CUSTOMER LOGIN
Mastering the Art of Tekcel CNC Router Speeds and Feeds: A Comprehensive Guide
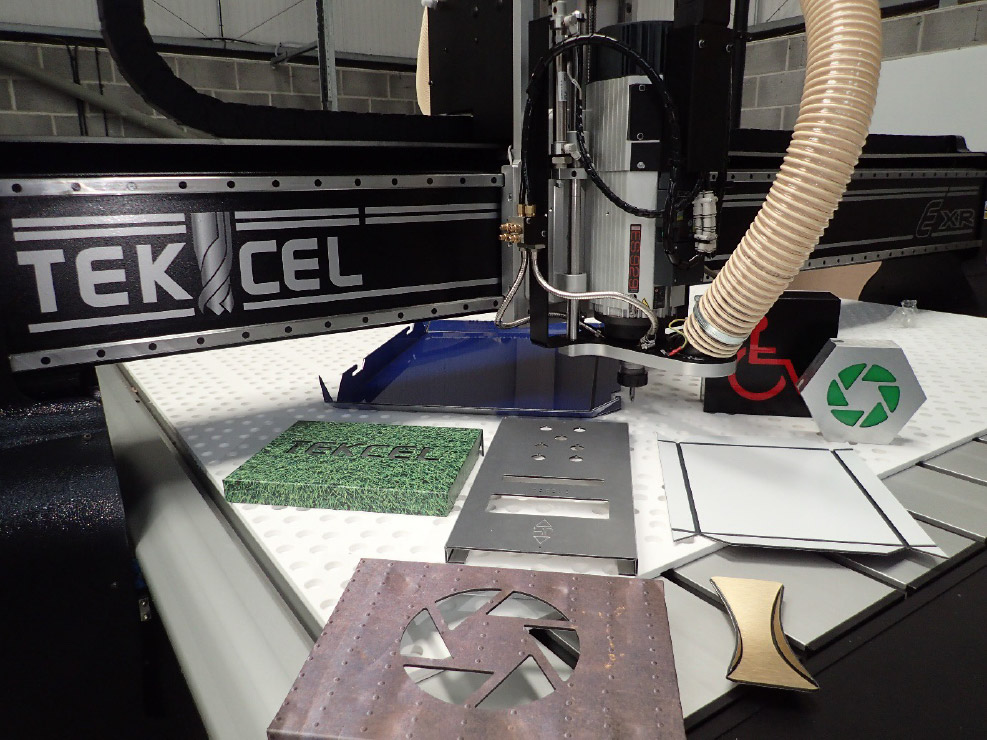
Mastering the Art of Tekcel CNC Router Speeds and Feeds: A Comprehensive Guide
Welcome to our comprehensive guide on mastering the art of Tekcel CNC router speeds and feeds! In the world of CNC machining, understanding and optimising speeds and feeds is crucial for achieving superior results in terms of efficiency, accuracy, and surface finish. With Tekcel CNC routers already popular in various industries, mastering the intricacies of speeds and feeds can elevate your CNC routing projects to new heights of precision and productivity.
Understanding Speeds and Feeds
Before we go into the specifics of Tekcel CNC router speeds and feeds, let's first establish a clear understanding of these terms:
X & Y Feed Rate: Refers to the rate at which the cutting tool or router bit moves in the X & Y direction. It is typically measured in meters per minute (m/min) or millimetres per second(mm/sec).
Z Plunge Feed Rate: Represents the speed the cutting tool advances into the workpiece on the Z axis. It is typically measured in meters per minute (m/min) or millimetres per second(mm/sec).
Spindle Speed: This is measured in revolutions per minute (RPM) and is the speed that the spindle motor turns the tool bit in the collet.
Optimising speeds and feeds involves finding the perfect balance between the two parameters to achieve efficient material removal while maintaining dimensional accuracy and surface quality.
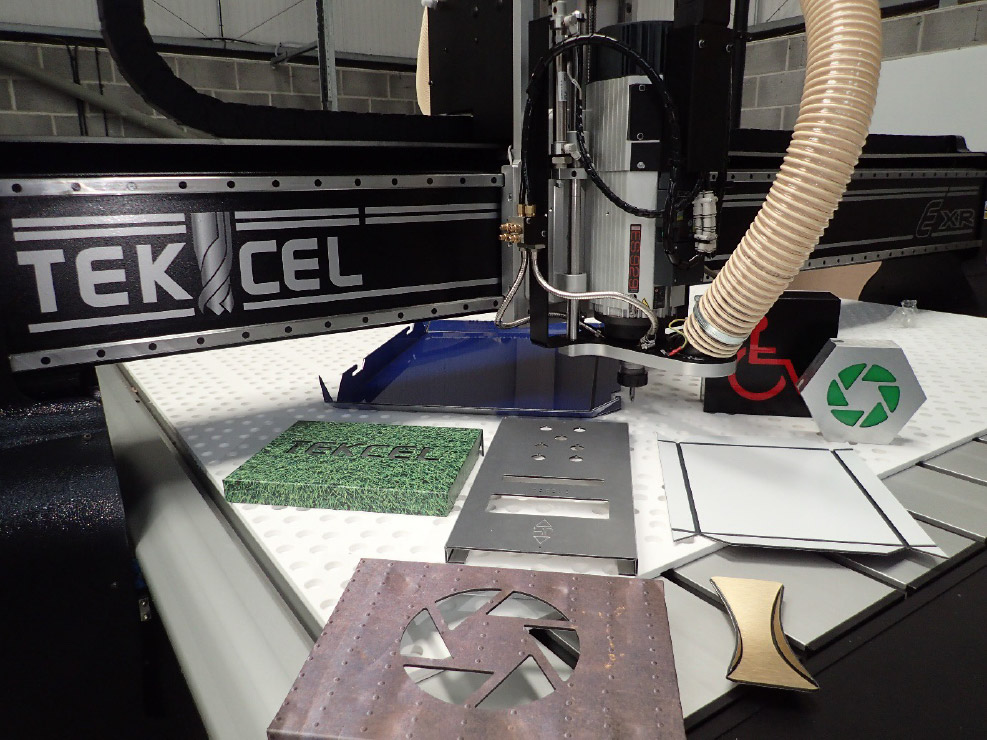
Factors Influencing Speeds and Feeds
Several factors influence the selection of speeds and feeds for Tekcel CNC router operations:
Material Type: Different materials (wood, plastic, aluminium, etc.) have varying cutting characteristics, necessitating adjustments in speeds and feeds to achieve optimal results.
Tooling: The type, size, and geometry of the router bit or cutting tool significantly impact the recommended speeds and feeds.
Machine Capability: Tekcel CNC routers come with High Frequency spindles, capable of running at 24,000 RPM. Horsepower, Torque & machine rigidity all have a big influence on machine cutting performance.
Cutting Depth and Width: The depth of cut (DOC) and width of cut (WOC) determine the amount of material removed with each pass, affecting the required speeds and feeds.
Optimising Speeds and Feeds with Tekcel CNC Routers
Now, let's explore some strategies for optimising speeds and feeds specifically for Tekcel CNC routers:
Start with Manufacturer Guidelines: We provide comprehensive guidelines and recommendations for speeds and feeds for our Tekcel machines. We can also offer guidelines for other machine makes too. These guidelines serve as an excellent starting point for your CNC routing projects.
Experimentation and Testing: Conducting test cuts with varying speeds and feeds allows you to observe the effects on material removal rate, surface finish, and tool life. This empirical approach helps in fine-tuning the settings for optimal performance.
Use Quality Tooling https://completecnc.co.uk/products/plastics-metals-acm/ Invest in high-quality router bits and cutting tools specifically designed for CNC routing applications. Quality tooling ensures better performance and longevity while enabling higher speeds and feeds.
Consider Material Properties: Different materials exhibit unique cutting characteristics, such as hardness, brittleness, and thermal conductivity. Adjust speeds and feeds accordingly to accommodate these material-specific traits.
Monitor Performance: Regularly monitor the performance of your Tekcel CNC router, including spindle RPM, cutting forces, and tool wear. Adjust speeds and feeds as necessary to maintain consistent and efficient machining.
Mastering the art of Tekcel CNC router speeds and feeds is a continuous journey of experimentation, optimisation, and adaptation. By understanding the fundamentals of speeds and feeds and employing the strategies outlined in this guide, you can unleash the full potential of your Tekcel CNC router, achieving superior results in terms of efficiency, precision, and surface finish across a wide range of materials and applications.
Contact us today to learn more or request a quote tailored to your specific requirements.
Further Blog Posts
Avoid These CNC Pitfalls in Illuminated Signmaking
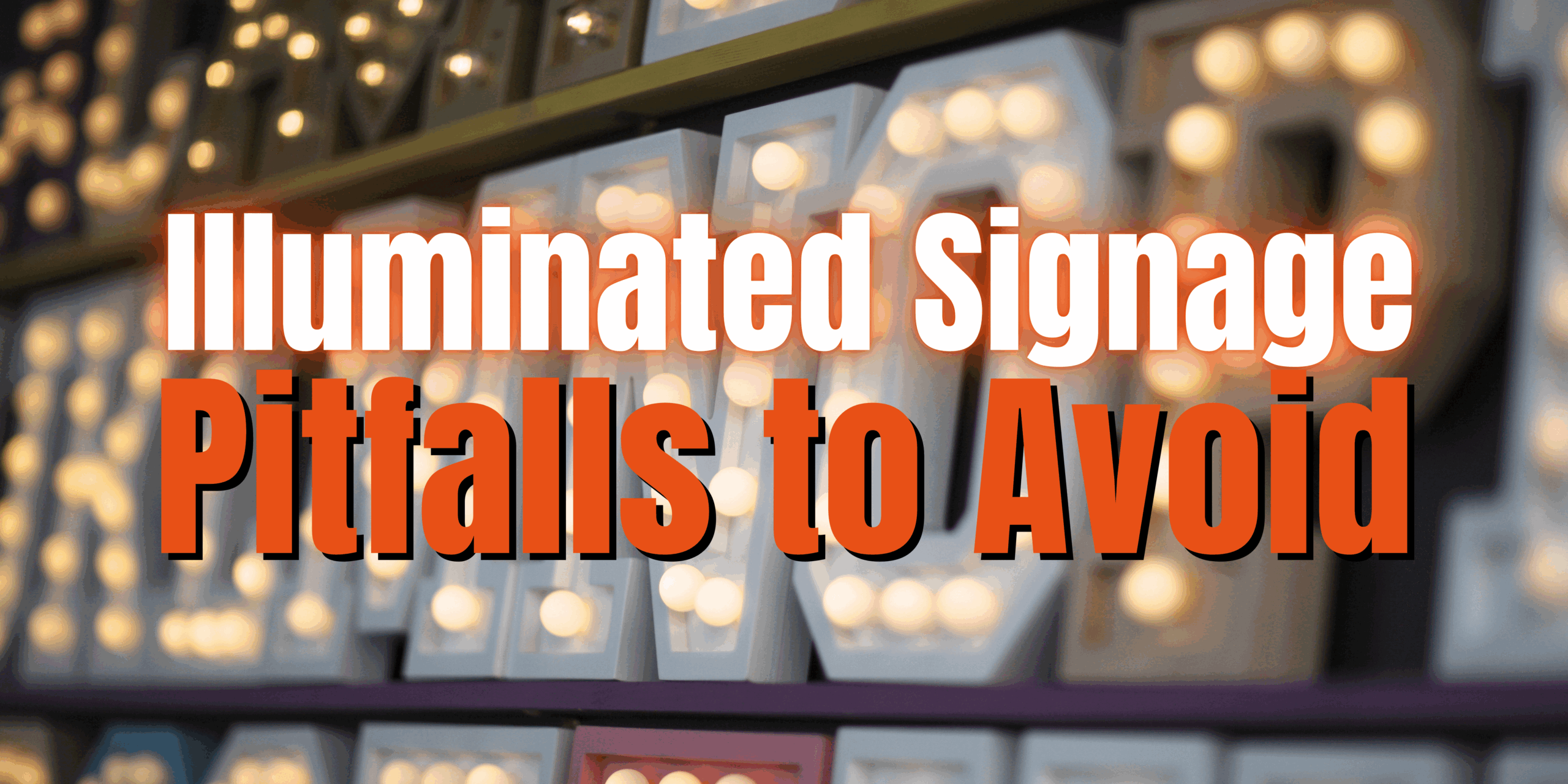
Essential CNC Router Tips for Cutting Acrylic
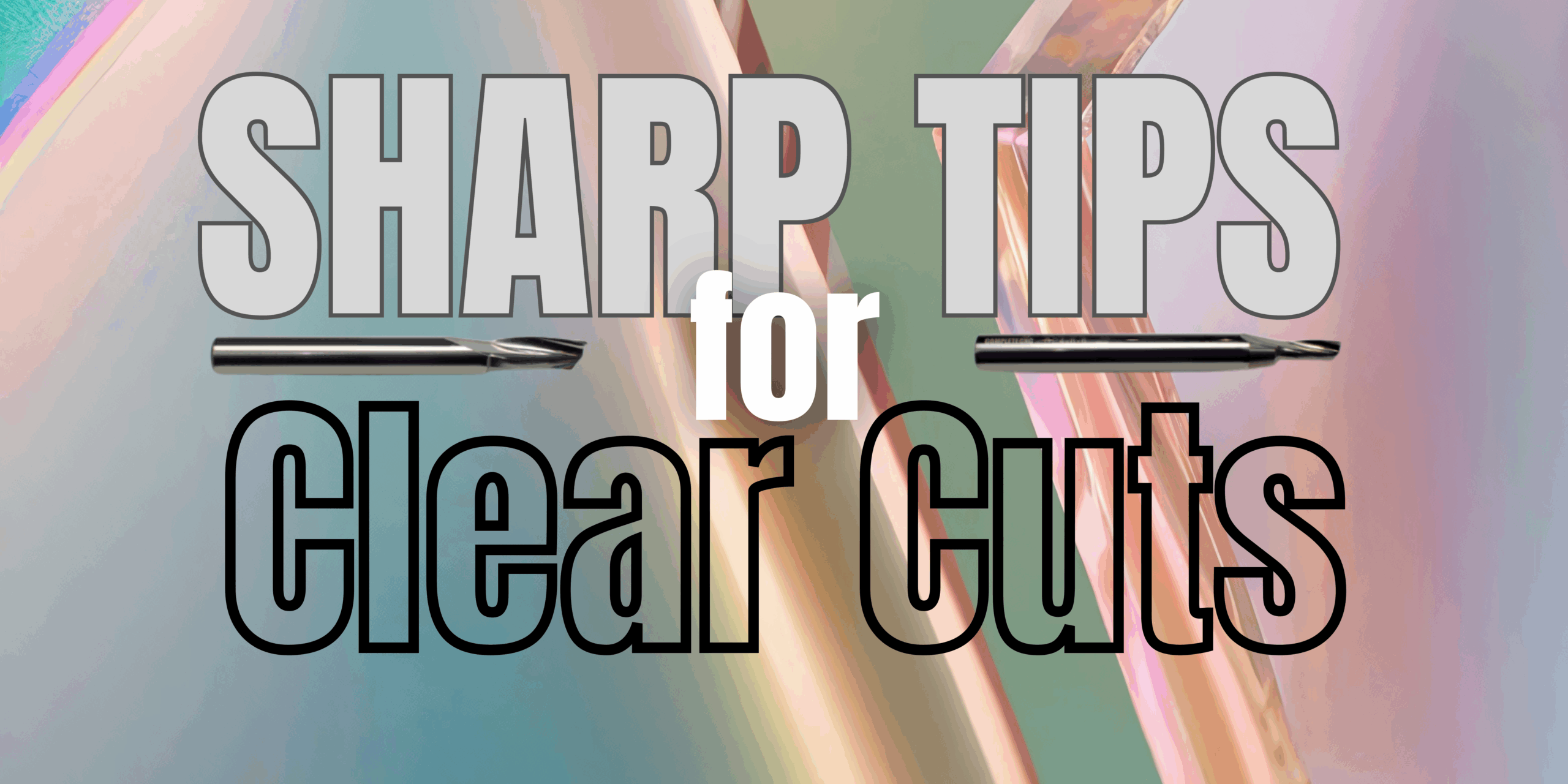
Nesting Your Way to Better Margins in Joinery
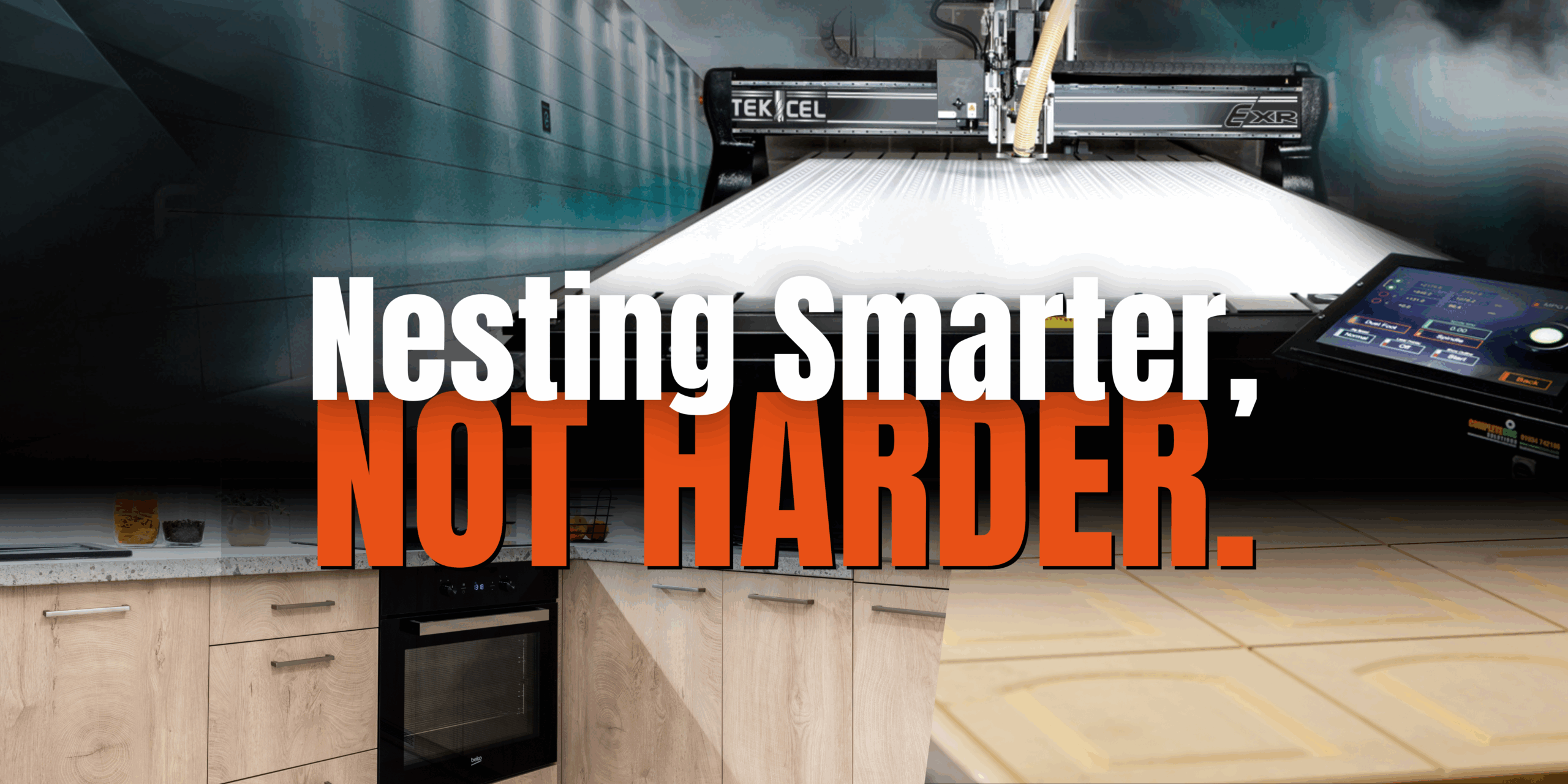
Is Your CNC Router Holding Your Business Back?
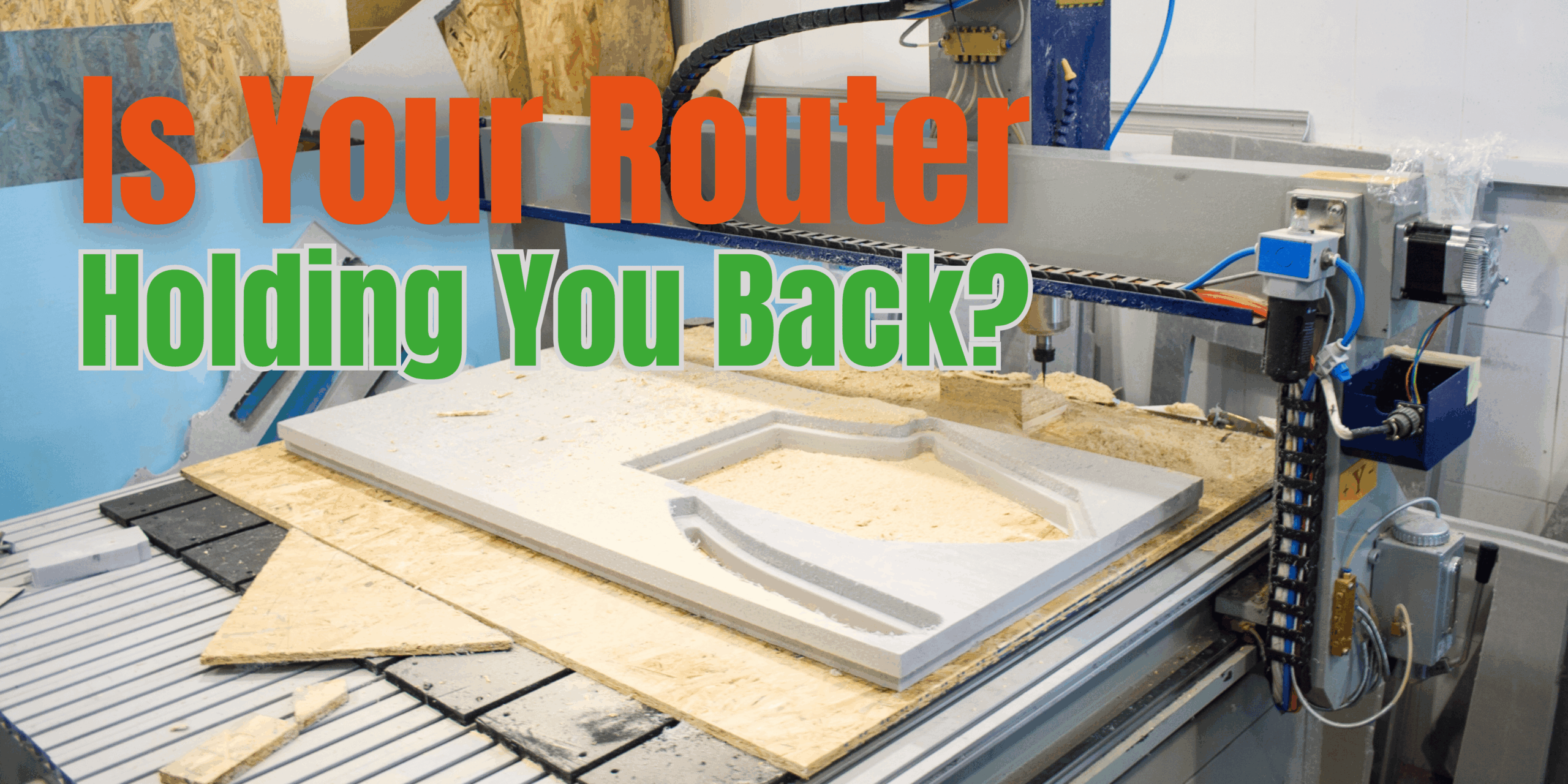
Can a CNC Router Cover Lots of Different Industries?
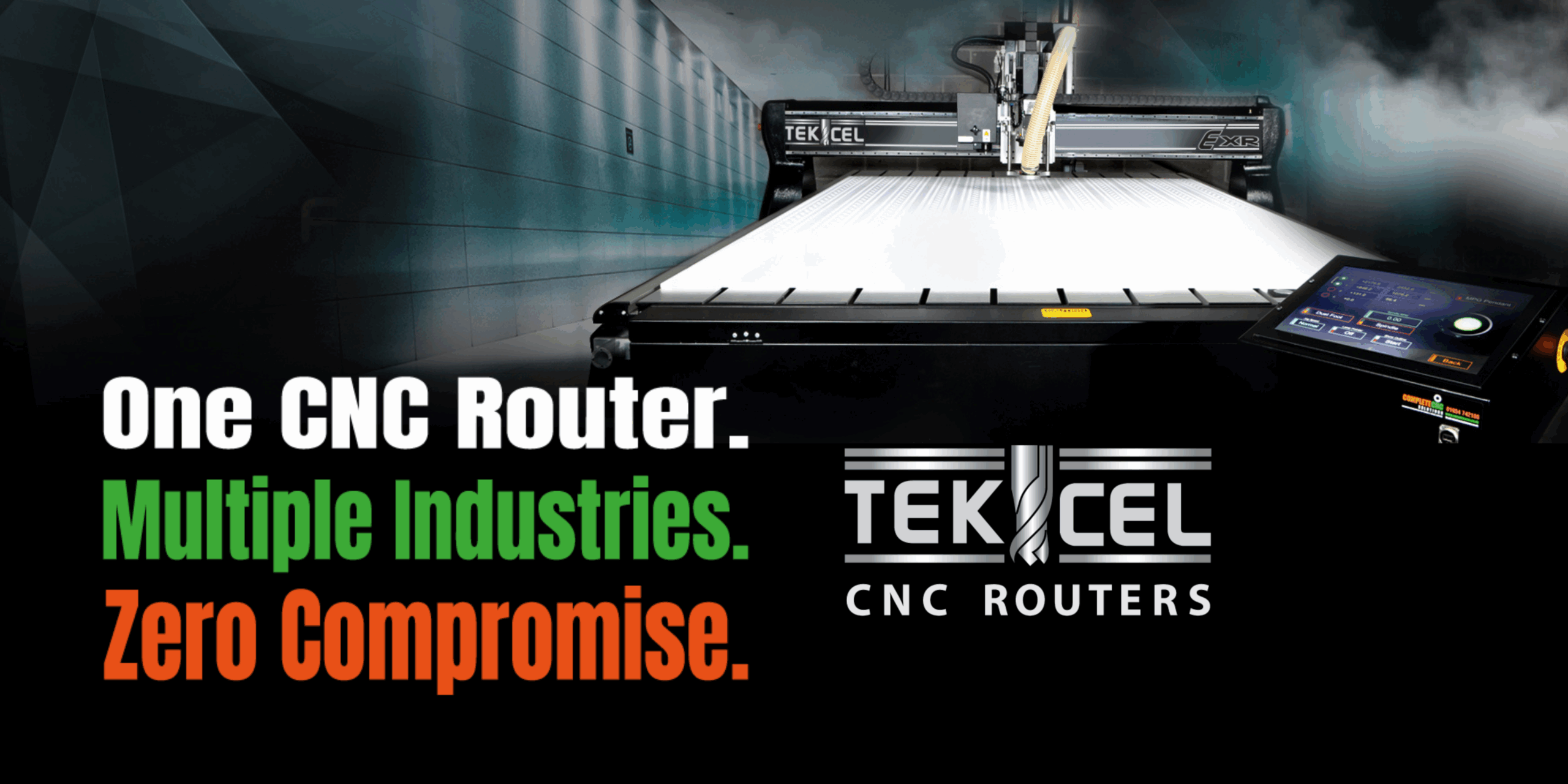
Why Case Makers Should Be Cutting Foam In-House With a CNC Router
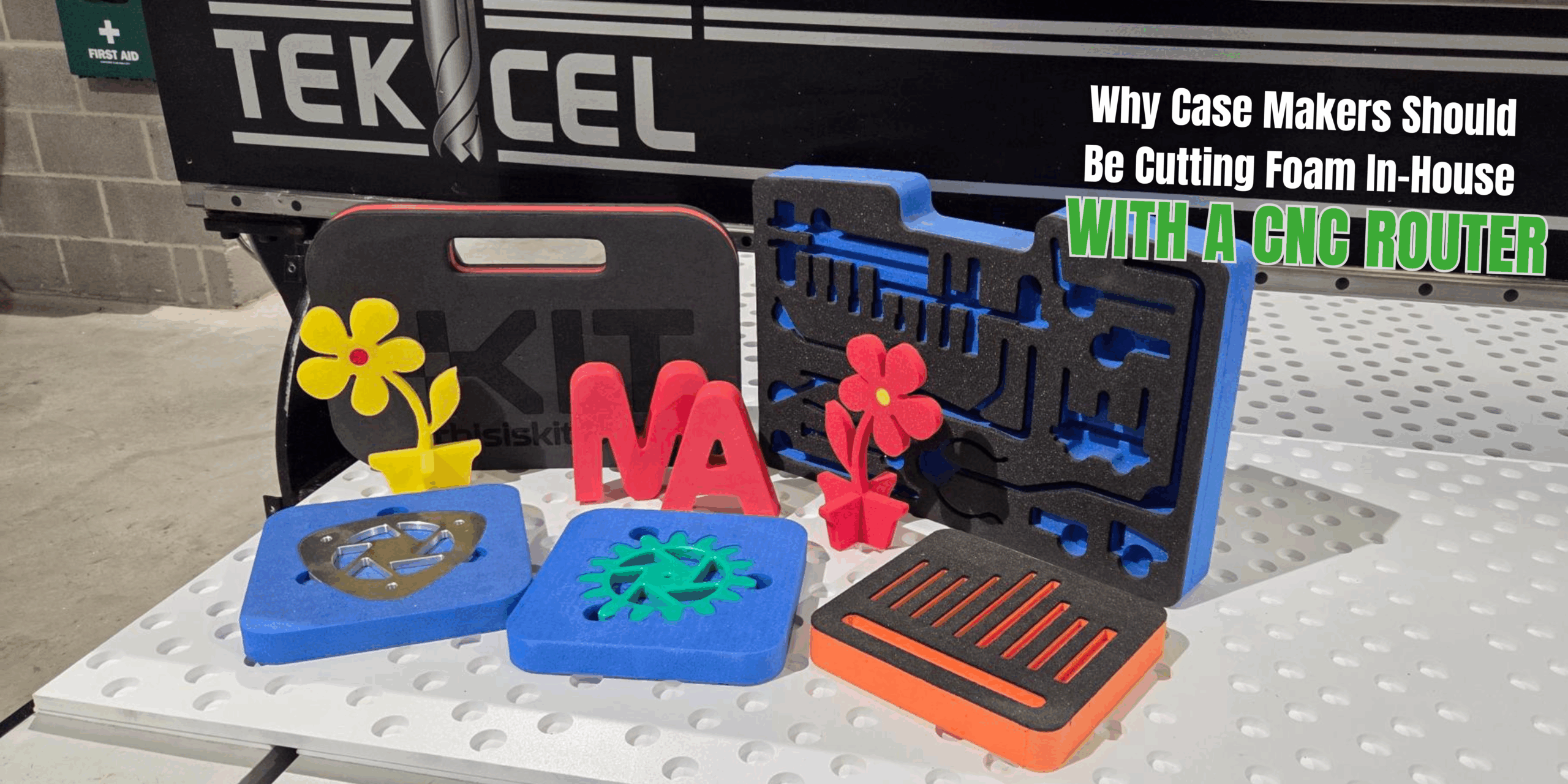
FAQ: What Tips Do You Have For Cutting MDF?
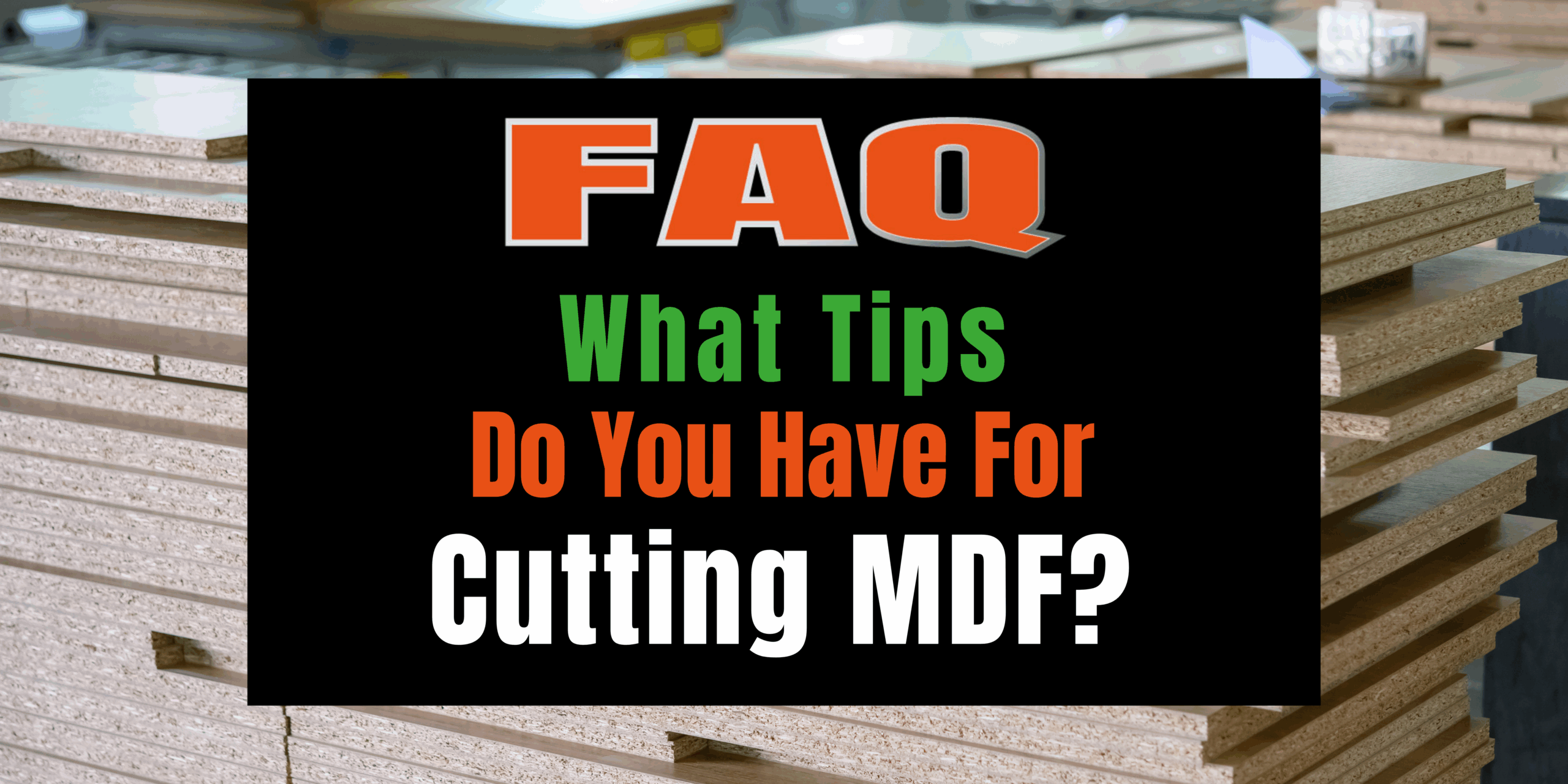
Thinking About Investing in a CNC Router?
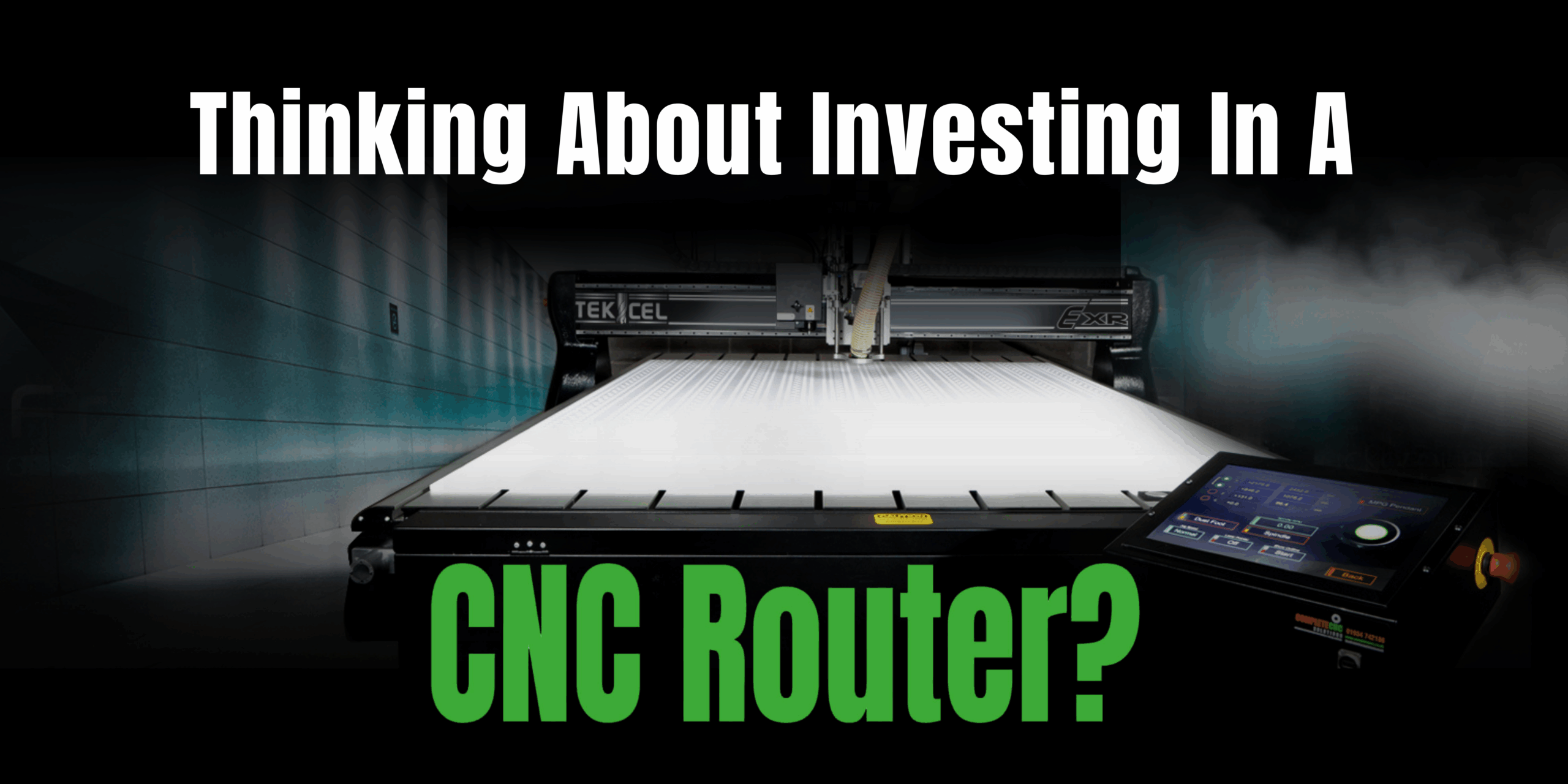
Why Tekcel EXR is the CNC Router You Need
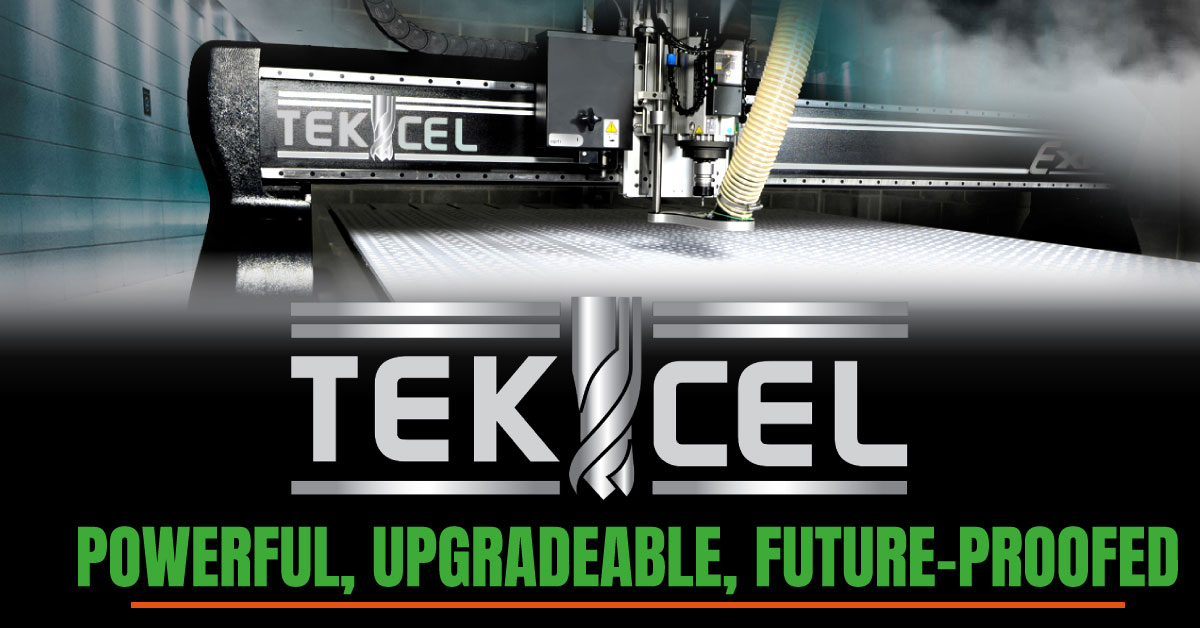
CNC Woodworking Without The Headaches
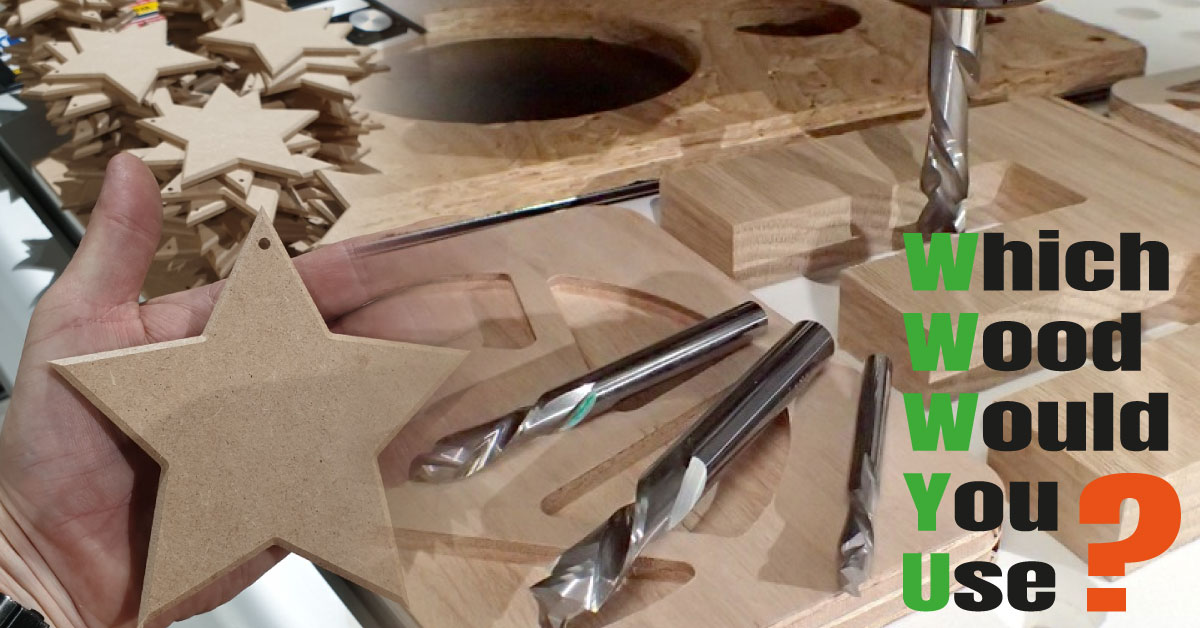
No More Botched Cuts on Plastics & Acrylics!
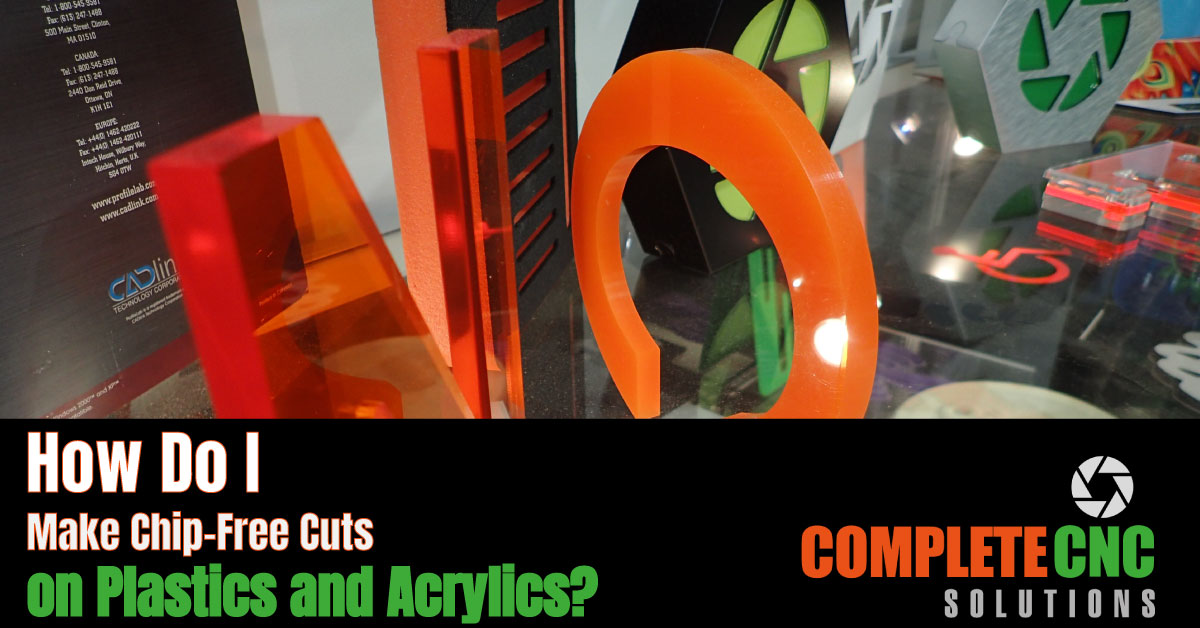
Struggling with Tool Wear?
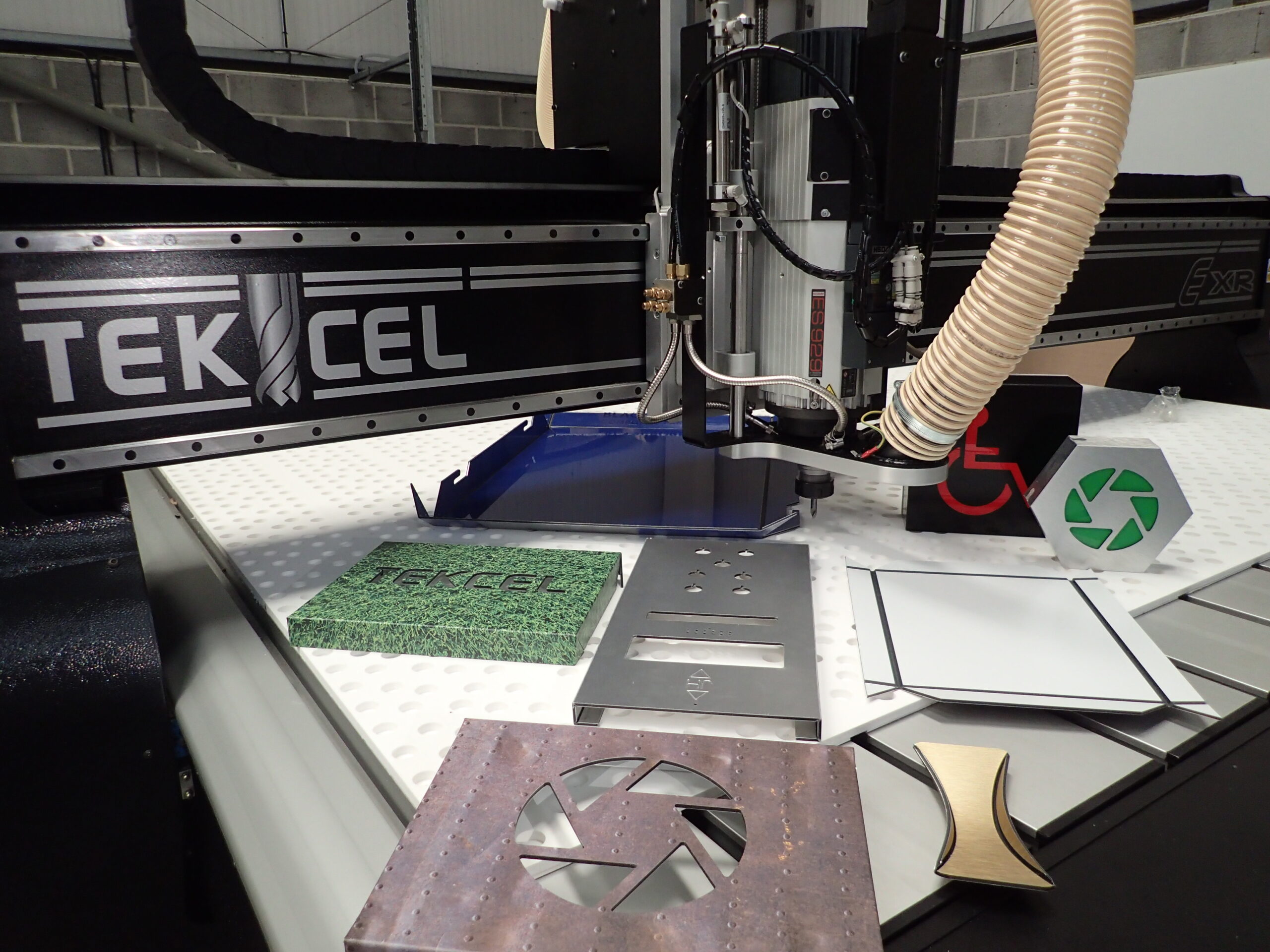
How to Successfully Cut Small Shapes Without Them Moving
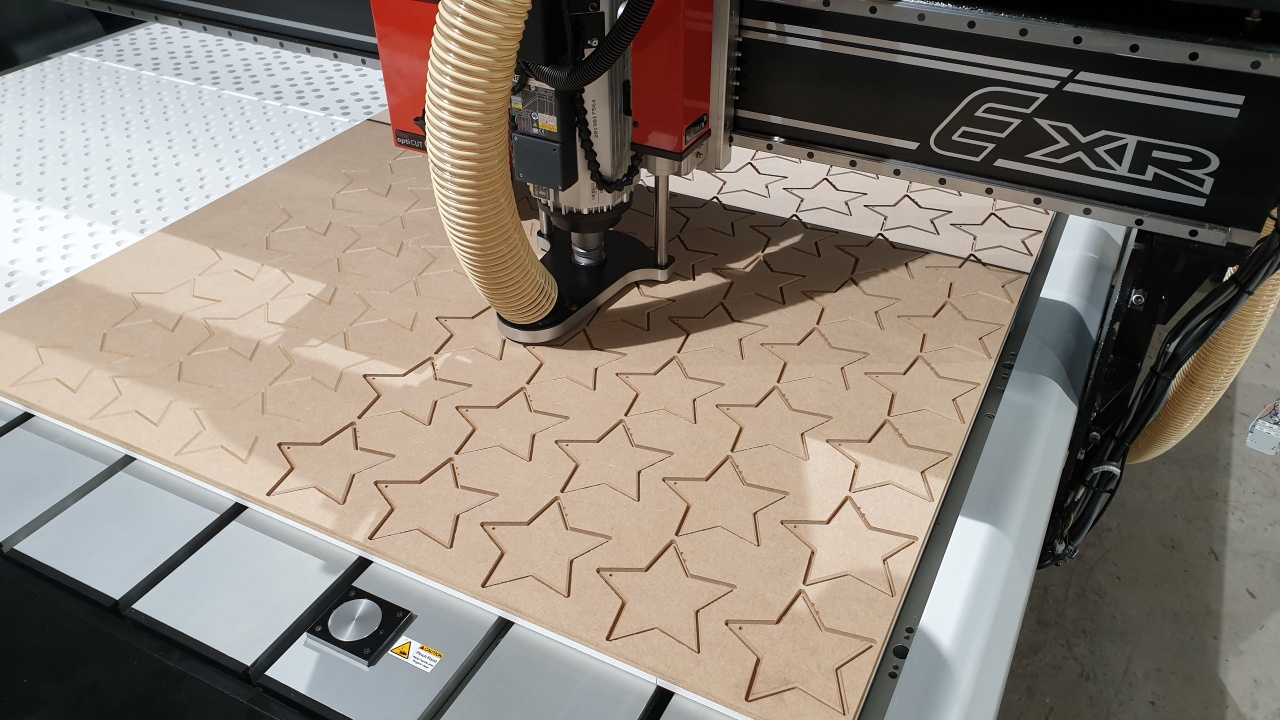
Documenting CNC Router Settings and Processes for Future Success
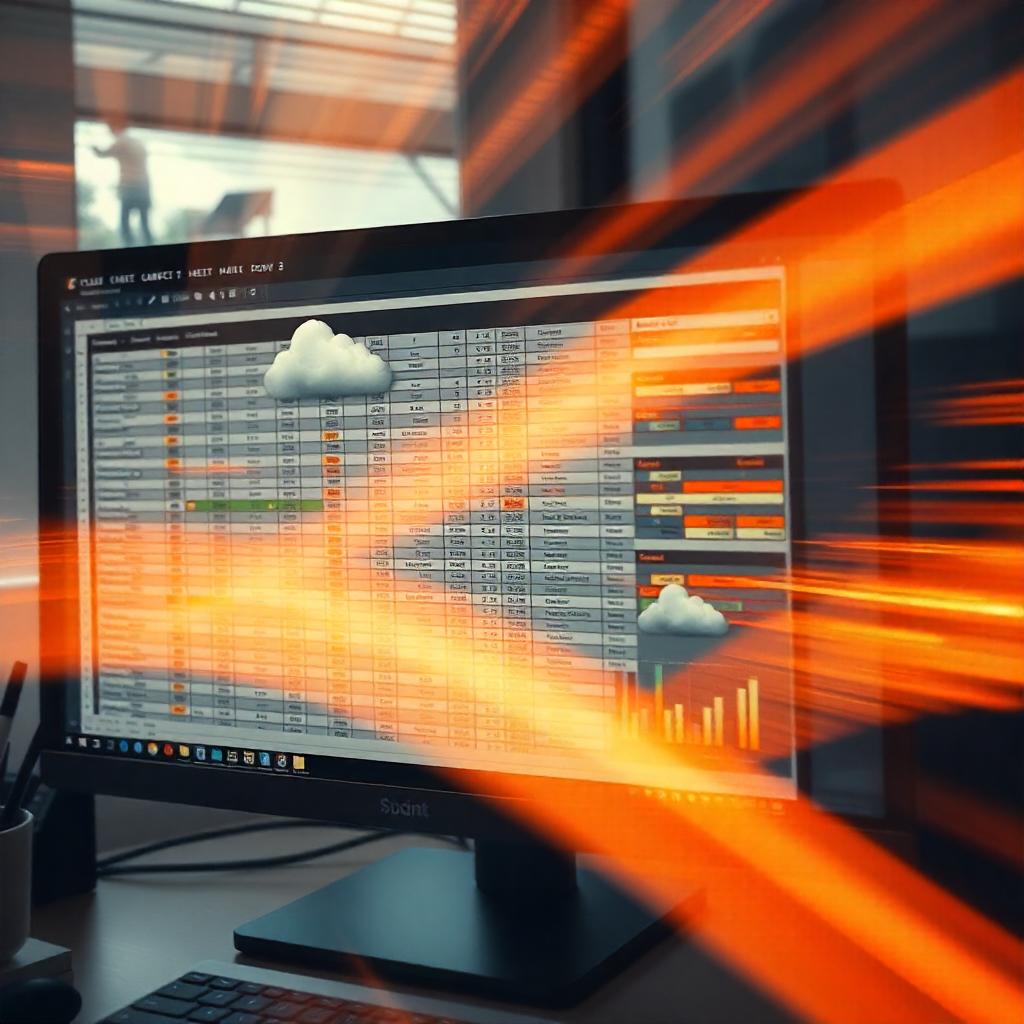
Training Tailored For Success With Your Tekcel CNC Router
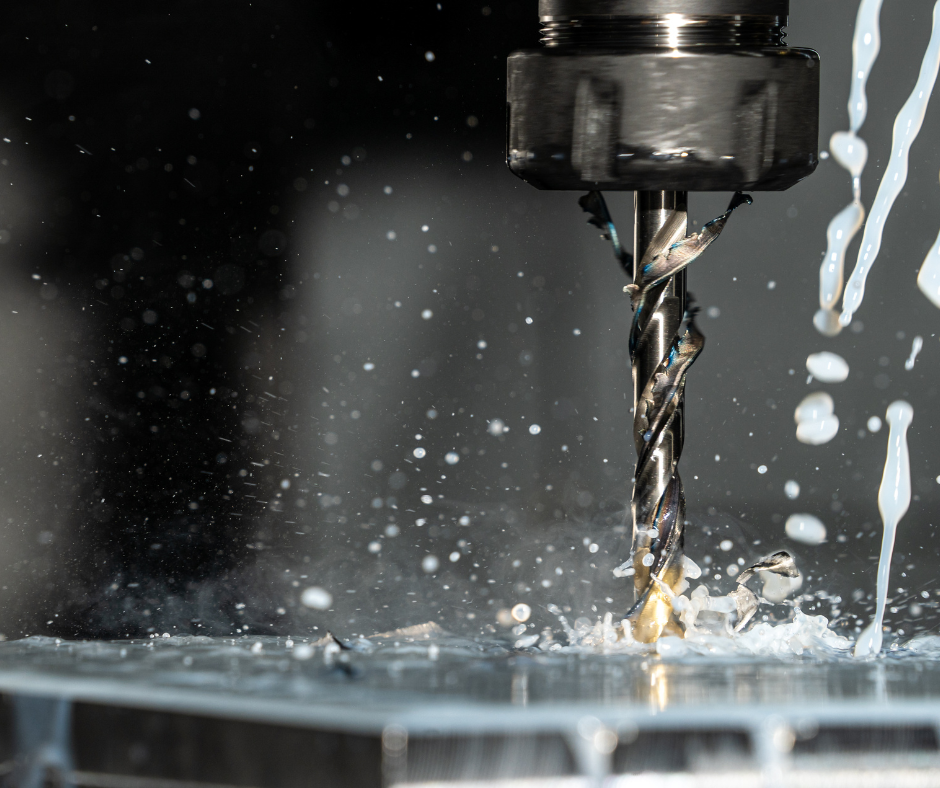
Stay Ahead with Software Updates for Your Tekcel CNC Router
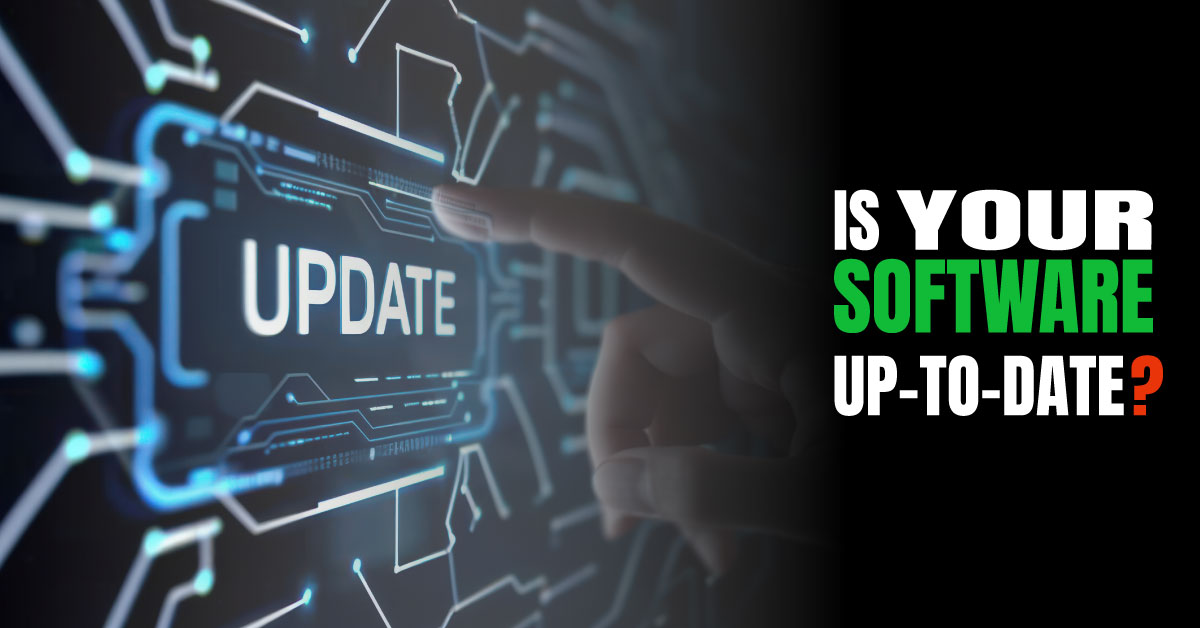
Revolutionise Signage with Tekcel CNC and Precision ACM Tooling
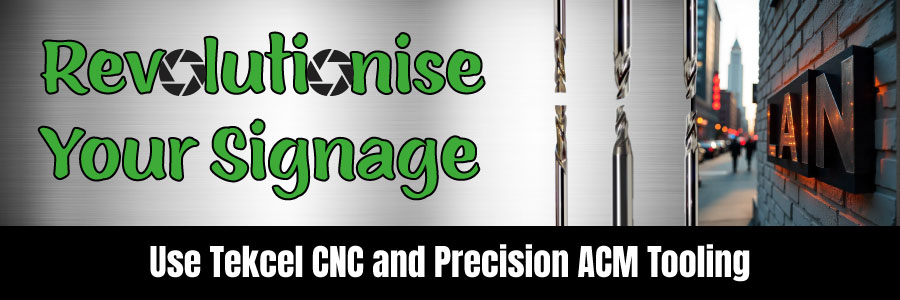
Cutting it Close? Know When to Change Your Collet for Safe, Sharp Results
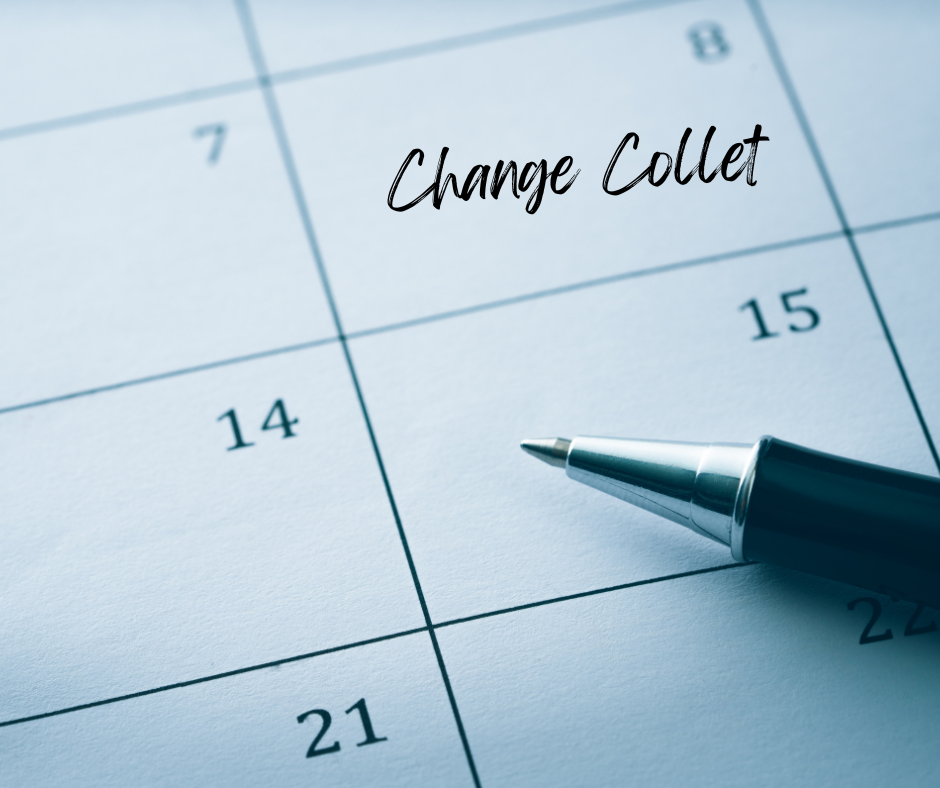
How to Avoid Burning and Furring When Cutting Wood with a CNC Router
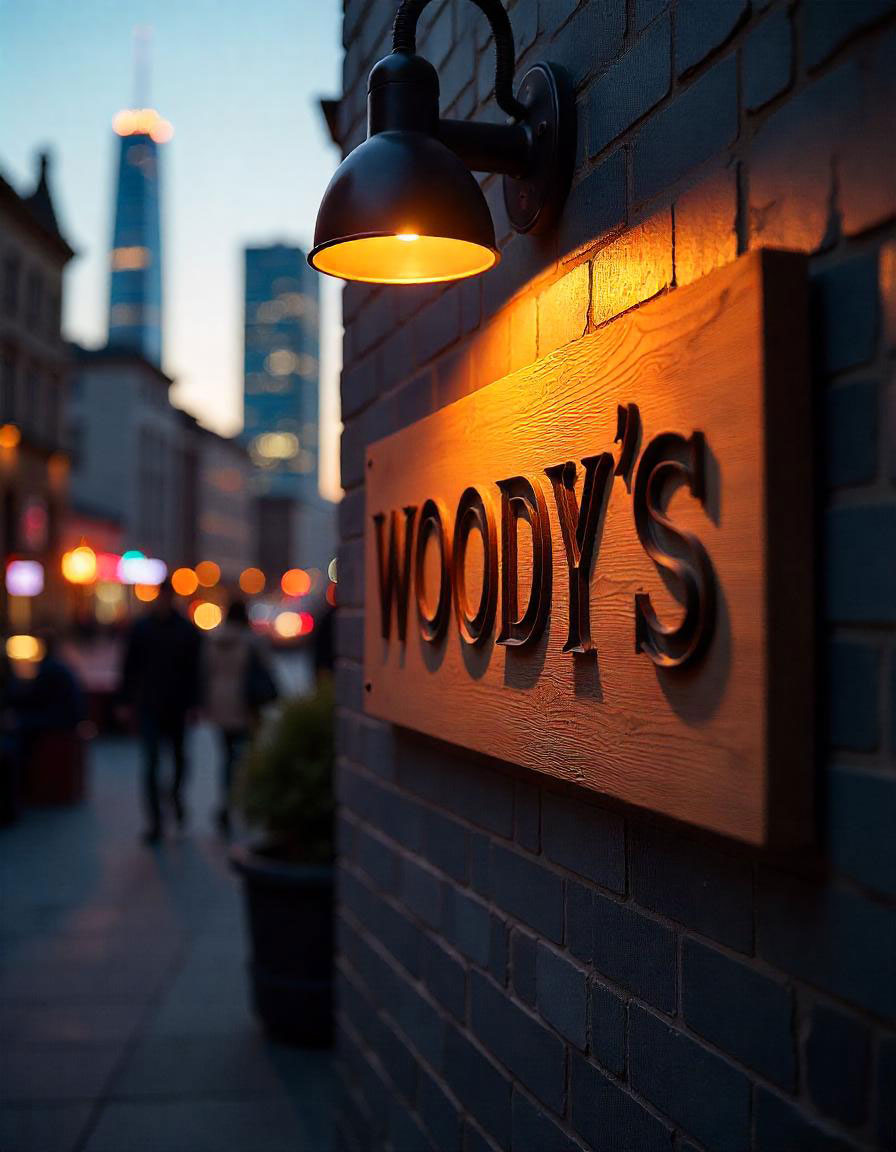
How to choose the right CNC tool for the job/material
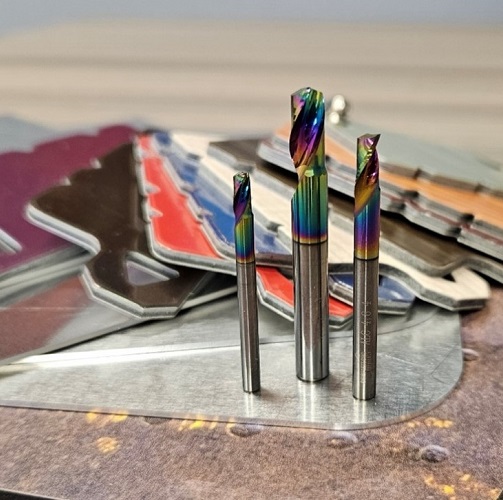
Which CNC Router covers all the bases for a signage manufacturer?
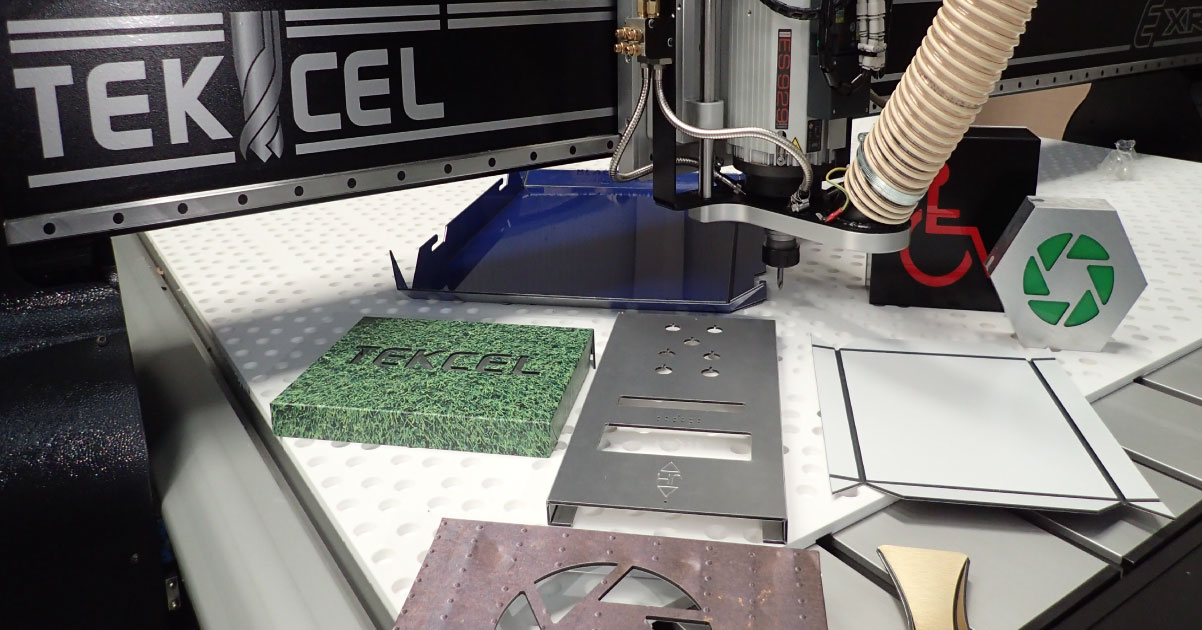
The Tekcel – High Pressure Mist Coolant System for Metal Cutting
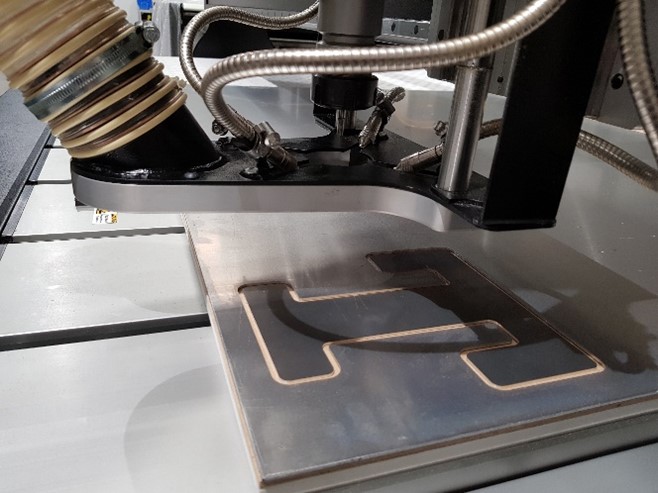
Tekcel CNC Routers – Furniture & Woodworkers dream machine
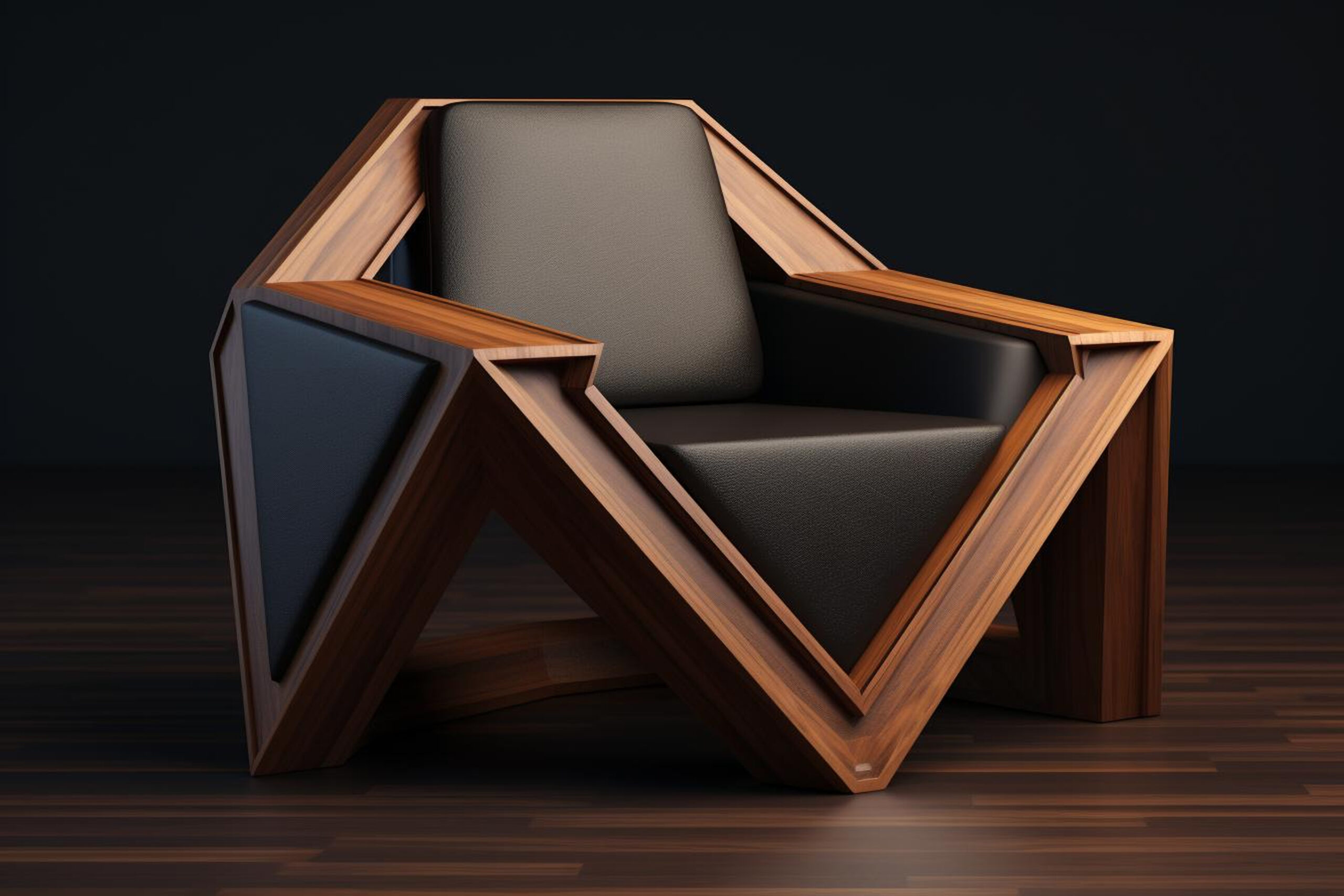
Start with a “Tekcel CNC” for the best finish…
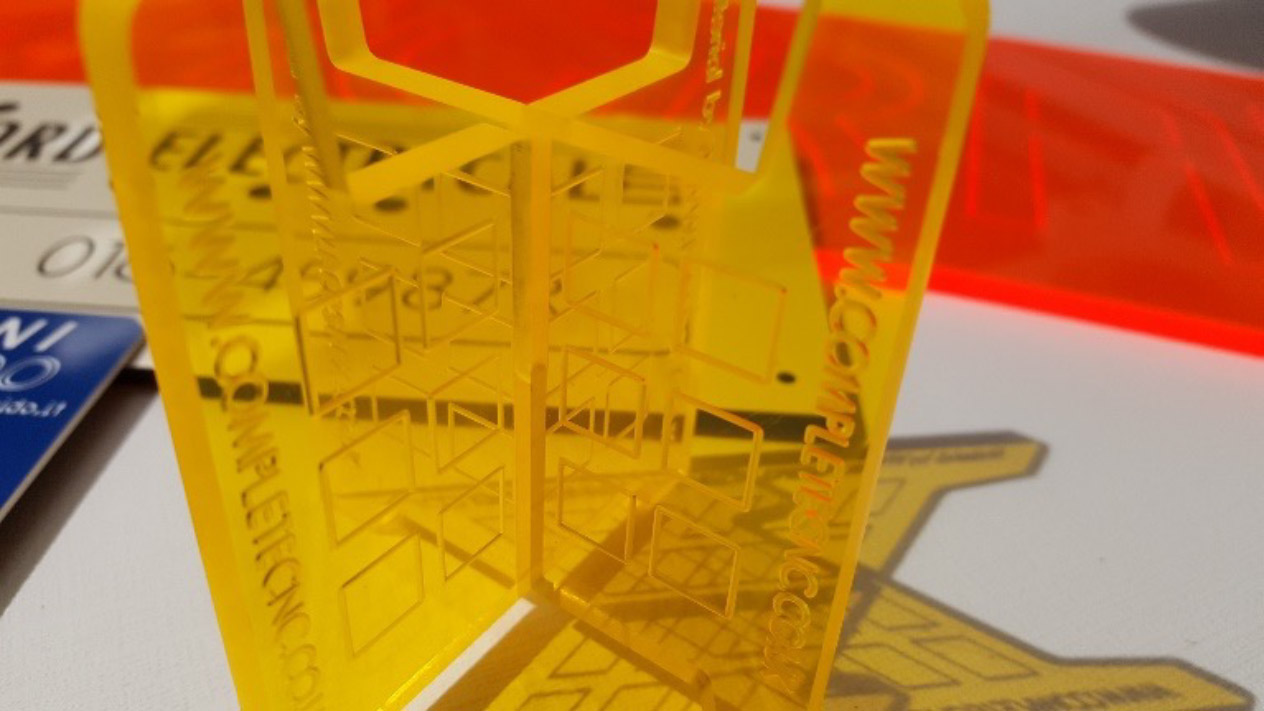
Under the Bonnet of a Tekcel EXR CNC Router
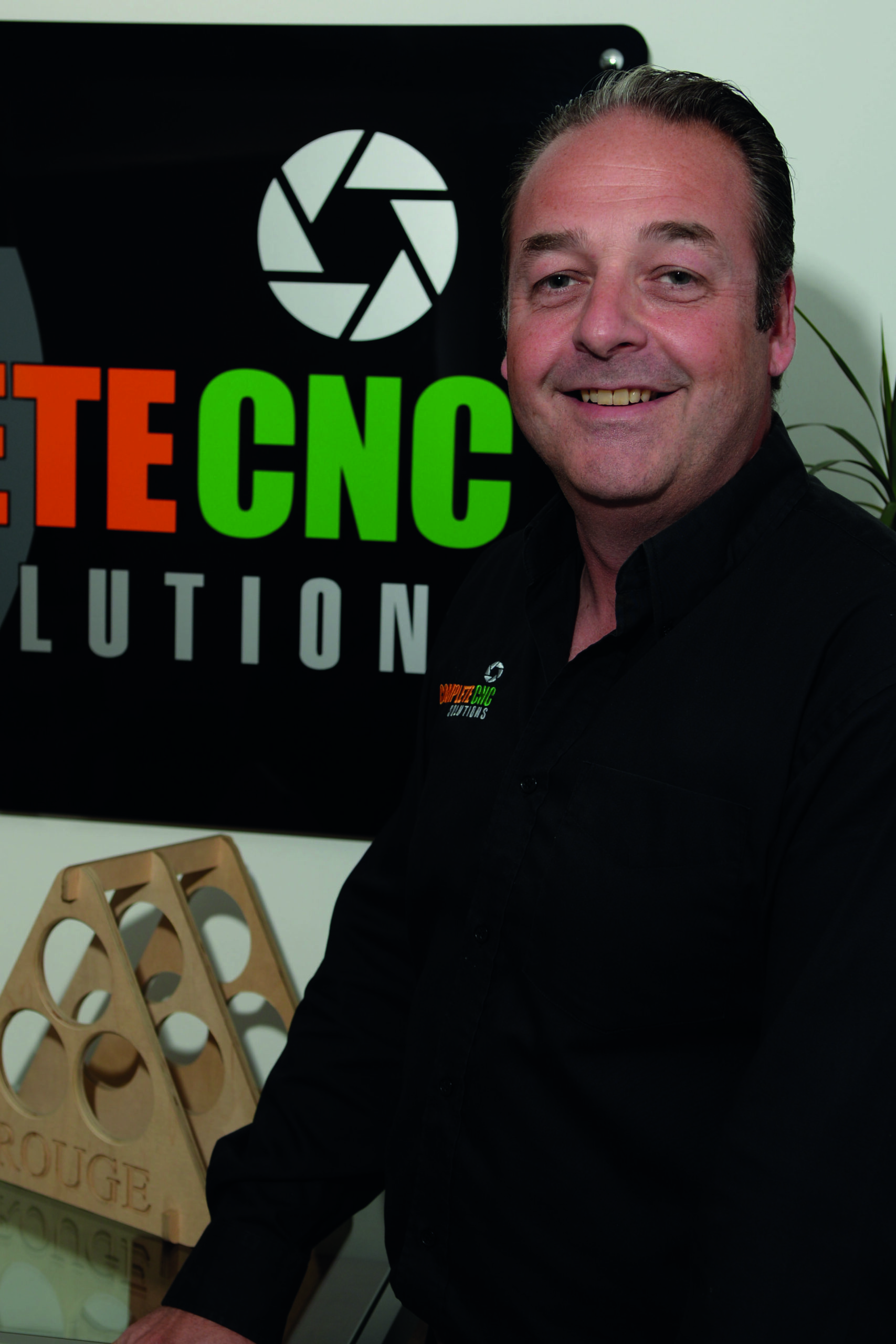
How to Skim the MDF Sacrificial Bed on your Tekcel CNC Router: A Step-by-Step Guide
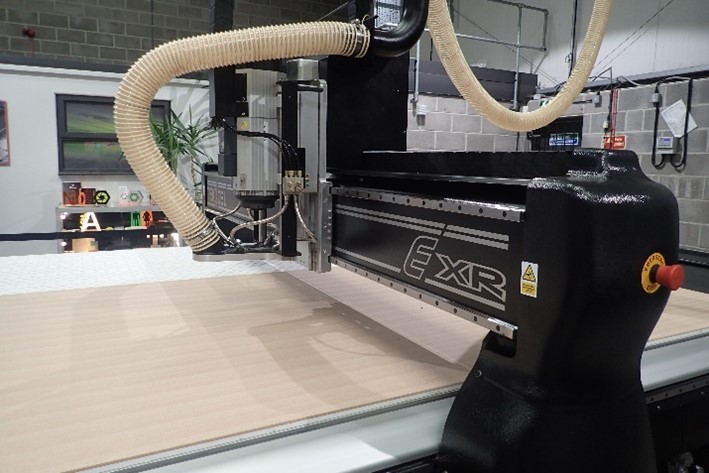
What is an ATC and why do I need one?
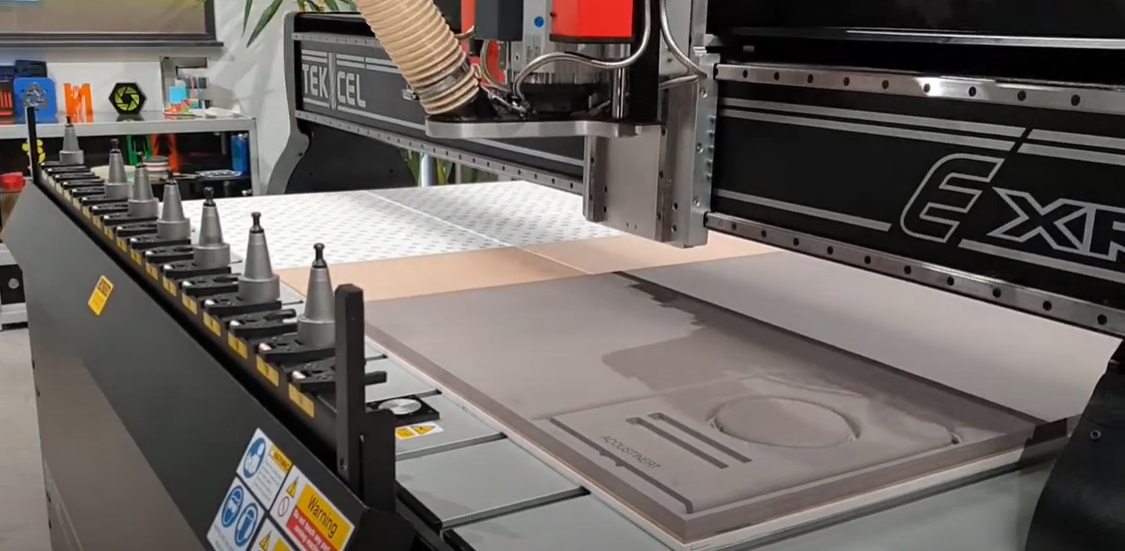
Tekcel CNC for ACM (Aluminium Composite Material) Signage:
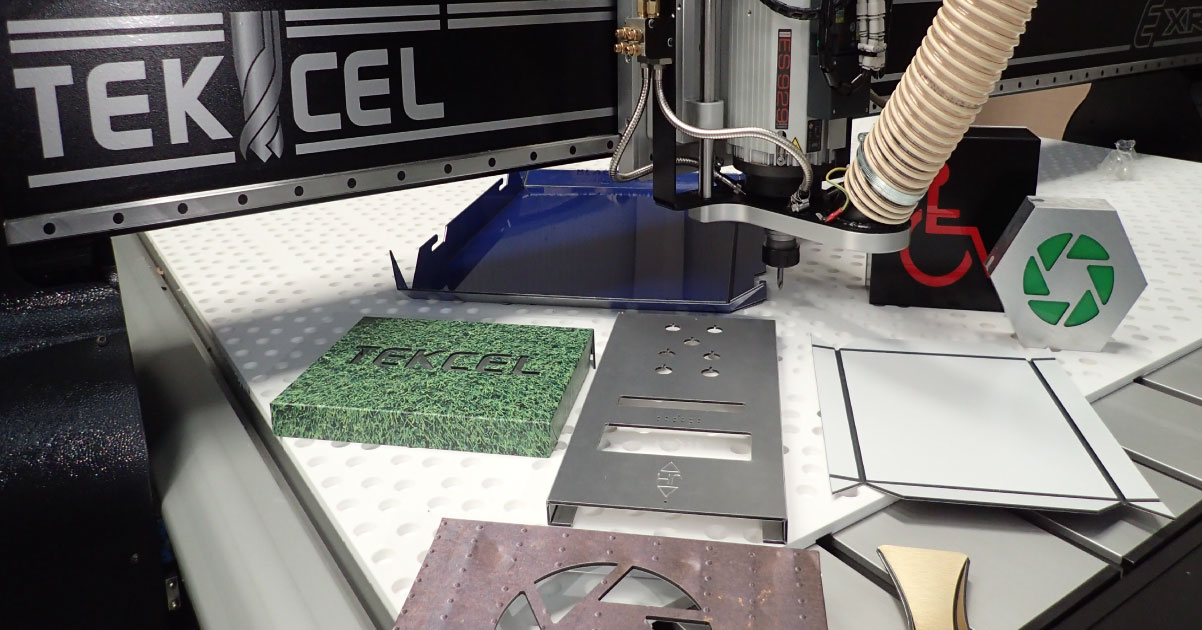
The Benefits of Acrylic
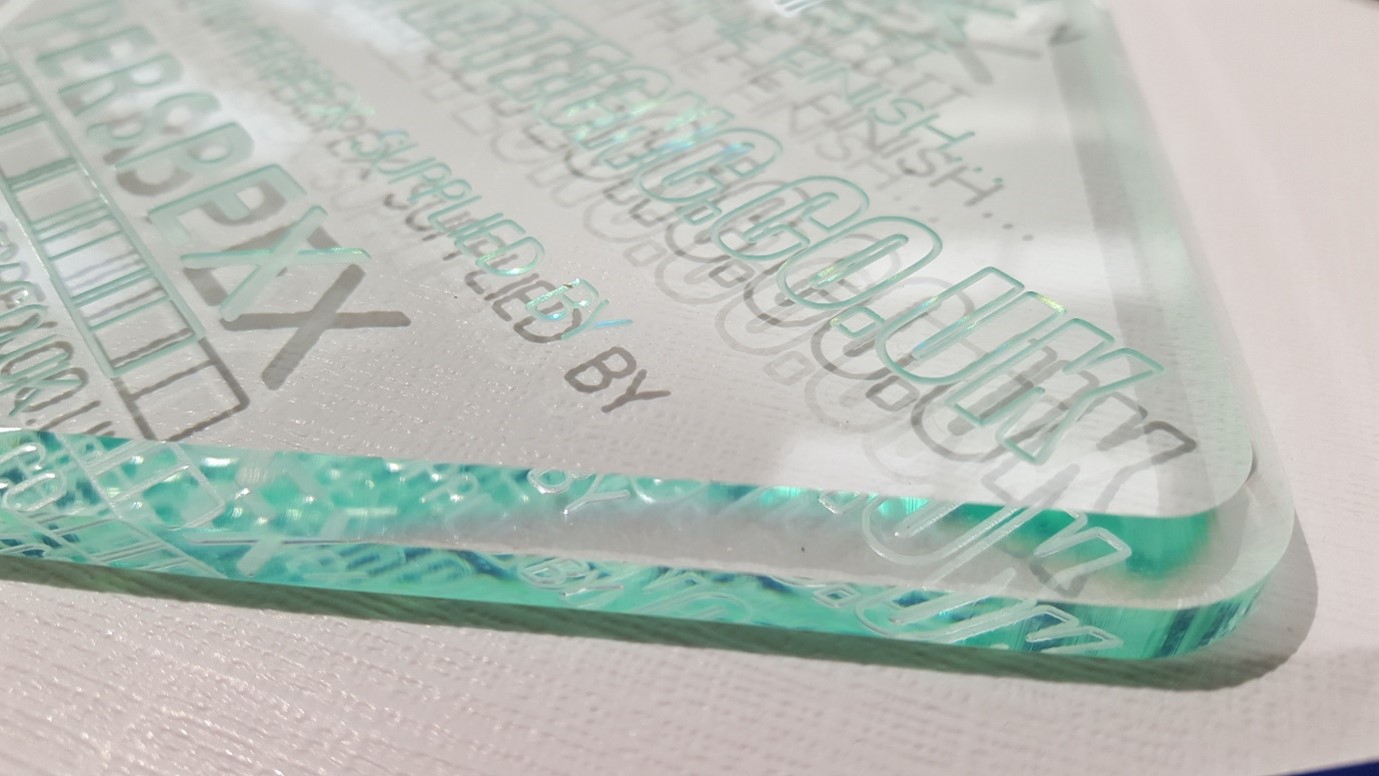
CNC for DFM
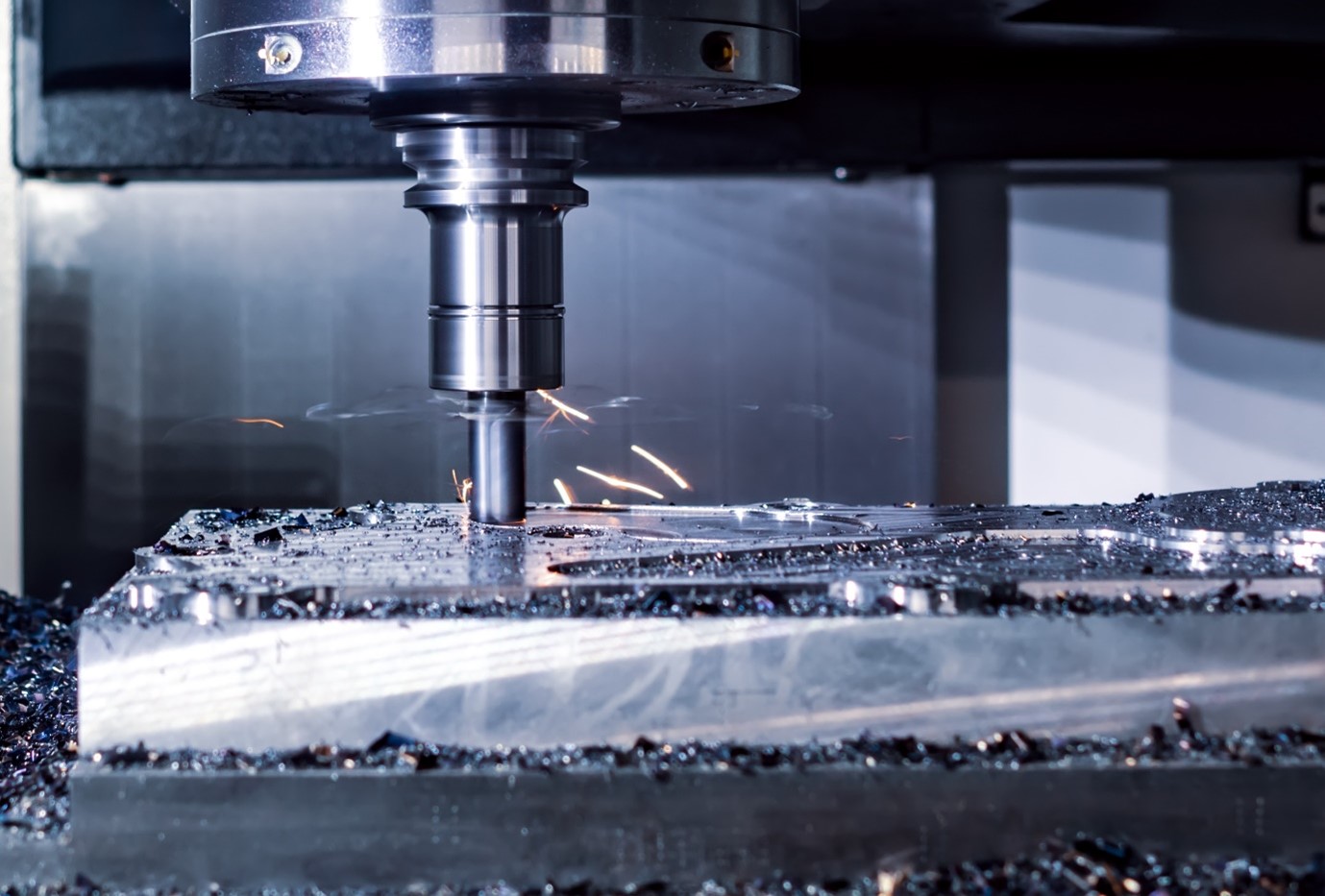
The Unbreakable Rules!
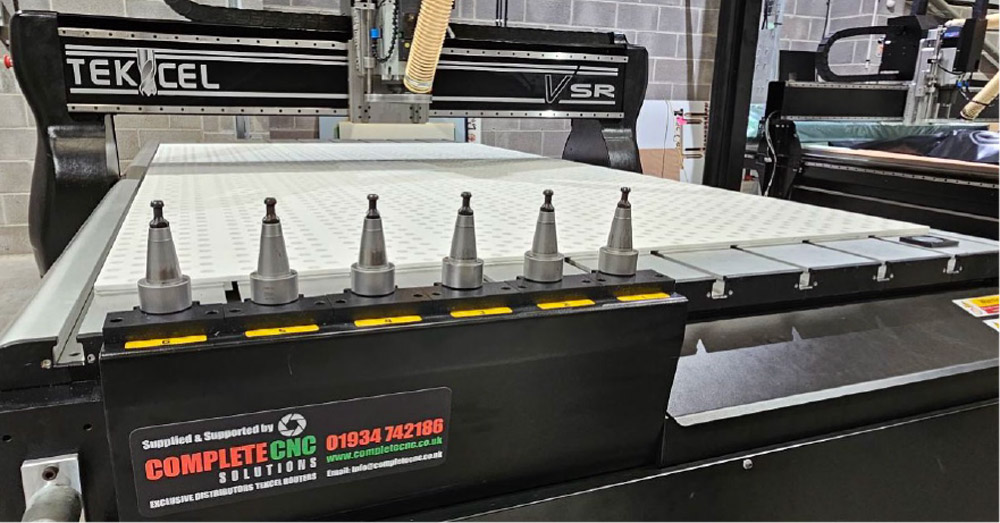
Welcome to the world of CAD/CAM
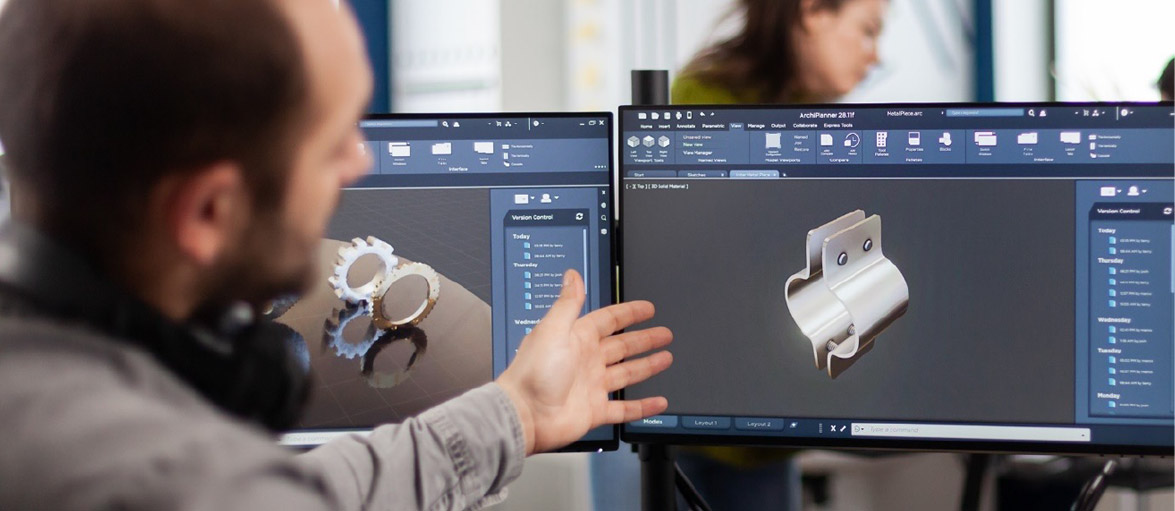
10 Tips for Successful Aluminium Cutting with CNC Routers
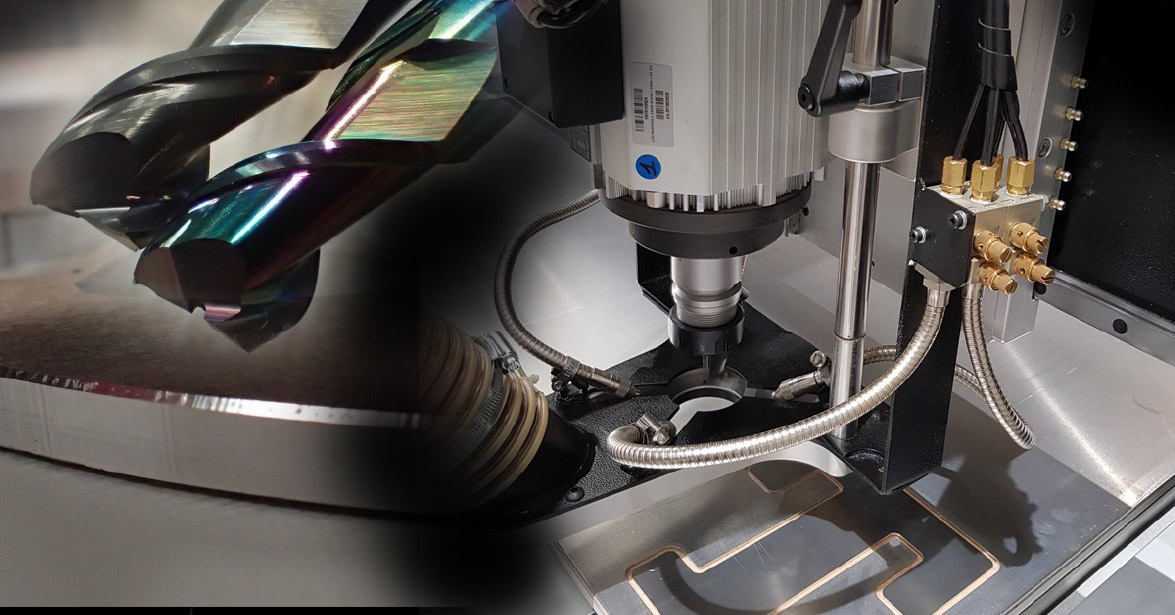
Mastering the Art of Tekcel CNC Router Speeds and Feeds: A Comprehensive Guide
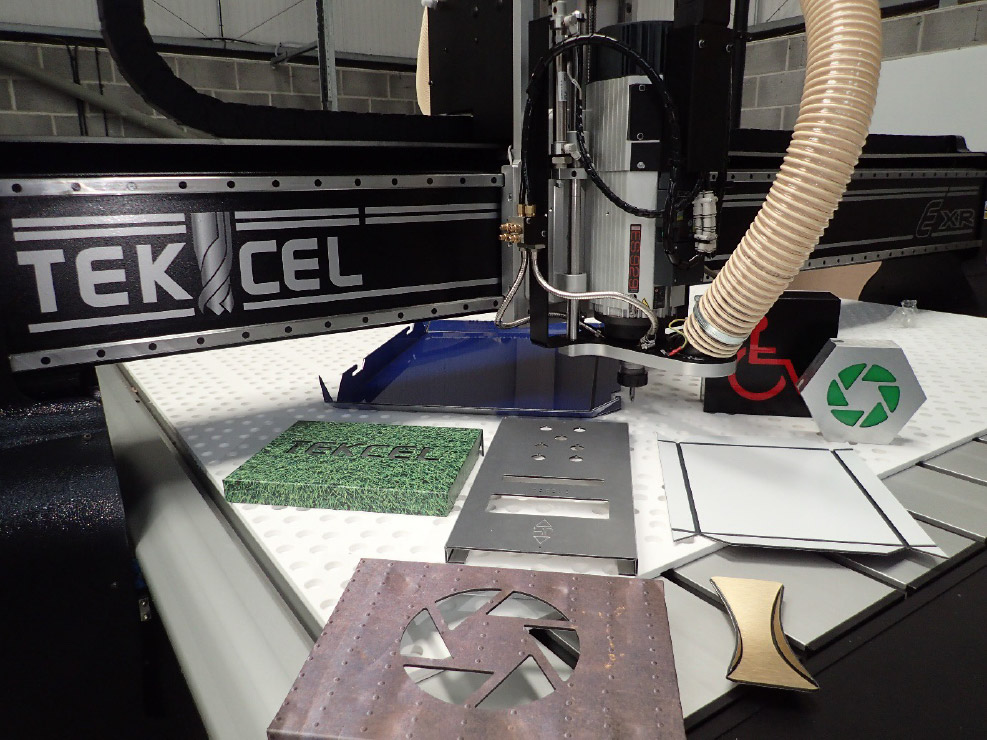
CNC Routers For Sign Making
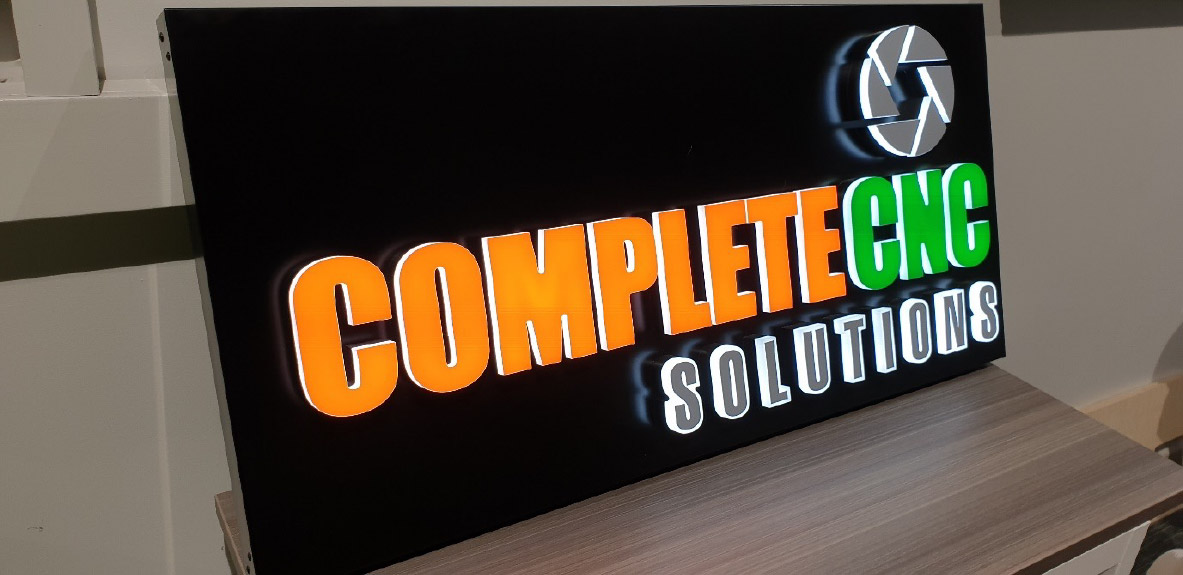
Cutting Acrylic With Your CNC Router
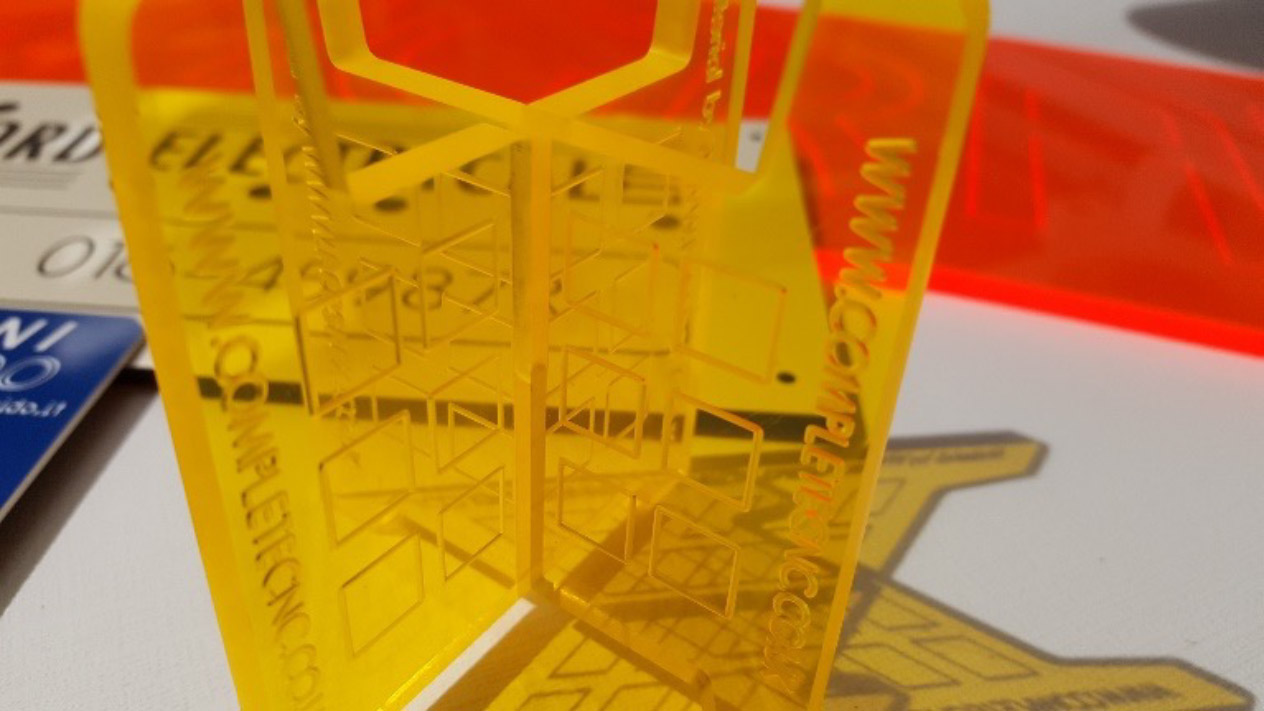
Collets: An Essential Tool
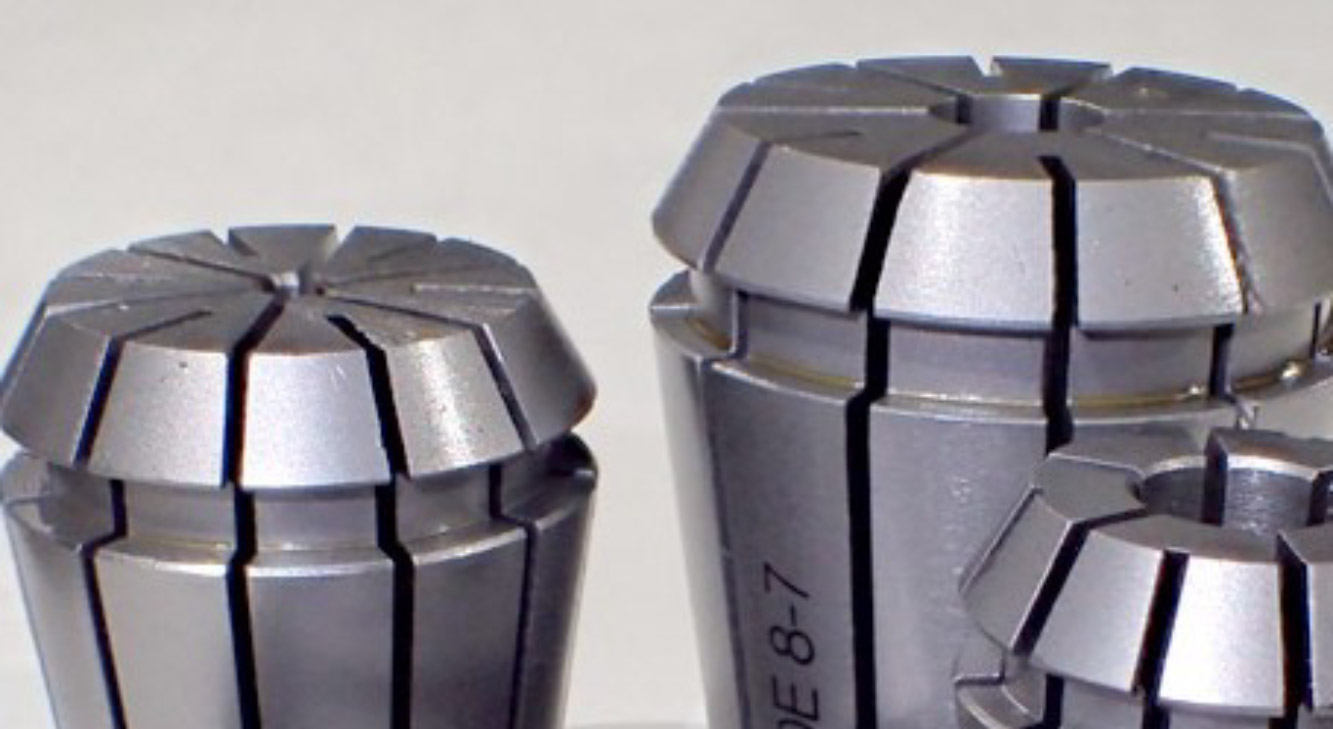
Calling all converters: How CNC Routers Elevate Vehicle Conversions
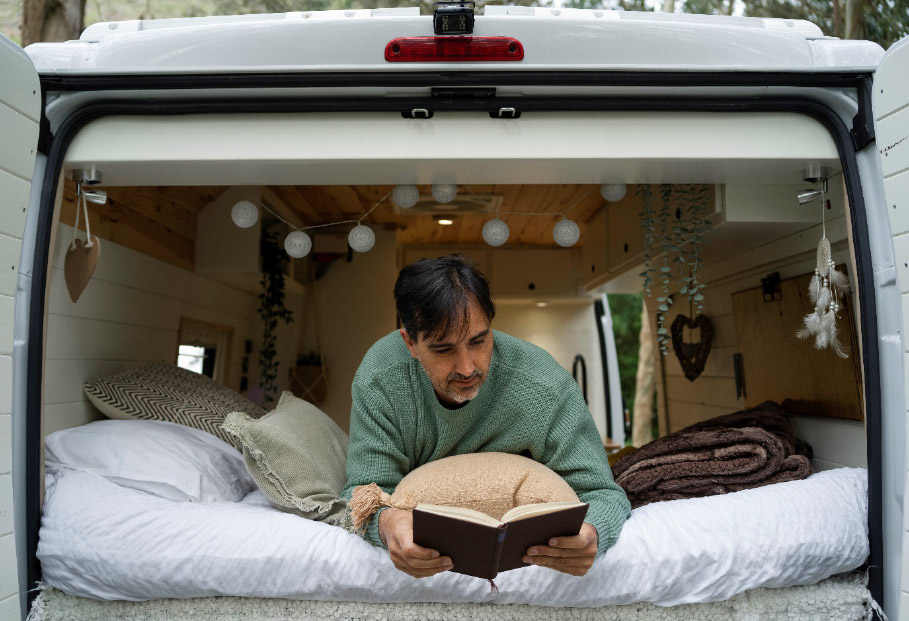
The Right tool for the job
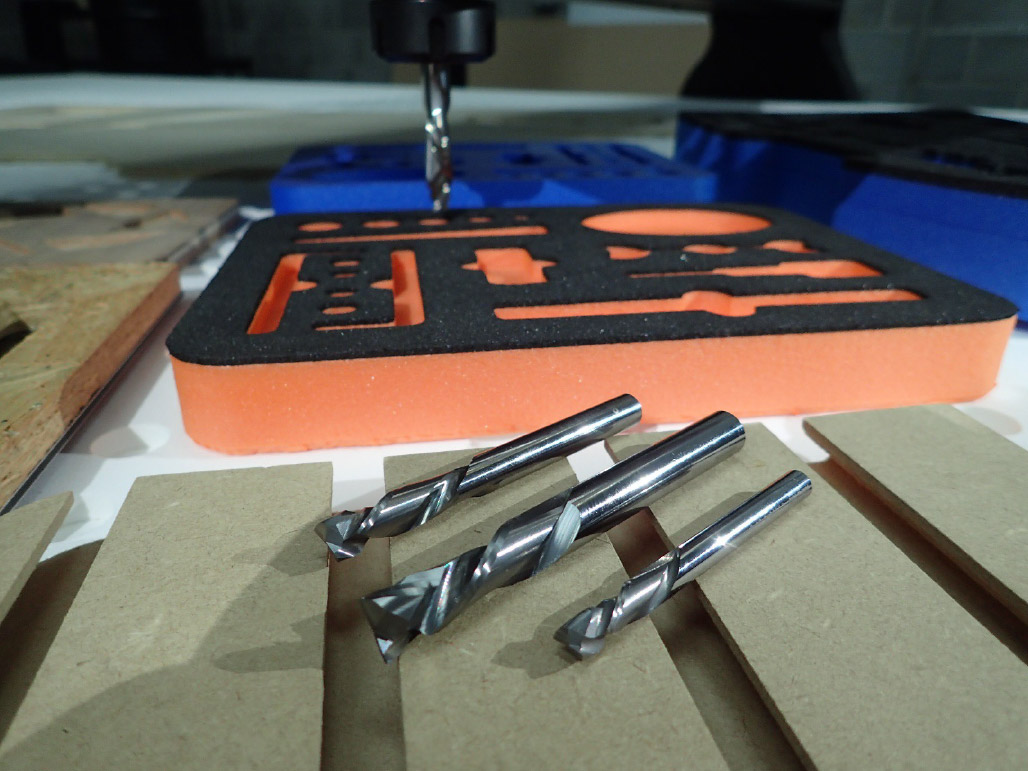
What is the cutting speed of a CNC router?
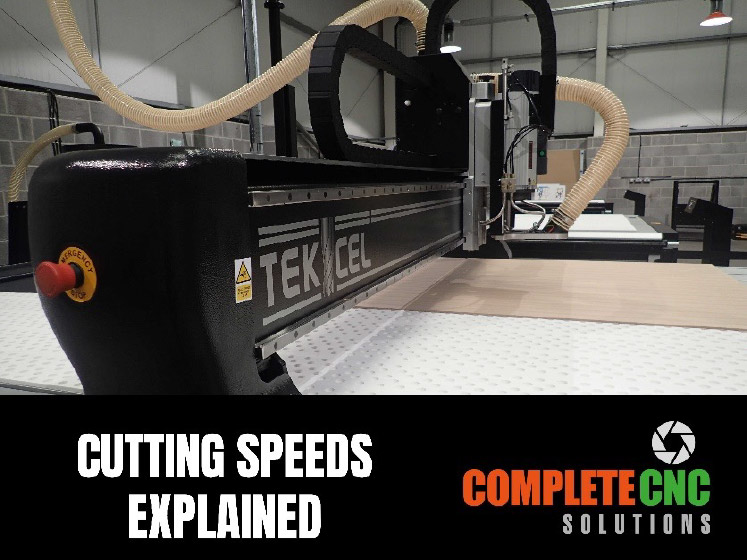
Unravelling the Mystery: Common themes overlooked with CNC Routers
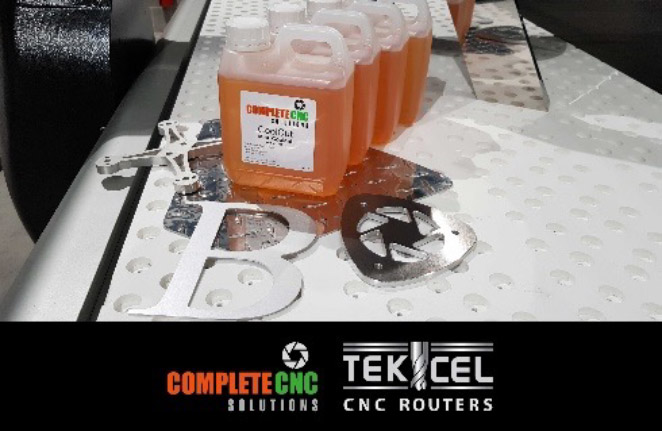
CNC Router Maintenance Guide for Longevity and Efficiency
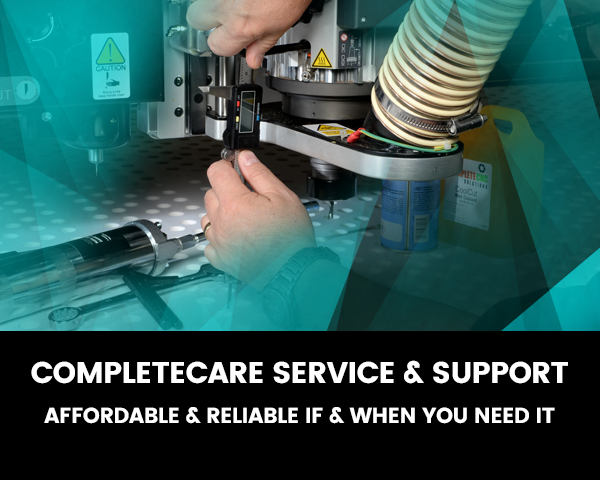
Tekcel Graphical User Interface
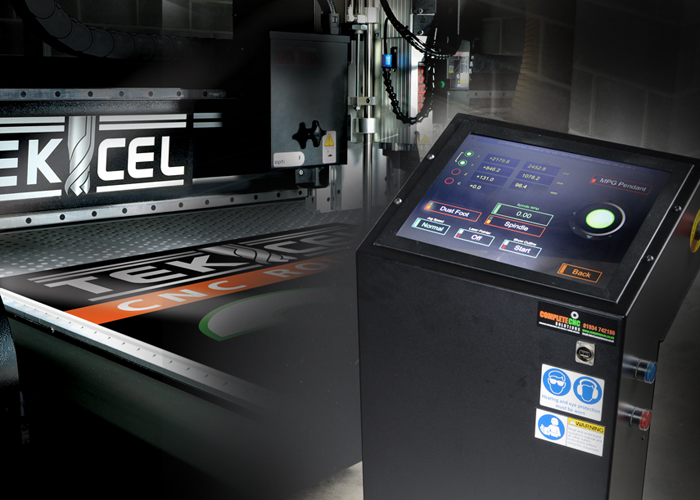
Unlock the World of Carving with CNC Routers!
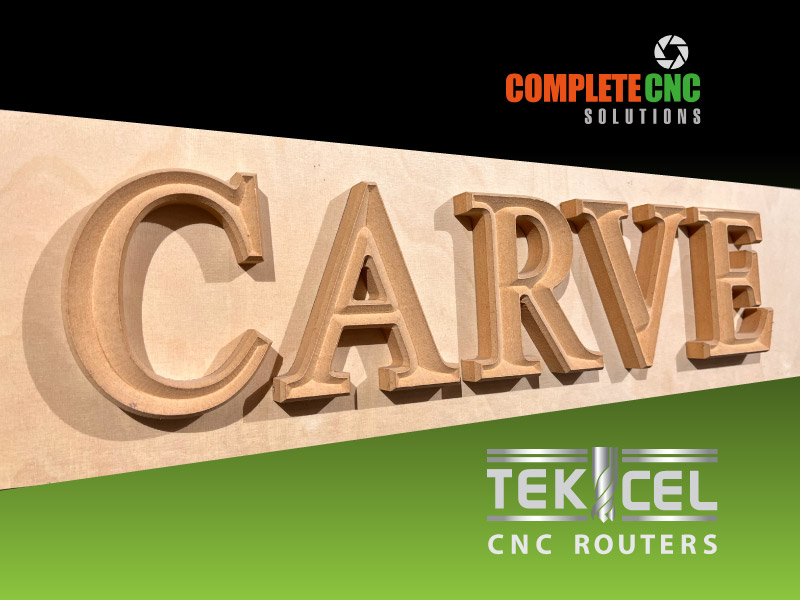
Can a CNC Router Carve Intricate Details? Yes!
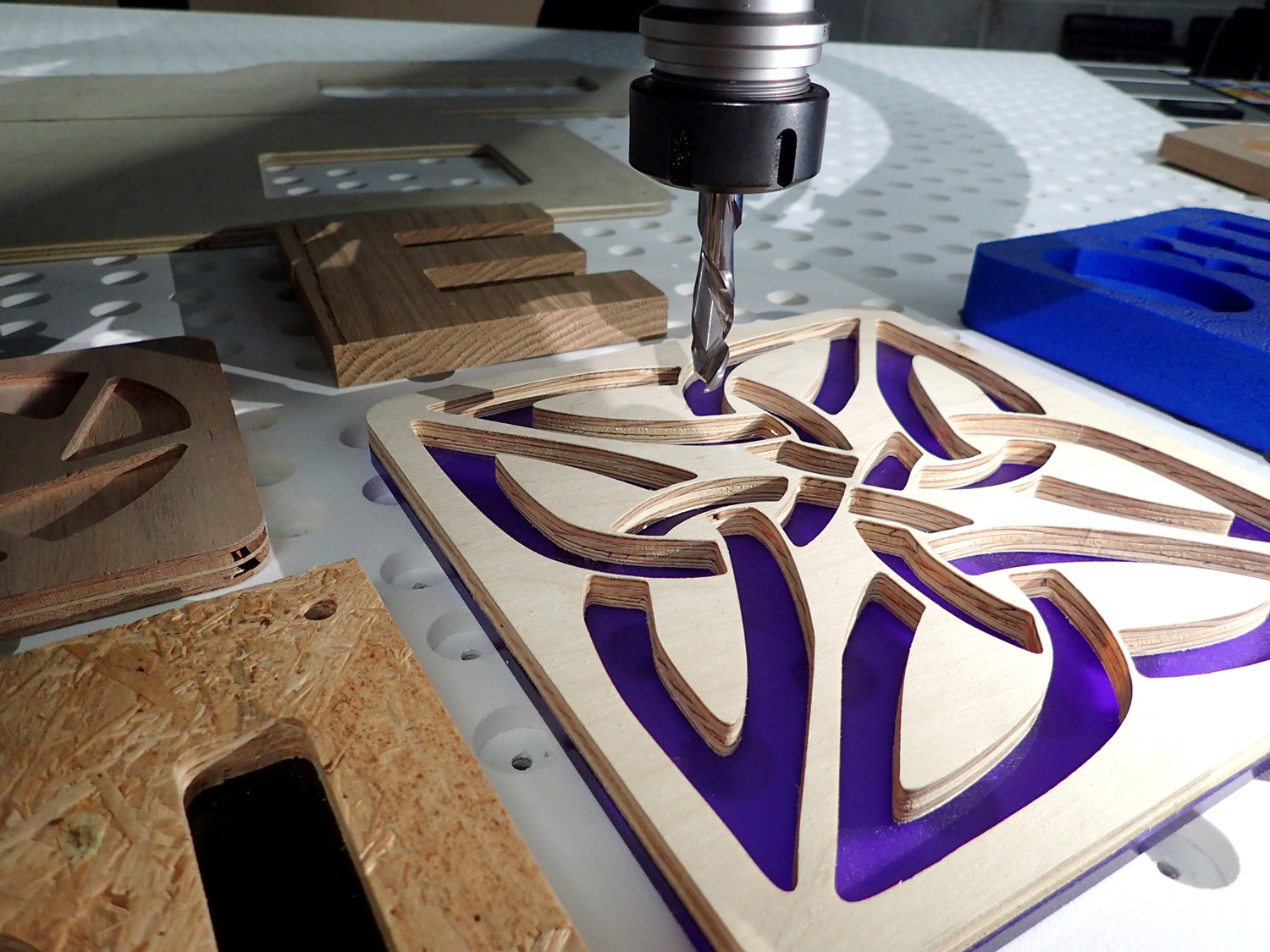
How a Tekcel CNC machine can provide value for your business
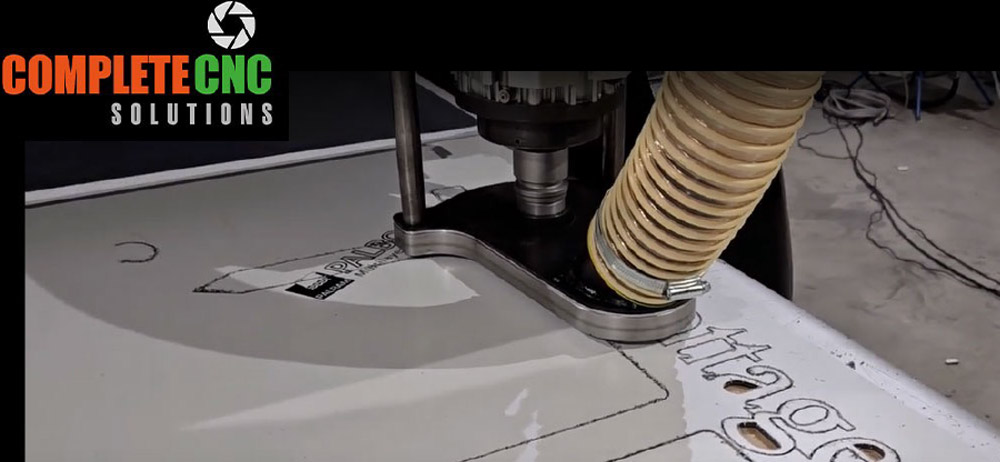
Elevating Point of Sale Production with CNC Machines
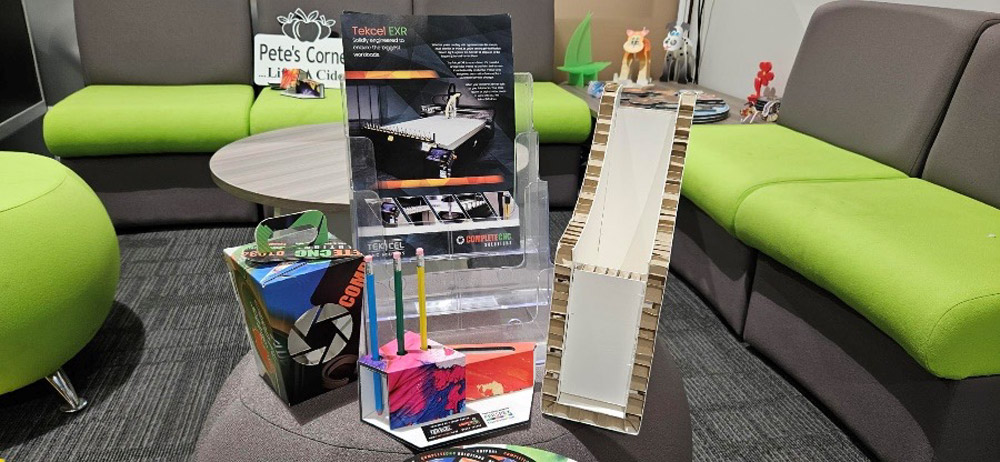
Why Sign Makers are Upgrading to CNC Cutting Machines
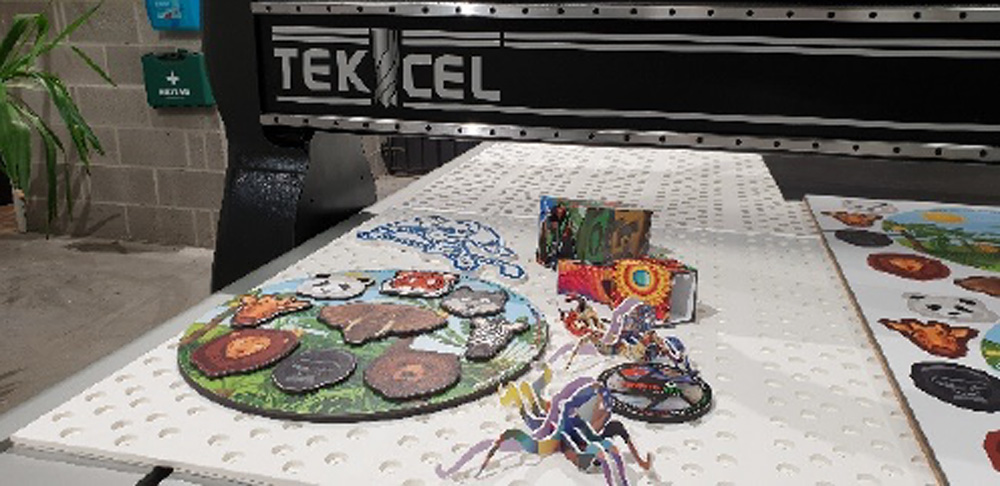
Hibernating Your CNC System During Lockdown.
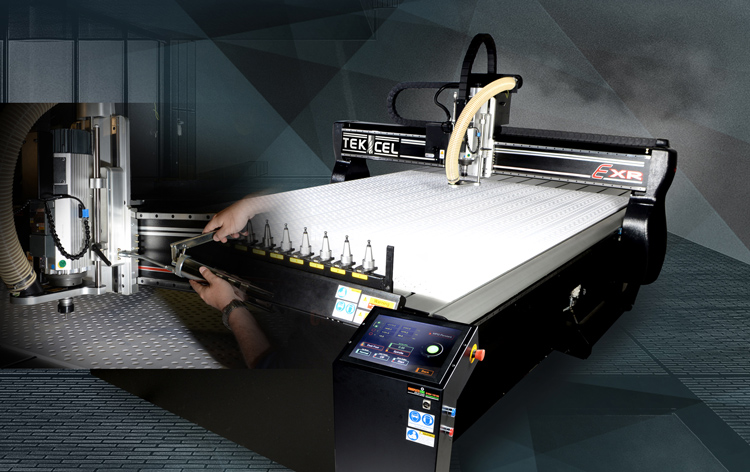
START BIG. GET BIGGER.
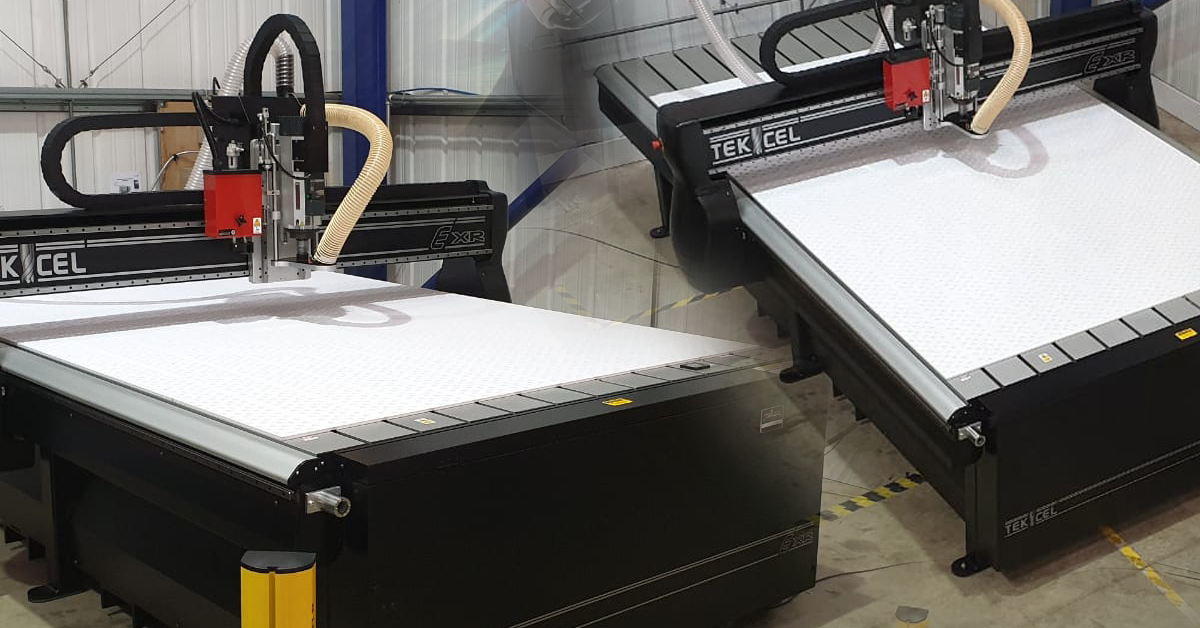
START WITH THE FINISH. FINISH WITH A PROFIT.
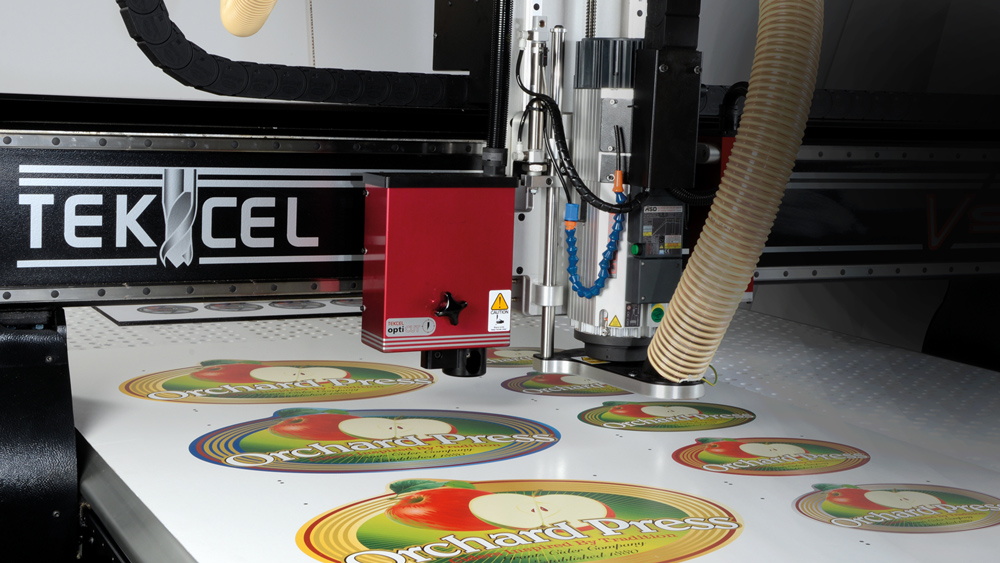
HEAVY METAL. LIGHT WORK.
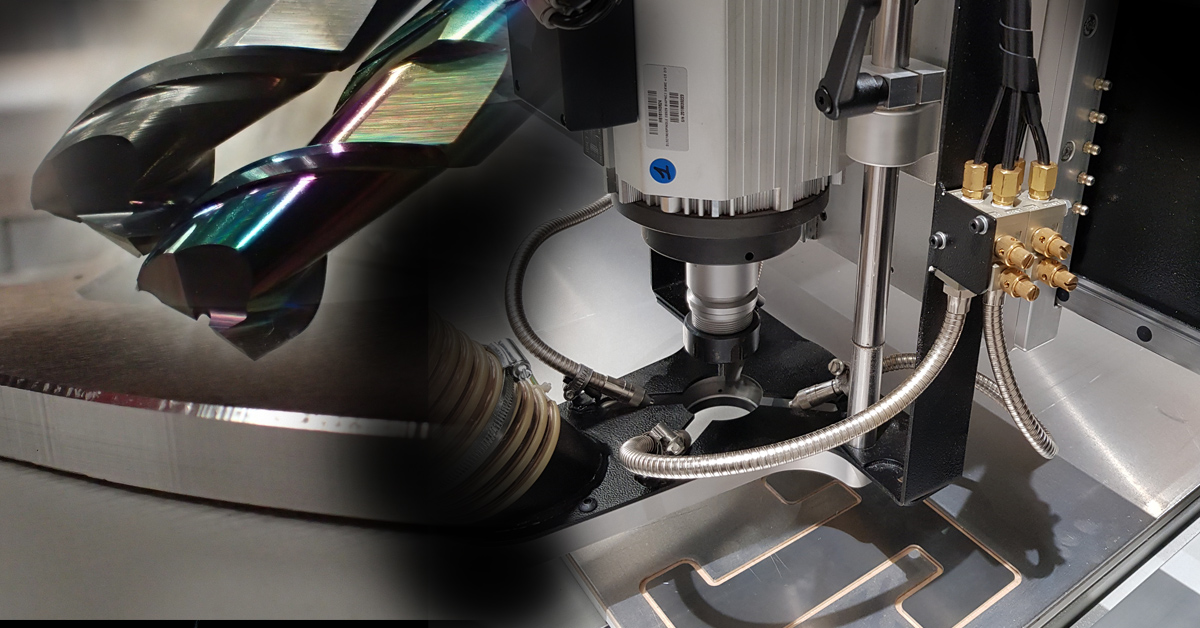
MAKE MORE WITH CORREX
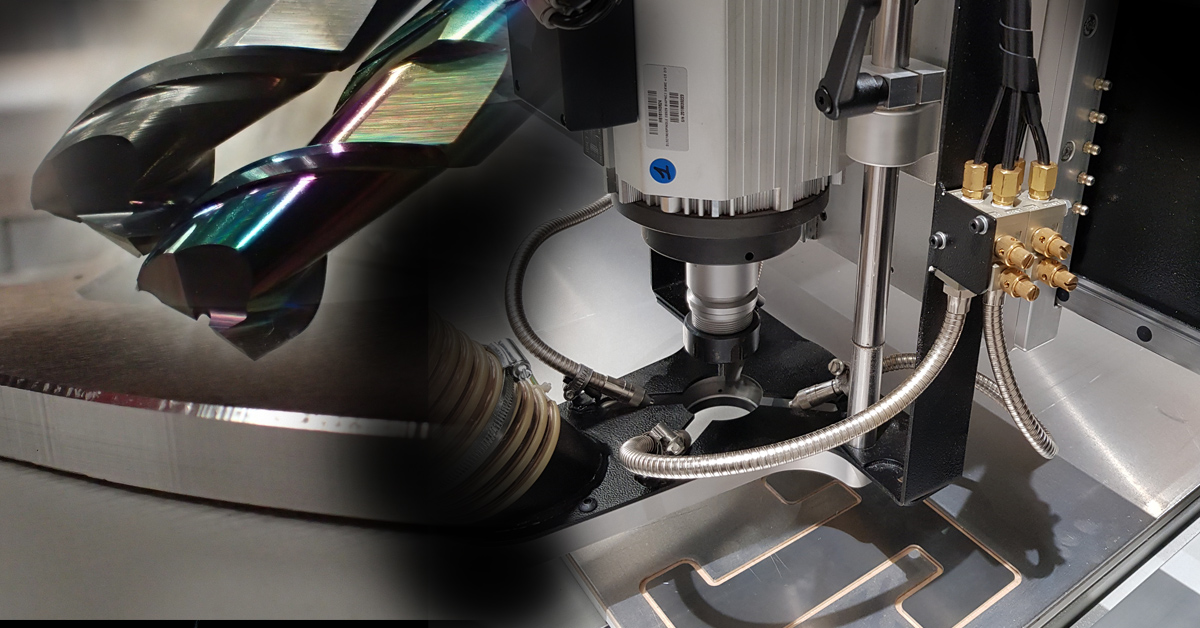
HOW SHOULD I APPROACH CUTTING OF SOLID SURFACE MATERIALS, CORIAN, AVONITE, THAT KIND OF THING?
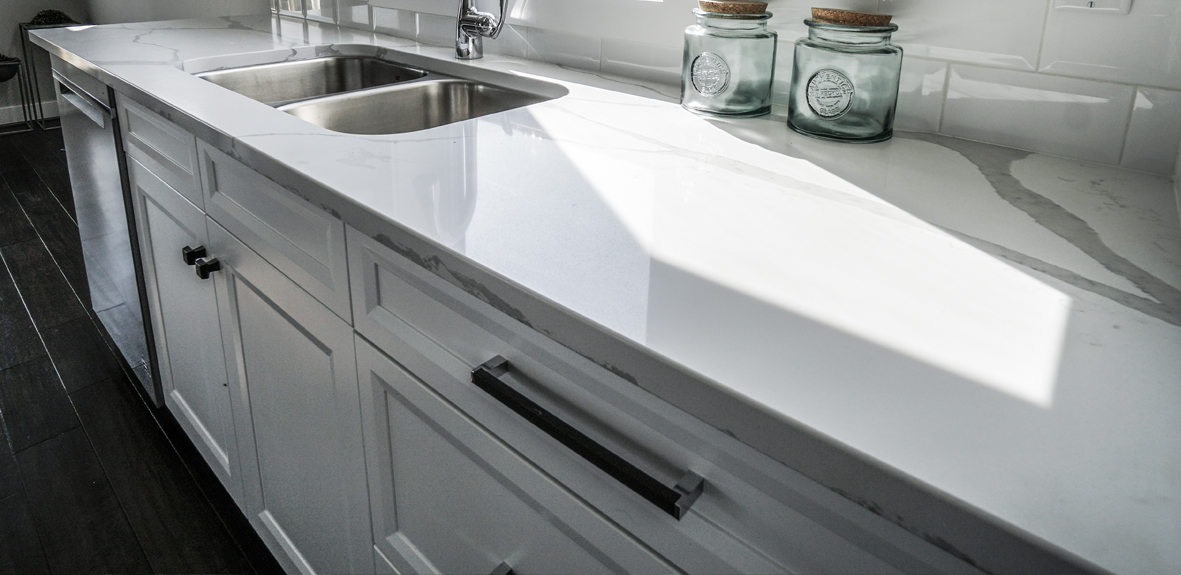
Achieving good results when you’re routing Woods, MDF, Laminates or Ply

HOW DO I GET THE BEST RESULTS POSSIBLE WHEN I’M CUTTING ACM ON MY CNC ROUTER?
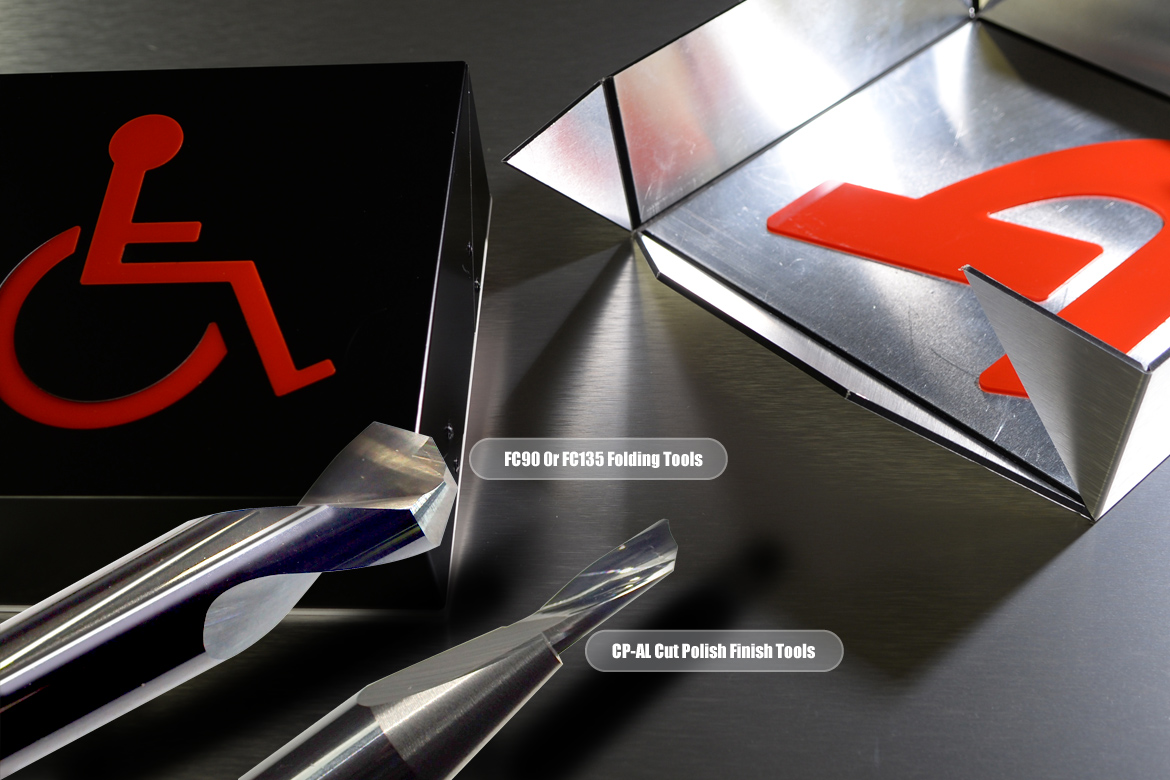
HOW CAN I GROW MY SIGNAGE AND GRAPHICS BUSINESS?
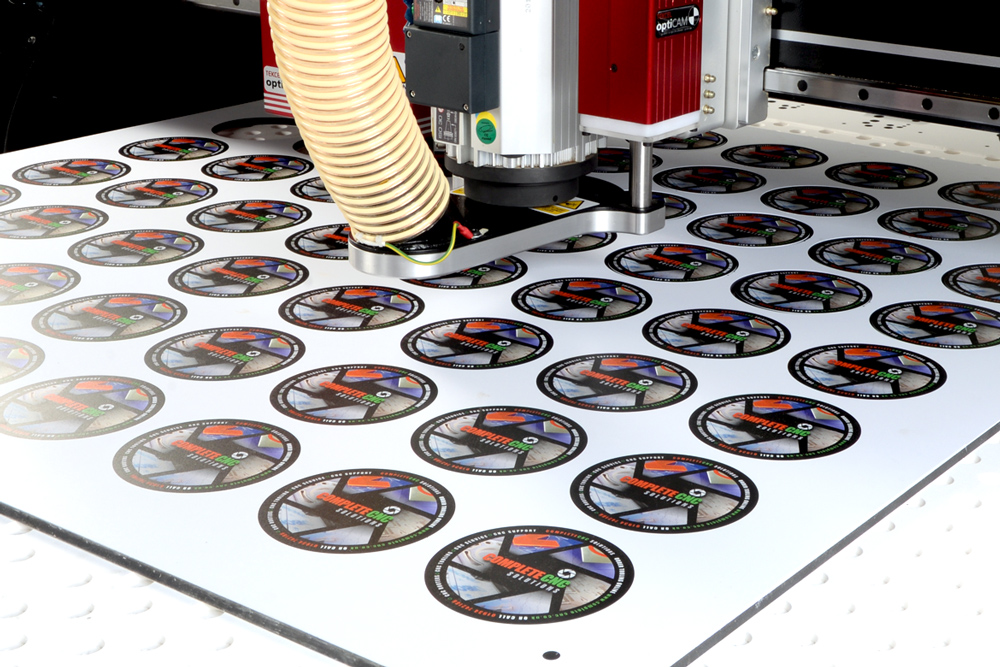
HOW CAN I REDUCE THE TIME I SPEND POLISHING THE EDGE ON THE OUTPUT FROM MY CNC ROUTER?
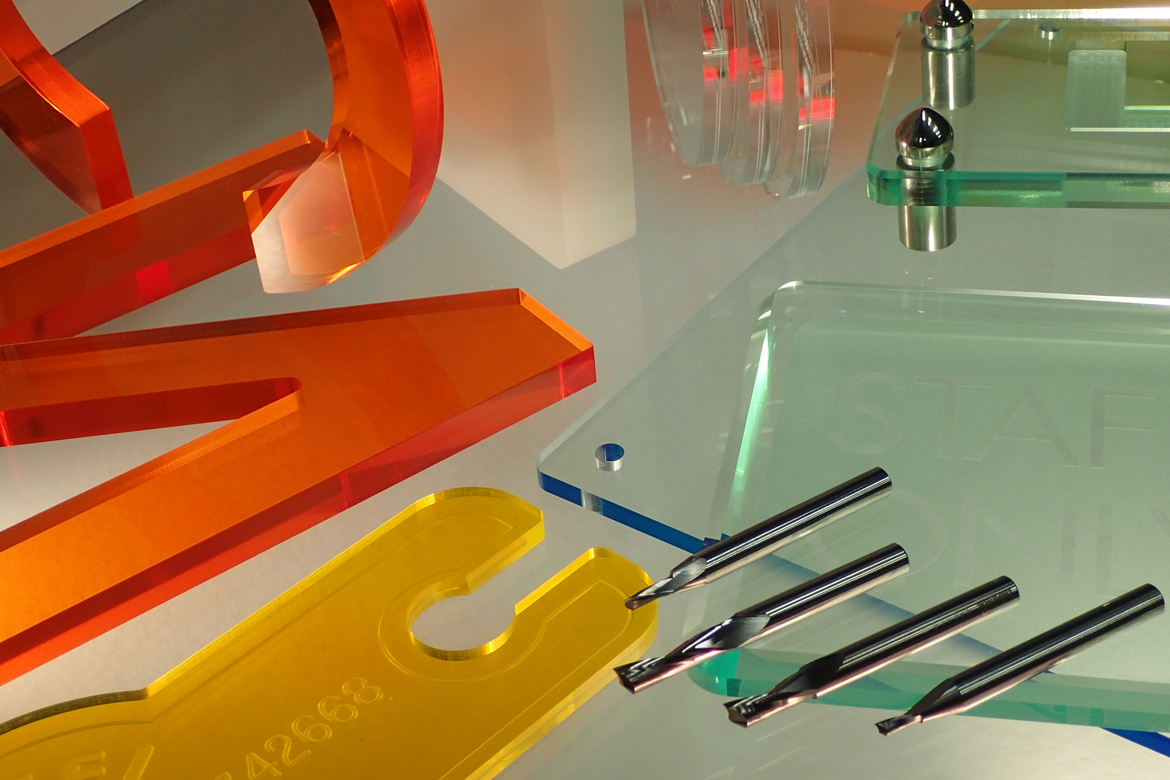
THE FLATTER THE BETTER
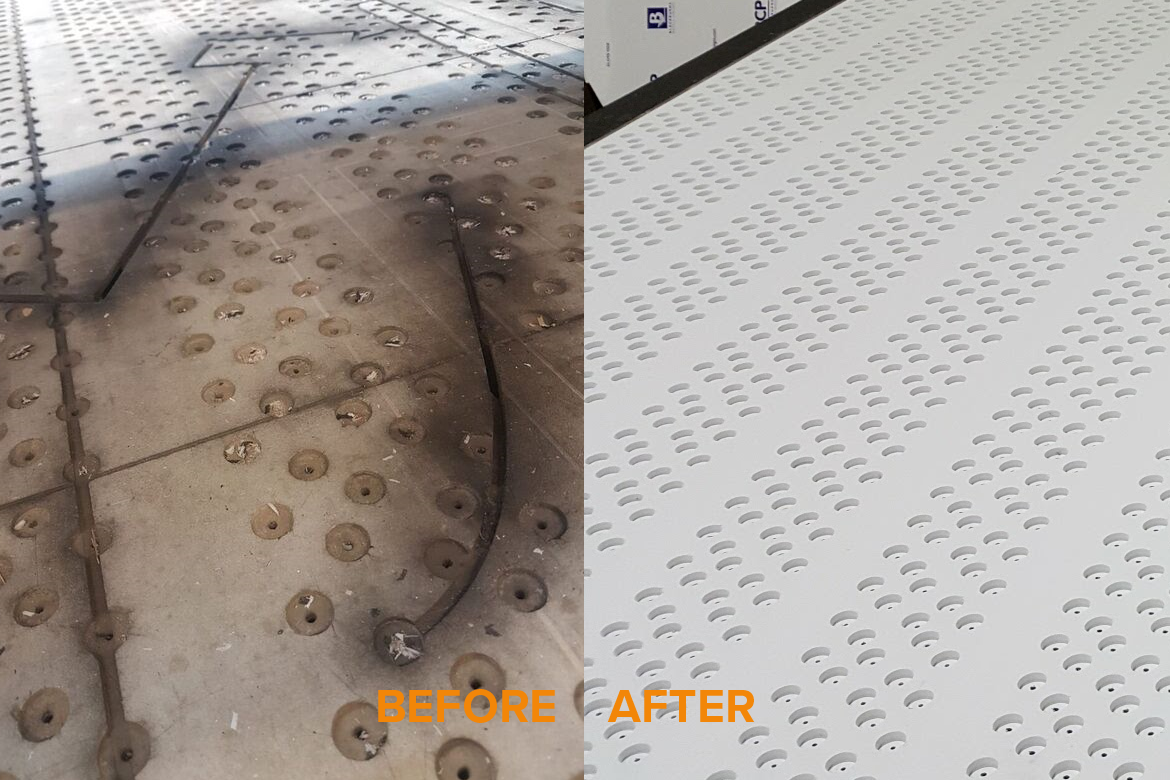
IS MY BUSINESS READY TO BUY A CNC ROUTER?
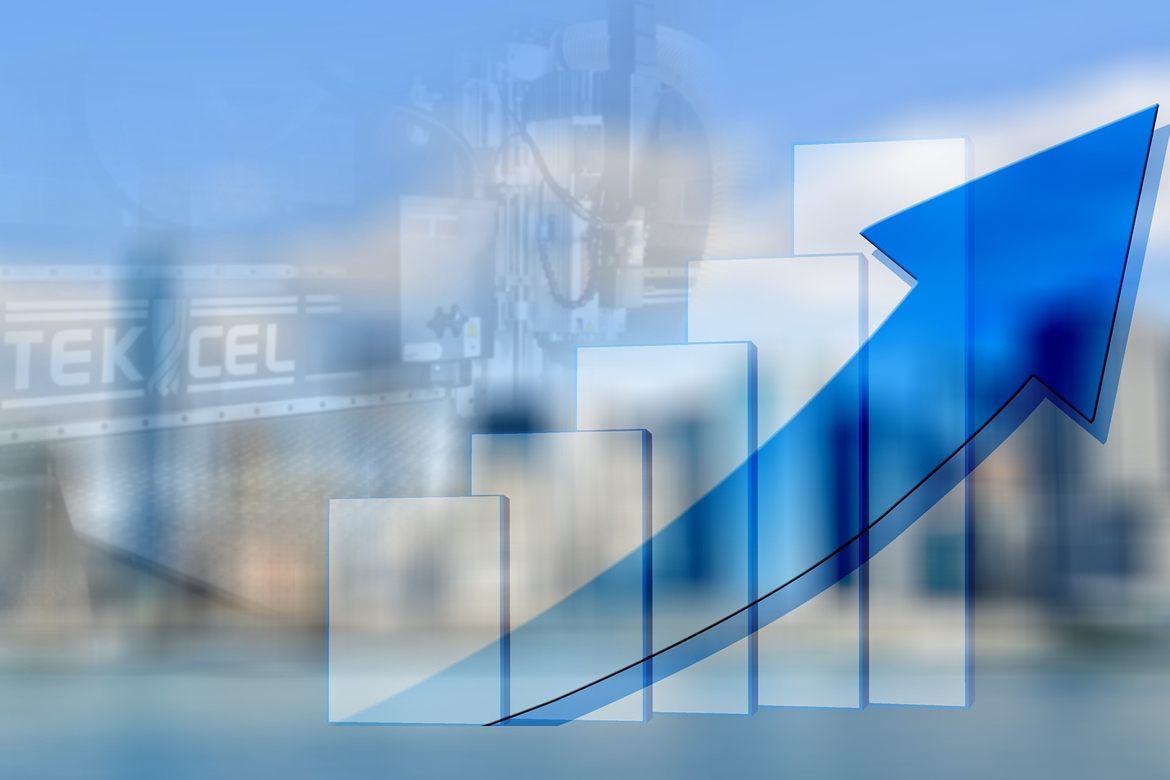
HEARD AT A TRADE SHOW
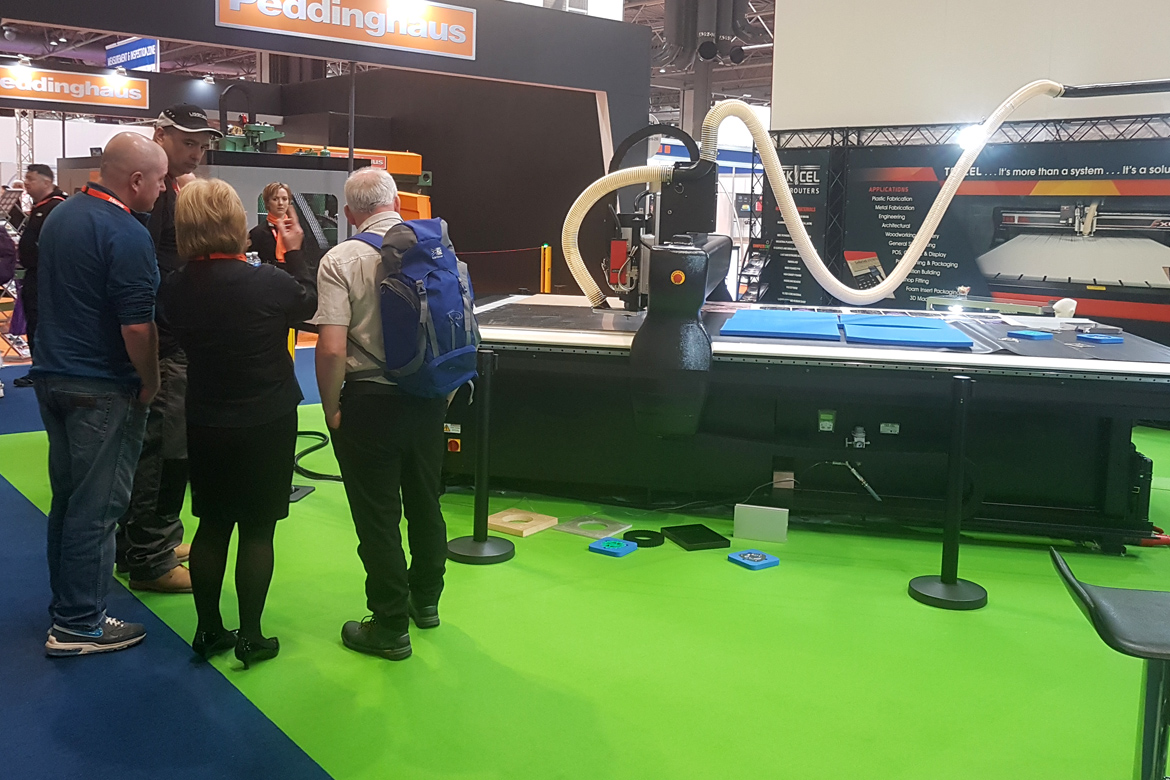
THE IMPORTANCE OF CHANGING CNC ROUTER COLLETS REGULARLY
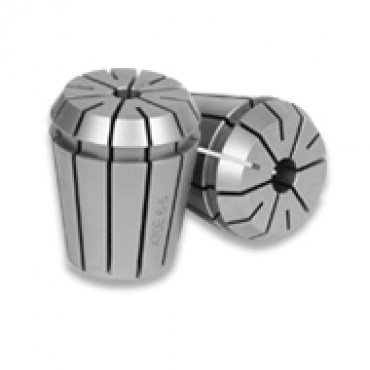
WITH YOU ALL THE WAY
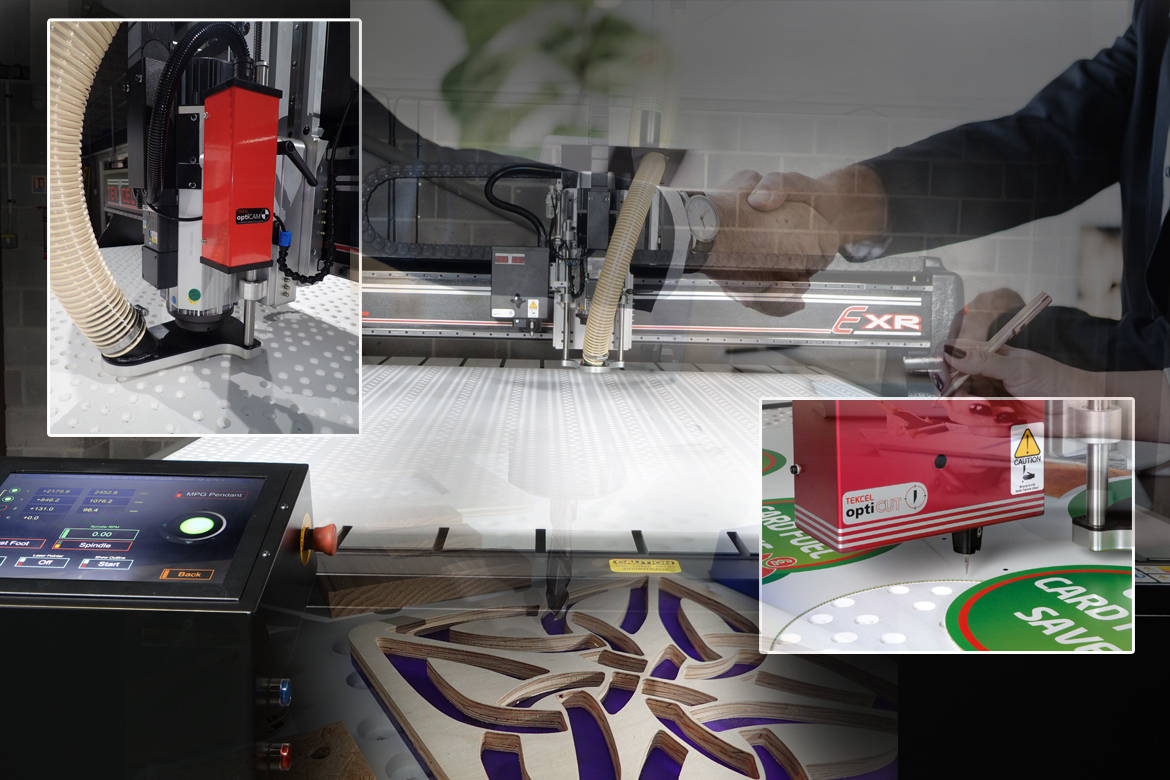