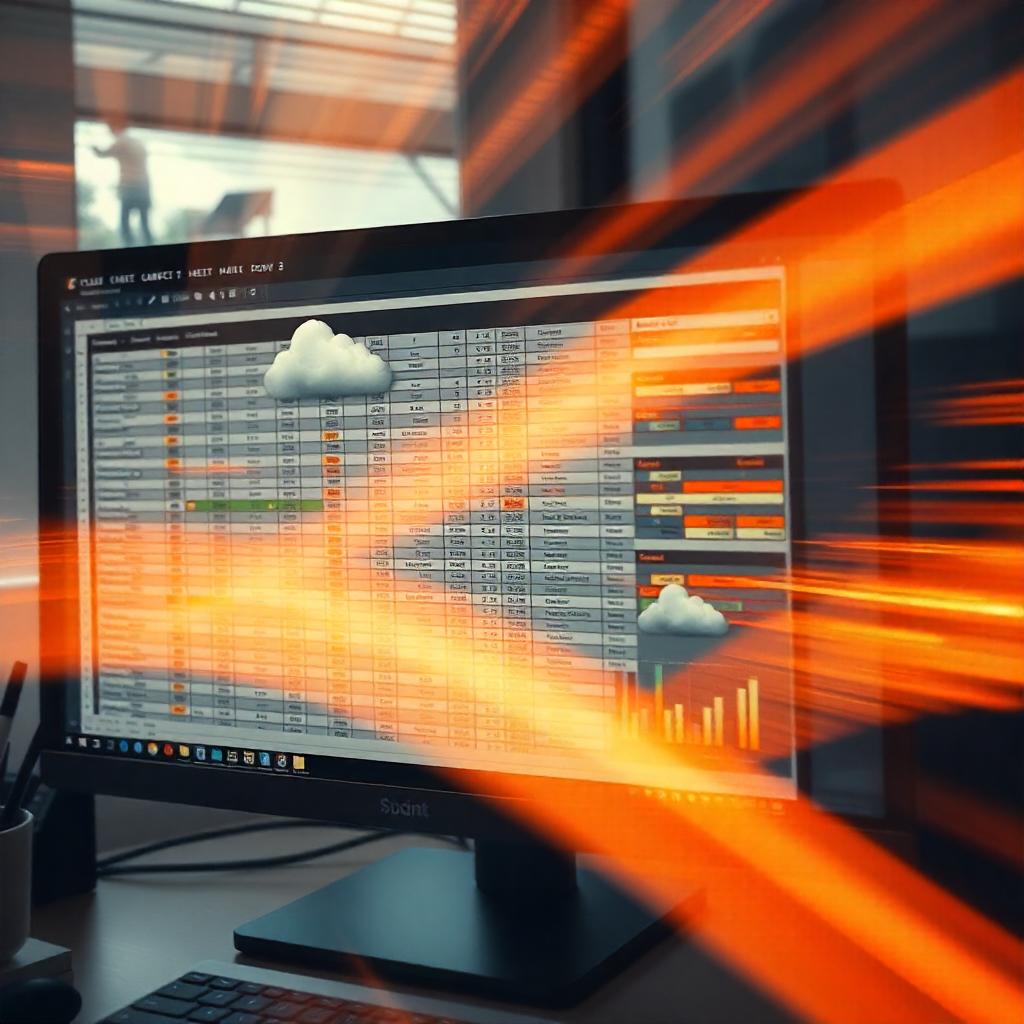
Training Tailored For Success With Your Tekcel CNC Router
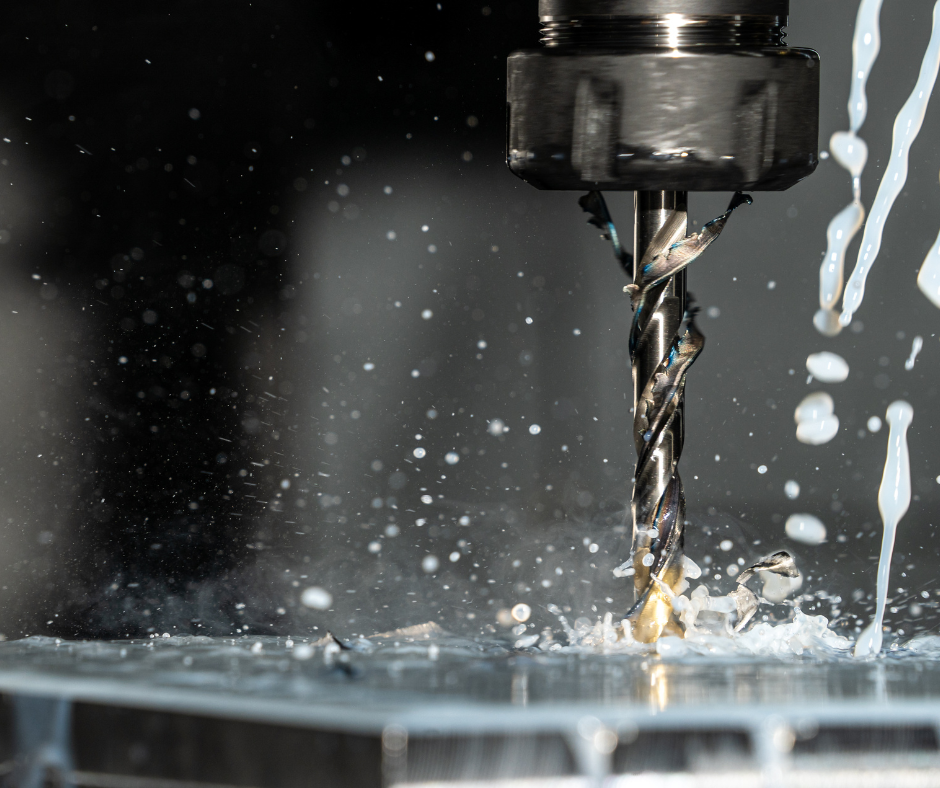
Stay Ahead with Software Updates for Your Tekcel CNC Router
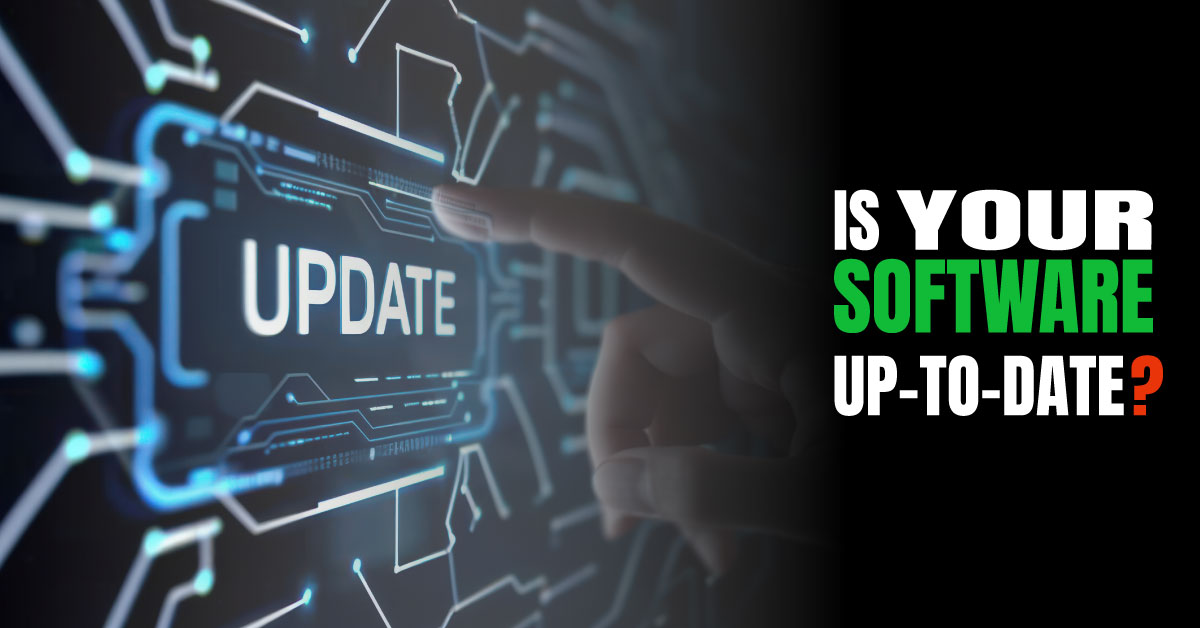
Revolutionise Signage with Tekcel CNC and Precision ACM Tooling
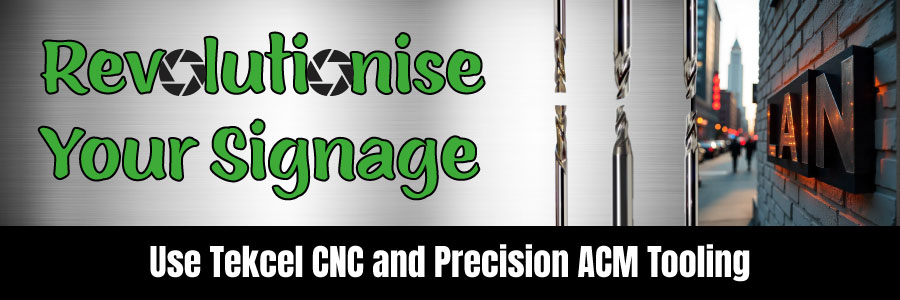
Cutting it Close? Know When to Change Your Collet for Safe, Sharp Results
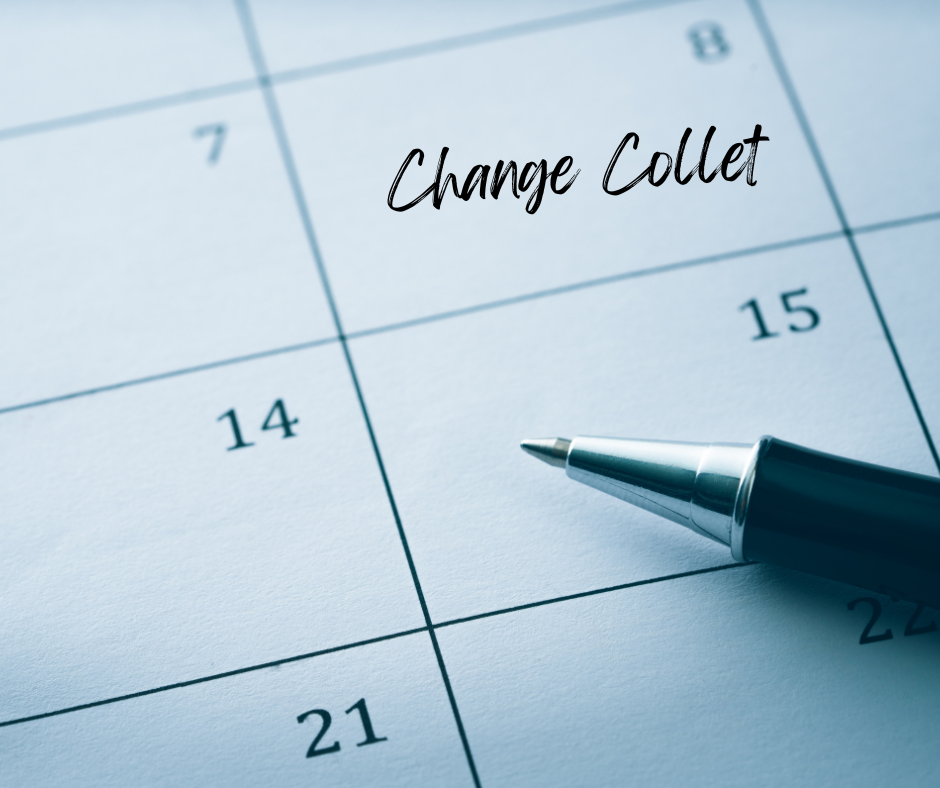
How to Avoid Burning and Furring When Cutting Wood with a CNC Router
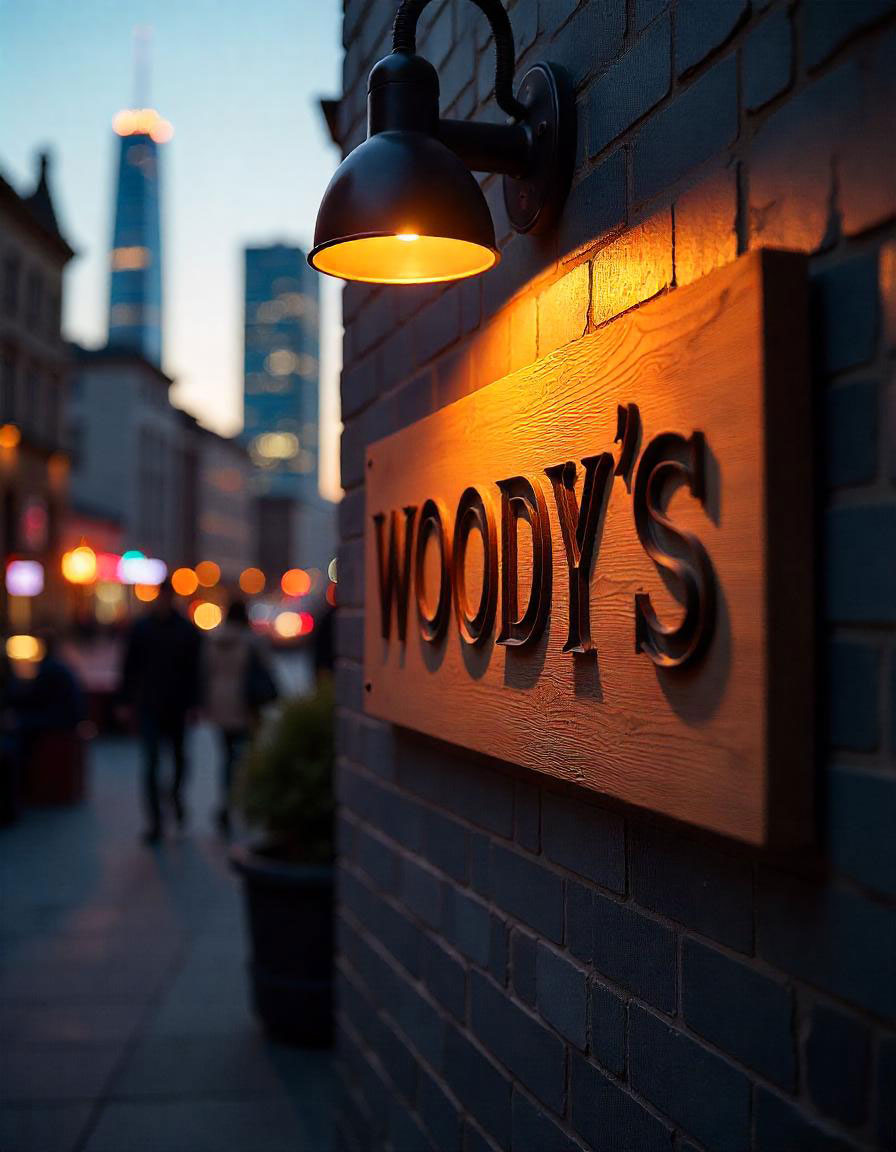
How to choose the right CNC tool for the job/material
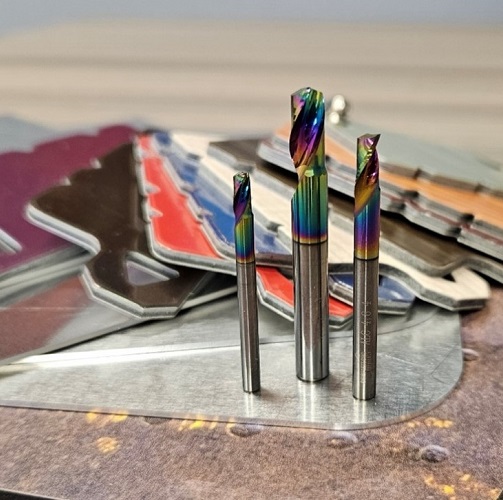
Which CNC Router covers all the bases for a signage manufacturer?
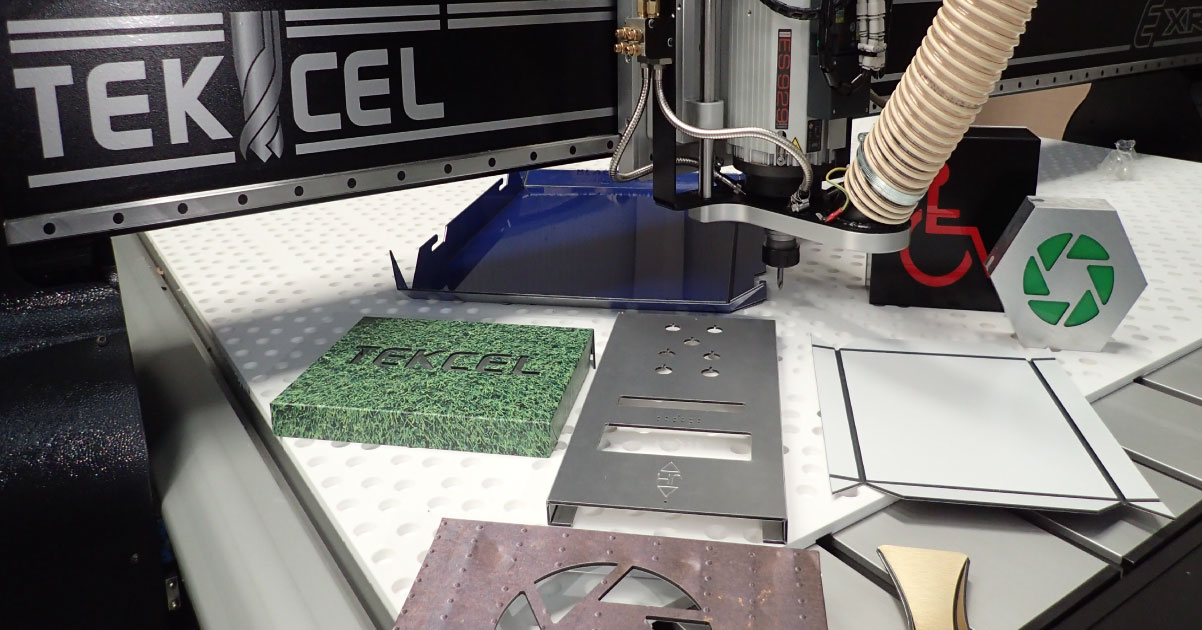
The Tekcel – High Pressure Mist Coolant System for Metal Cutting
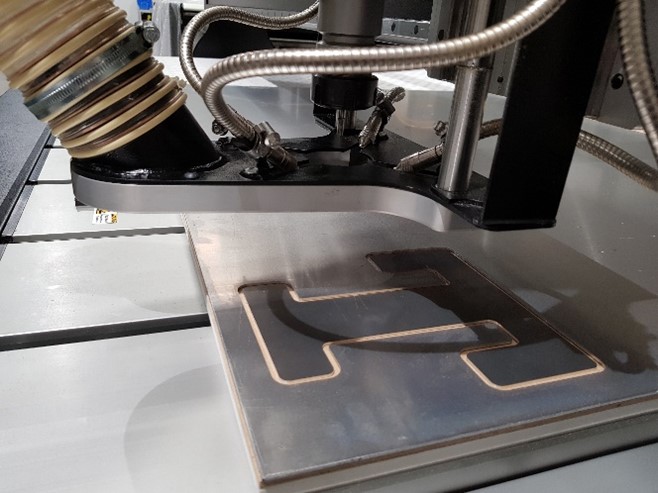
Tekcel CNC Routers – Furniture & Woodworkers dream machine
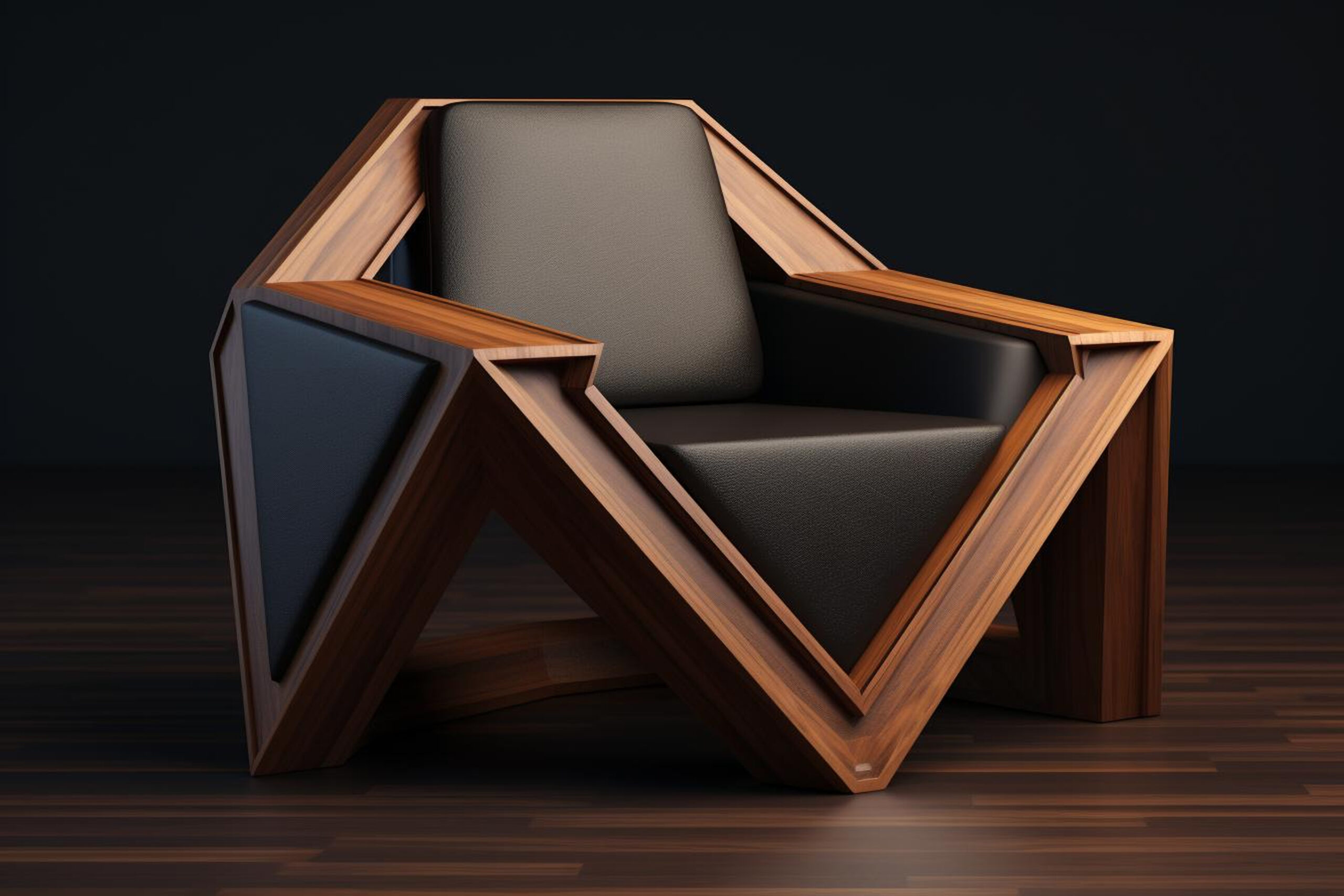
Start with a “Tekcel CNC” for the best finish…
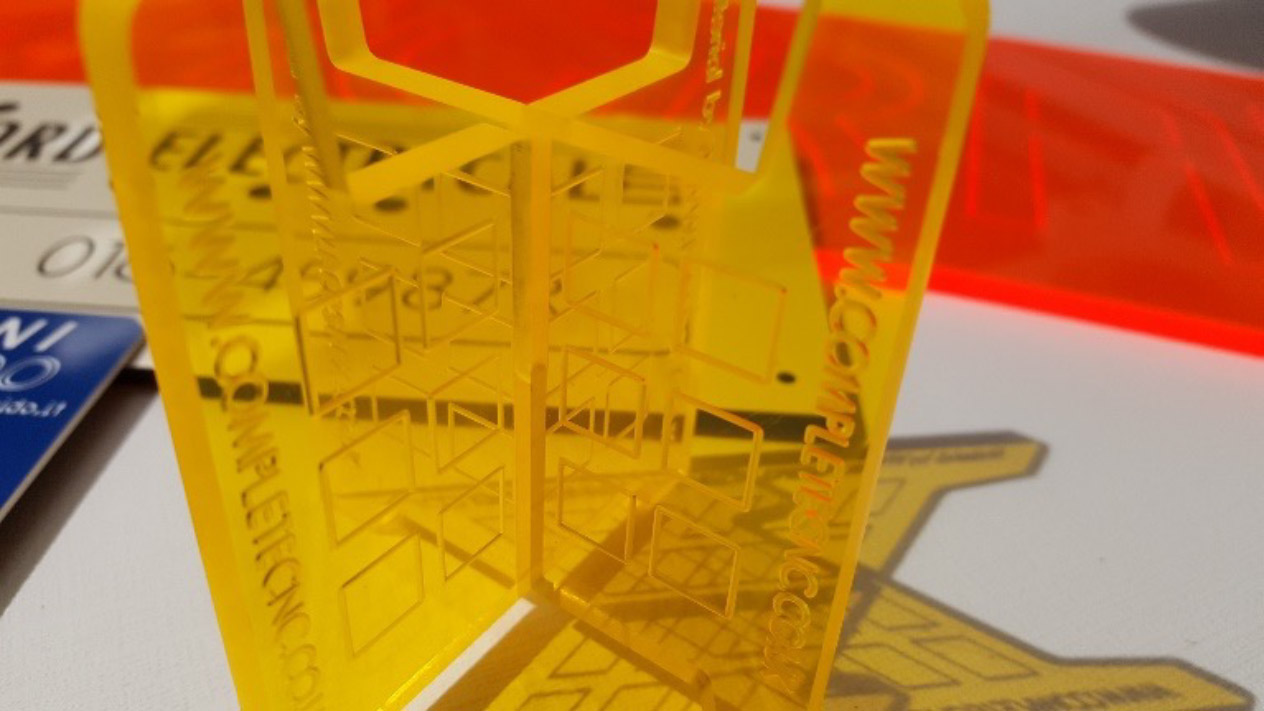
Under the Bonnet of a Tekcel EXR CNC Router
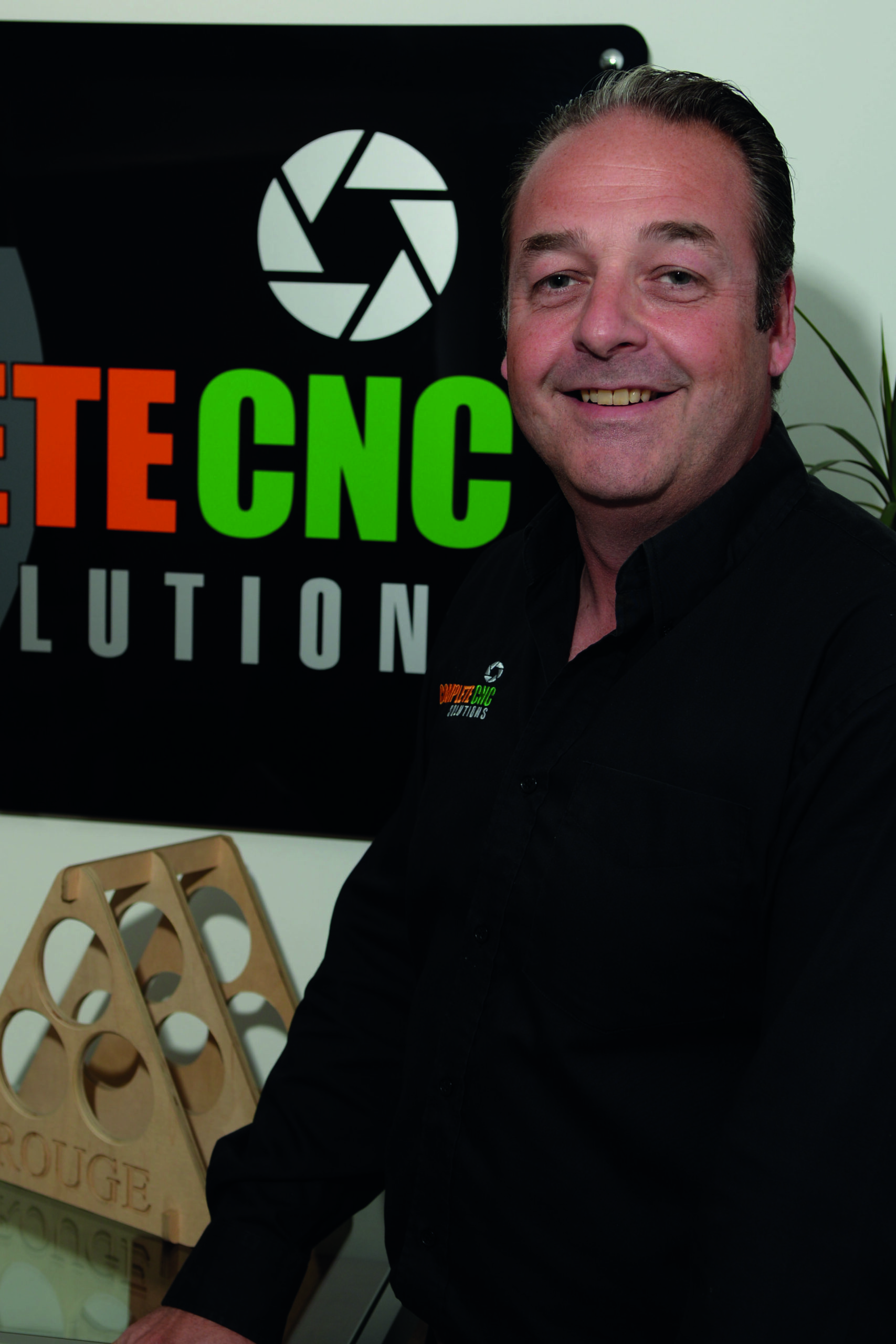
How to Skim the MDF Sacrificial Bed on your Tekcel CNC Router: A Step-by-Step Guide
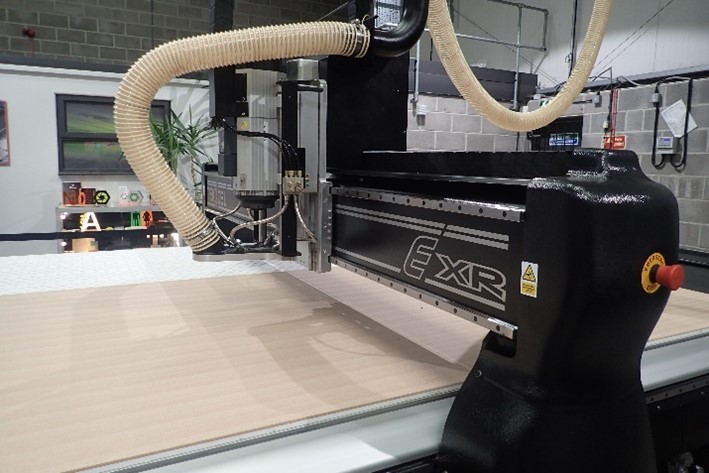
What is an ATC and why do I need one?
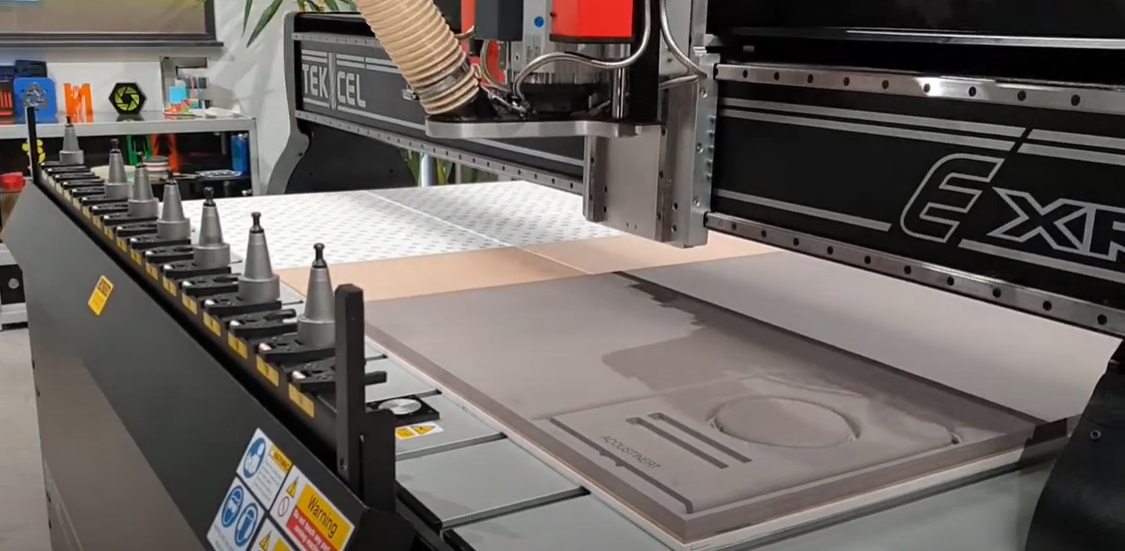
Tekcel CNC for ACM (Aluminium Composite Material) Signage:
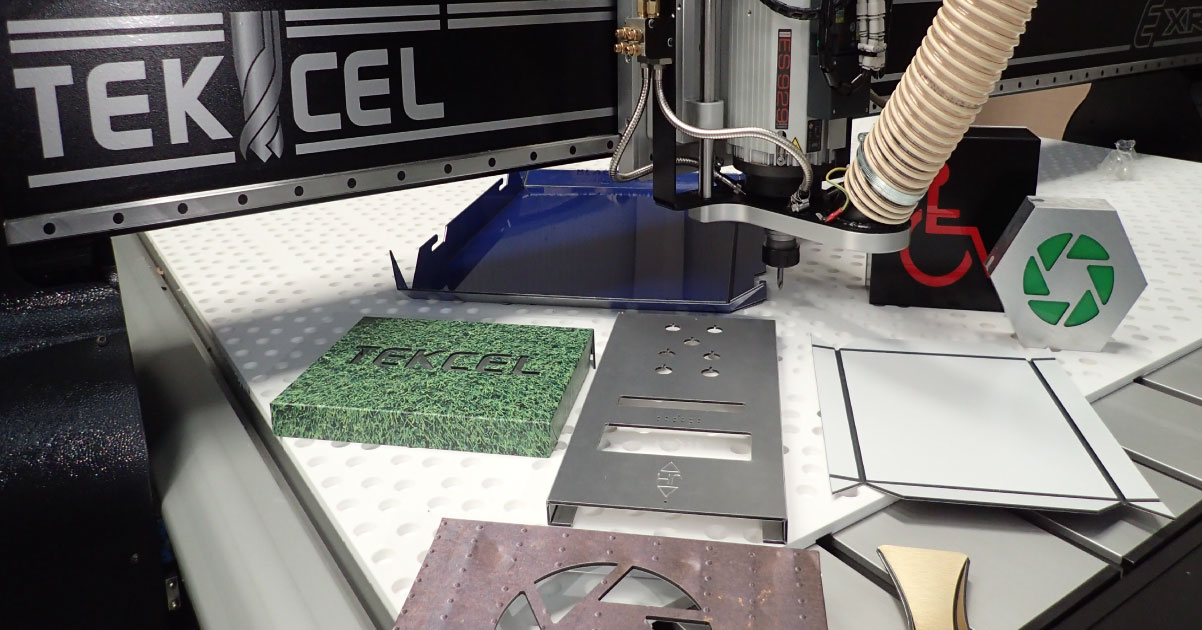
The Benefits of Acrylic
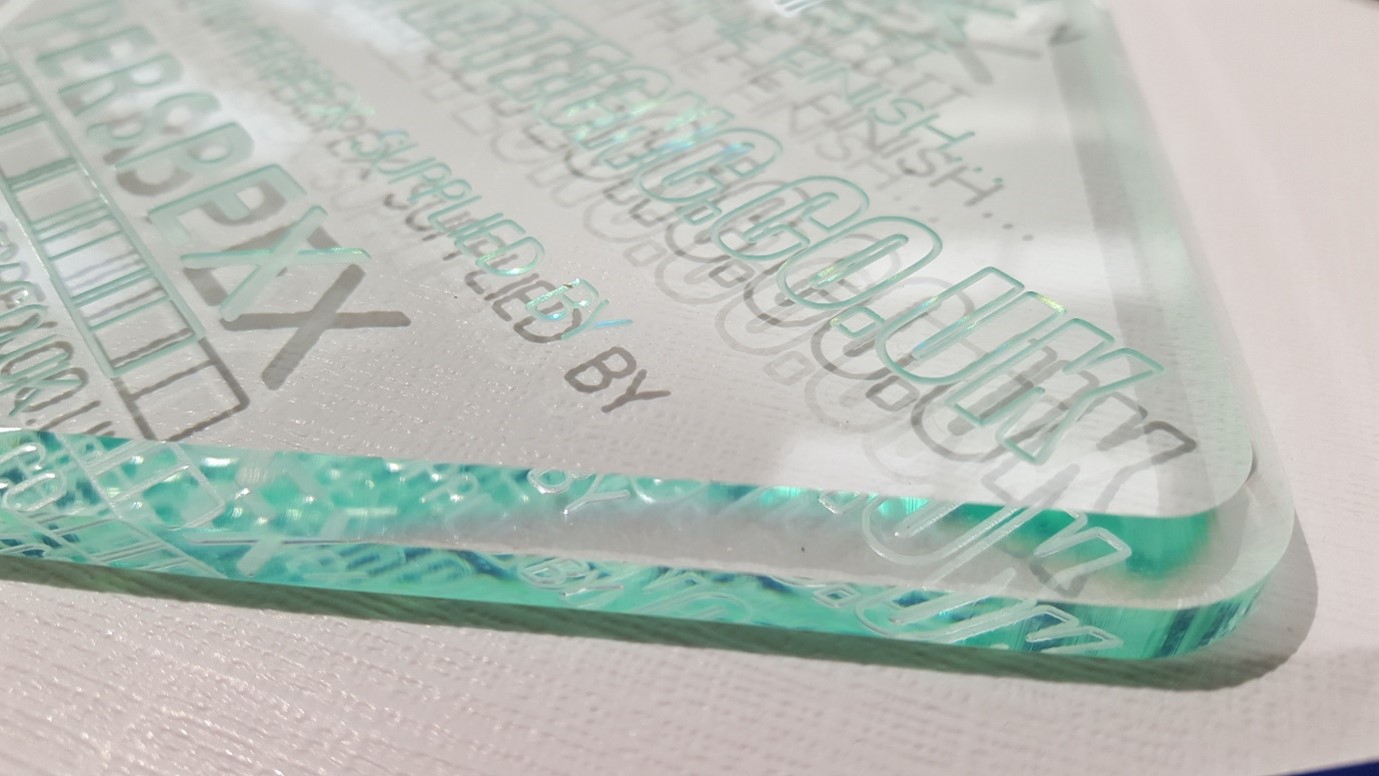
CNC for DFM
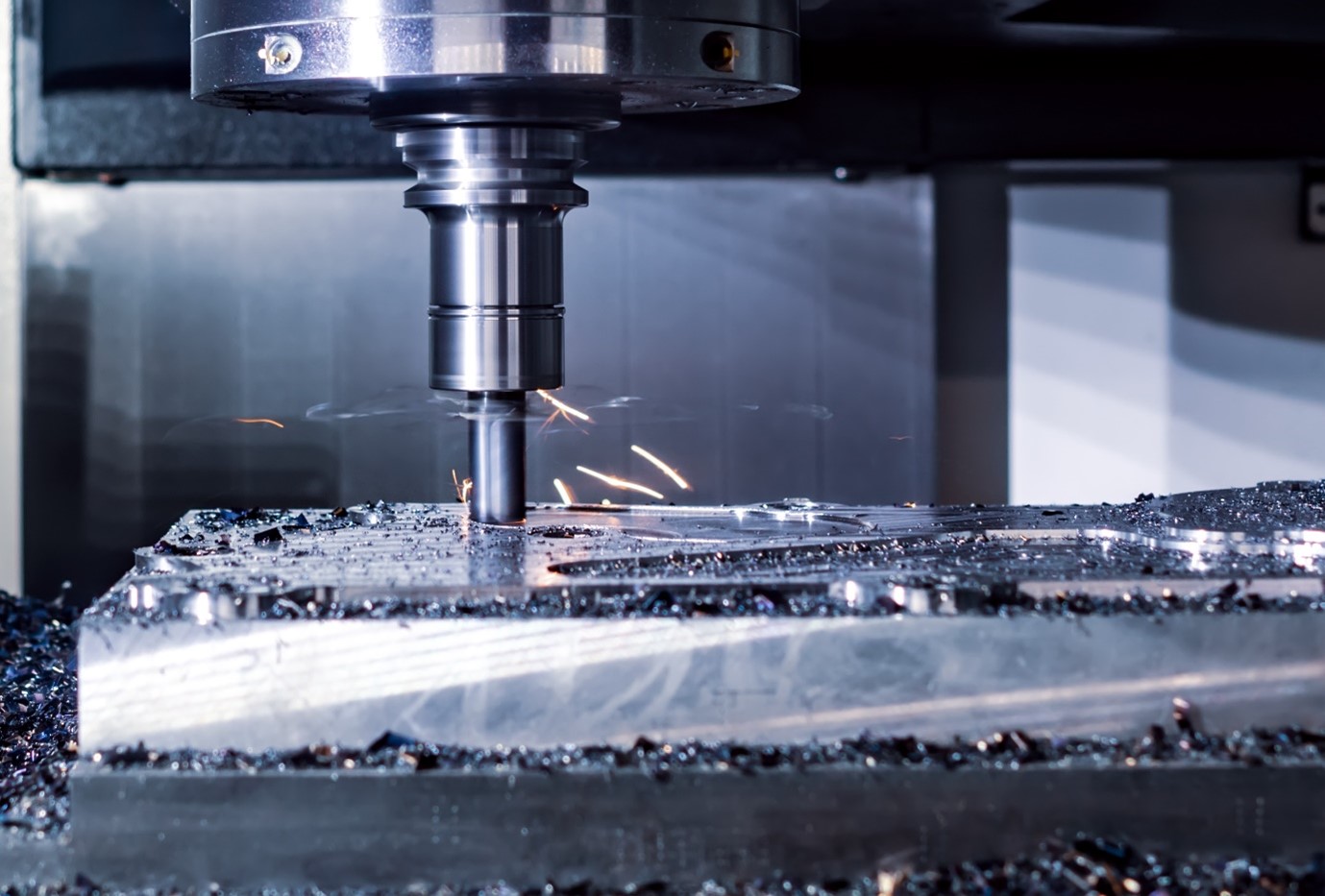
The Unbreakable Rules!
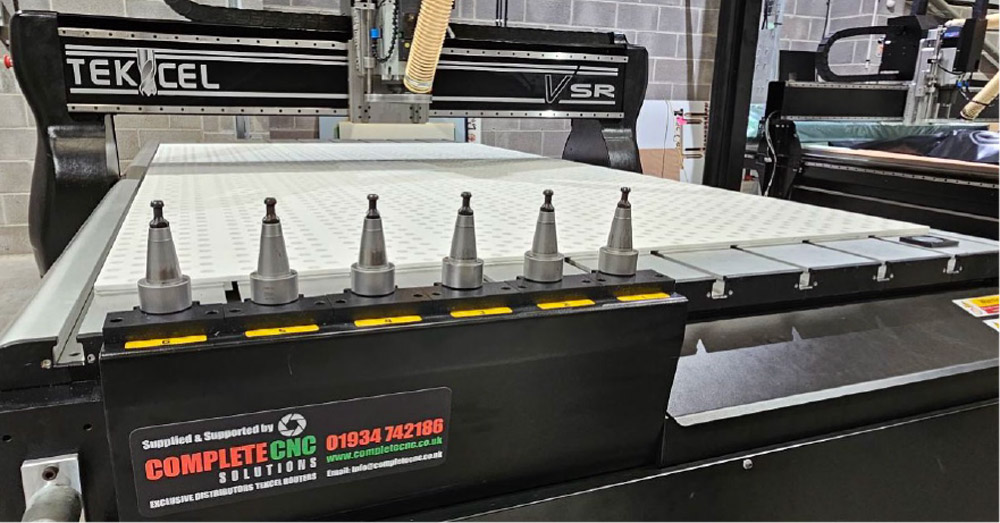
Welcome to the world of CAD/CAM
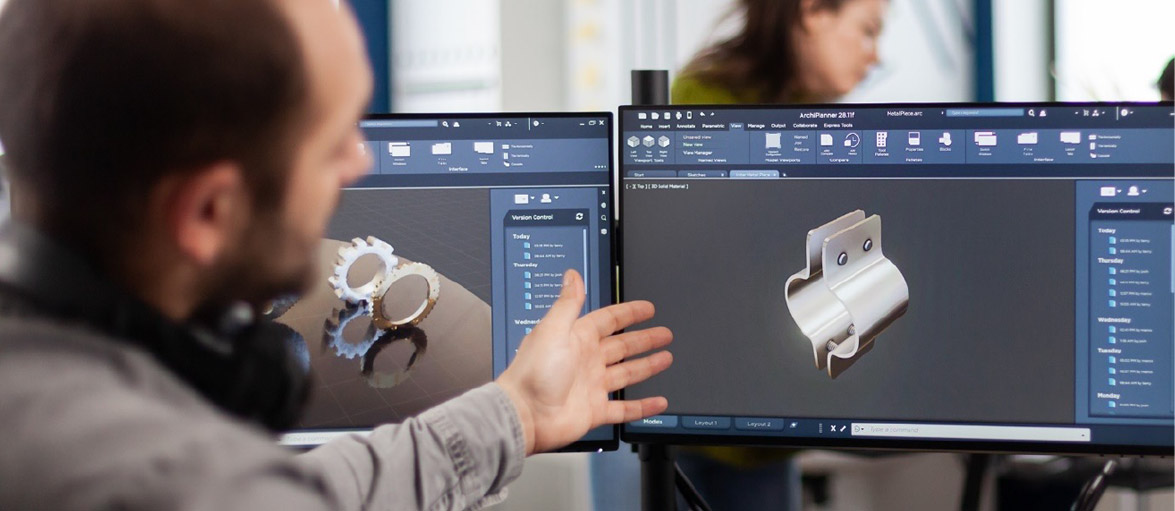
10 Tips for Successful Aluminium Cutting with CNC Routers
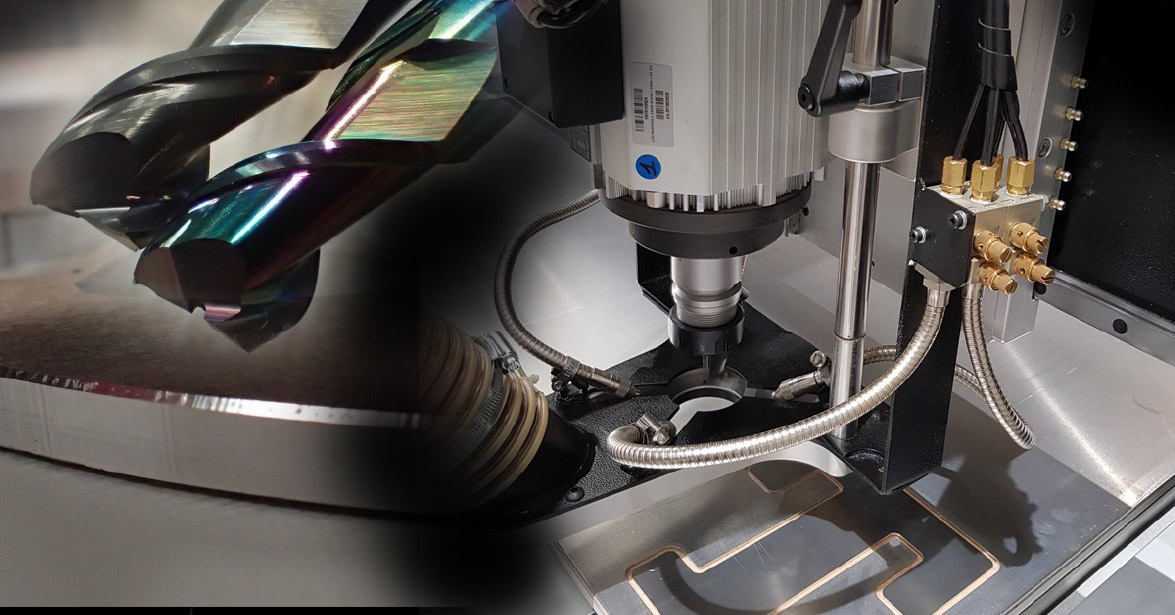
Mastering the Art of Tekcel CNC Router Speeds and Feeds: A Comprehensive Guide
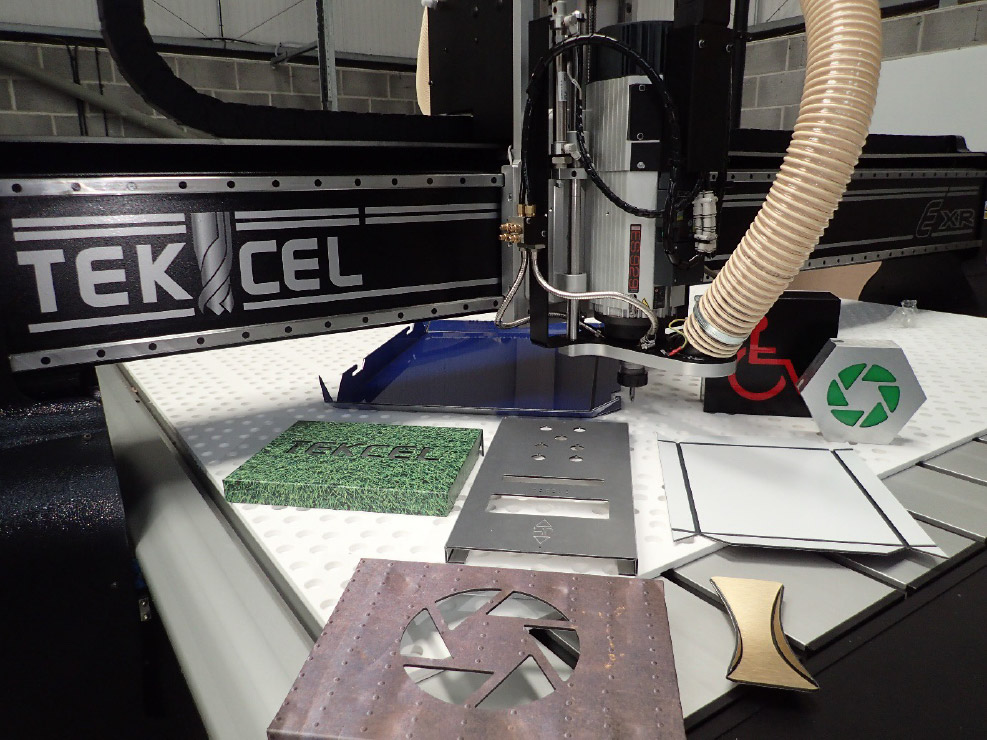
CNC Routers For Sign Making
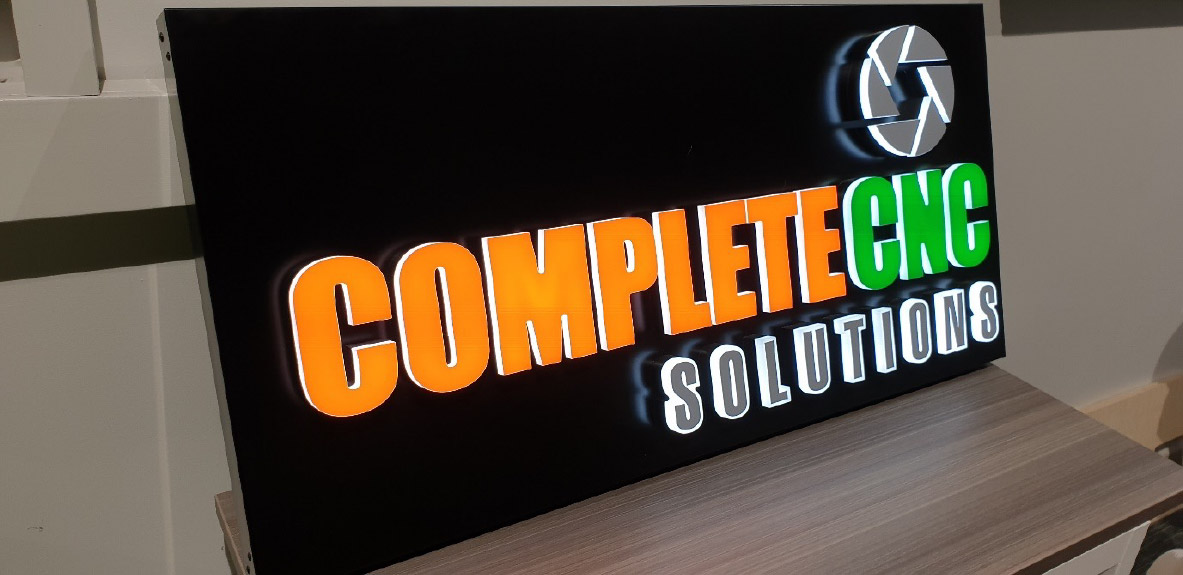
Cutting Acrylic With Your CNC Router
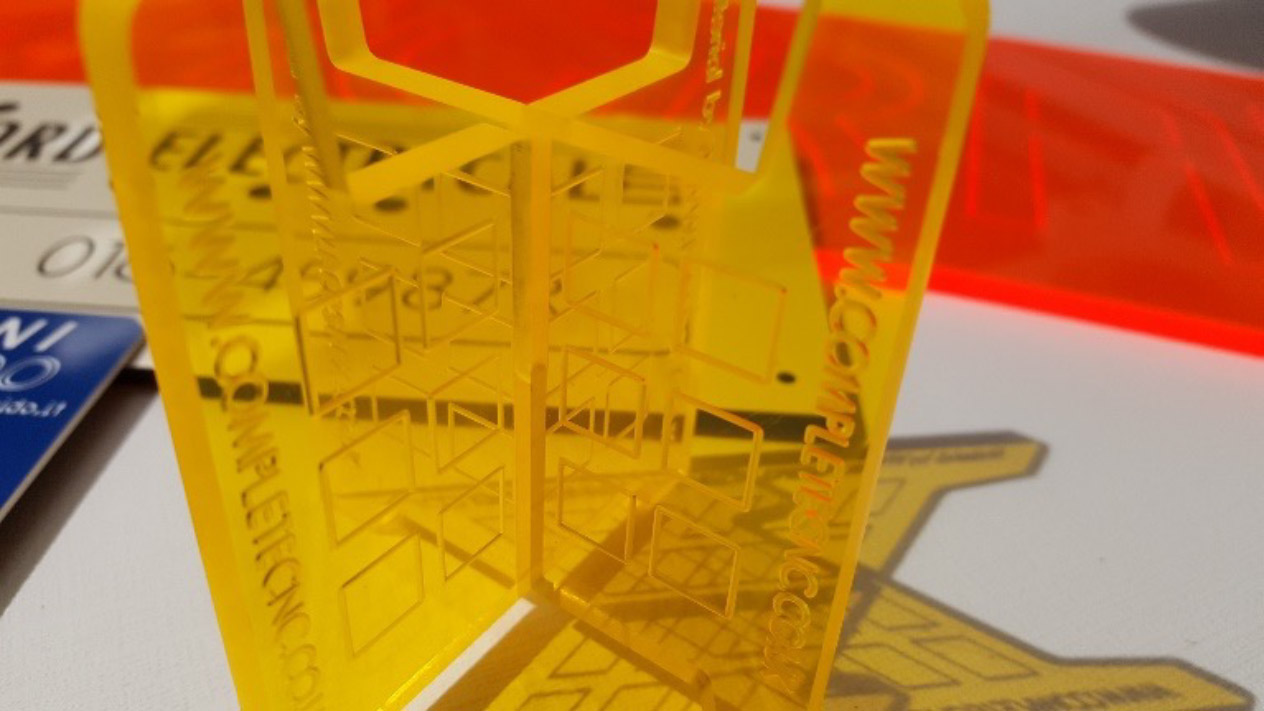
Collets: An Essential Tool
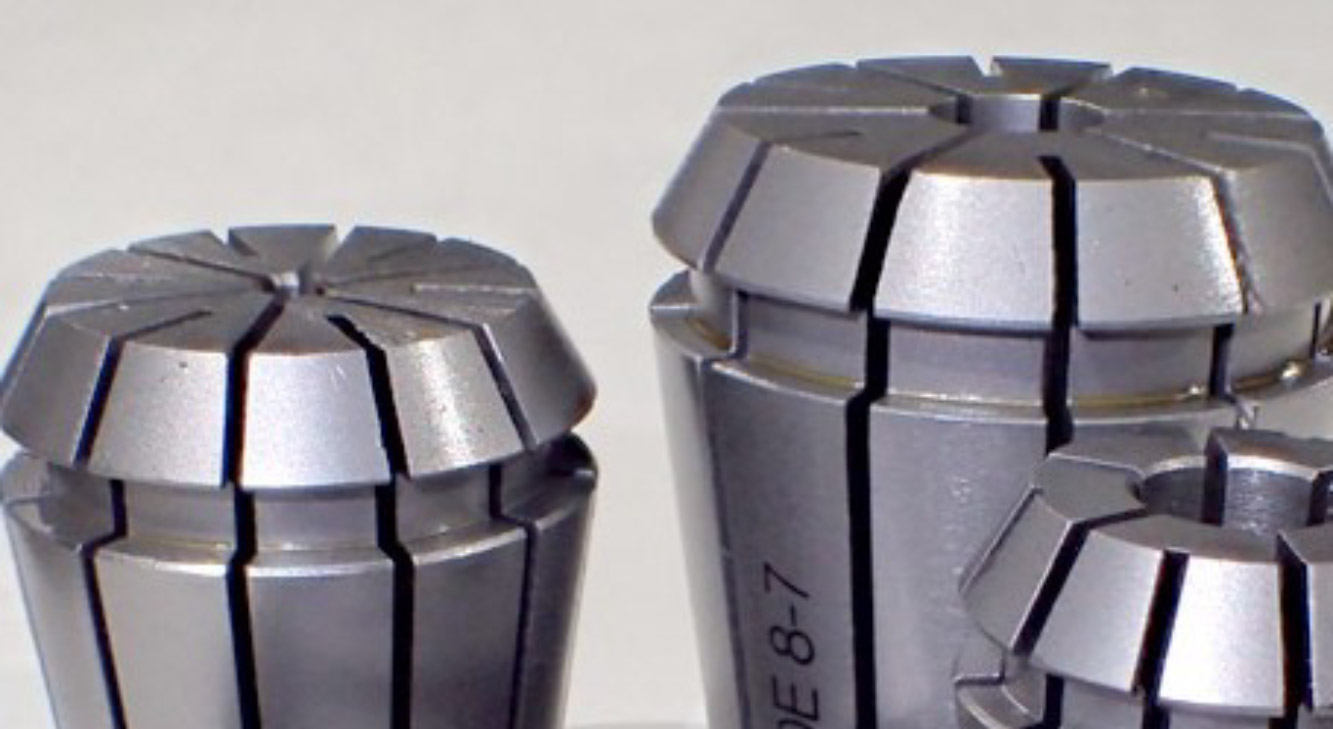
Calling all converters: How CNC Routers Elevate Vehicle Conversions
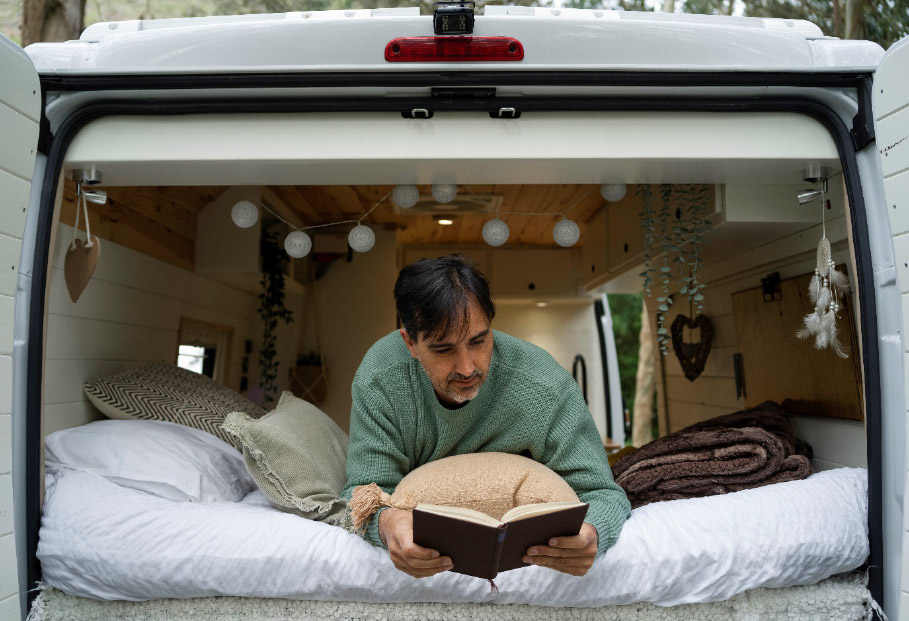
The Right tool for the job
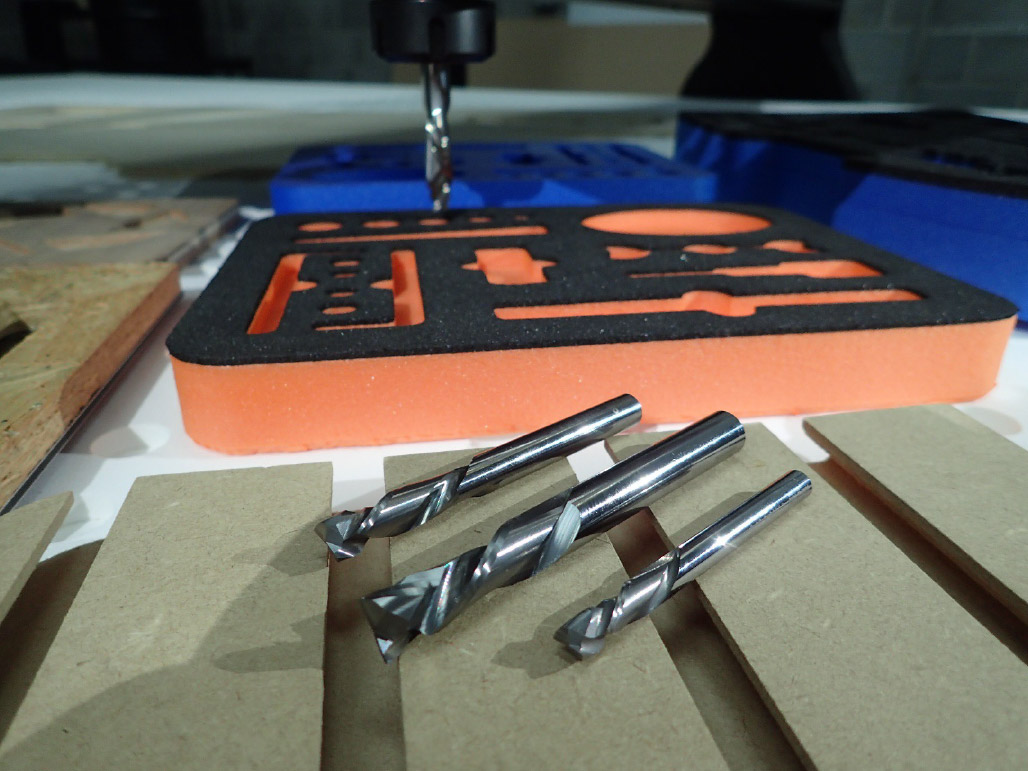
What is the cutting speed of a CNC router?
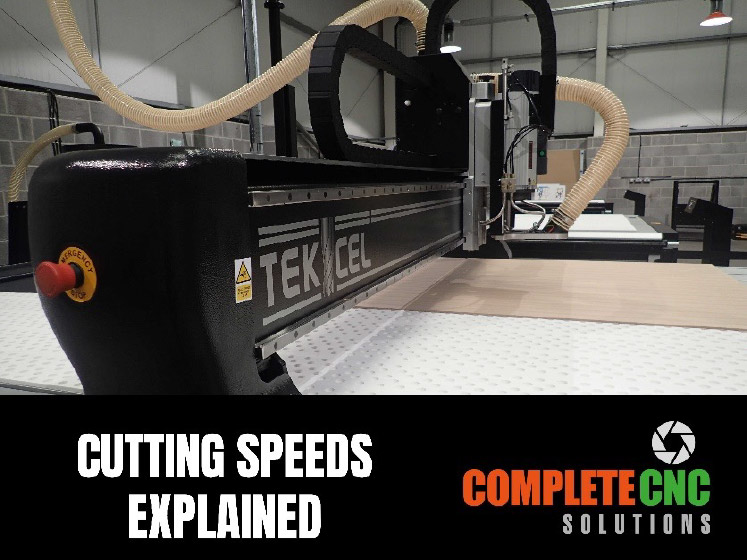
Unravelling the Mystery: Common themes overlooked with CNC Routers
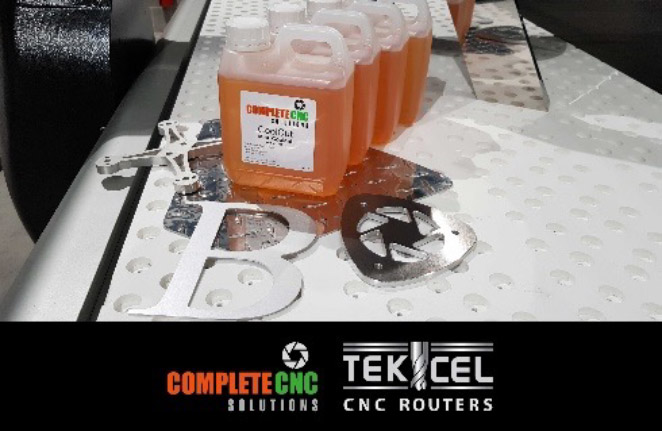
CNC Router Maintenance Guide for Longevity and Efficiency
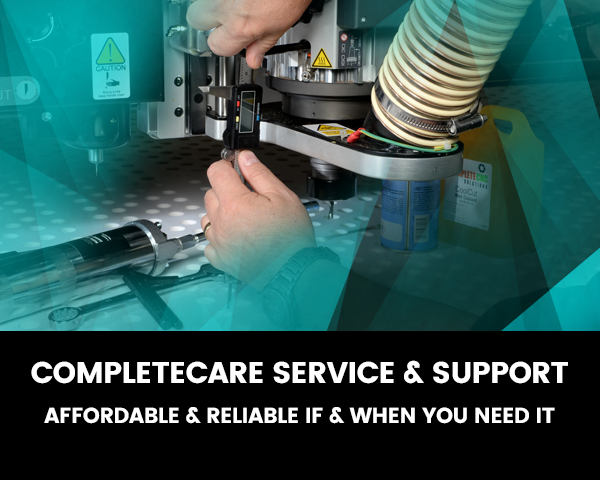
Tekcel Graphical User Interface
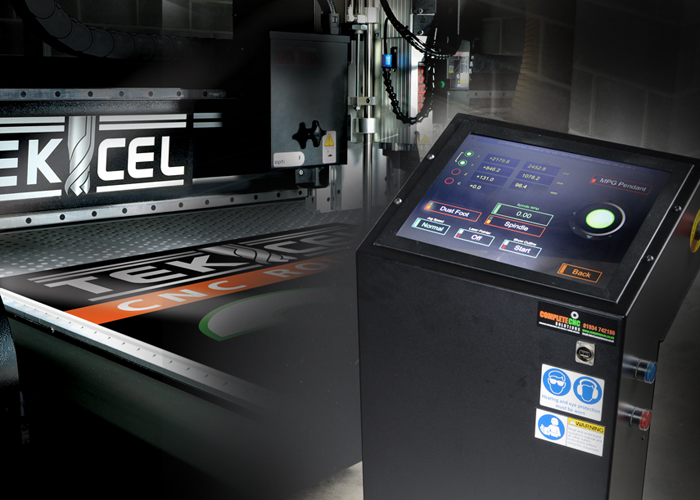
Unlock the World of Carving with CNC Routers!
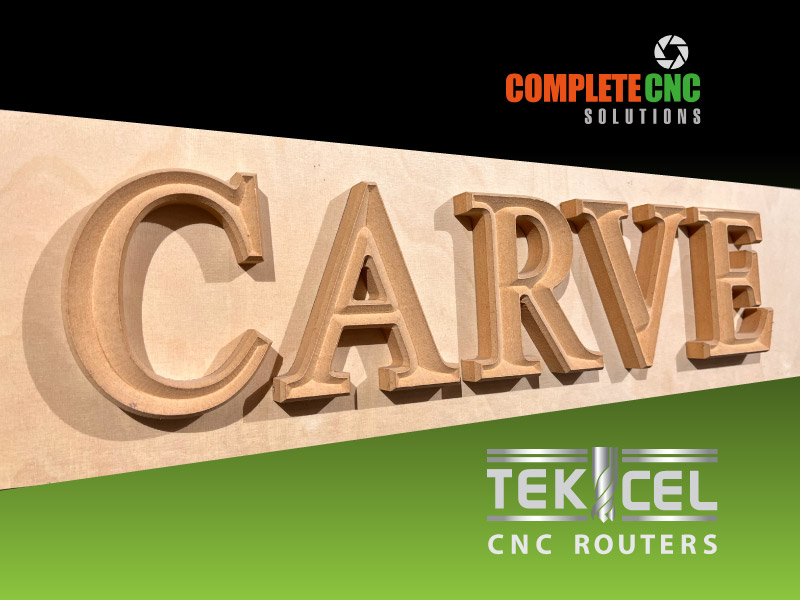
Can a CNC Router Carve Intricate Details? Yes!
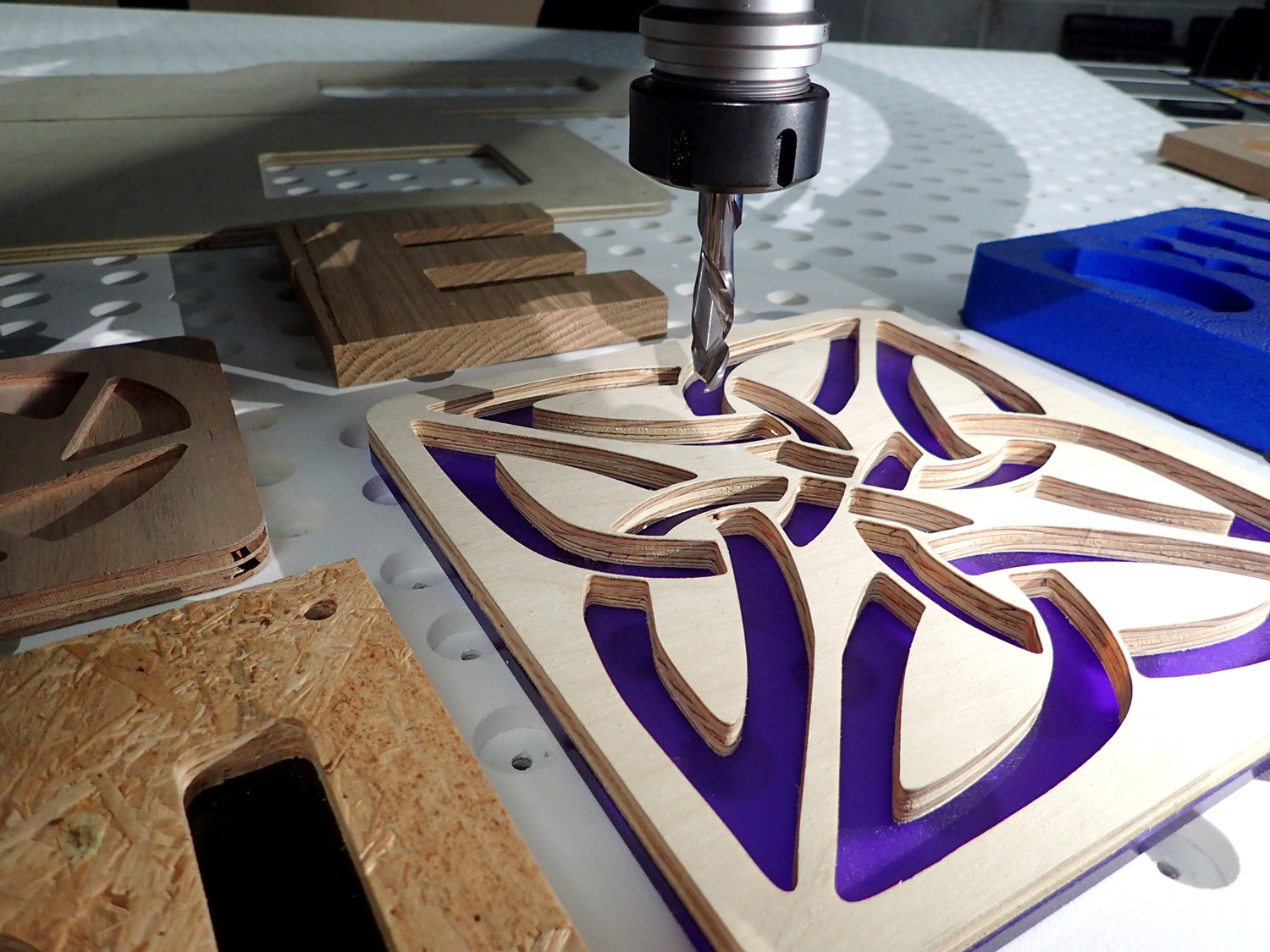
How a Tekcel CNC machine can provide value for your business
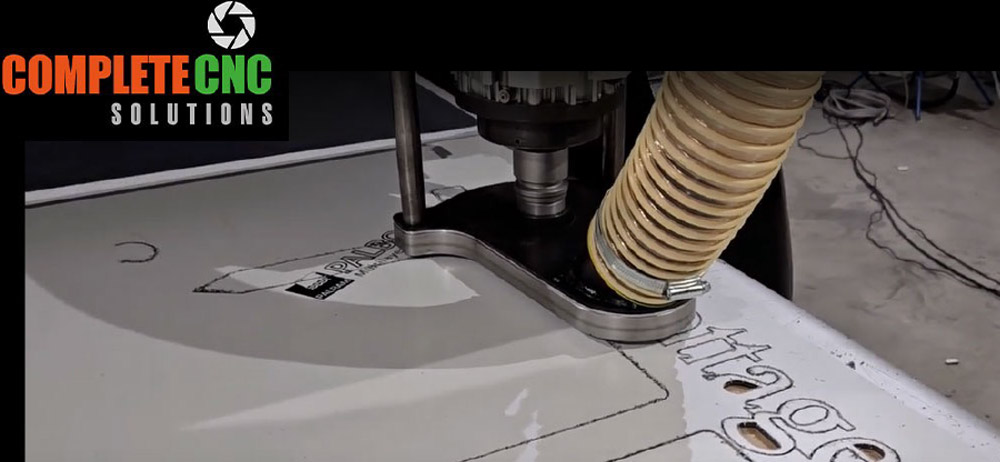
Elevating Point of Sale Production with CNC Machines
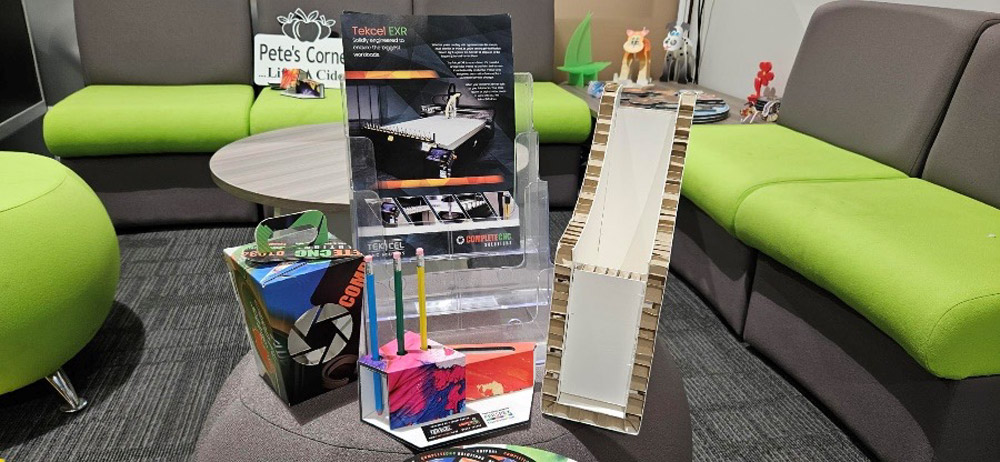
Why Sign Makers are Upgrading to CNC Cutting Machines
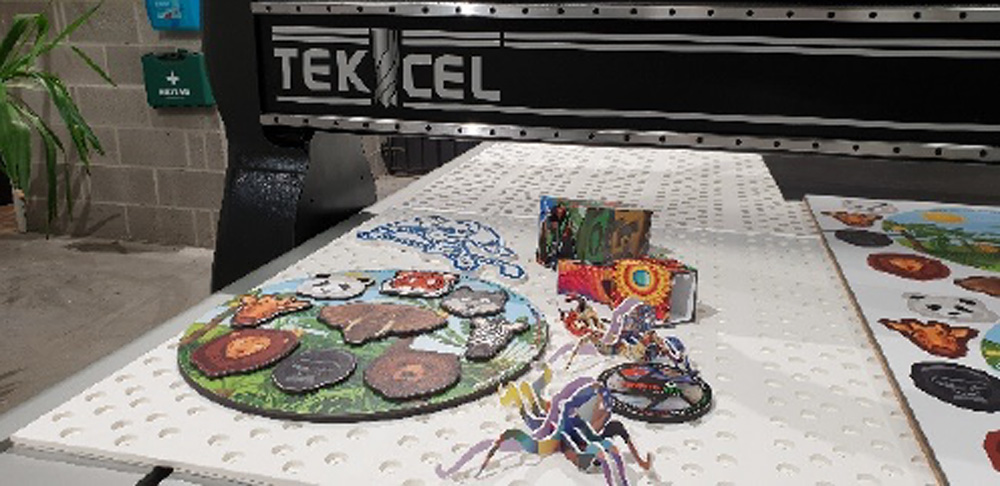
Hibernating Your CNC System During Lockdown.
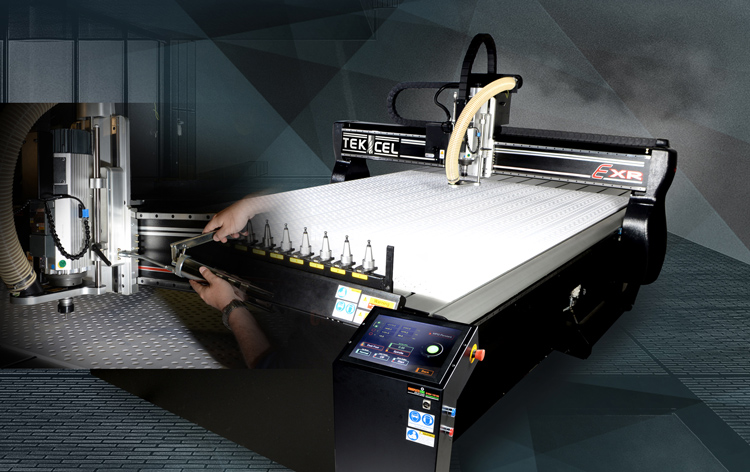
START BIG. GET BIGGER.
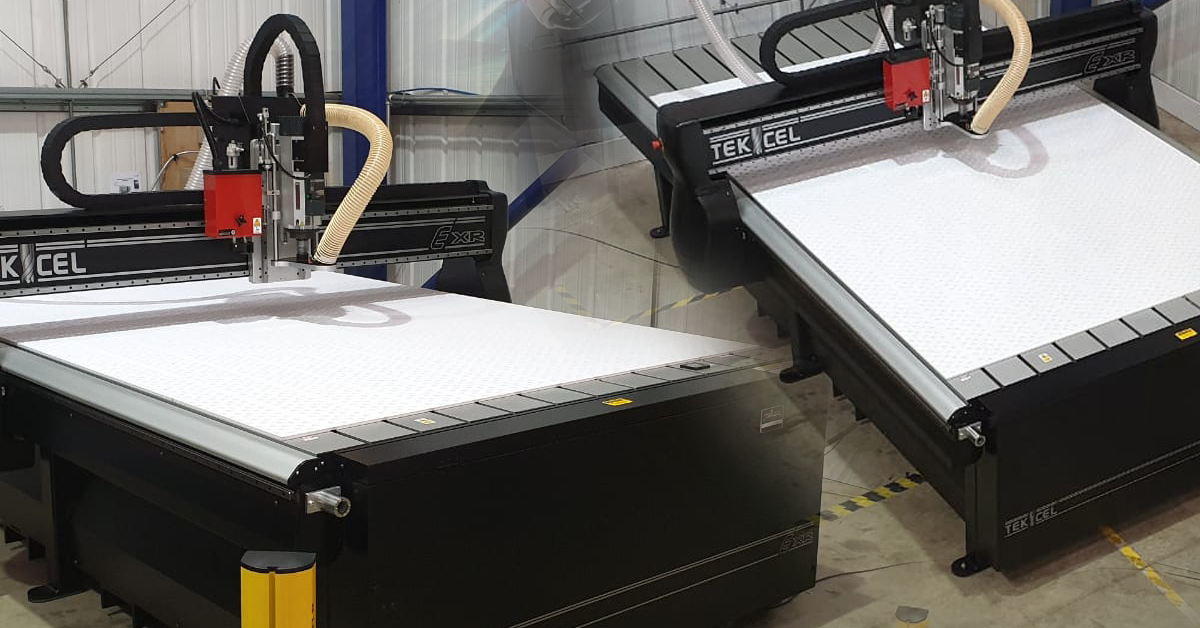
START WITH THE FINISH. FINISH WITH A PROFIT.
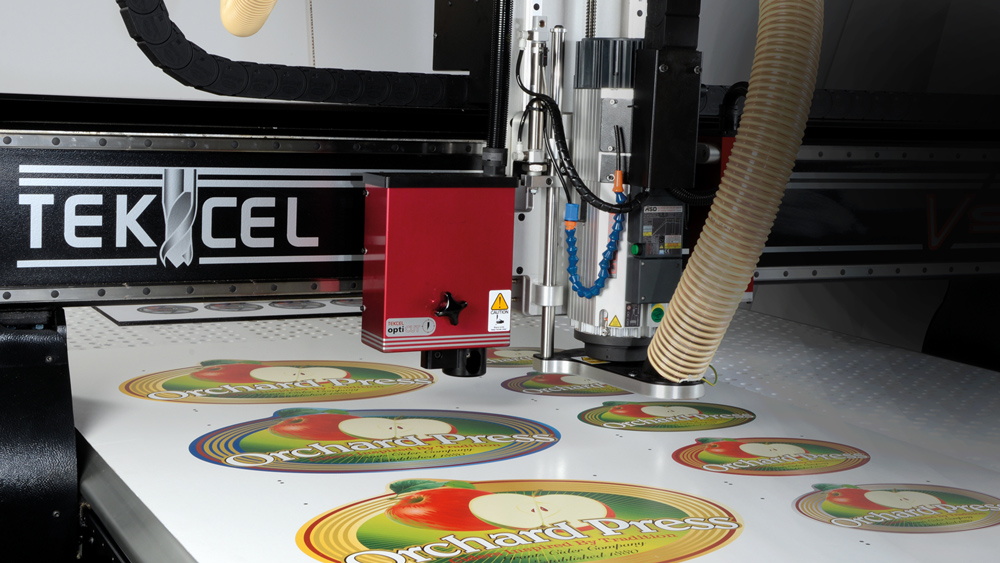
HEAVY METAL. LIGHT WORK.
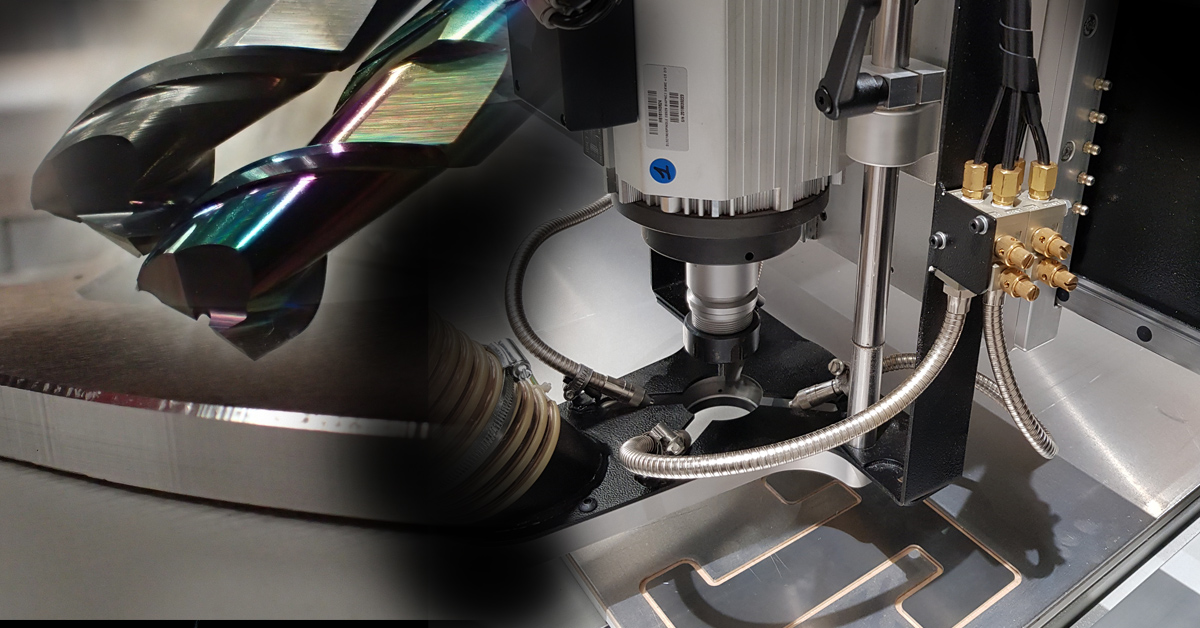
MAKE MORE WITH CORREX
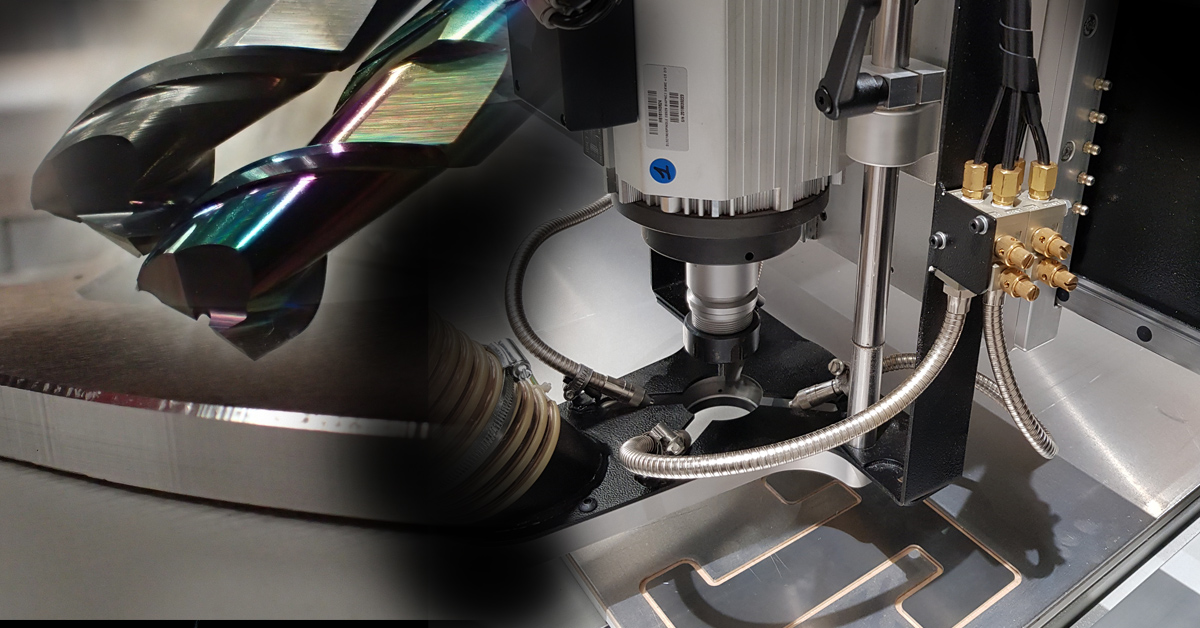
HOW SHOULD I APPROACH CUTTING OF SOLID SURFACE MATERIALS, CORIAN, AVONITE, THAT KIND OF THING?
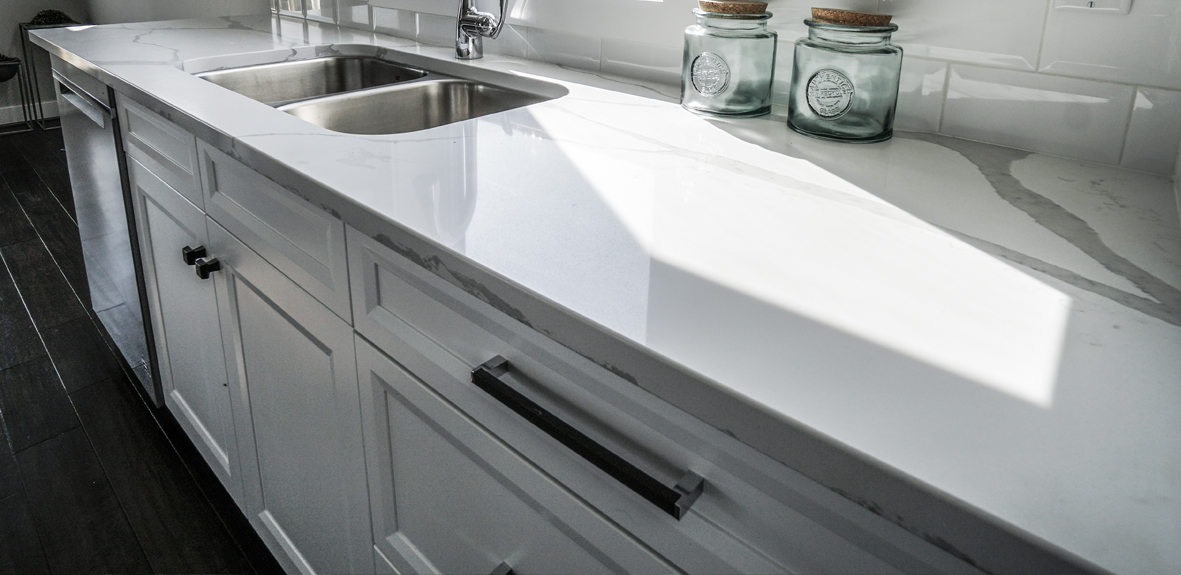
Achieving good results when you’re routing Woods, MDF, Laminates or Ply

HOW DO I GET THE BEST RESULTS POSSIBLE WHEN I’M CUTTING ACM ON MY CNC ROUTER?
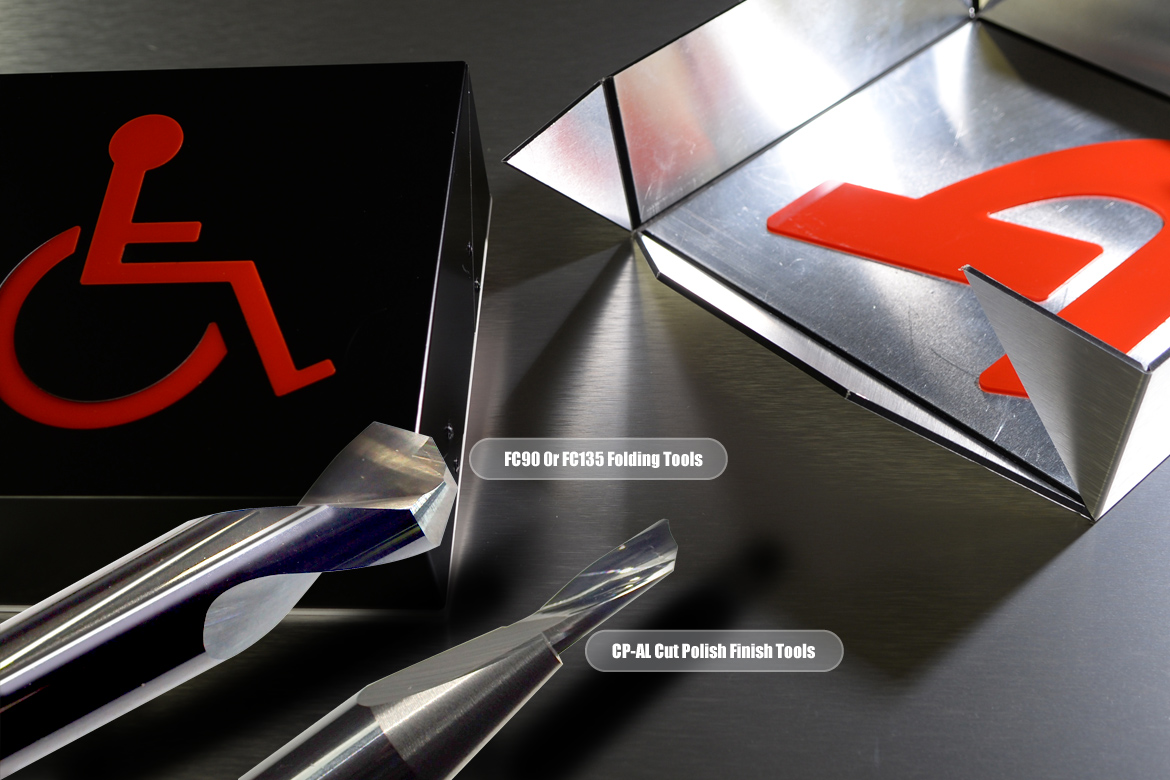
HOW CAN I GROW MY SIGNAGE AND GRAPHICS BUSINESS?
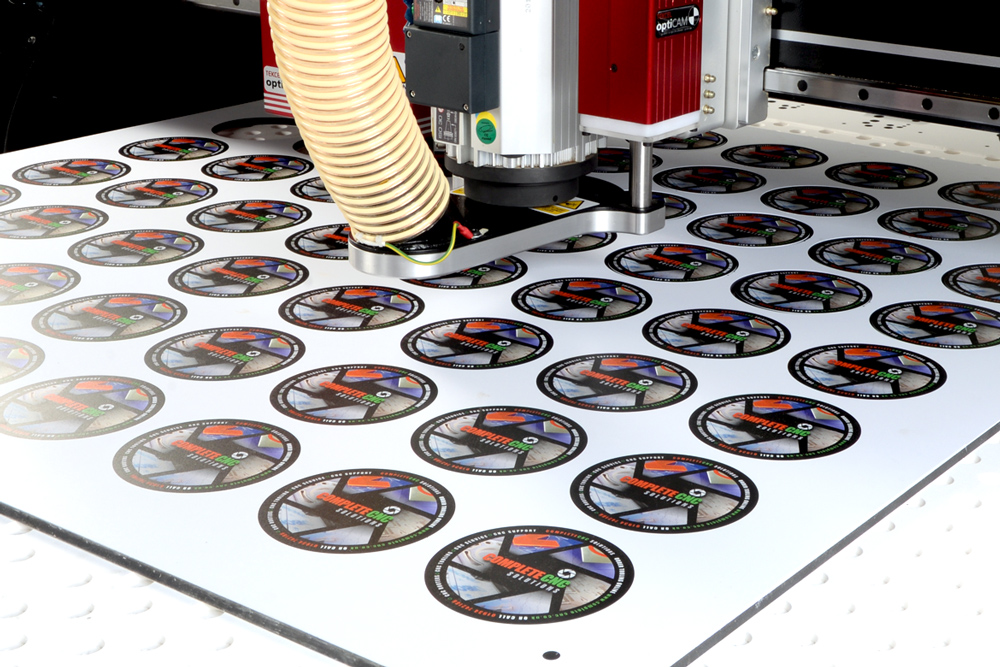
HOW CAN I REDUCE THE TIME I SPEND POLISHING THE EDGE ON THE OUTPUT FROM MY CNC ROUTER?
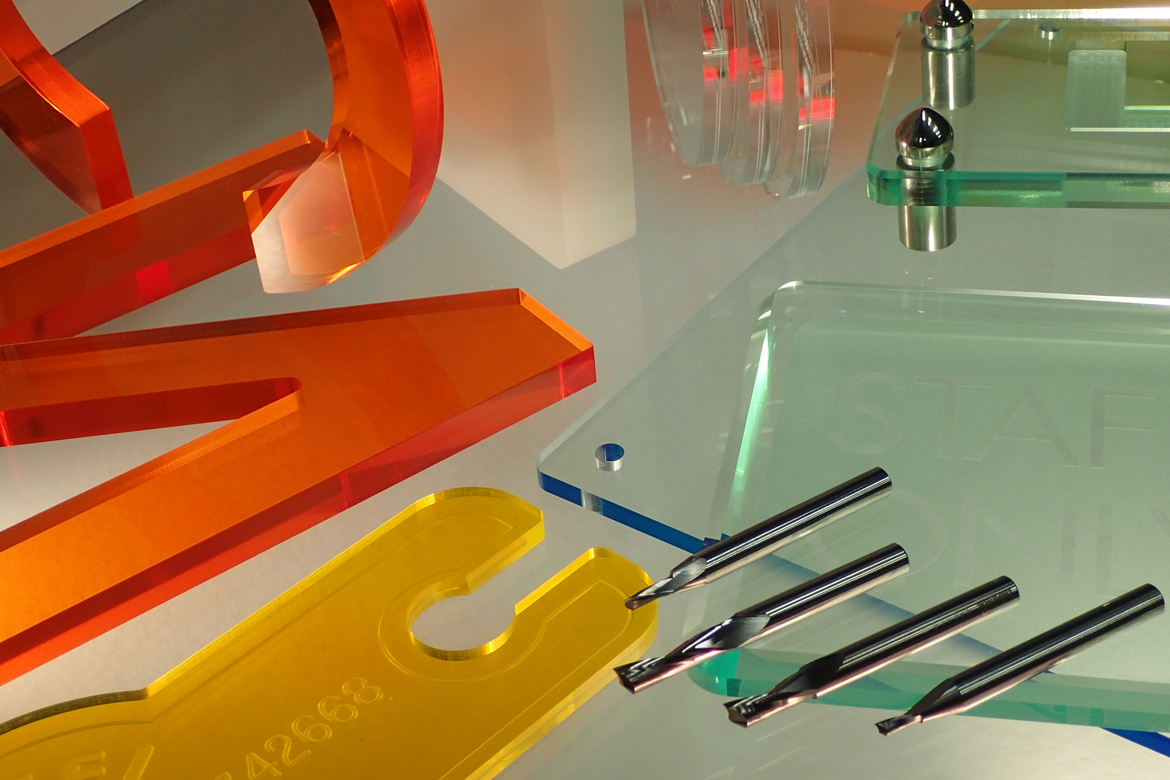
THE FLATTER THE BETTER
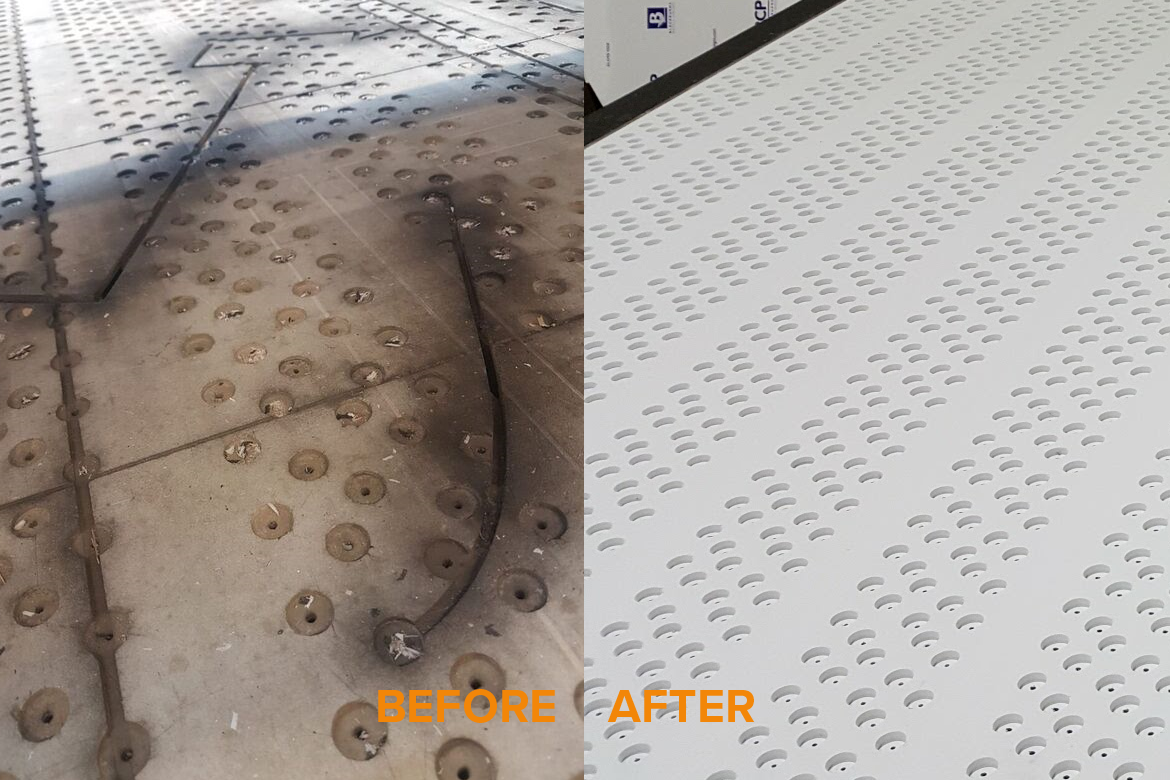
IS MY BUSINESS READY TO BUY A CNC ROUTER?
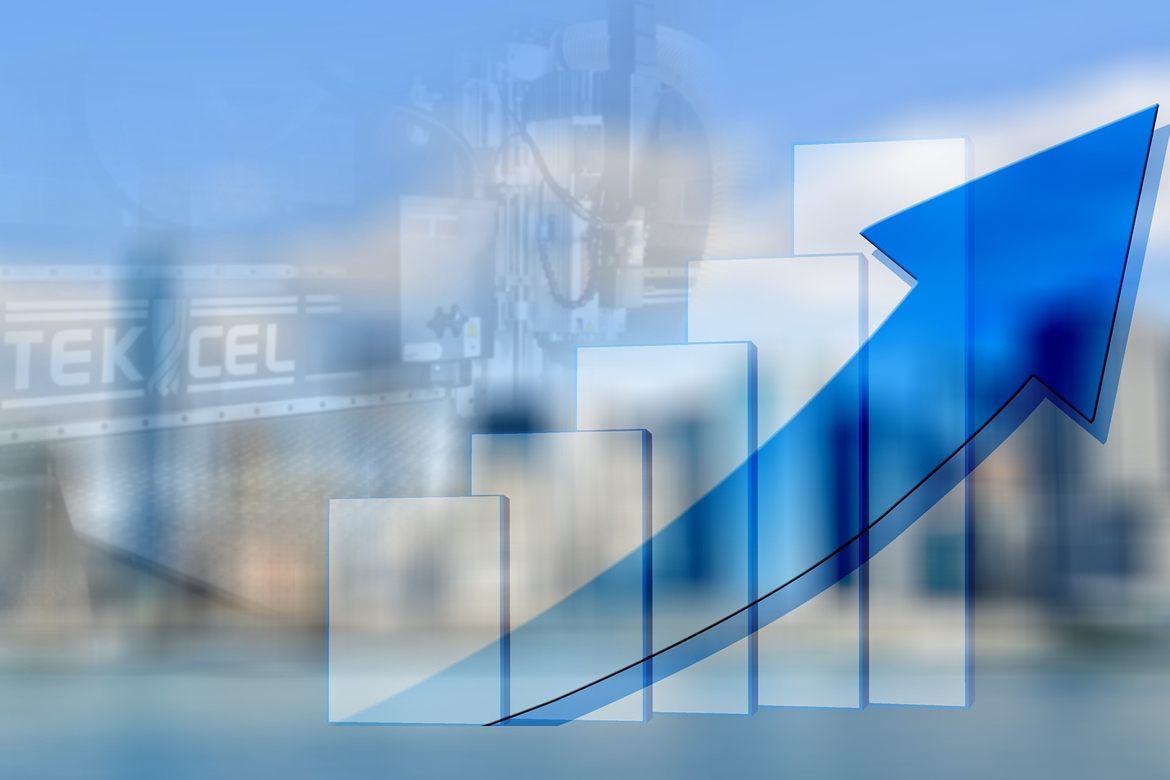
HEARD AT A TRADE SHOW
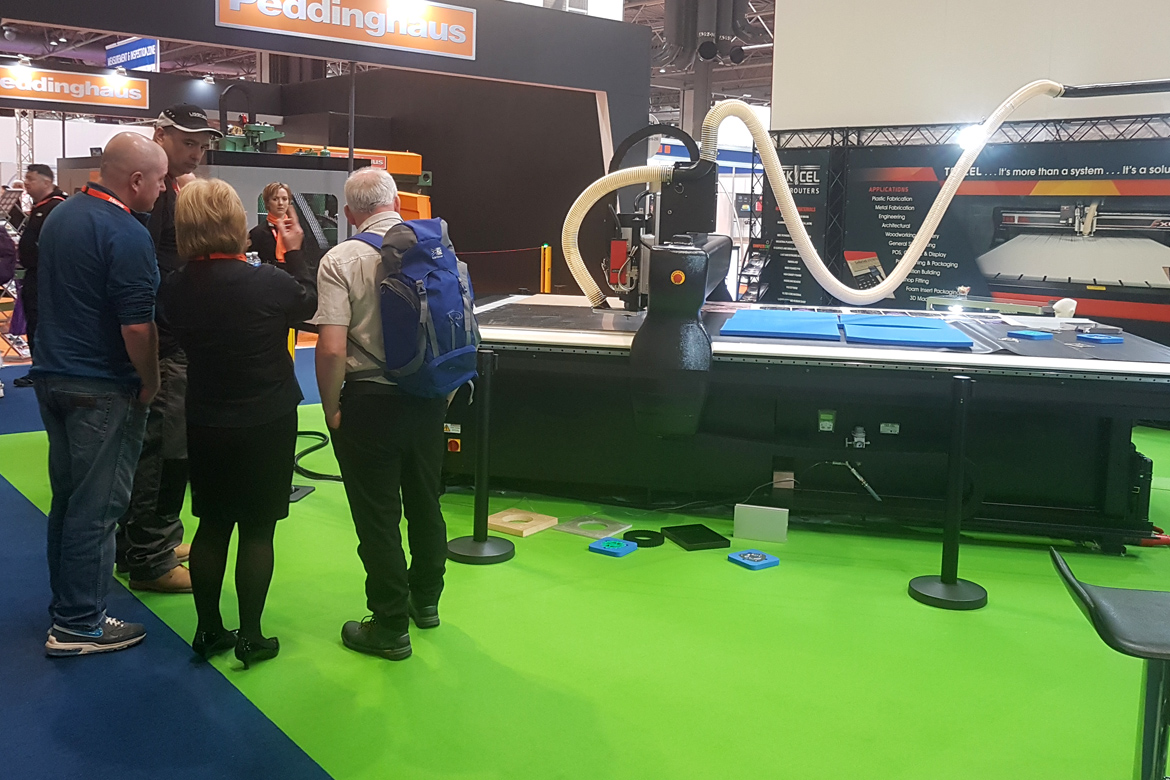
THE IMPORTANCE OF CHANGING CNC ROUTER COLLETS REGULARLY
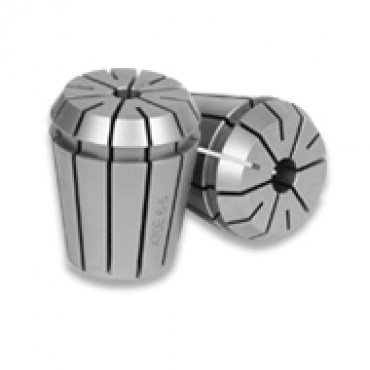
WITH YOU ALL THE WAY
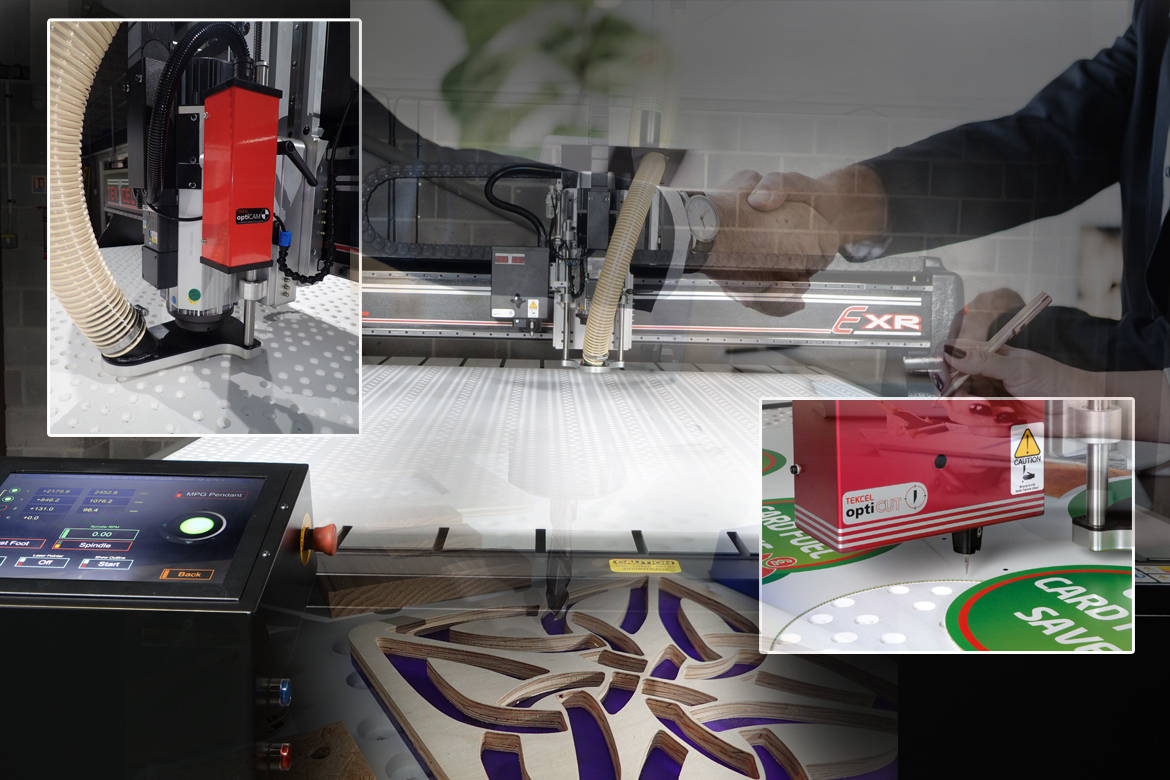