CUSTOMER LOGIN
CNC Woodworking Without The Headaches
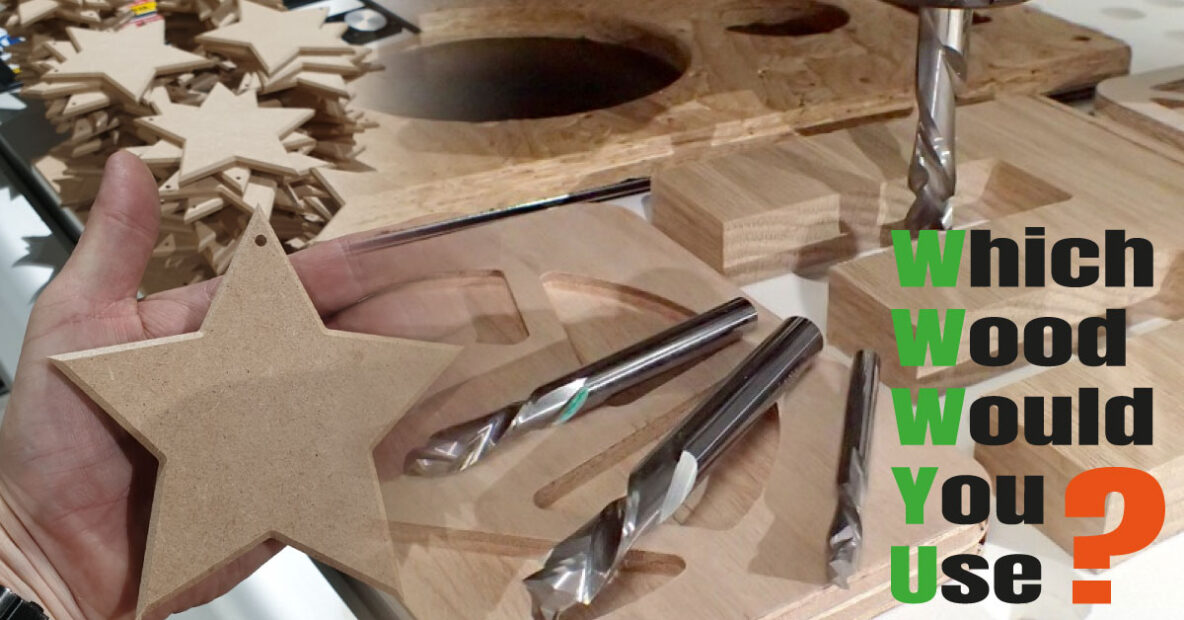
CNC Woodworking Without The Headaches
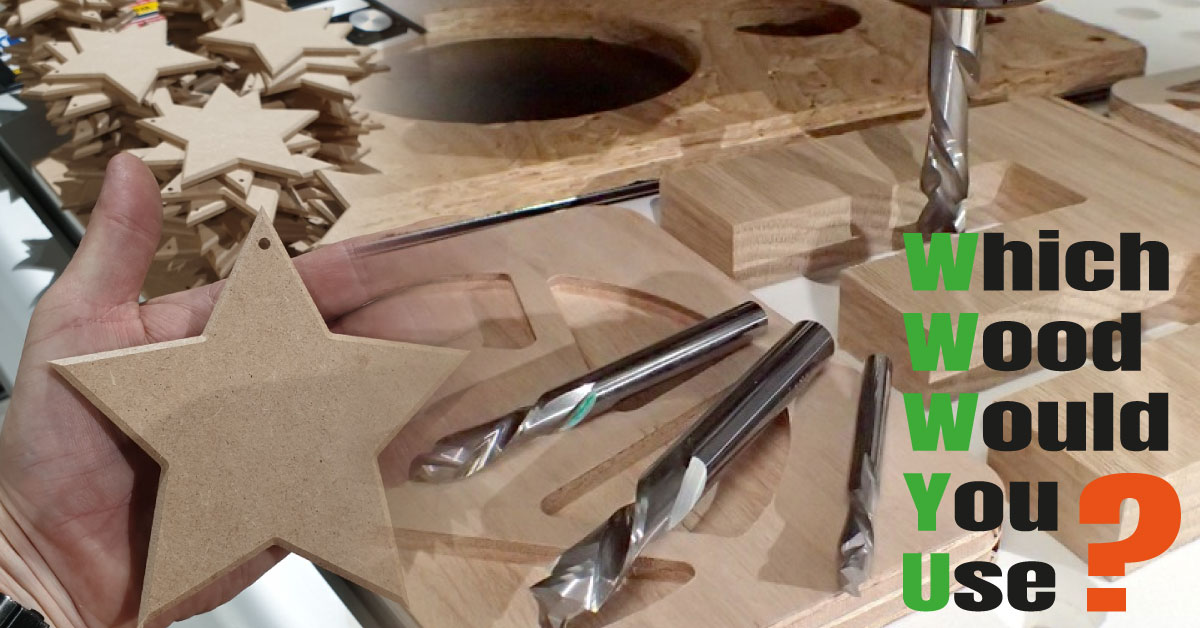
Wood is often seen as an easy-to-machine material, especially compared to metals. However, CNC woodworking presents unique challenges due to the natural variations in wood grain, density, and moisture content. Understanding these properties is crucial for optimising tool performance, minimising waste, and achieving clean, precise cuts.
Here’s a closer look at the key factors that affect CNC machining of wood and how to account for them.
Types Of Wood For CNC Machining
Wood is generally classified into three main categories: hardwood, softwood, and engineered wood. Each type behaves differently during machining, requiring adjustments in tool selection, cutting speeds, and feed rates.
1. Hardwood – Strong, Durable, and Versatile
Hardwoods come from deciduous trees (angiosperms) such as oak, ash, and birch. They are generally denser and more durable than softwoods, making them ideal for furniture, flooring, and construction components.
However, their density can make machining more challenging. Sharp tools, optimised feed rates, and correct cutter selection are essential to prevent burn marks or tear-out when machining hardwoods.
2. Softwood – Easier to Cut, but Not Always "Soft"
Softwoods come from coniferous trees like pine, spruce, and cedar and are widely used in joinery, furniture making, and construction. They are typically less dense than hardwoods, making them easier to machine, but the term "softwood" can be misleading.
Species like Douglas fir and European larch are denser and tougher than some hardwoods, requiring the right tooling and cutting parameters. Checking the Janka hardness scale ensures the best CNC setup for clean, efficient machining.
3. Engineered Wood – Consistent but Abrasive
Engineered wood, such as MDF (Medium-Density Fibreboard), plywood, and particleboard is made from wood fibres or particles bonded with adhesives. While these materials offer consistent machining properties, the resins and adhesives make them highly abrasive, leading to faster tool wear.
Using solid carbide & coated tools helps maintain sharp edges and prolong tool life when machining engineered woods.
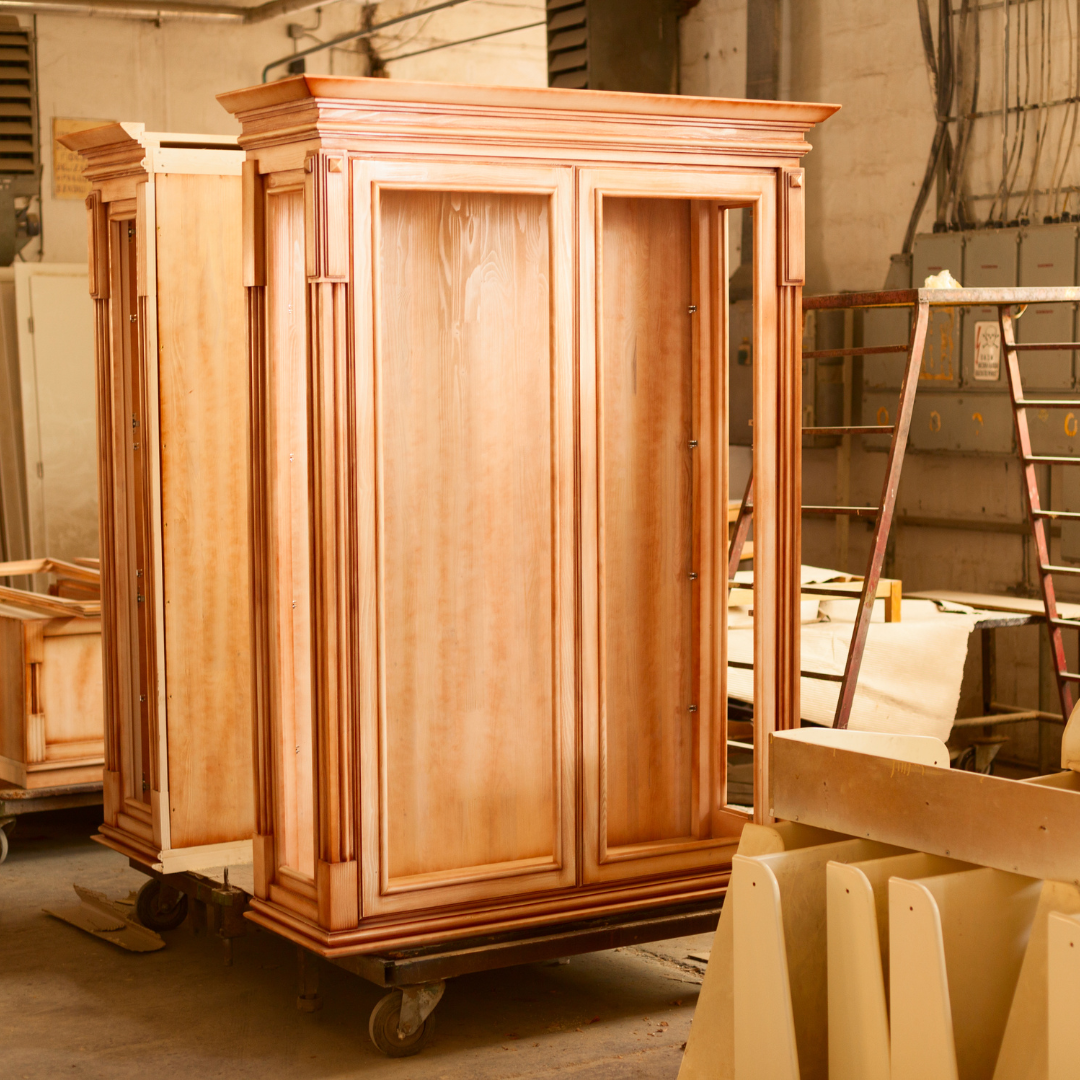
Key Wood Properties That Affect CNC Machining
1. Grain Structure – Coarse vs. Fine-Grained Woods
Wood is a natural composite material, with strong cellulose fibres held together by lignin. The grain structure significantly impacts machinability:
- Coarse-grained woods (e.g., oak, ash) have an open grain structure, which increases the risk of tear-out during machining.
- Fine-grained woods (e.g., beech, birch) have smaller, more uniform fibres, allowing for smoother cuts and easier machining.
2. Moisture Content – The Biggest Factor in Wood Stability
Wood naturally absorbs and releases moisture from the air, which can cause warping or dimensional changes. Managing moisture content (MC) is essential for CNC precision and stability.
- Ideal MC for machining: 8-12%, depending on the environment and application.
- Too high MC (>12%) – Wood is softer and harder to cut cleanly, requiring lower spindle speeds and reduced feed rates. It can also increase tool wear due to interactions with resins, sugars, and tannins.
- Too low MC (<8%) – Wood becomes brittle, increasing the risk of chipping and splintering.
3. Knots and Irregularities – A Machining Challenge
Knots are dense, irregular grain structures where a branch was once embedded in the tree trunk. These can disrupt machining by:
✔ Increasing tool wear
✔ Changing grain direction suddenly, causing tear-out
✔ Raising the risk of tool breakage due to their harder density
To prevent issues, reduce feed rates when machining near knots to avoid sudden stress on the tool.
Optimising CNC Cutting For Wood
To get the best results from CNC woodworking, follow these machining tips:
✔ Use Solid Carbide single flute or twin flute up spirals tools – Ideal for softwoods and MDF, they offer excellent chip evacuation and reduced heat buildup.
✔ Use down-cut or compression bits – Prevents tear-out on veneered plywood and laminated surfaces.
✔ Adjust spindle speed based on woods & engineered woods – Hardwoods, softwoods & Engineered Woods need to be cut at lower RPMs such as 18,000 rpm.
Always try to use a “ramp in” process on the toolpath so as to limit a vertical plunge that can create heat and generate scorching .
✔ Minimise tool dwell time – Reduces heat buildup and prevents burn marks on wood surfaces.
At Complete CNC Solutions, we supply high-performance CNC tooling optimised for cutting all types of wood. From solid carbide compression cutters to single or twin flute up-spiral carbide tools for engineered materials, we ensure you get precision, efficiency, and longevity from your CNC router.
Need the Best CNC Tooling for Woodworking?
Further Blog Posts
Avoid These CNC Pitfalls in Illuminated Signmaking
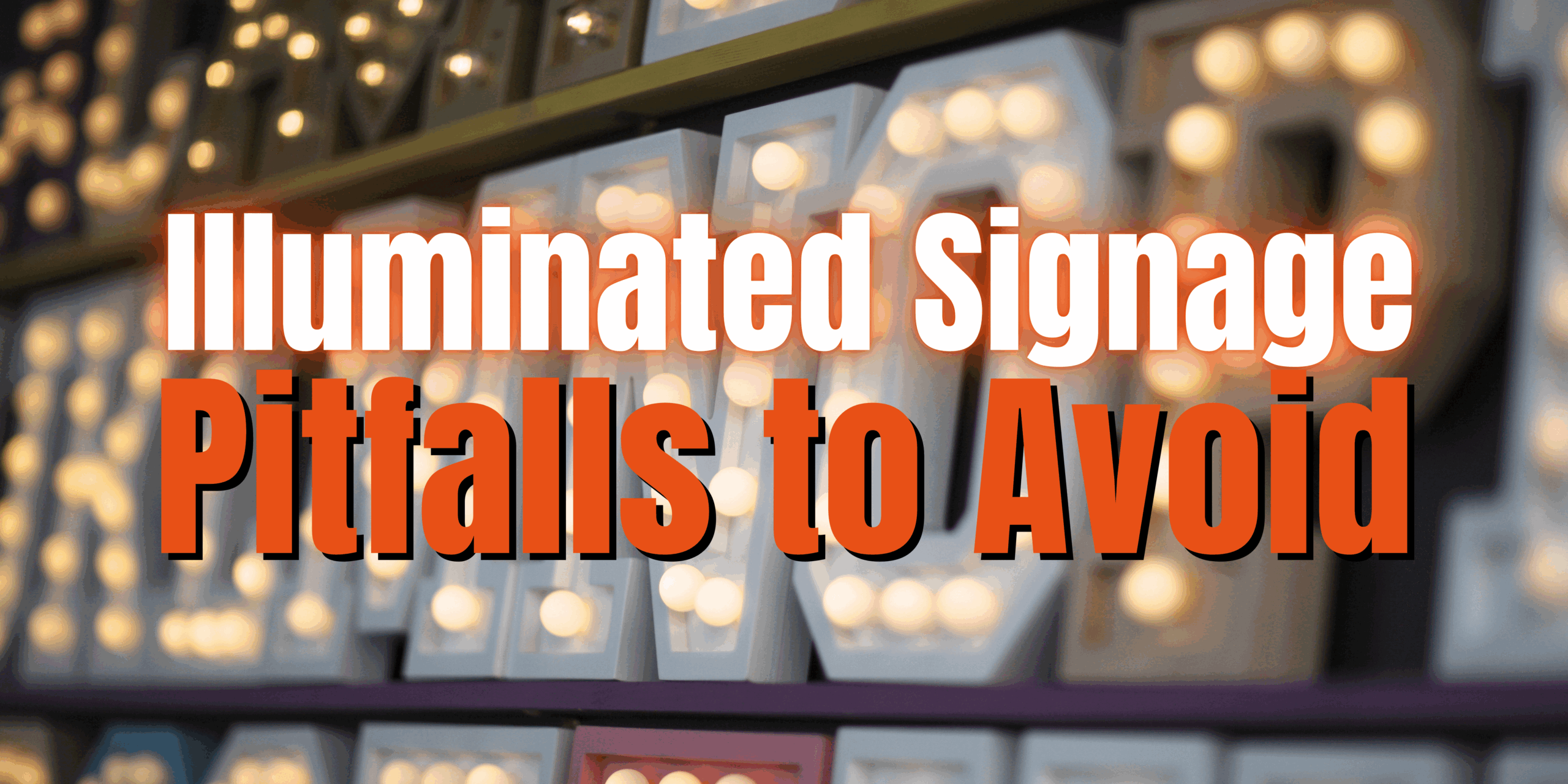
Essential CNC Router Tips for Cutting Acrylic
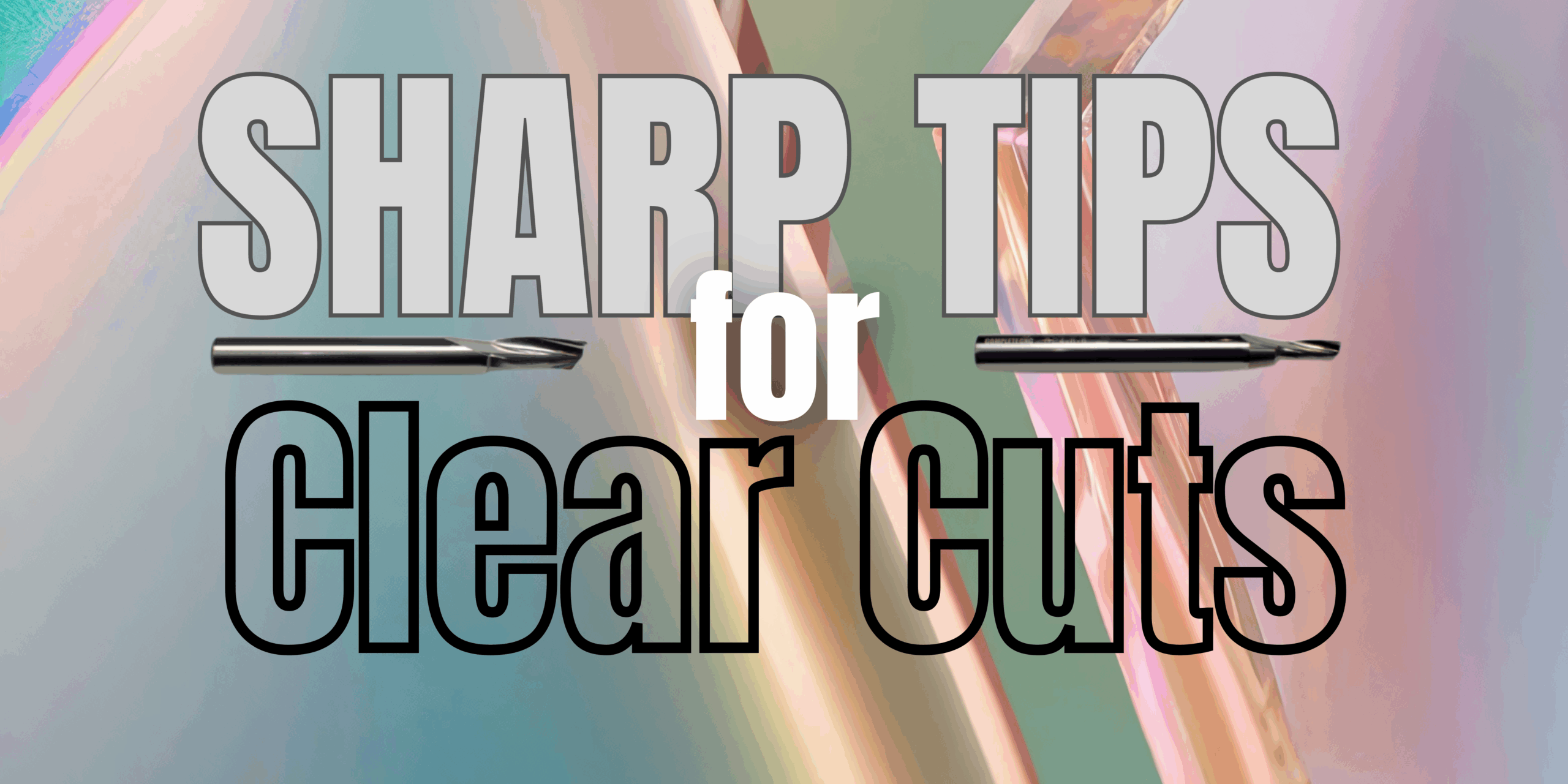
Nesting Your Way to Better Margins in Joinery
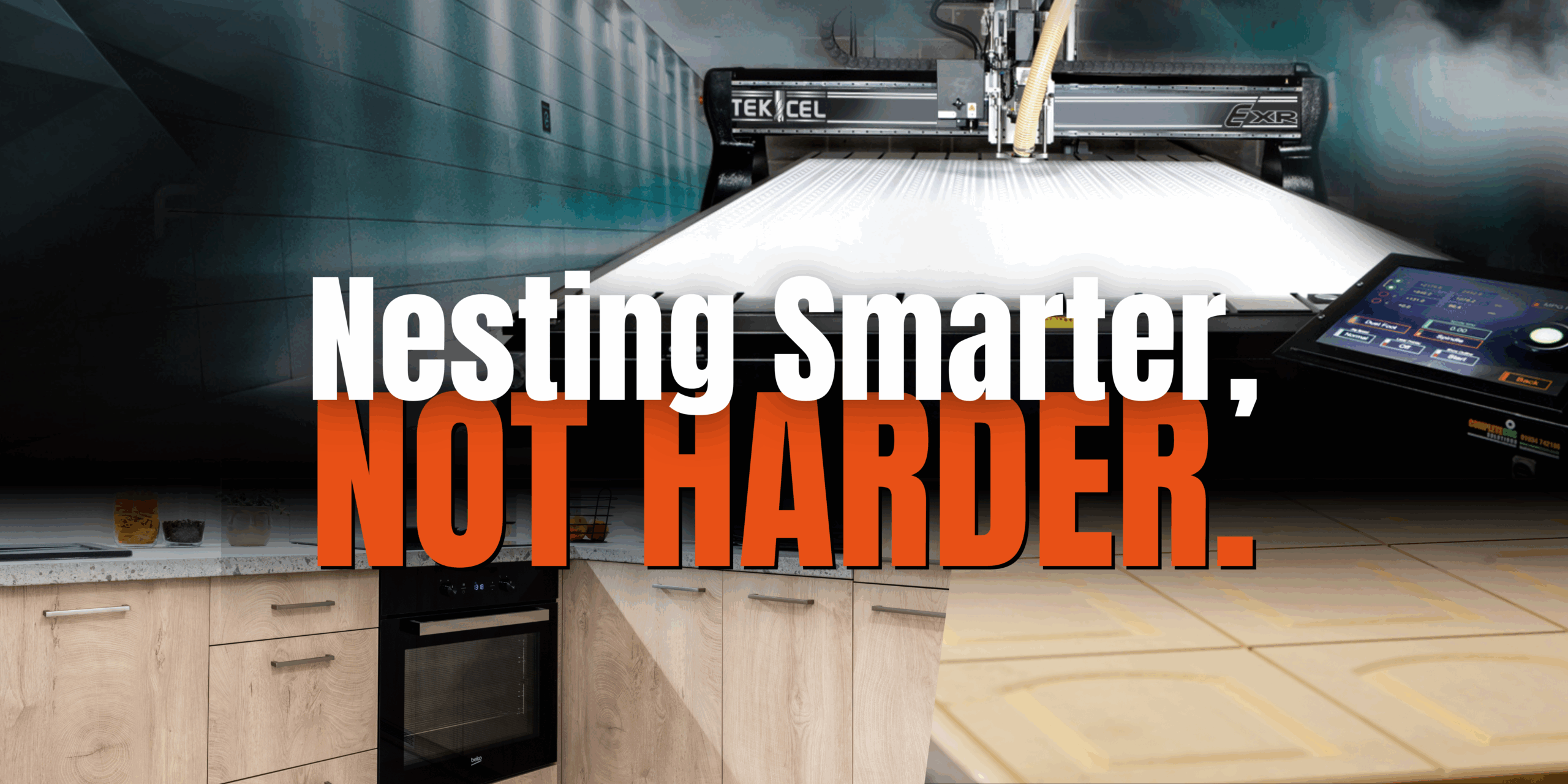
Is Your CNC Router Holding Your Business Back?
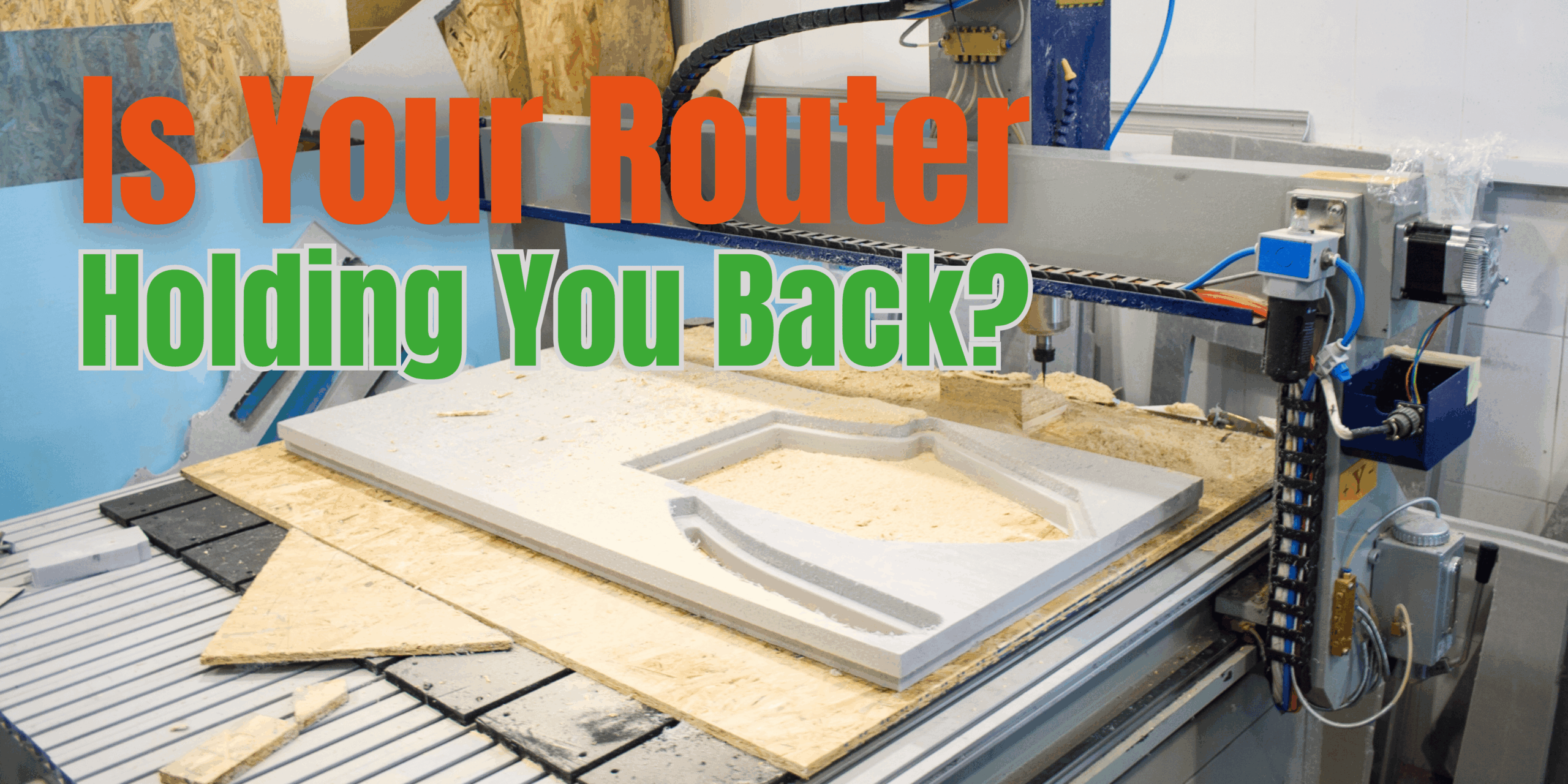
Can a CNC Router Cover Lots of Different Industries?
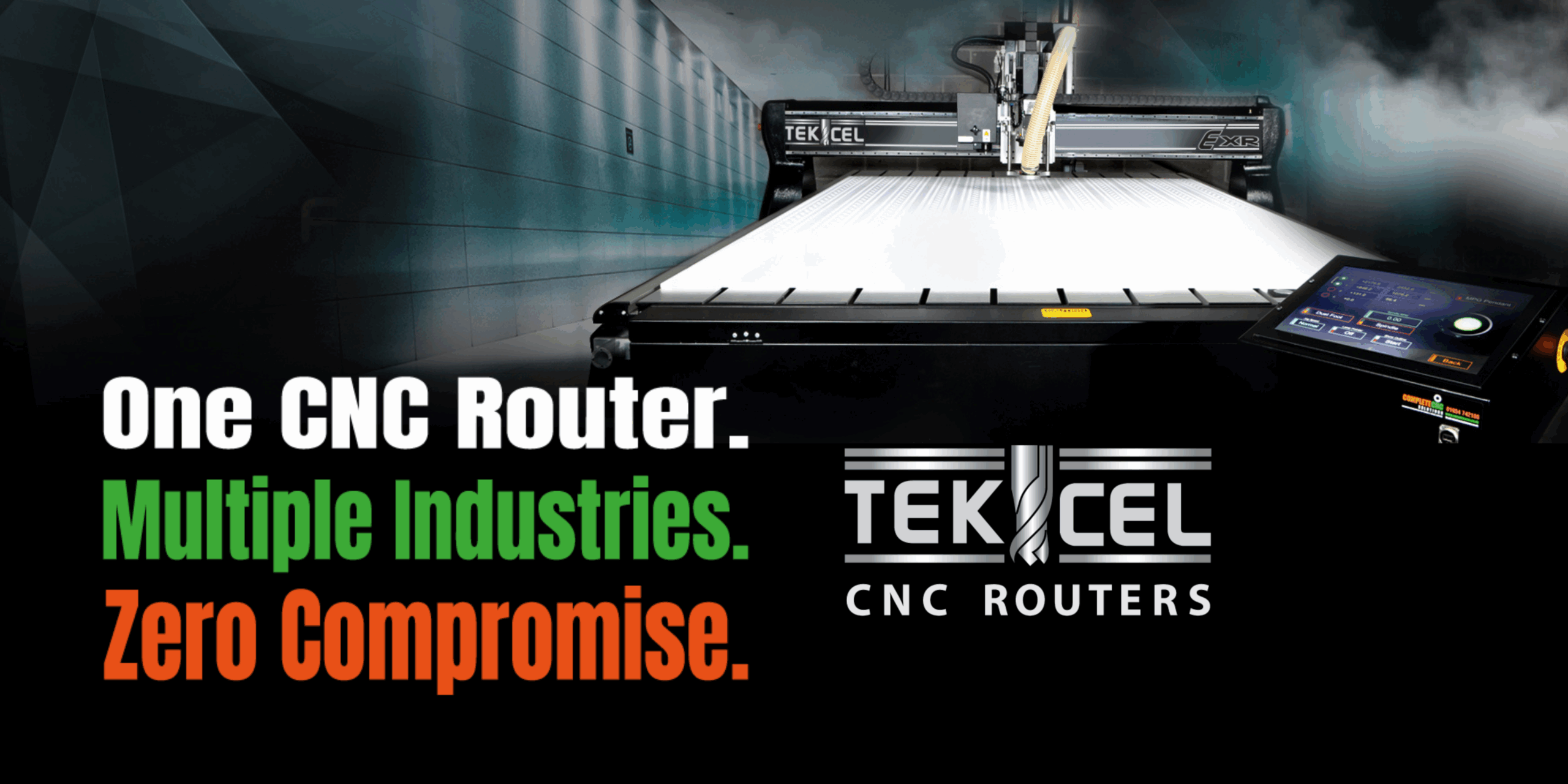
Why Case Makers Should Be Cutting Foam In-House With a CNC Router
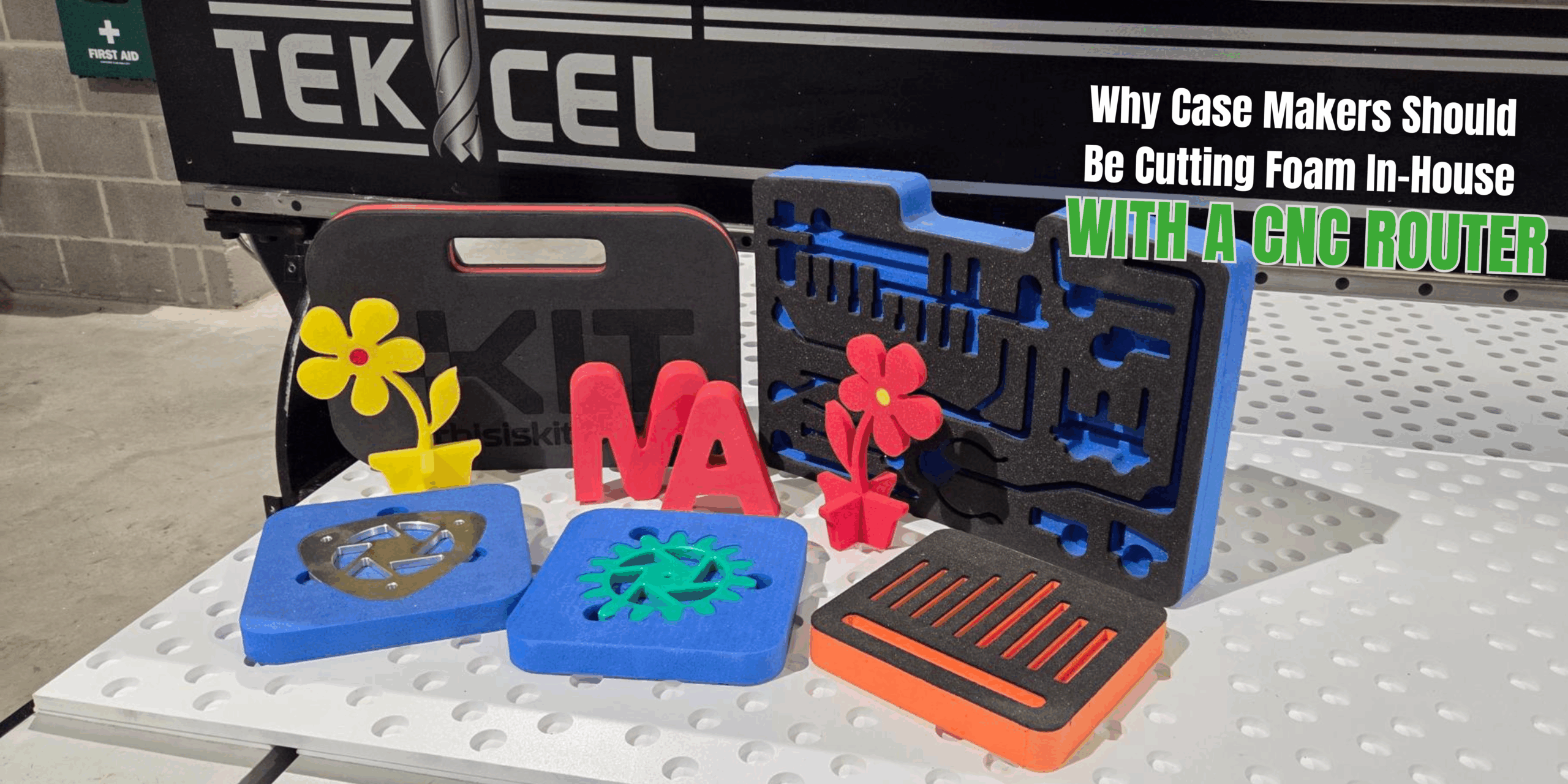
FAQ: What Tips Do You Have For Cutting MDF?
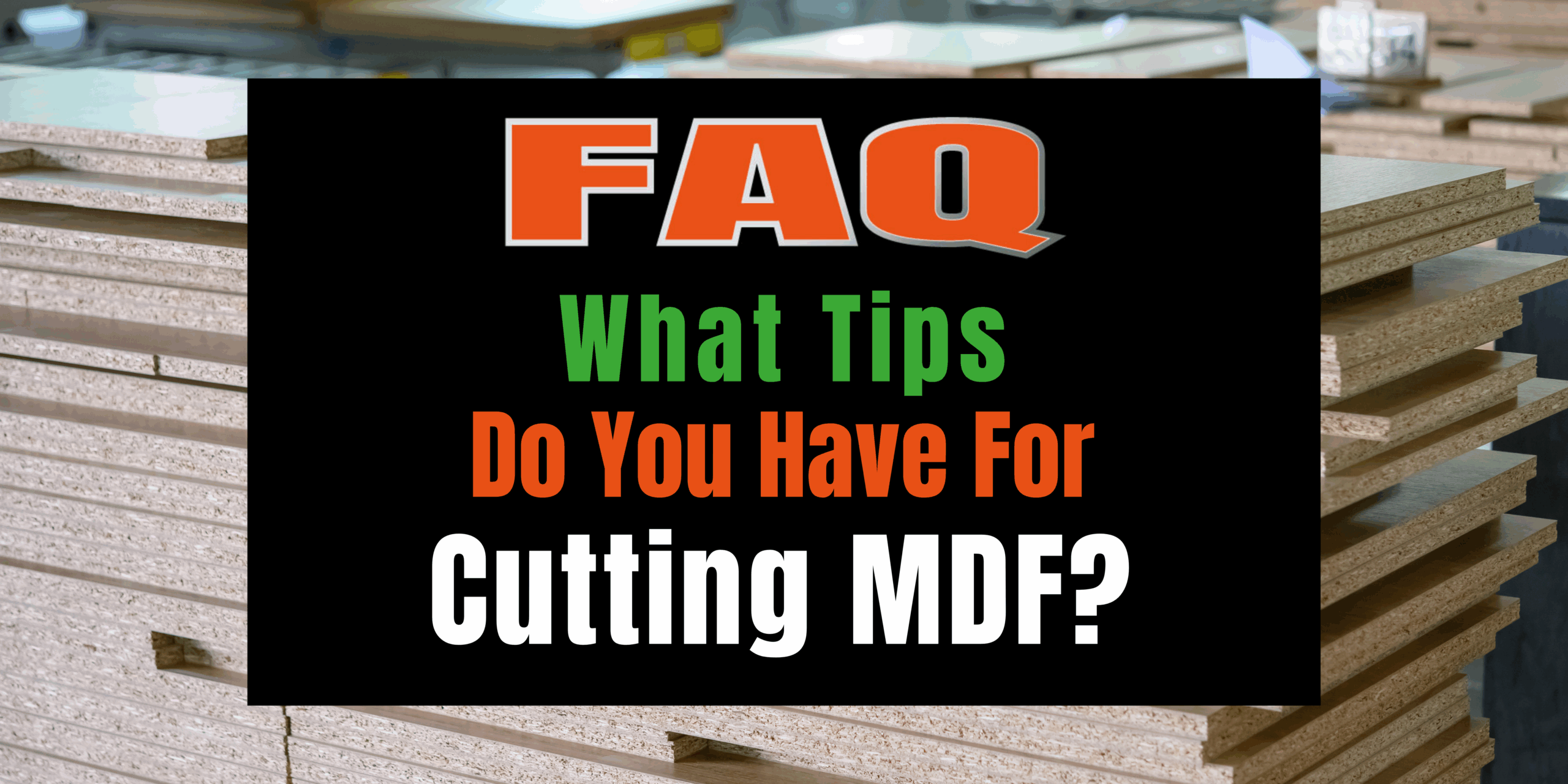
Thinking About Investing in a CNC Router?
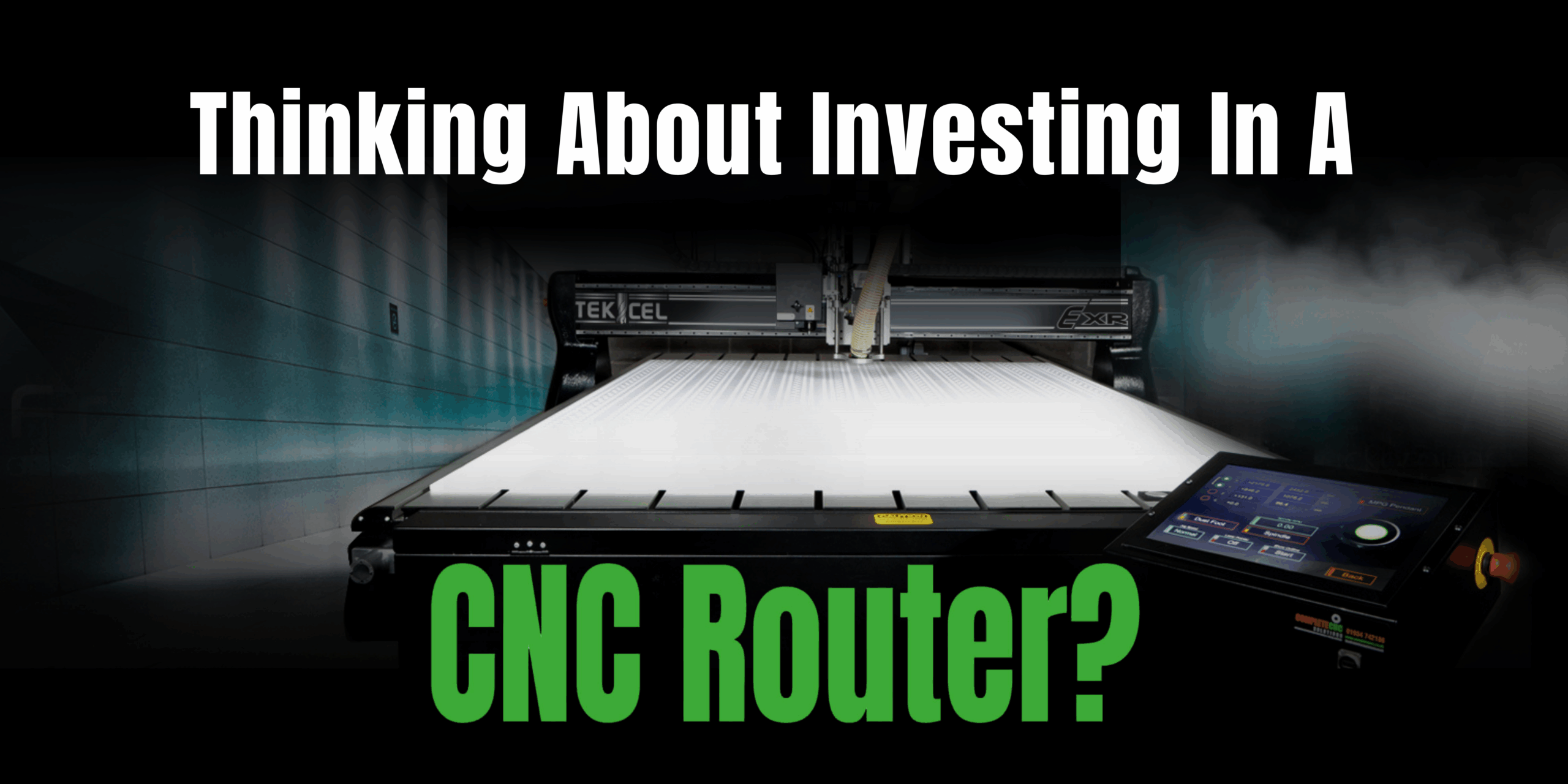
Why Tekcel EXR is the CNC Router You Need
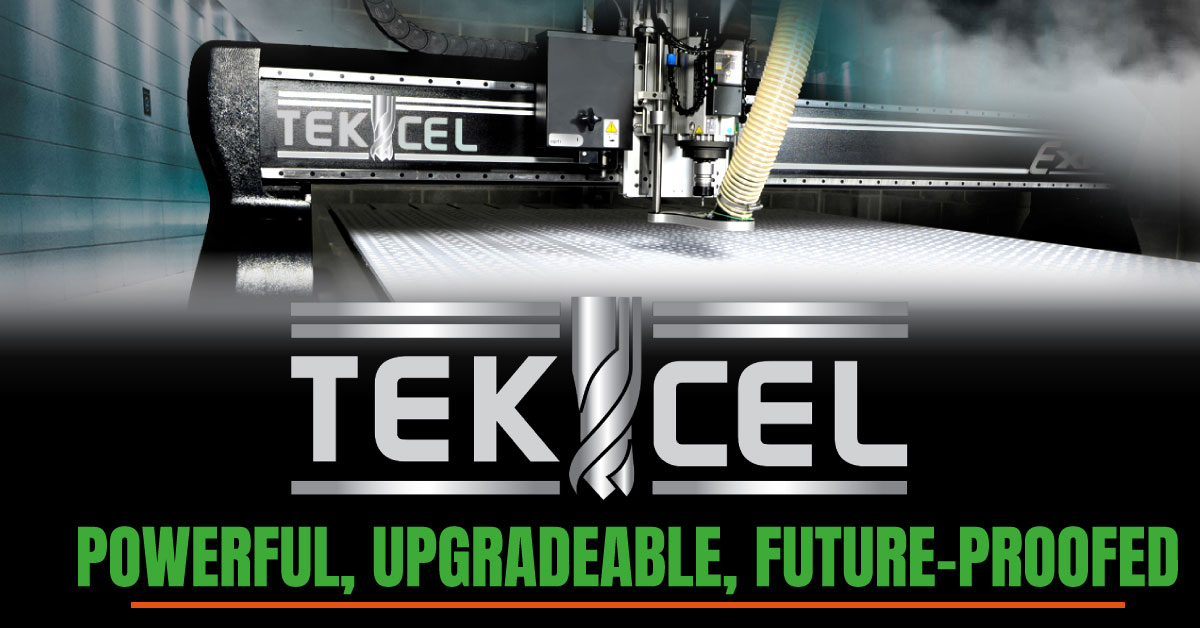
CNC Woodworking Without The Headaches
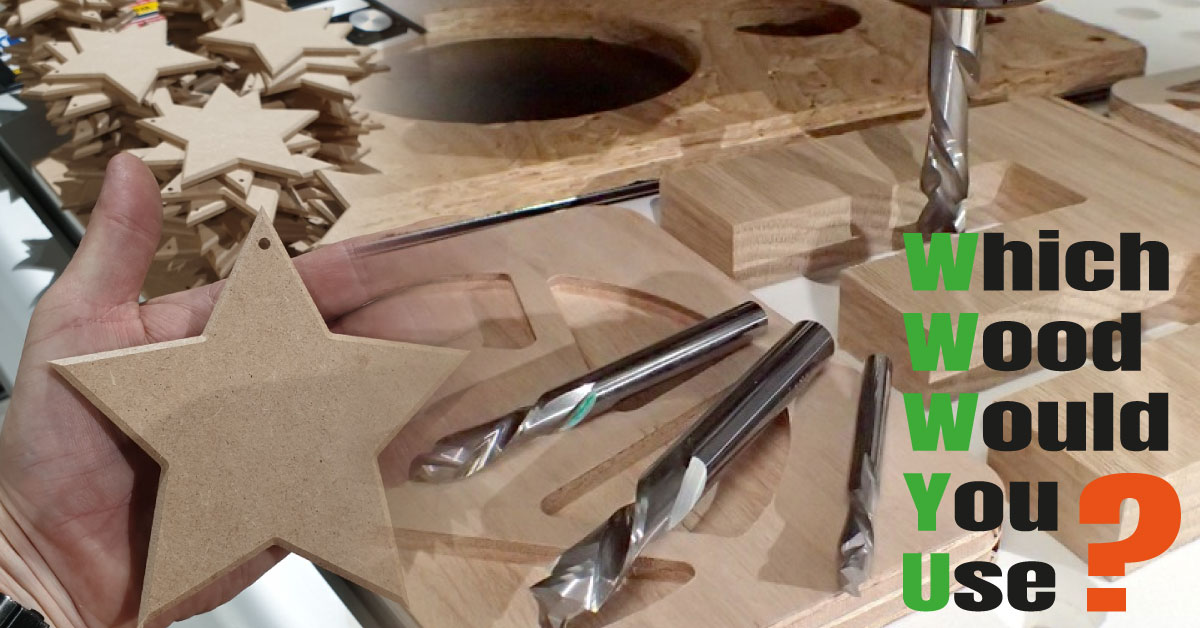
No More Botched Cuts on Plastics & Acrylics!
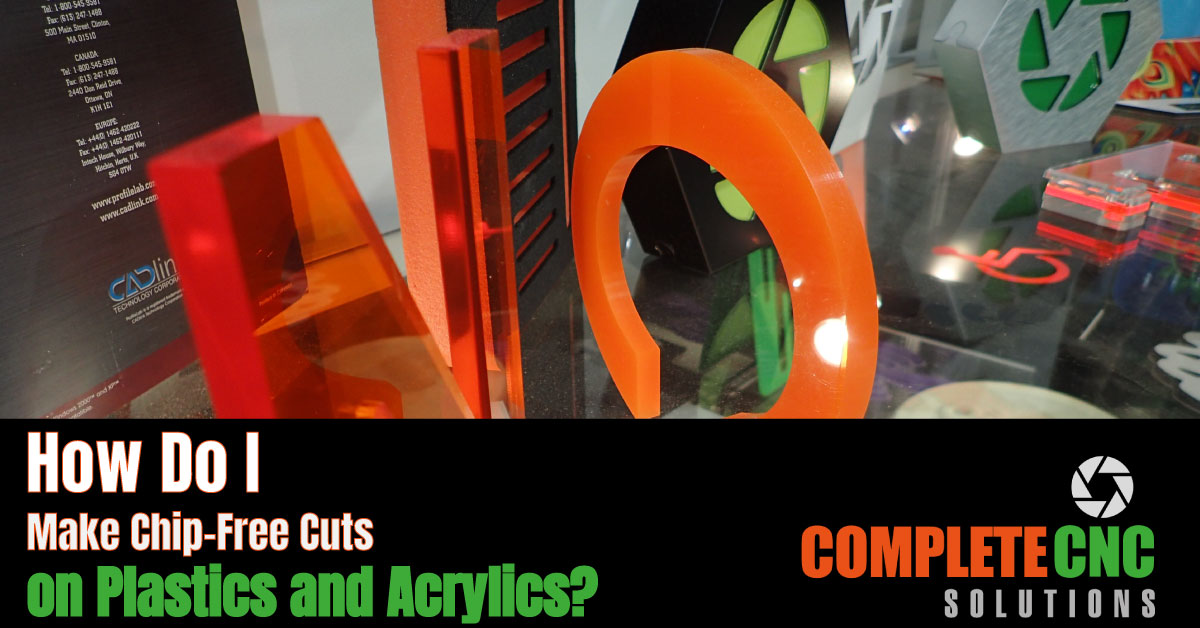
Struggling with Tool Wear?
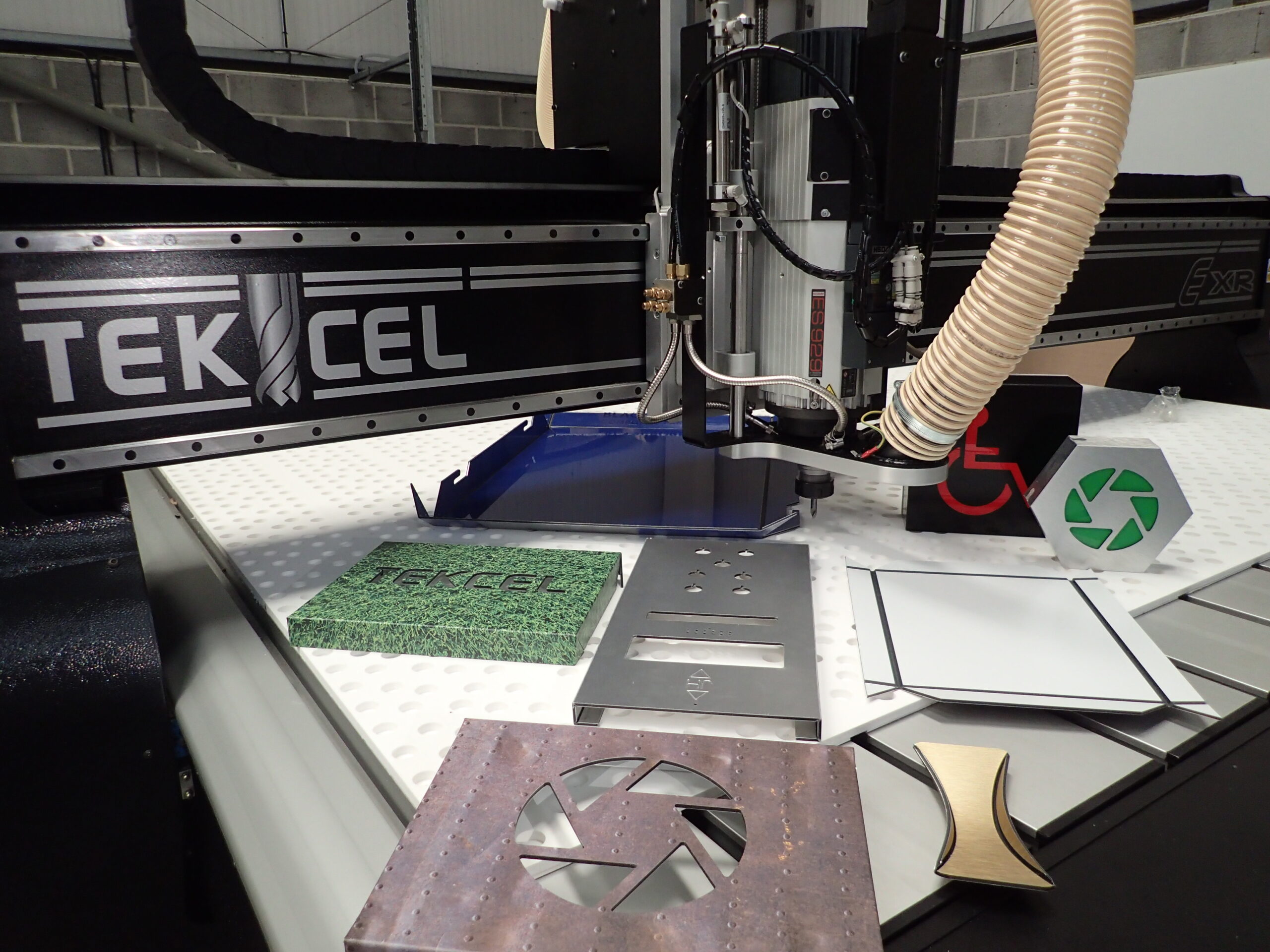
How to Successfully Cut Small Shapes Without Them Moving
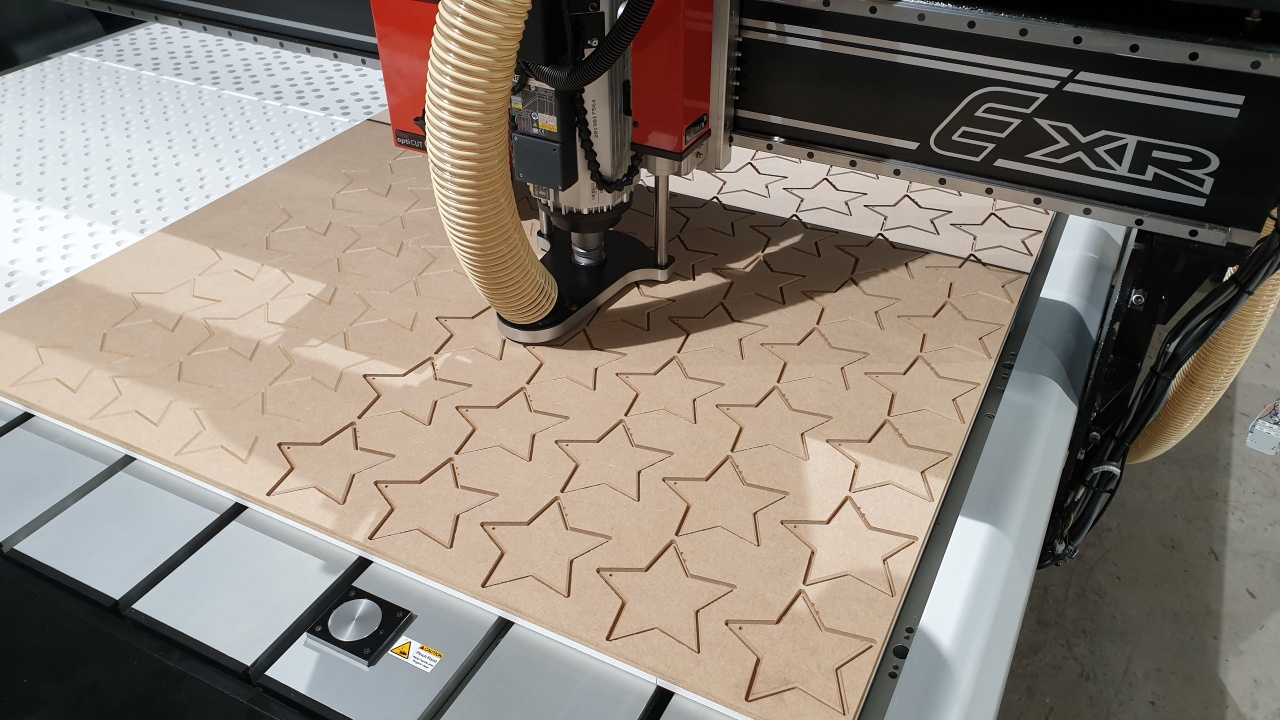
Documenting CNC Router Settings and Processes for Future Success
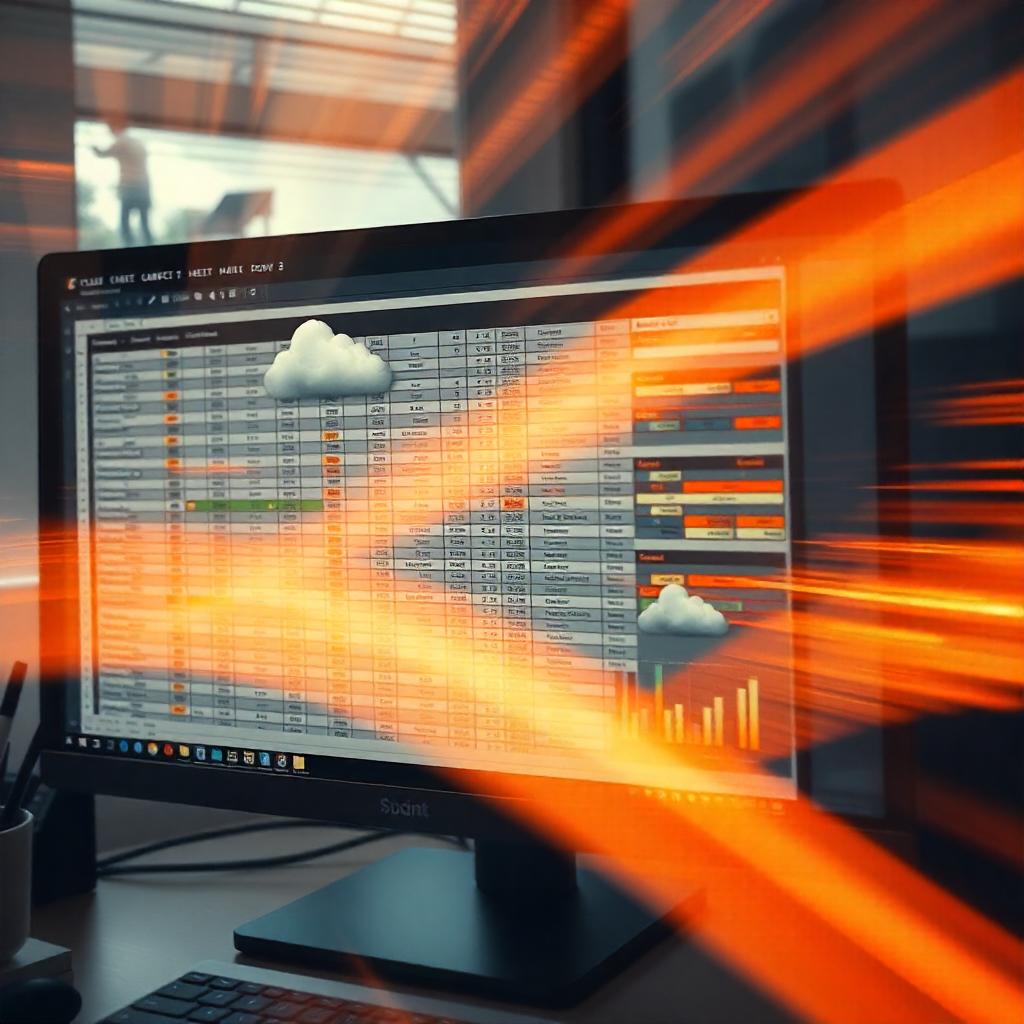
Training Tailored For Success With Your Tekcel CNC Router
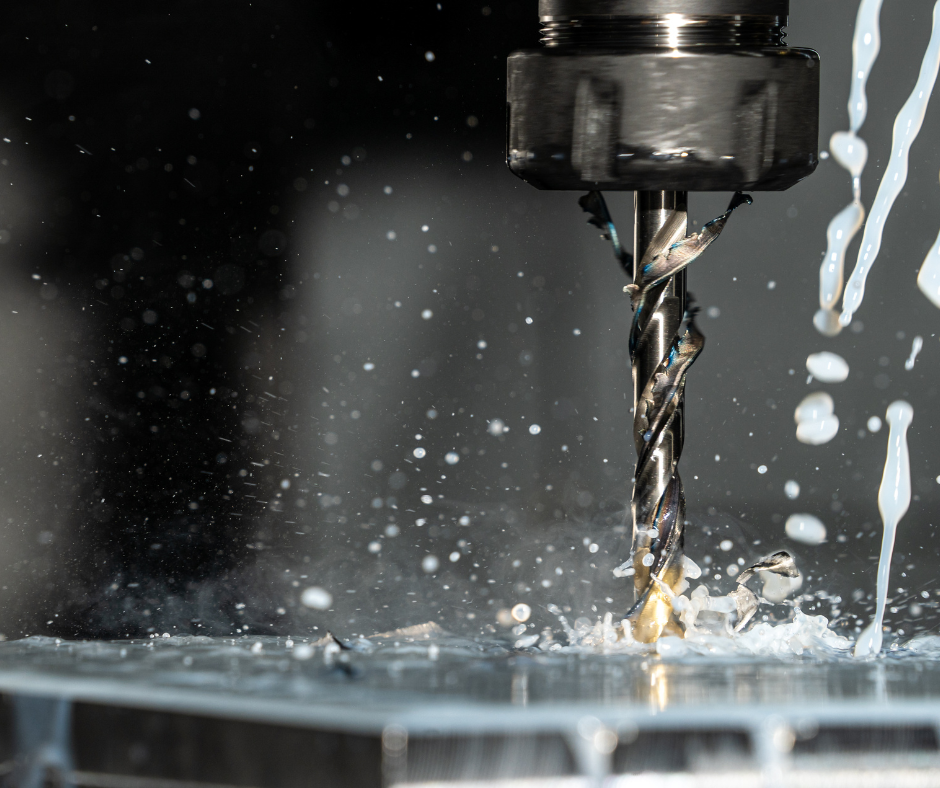
Stay Ahead with Software Updates for Your Tekcel CNC Router
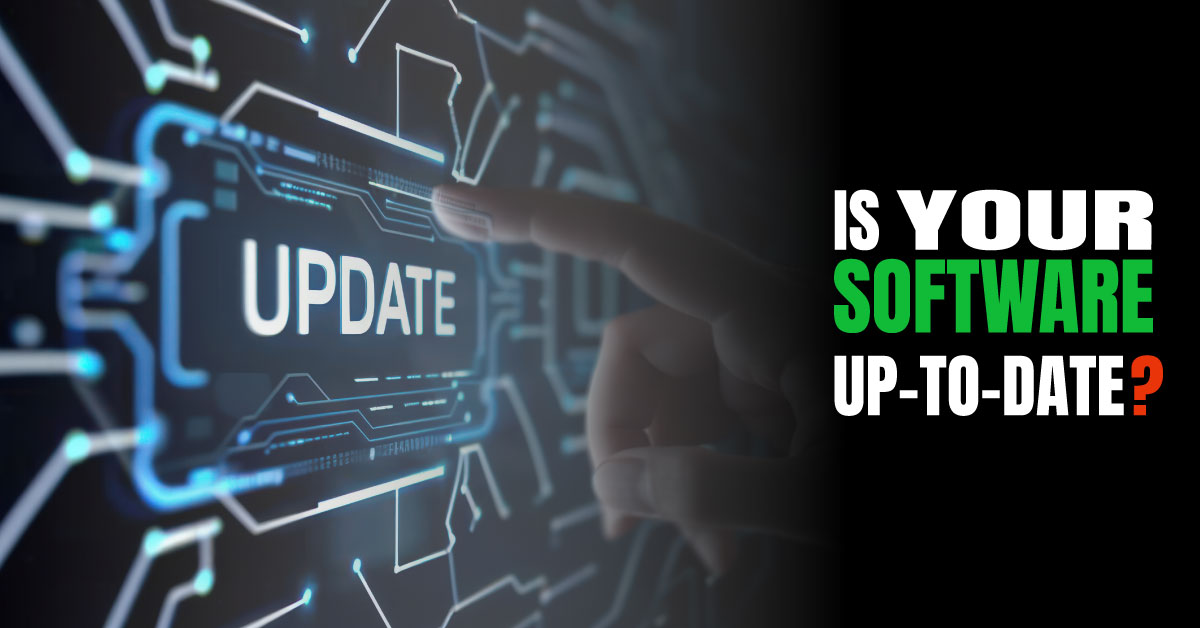
Revolutionise Signage with Tekcel CNC and Precision ACM Tooling
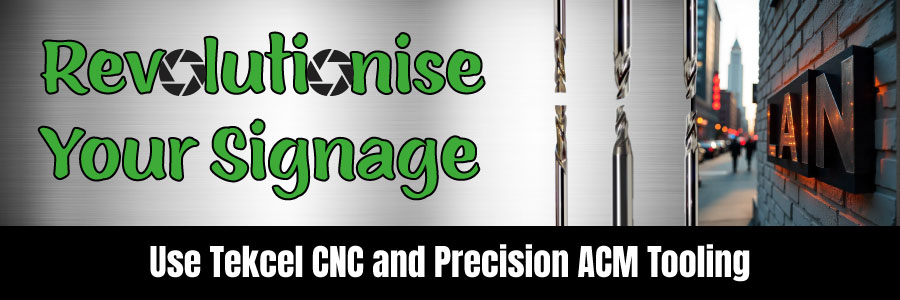
Cutting it Close? Know When to Change Your Collet for Safe, Sharp Results
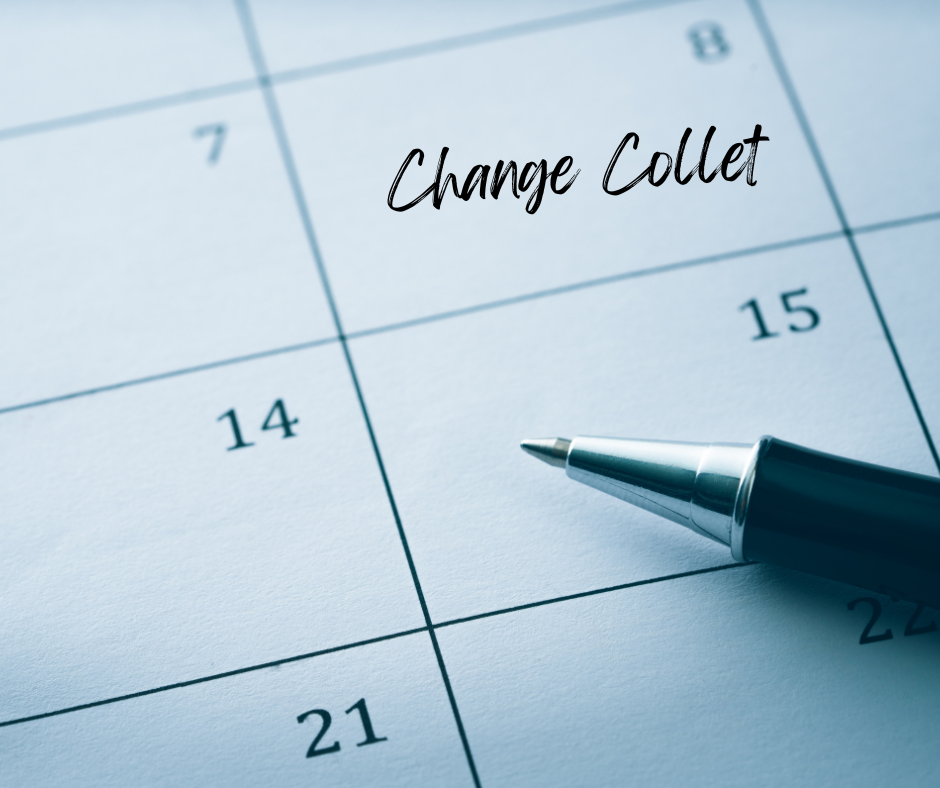
How to Avoid Burning and Furring When Cutting Wood with a CNC Router
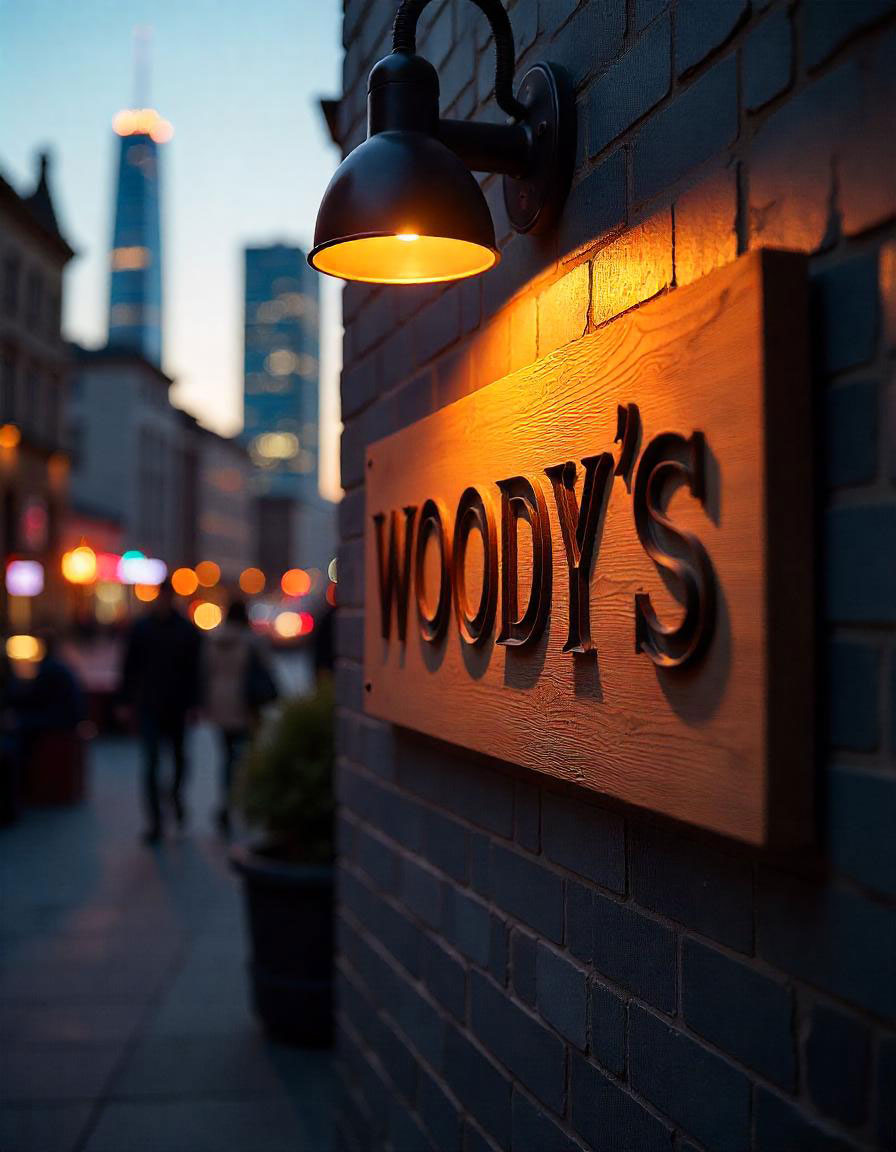
How to choose the right CNC tool for the job/material
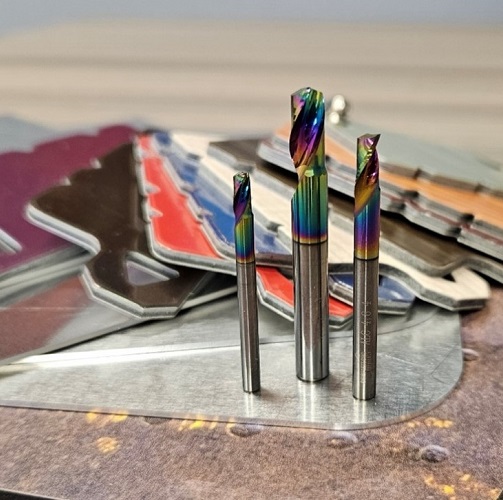
Which CNC Router covers all the bases for a signage manufacturer?
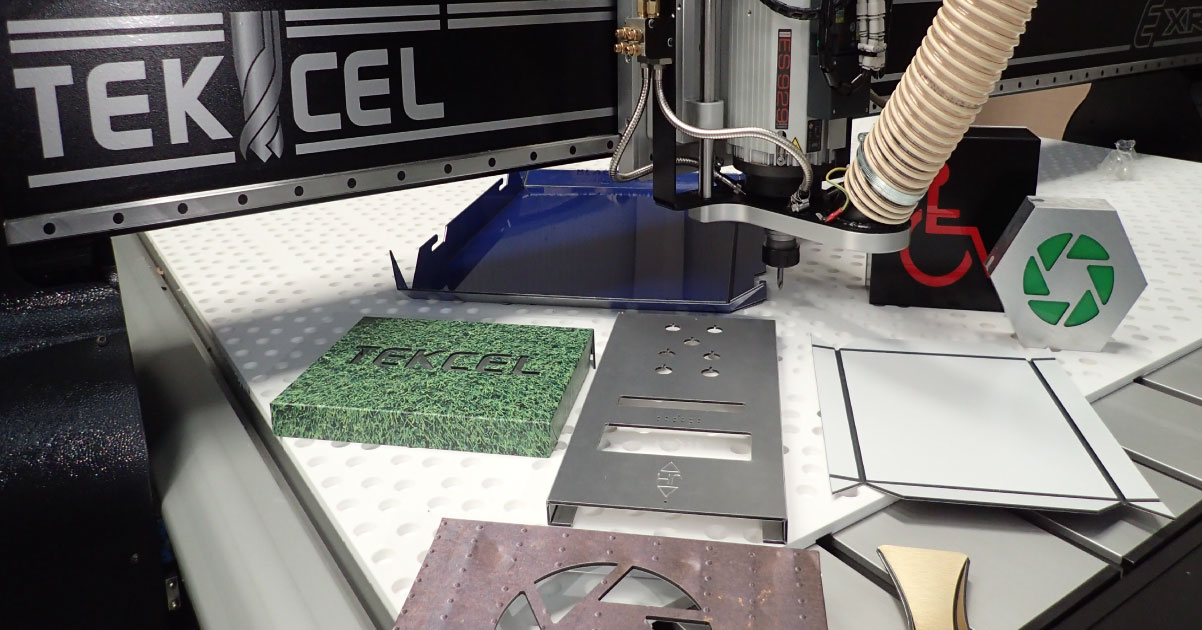
The Tekcel – High Pressure Mist Coolant System for Metal Cutting
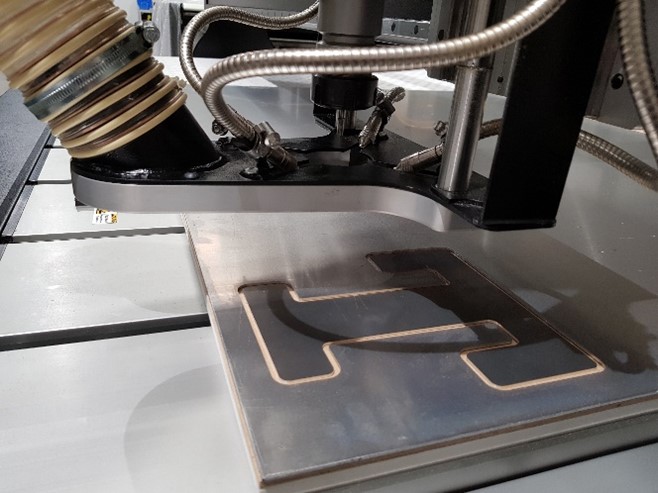
Tekcel CNC Routers – Furniture & Woodworkers dream machine
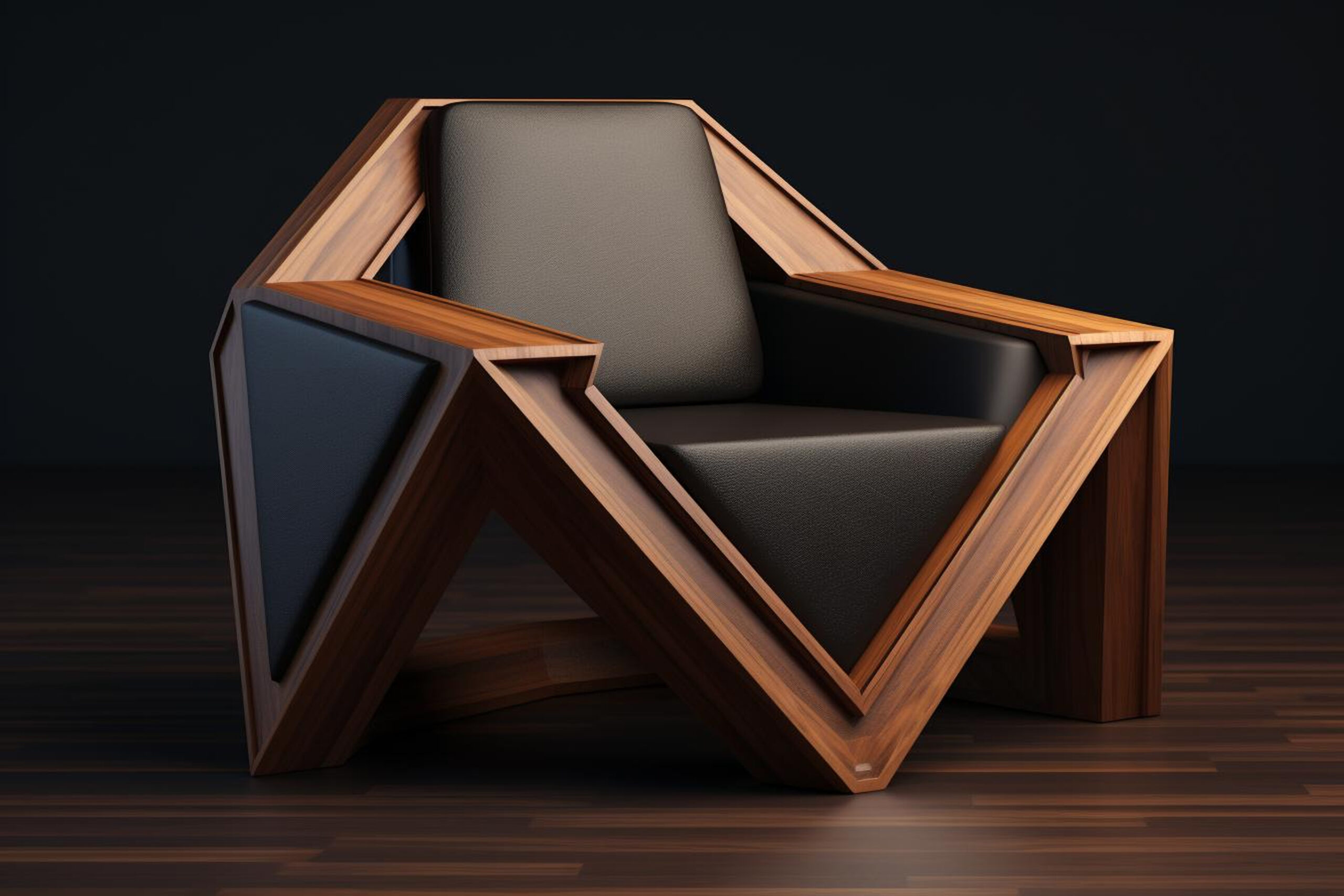
Start with a “Tekcel CNC” for the best finish…
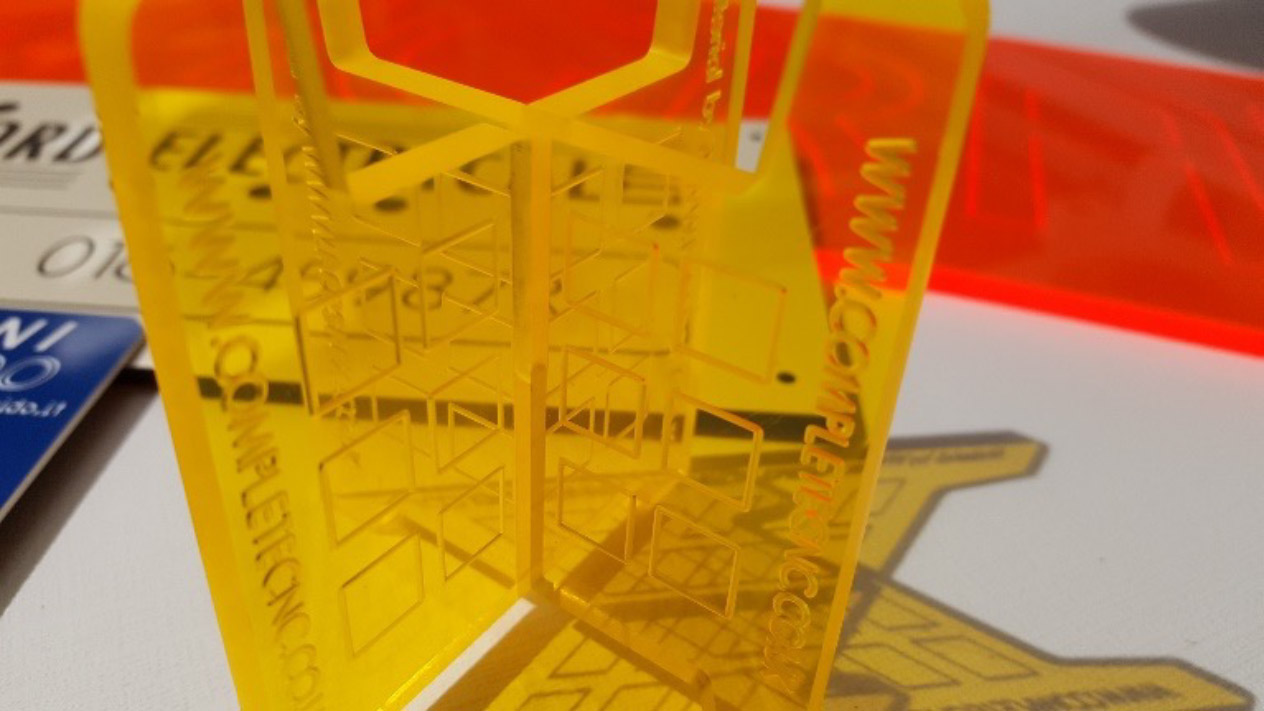
Under the Bonnet of a Tekcel EXR CNC Router
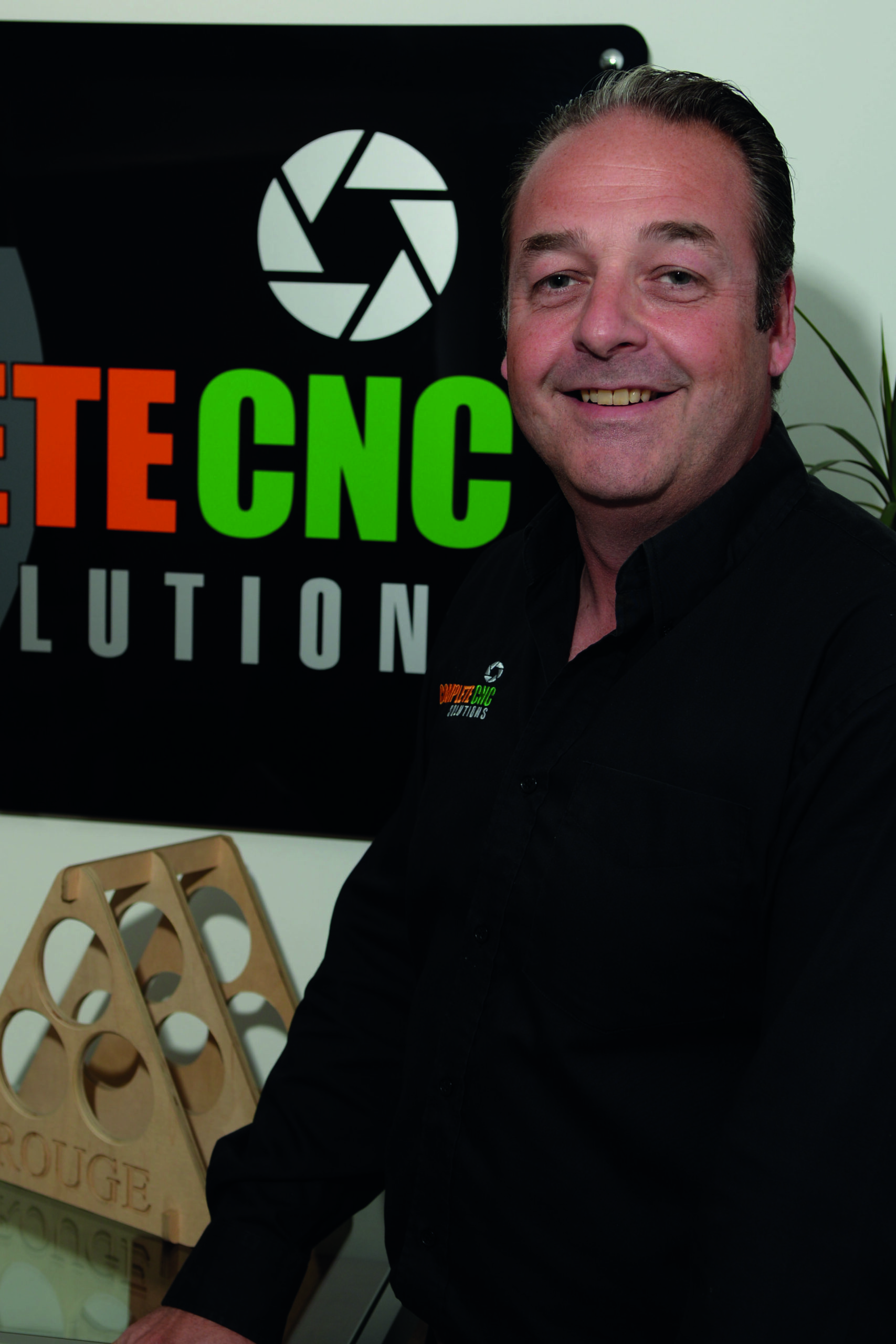
How to Skim the MDF Sacrificial Bed on your Tekcel CNC Router: A Step-by-Step Guide
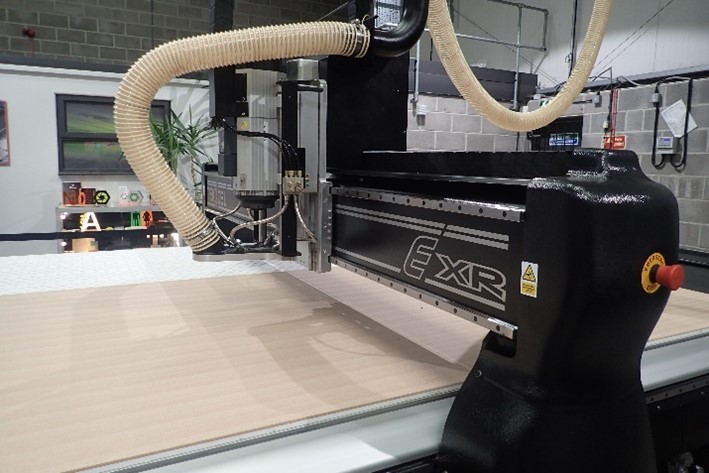
What is an ATC and why do I need one?
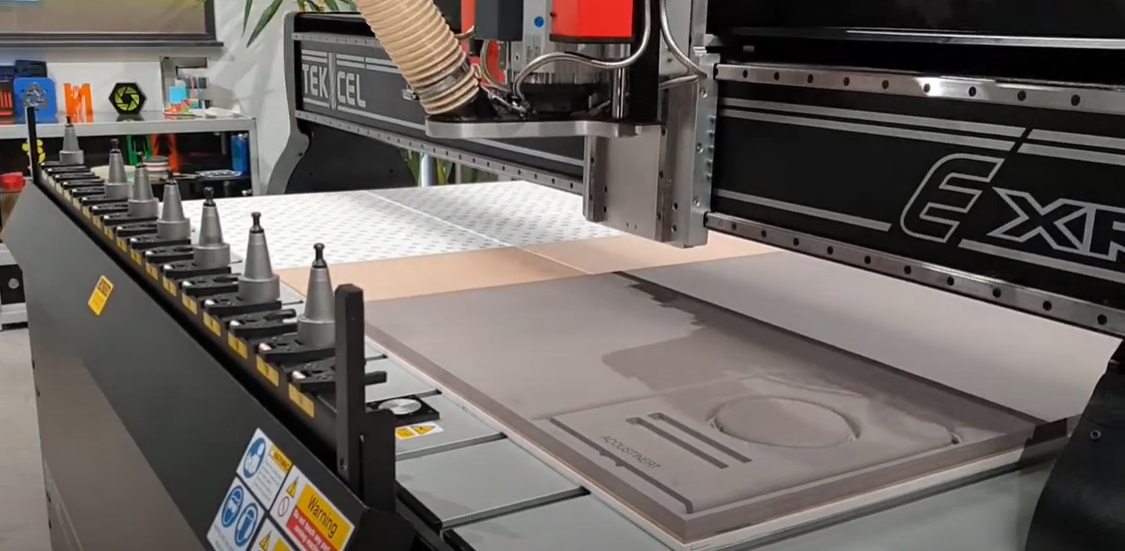
Tekcel CNC for ACM (Aluminium Composite Material) Signage:
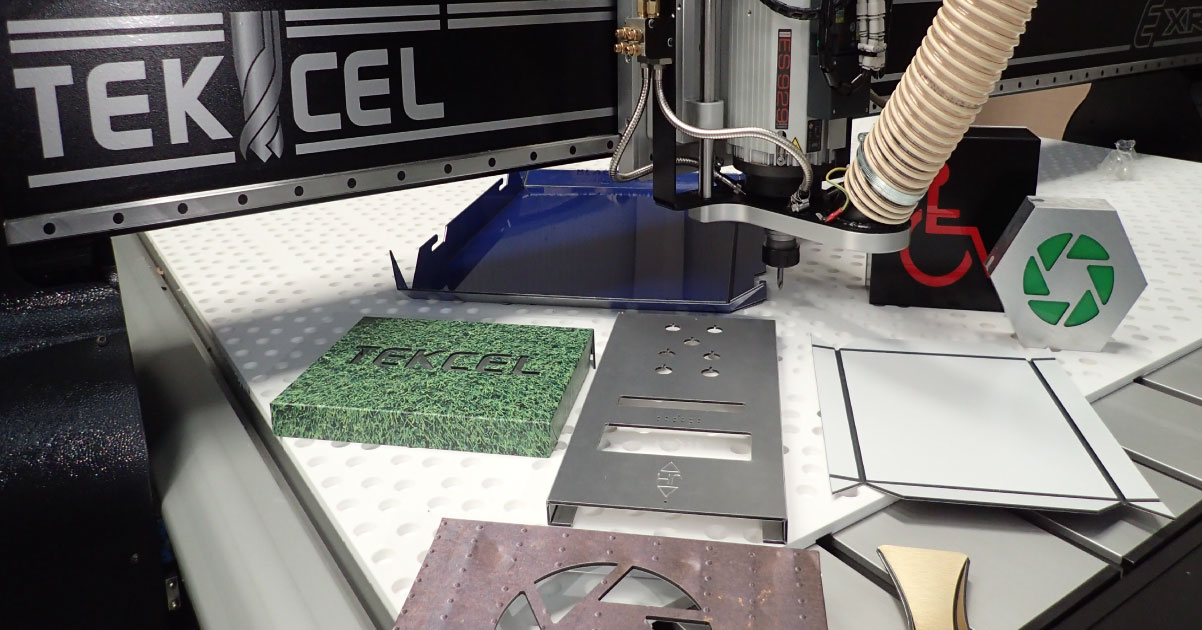
The Benefits of Acrylic
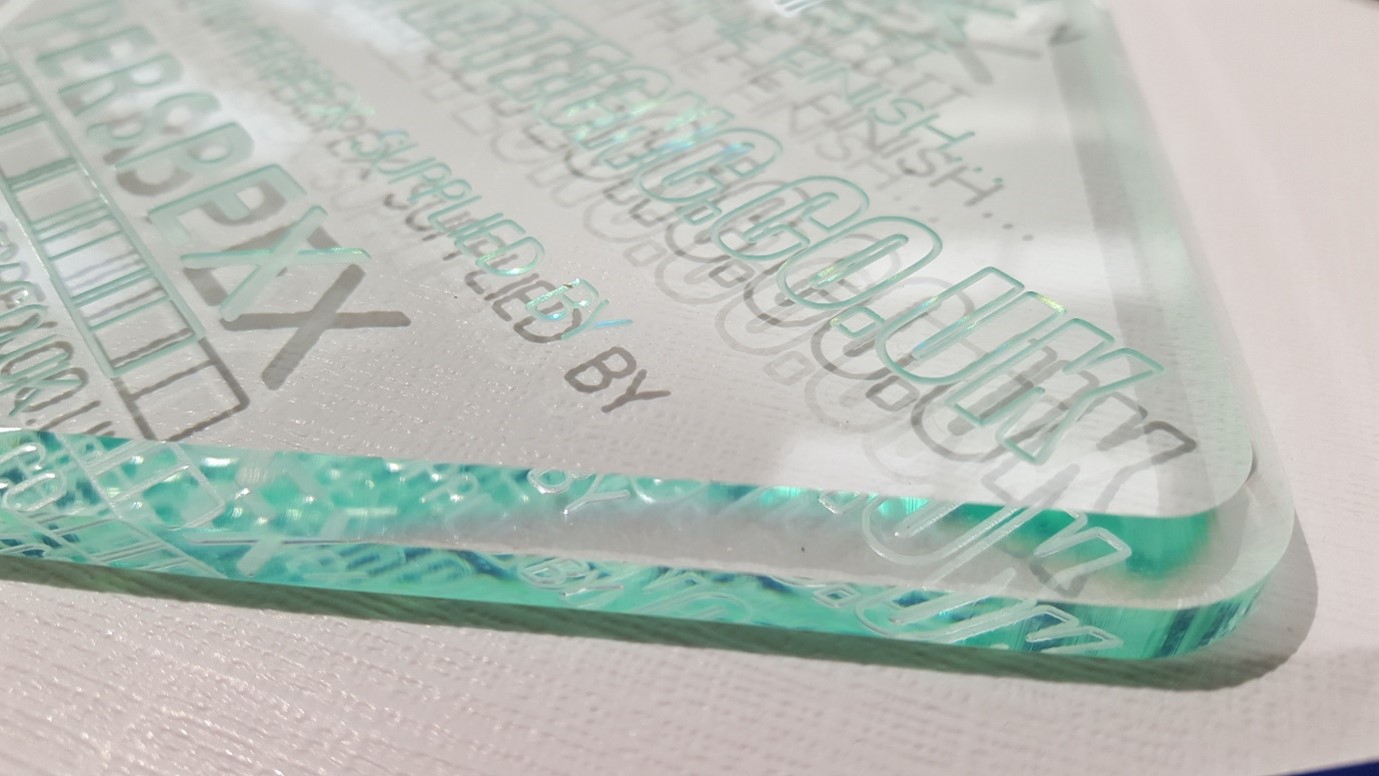
CNC for DFM
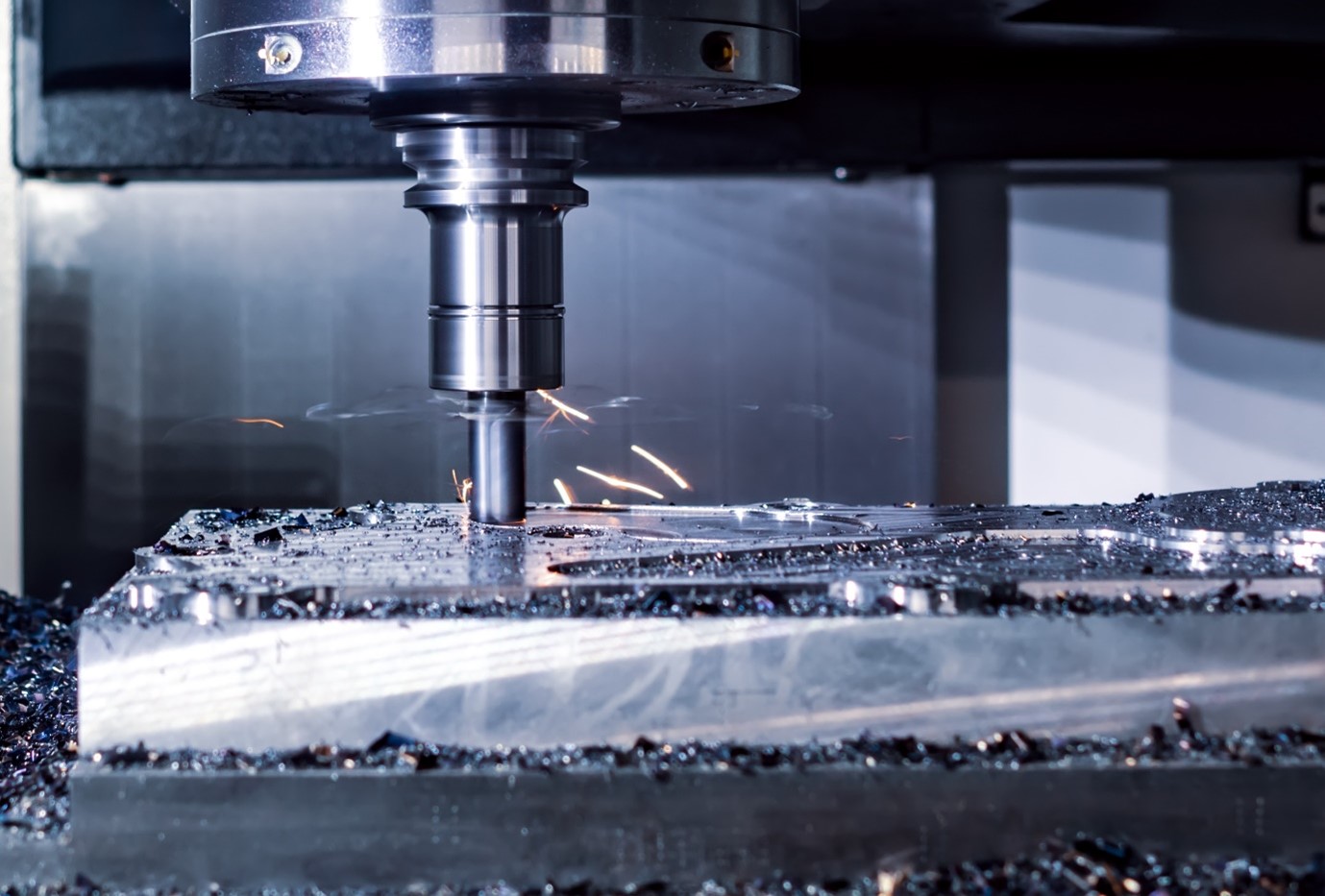
The Unbreakable Rules!
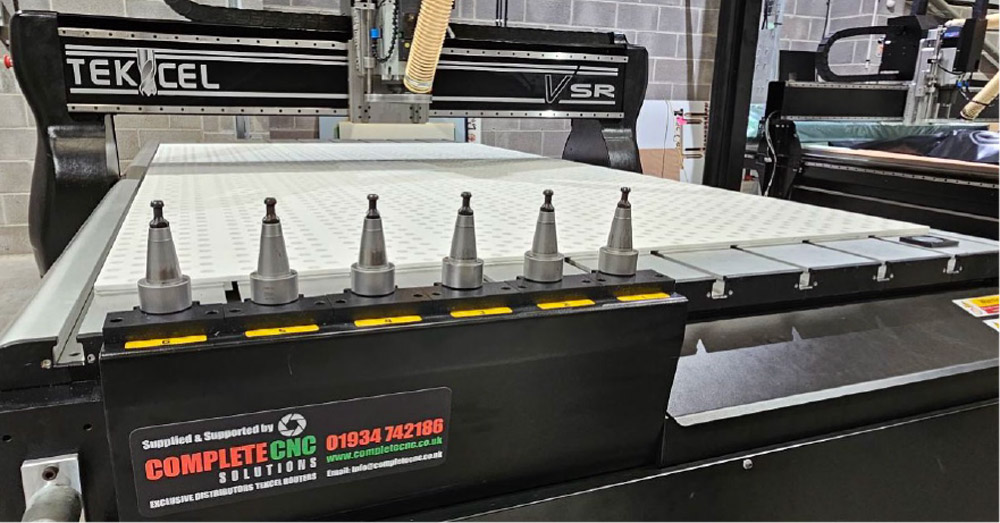
Welcome to the world of CAD/CAM
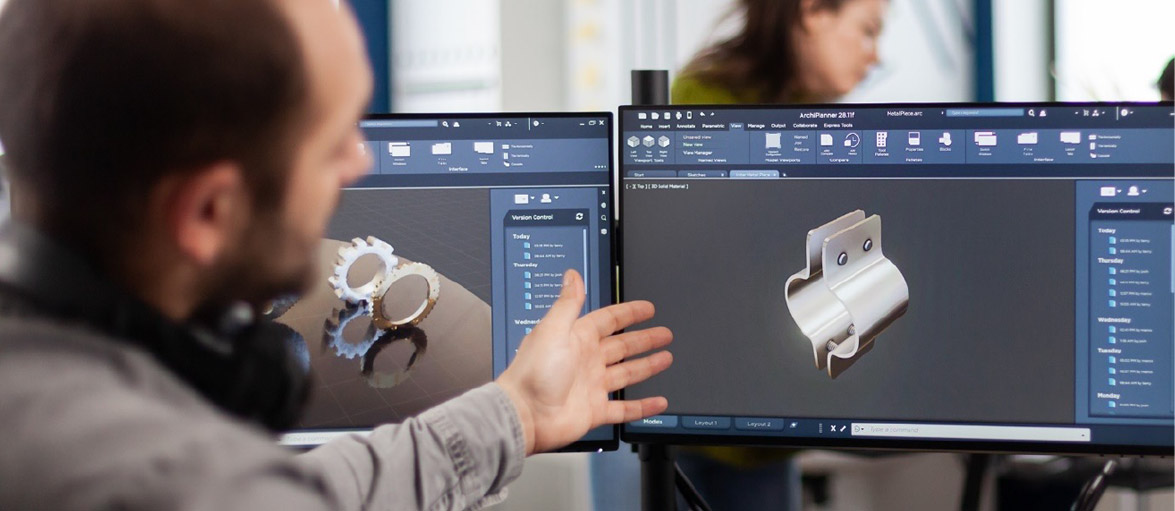
10 Tips for Successful Aluminium Cutting with CNC Routers
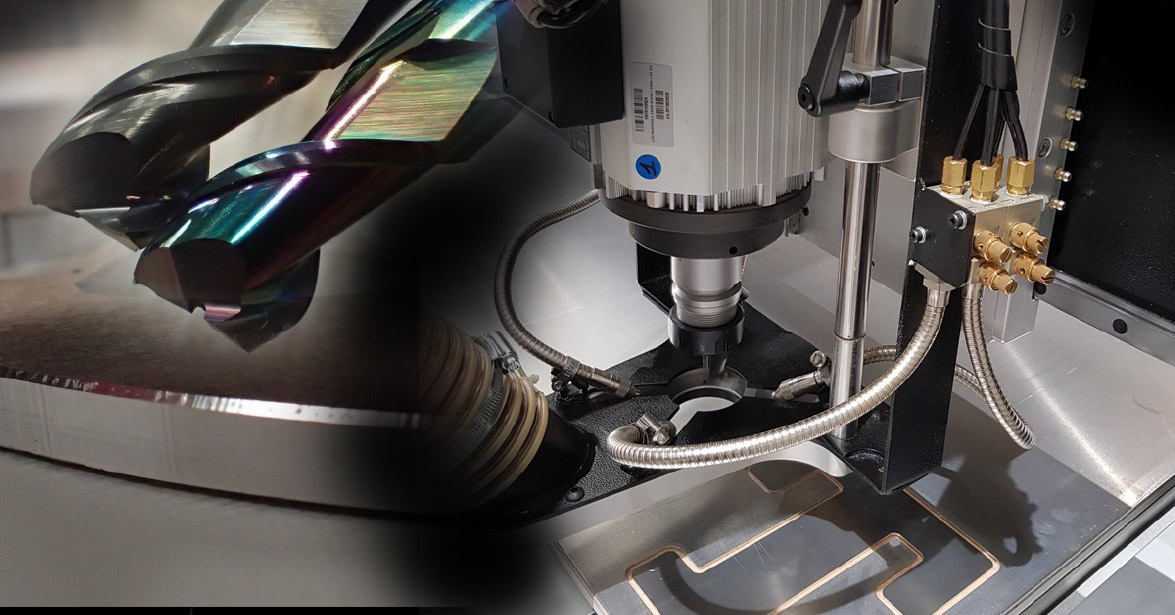
Mastering the Art of Tekcel CNC Router Speeds and Feeds: A Comprehensive Guide
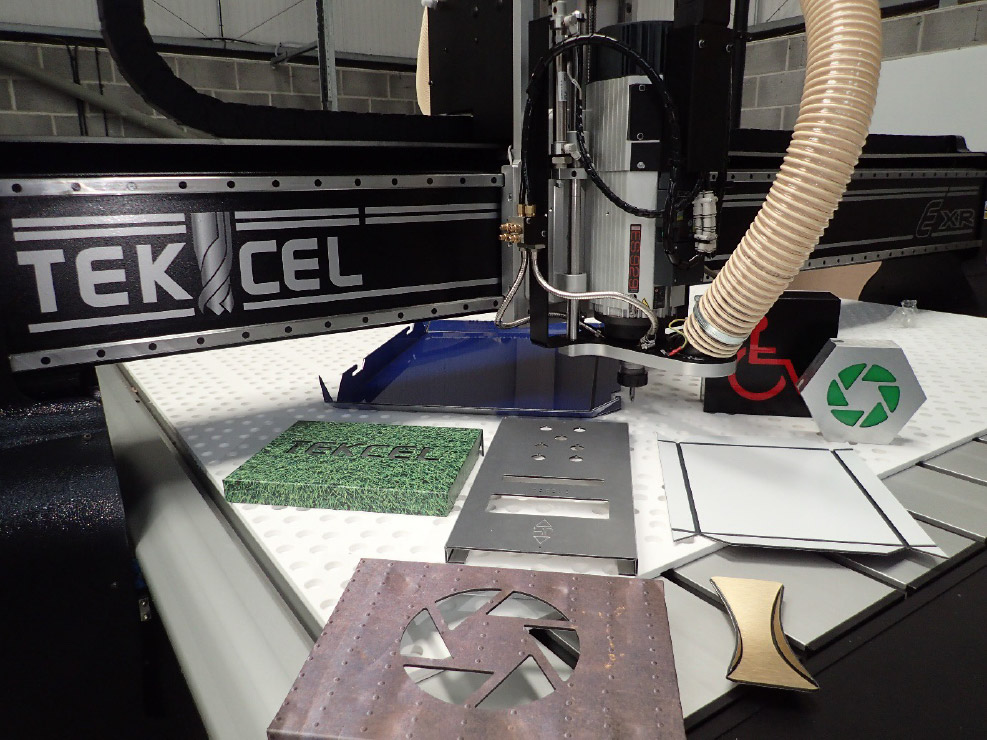
CNC Routers For Sign Making
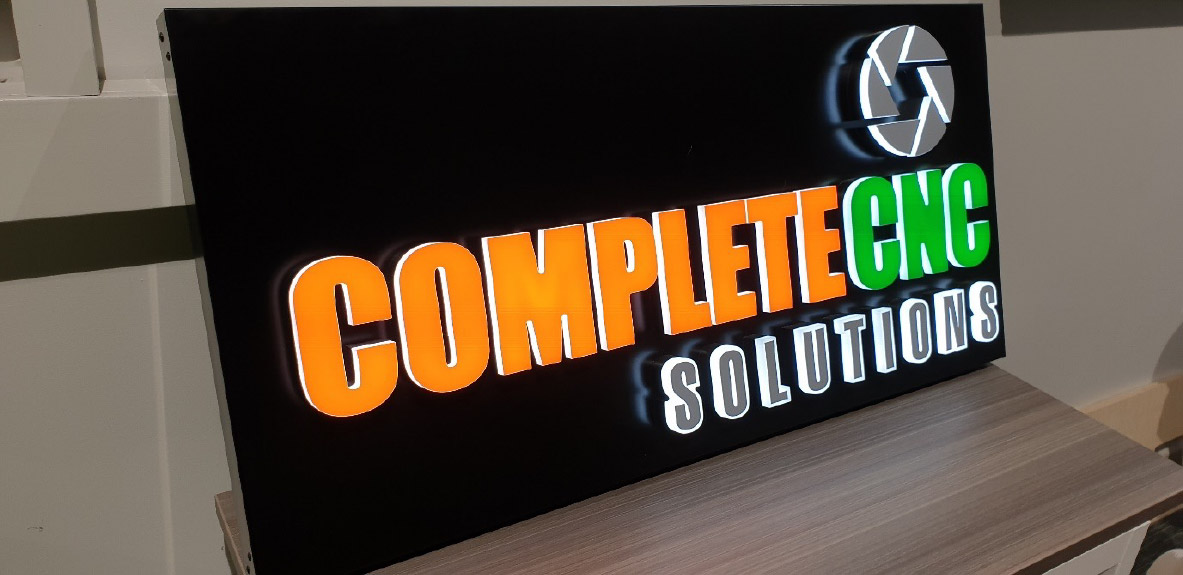
Cutting Acrylic With Your CNC Router
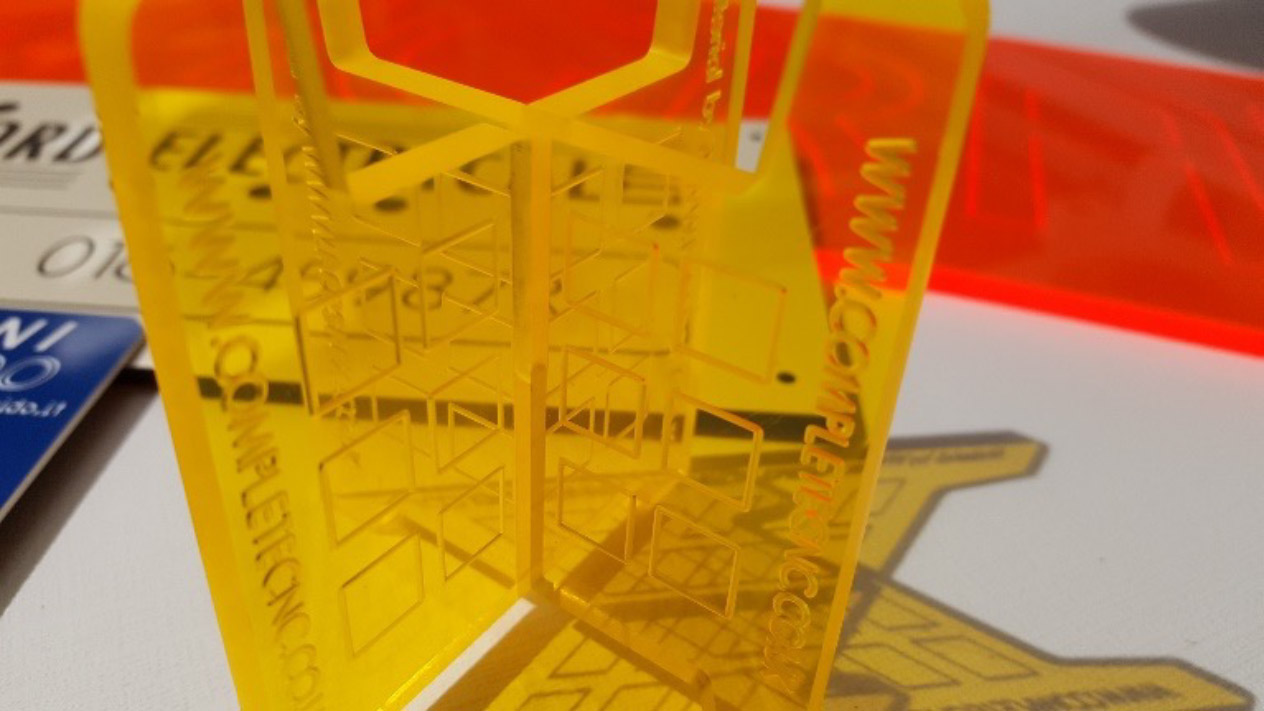
Collets: An Essential Tool
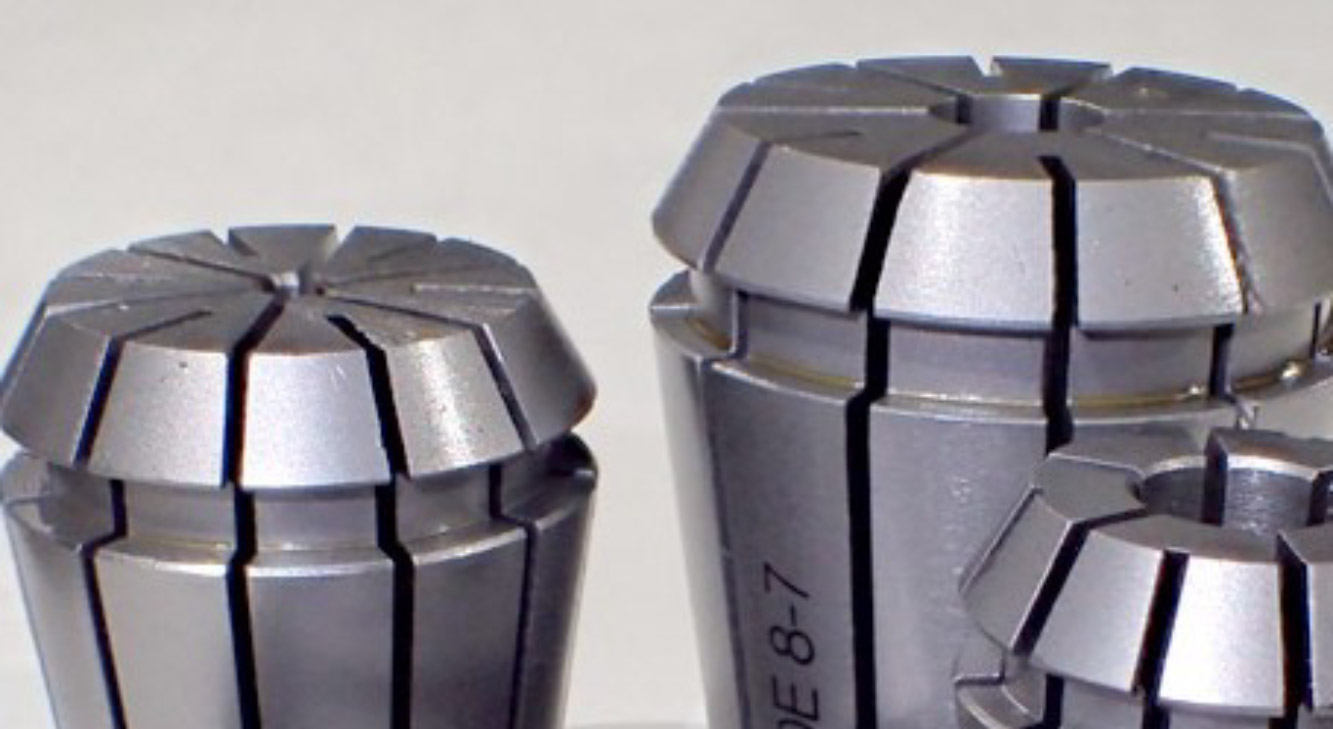
Calling all converters: How CNC Routers Elevate Vehicle Conversions
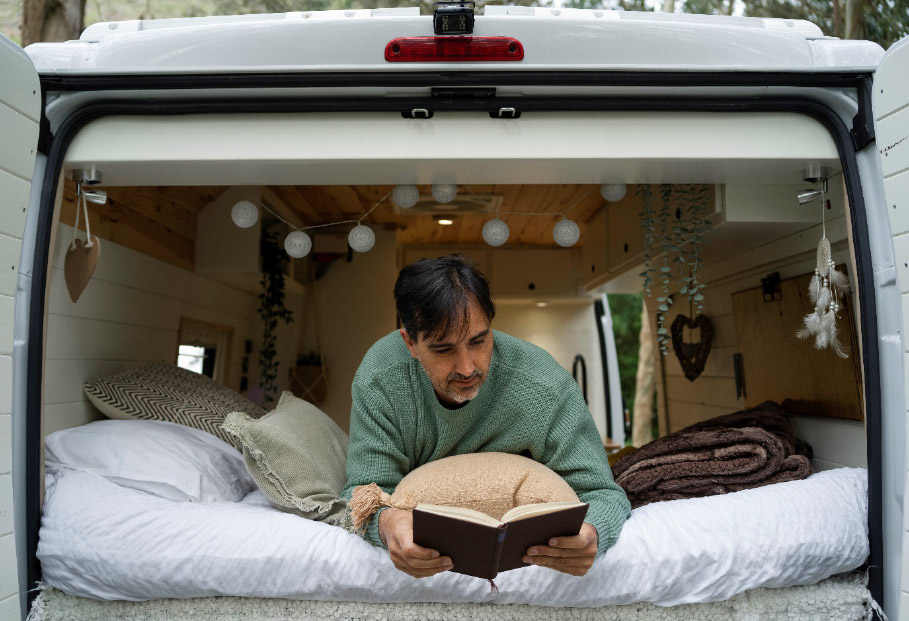
The Right tool for the job
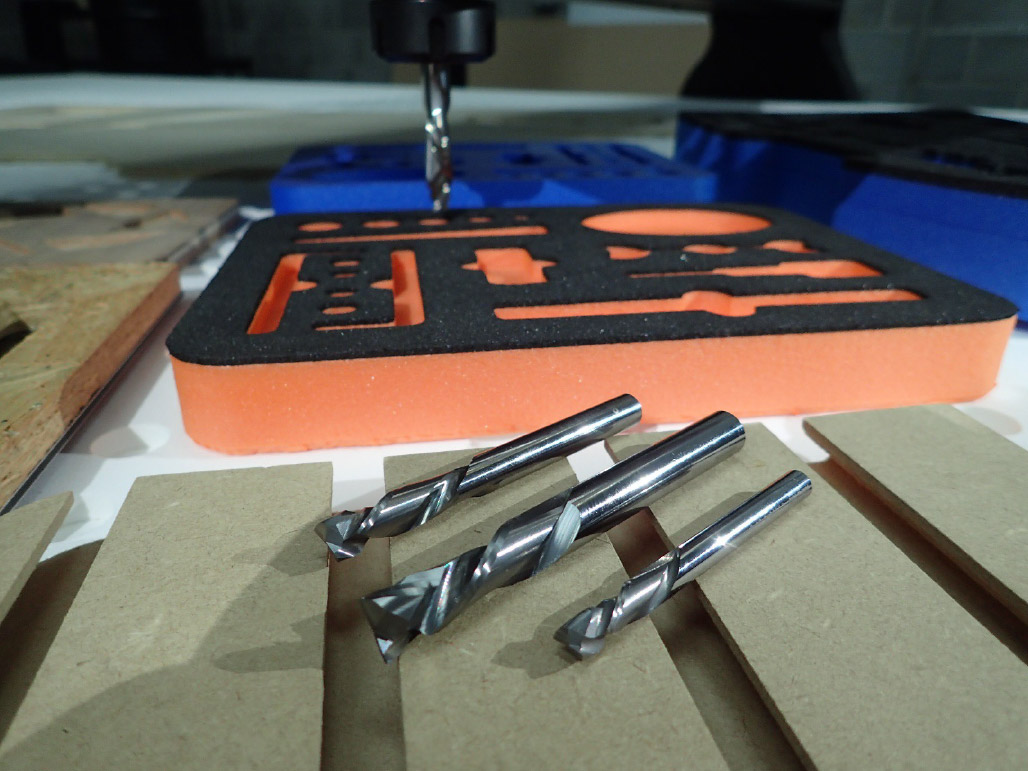
What is the cutting speed of a CNC router?
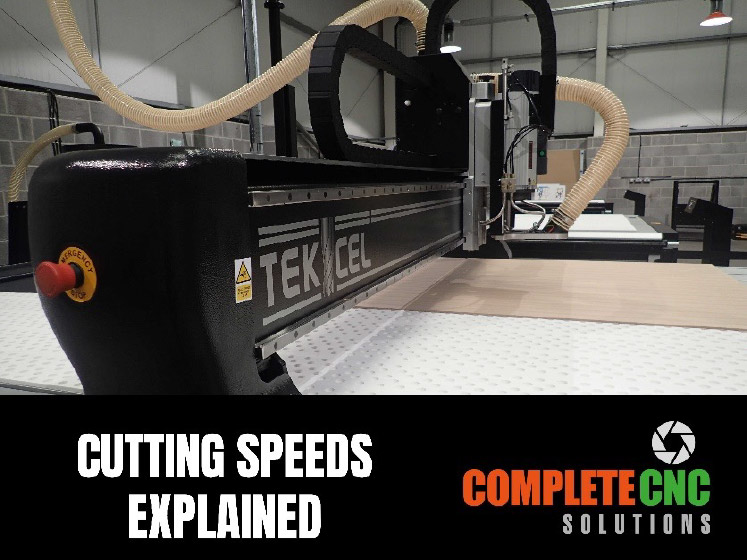
Unravelling the Mystery: Common themes overlooked with CNC Routers
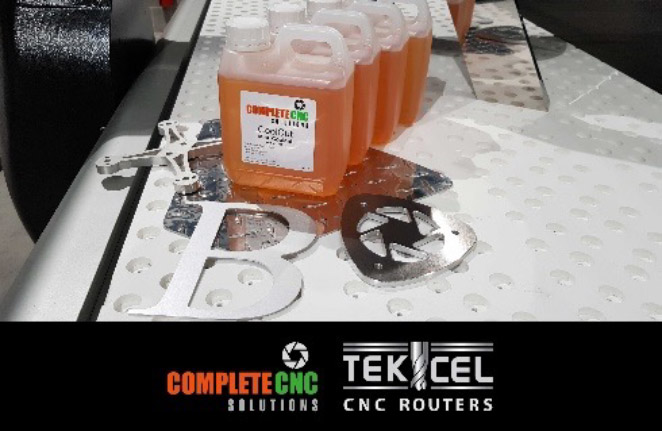
CNC Router Maintenance Guide for Longevity and Efficiency
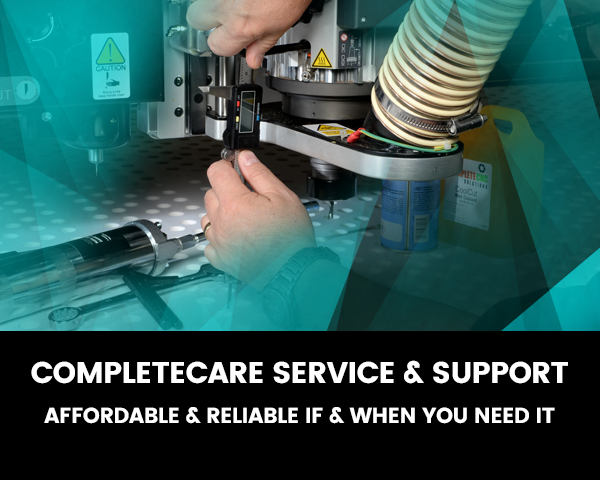
Tekcel Graphical User Interface
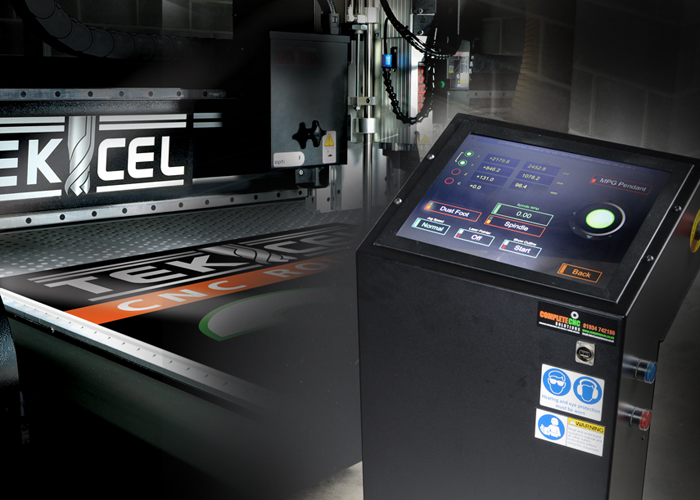
Unlock the World of Carving with CNC Routers!
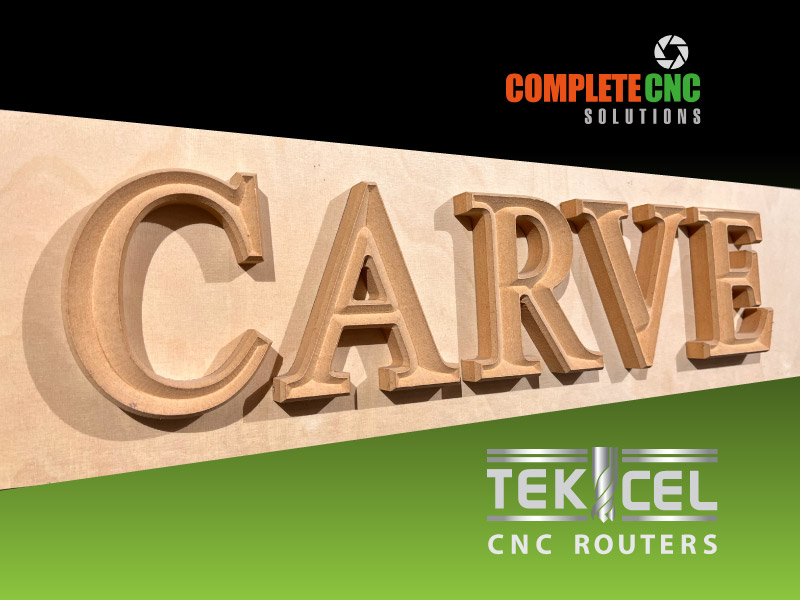
Can a CNC Router Carve Intricate Details? Yes!
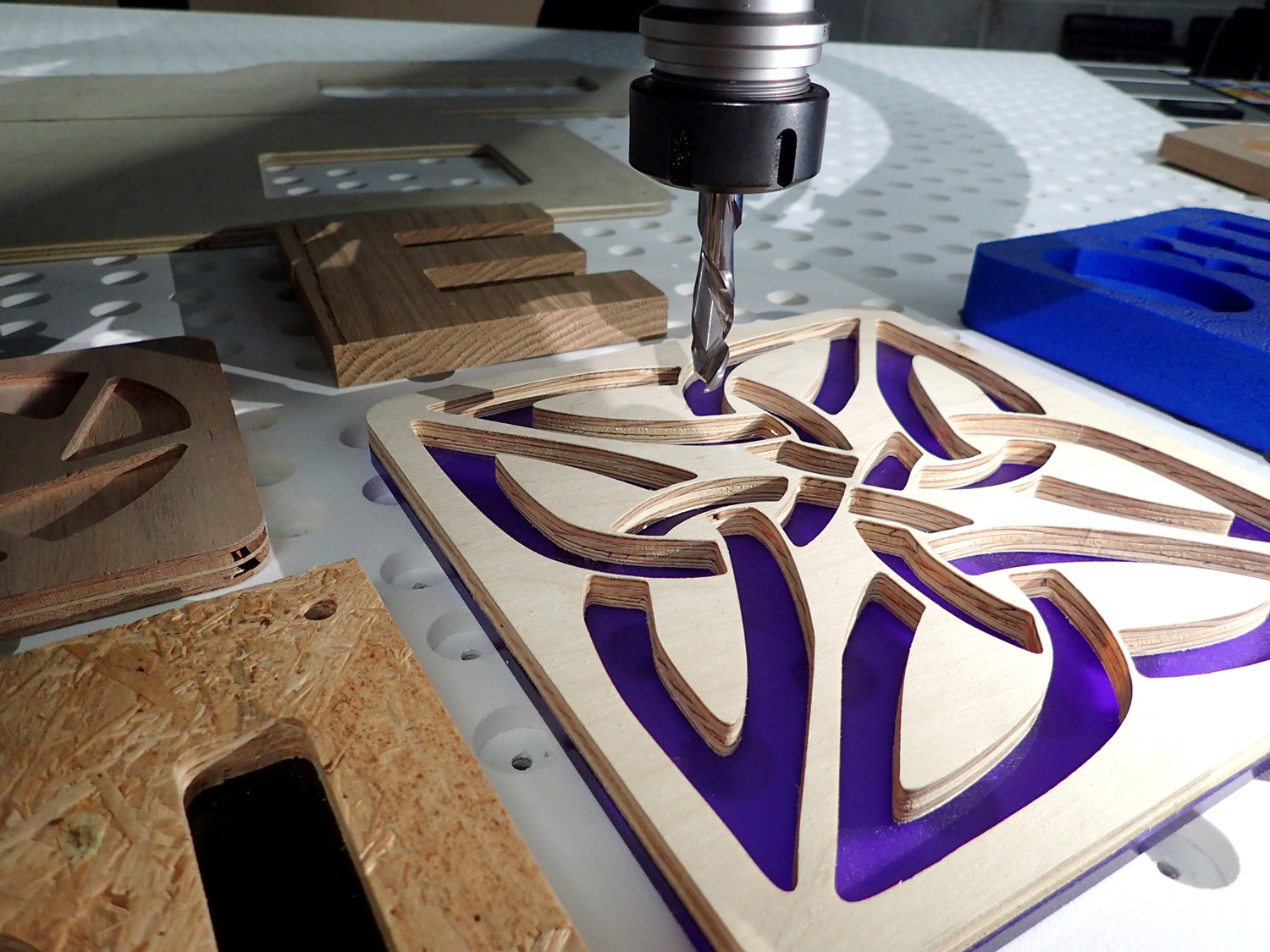
How a Tekcel CNC machine can provide value for your business
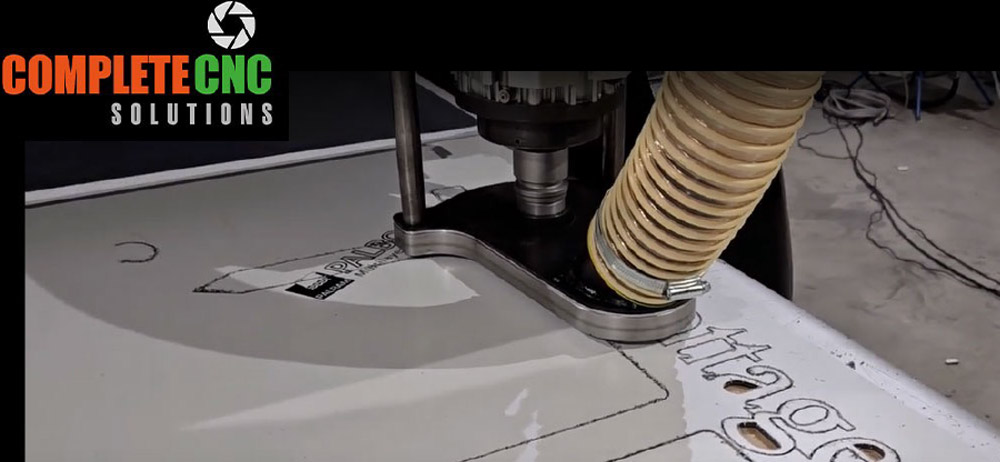
Elevating Point of Sale Production with CNC Machines
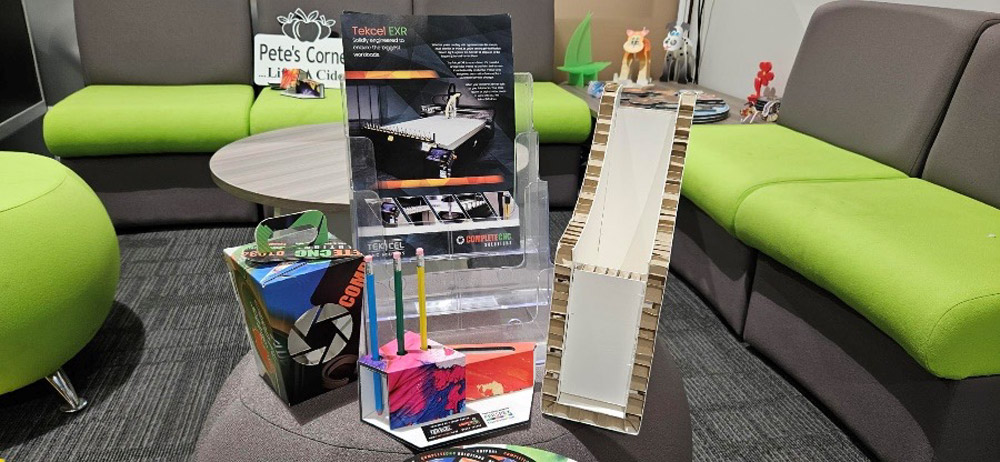
Why Sign Makers are Upgrading to CNC Cutting Machines
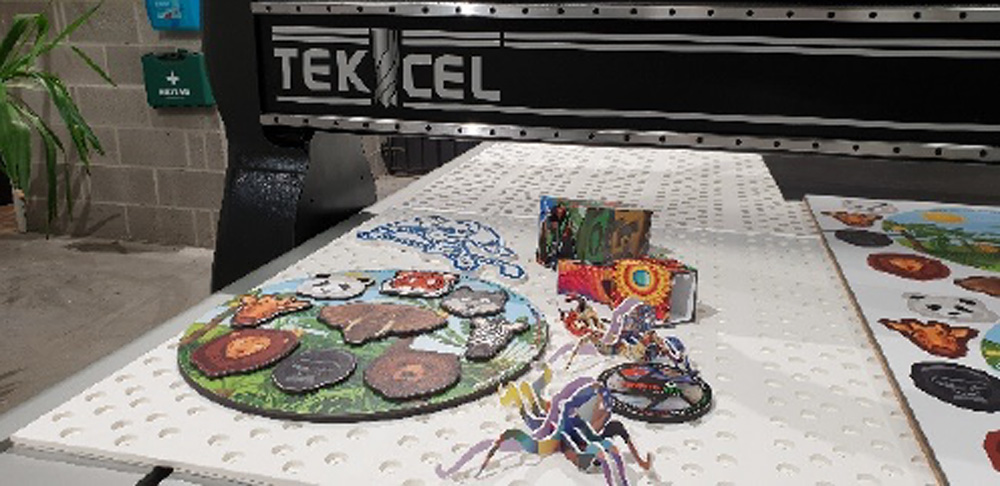
Hibernating Your CNC System During Lockdown.
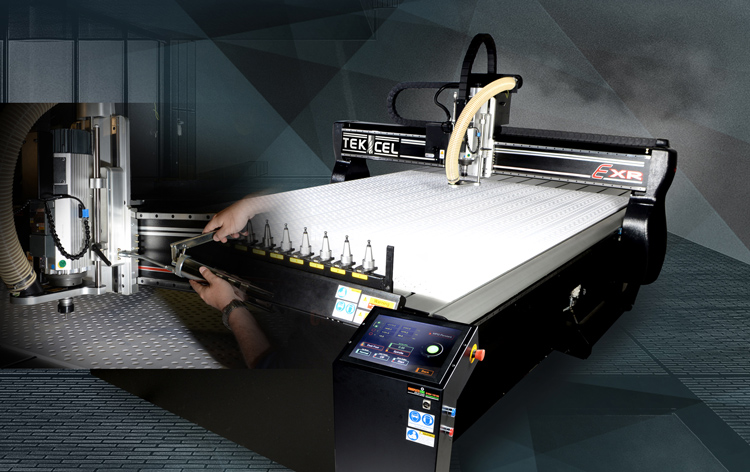
START BIG. GET BIGGER.
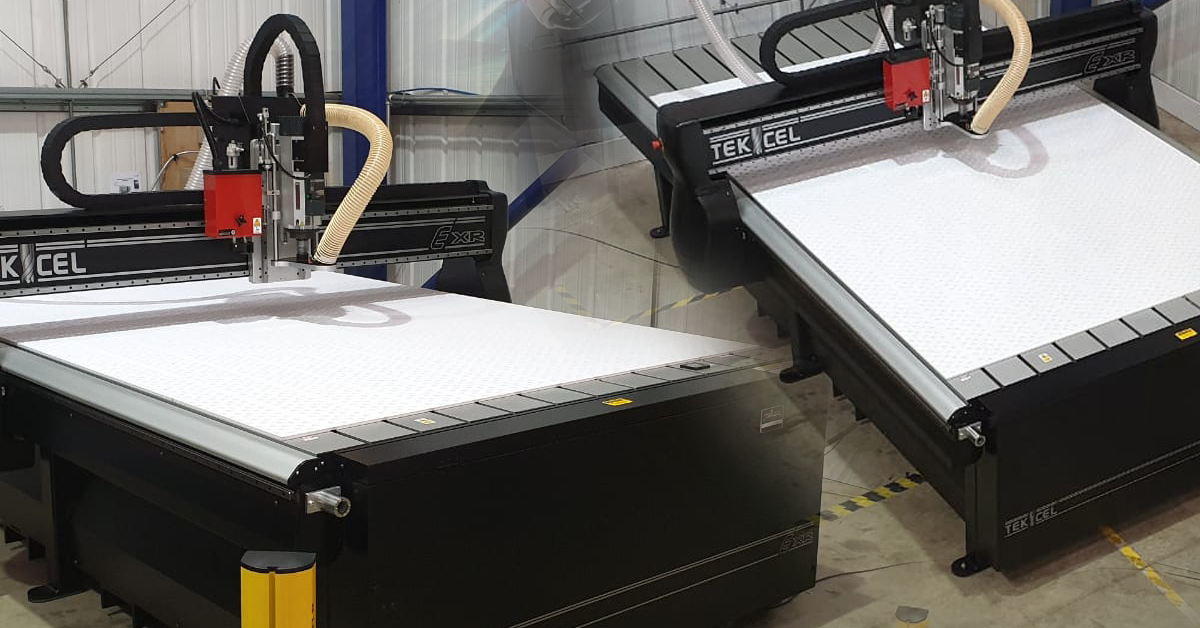
START WITH THE FINISH. FINISH WITH A PROFIT.
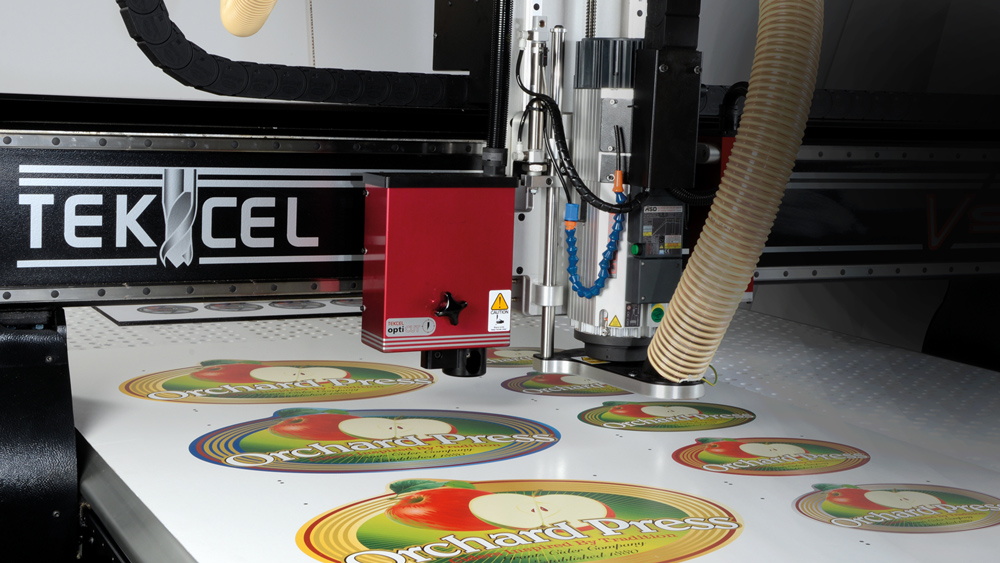
HEAVY METAL. LIGHT WORK.
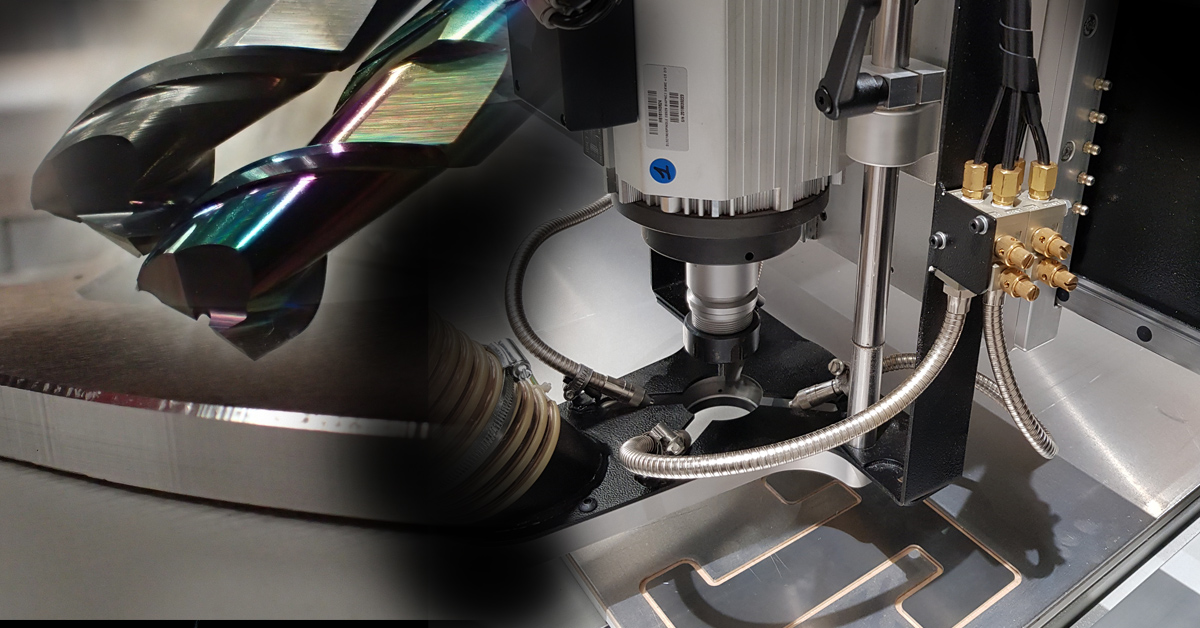
MAKE MORE WITH CORREX
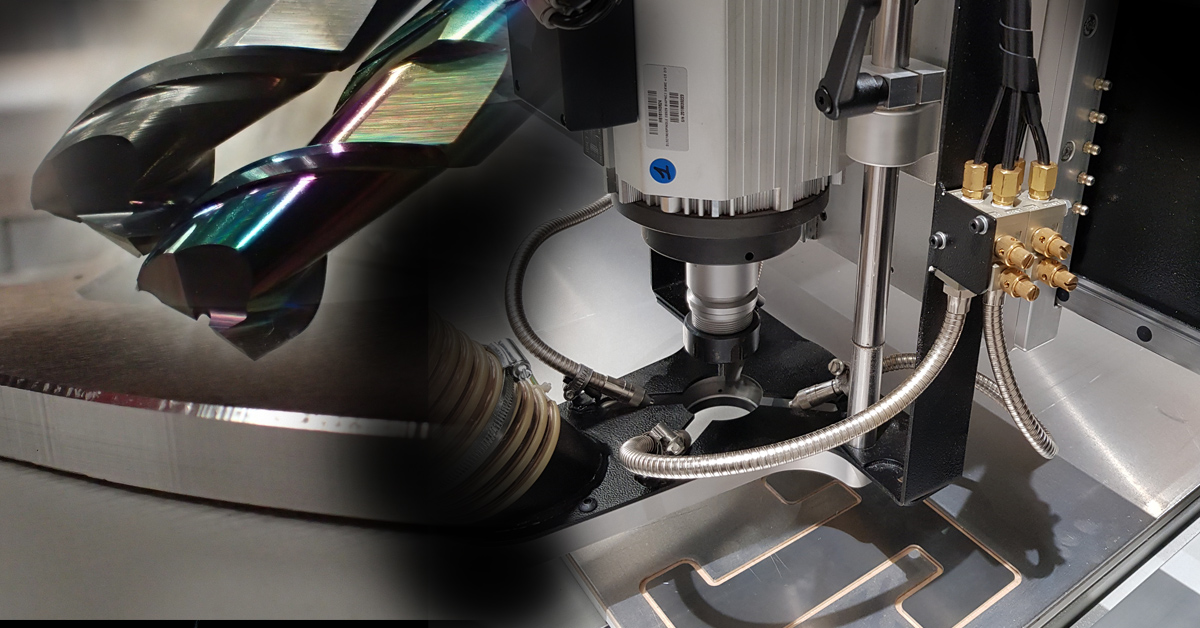
HOW SHOULD I APPROACH CUTTING OF SOLID SURFACE MATERIALS, CORIAN, AVONITE, THAT KIND OF THING?
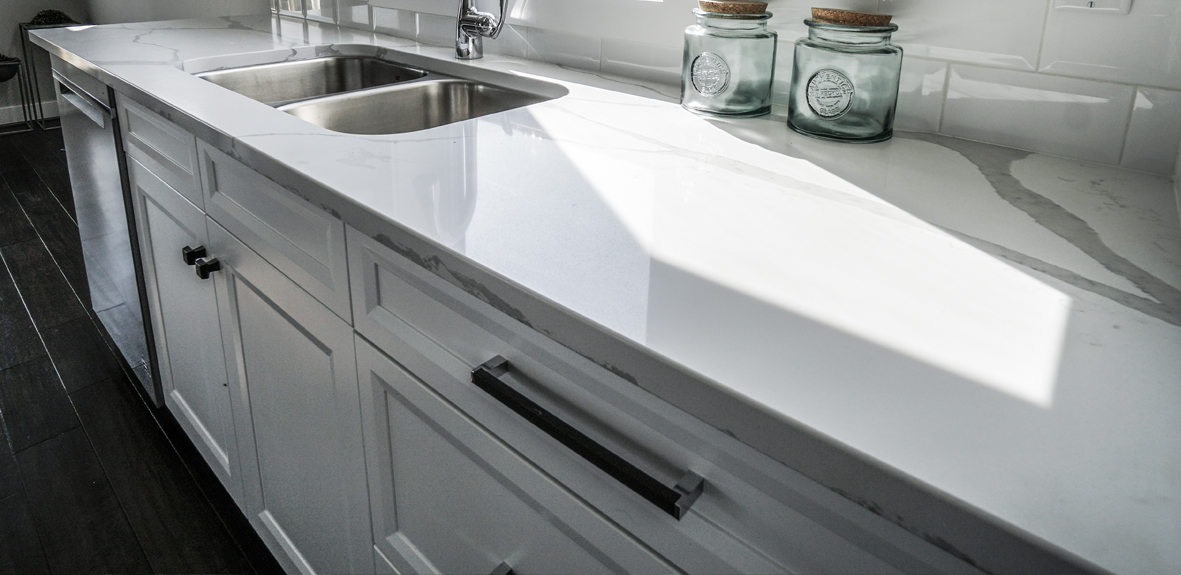
Achieving good results when you’re routing Woods, MDF, Laminates or Ply

HOW DO I GET THE BEST RESULTS POSSIBLE WHEN I’M CUTTING ACM ON MY CNC ROUTER?
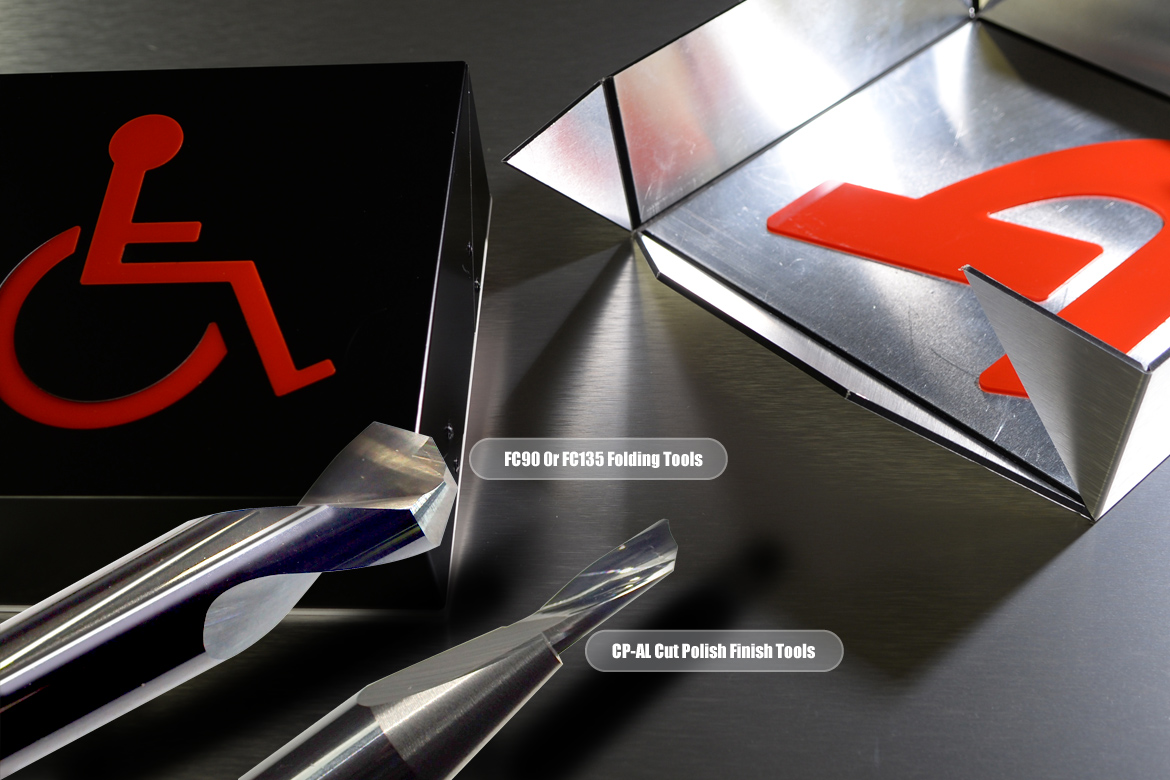
HOW CAN I GROW MY SIGNAGE AND GRAPHICS BUSINESS?
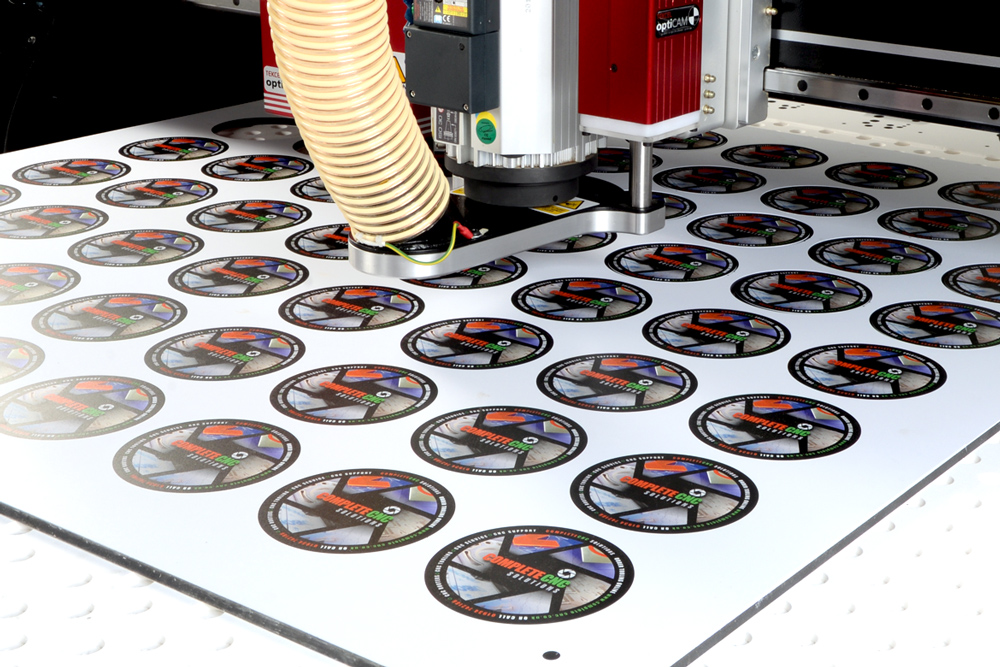
HOW CAN I REDUCE THE TIME I SPEND POLISHING THE EDGE ON THE OUTPUT FROM MY CNC ROUTER?
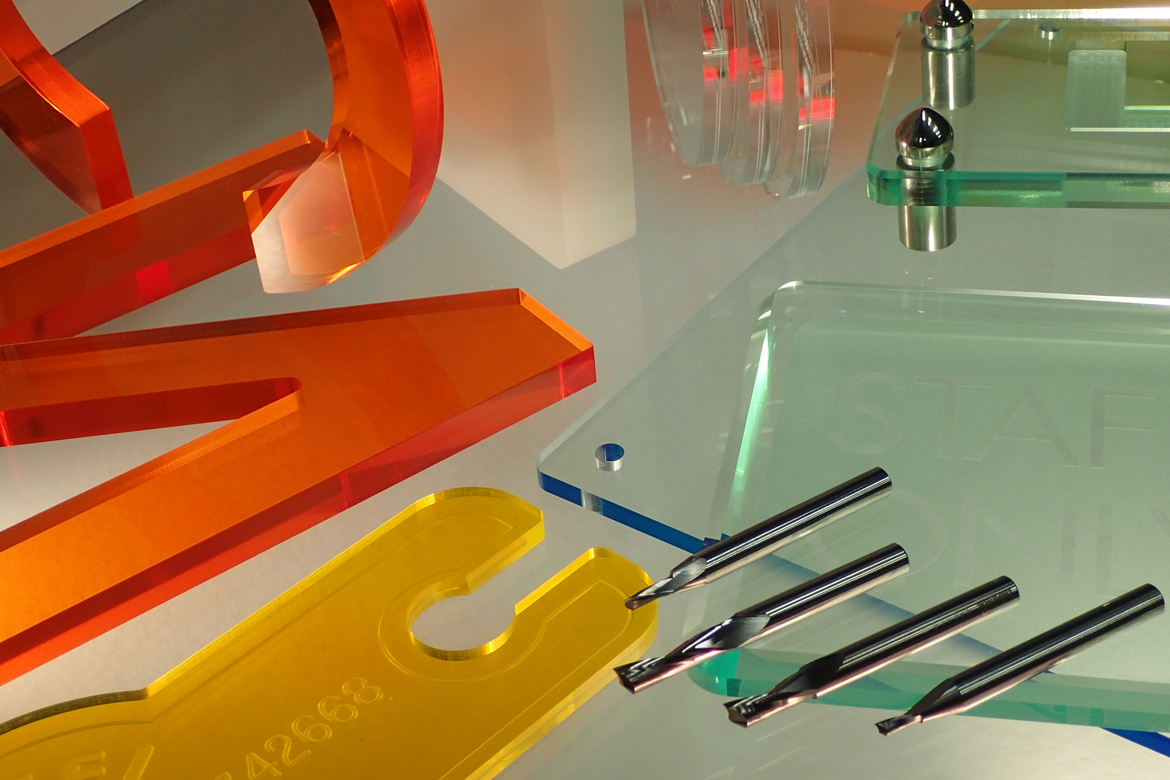
THE FLATTER THE BETTER
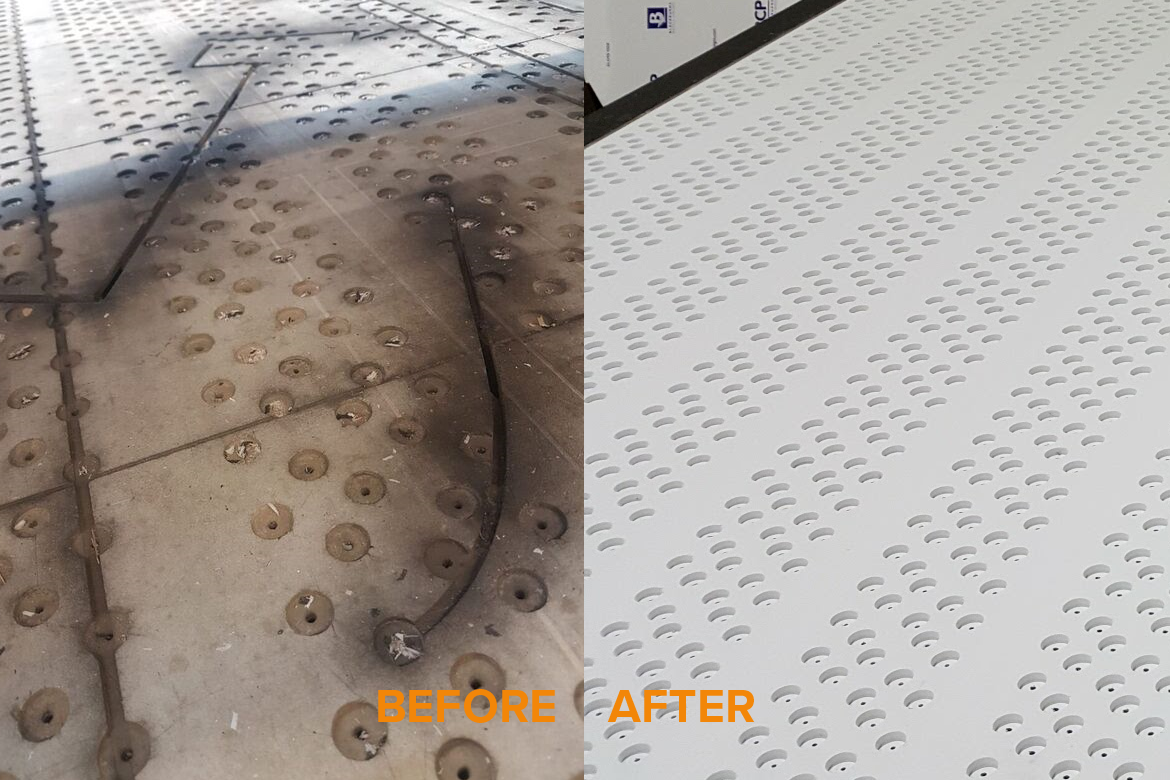
IS MY BUSINESS READY TO BUY A CNC ROUTER?
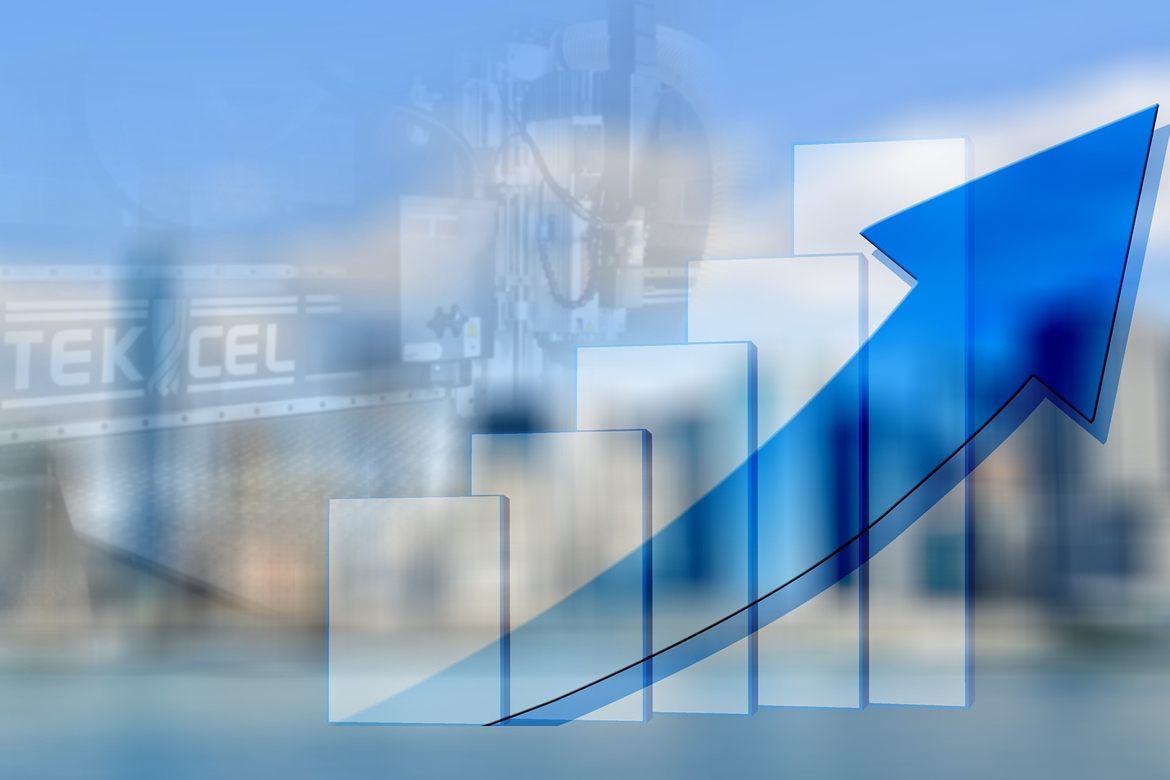
HEARD AT A TRADE SHOW
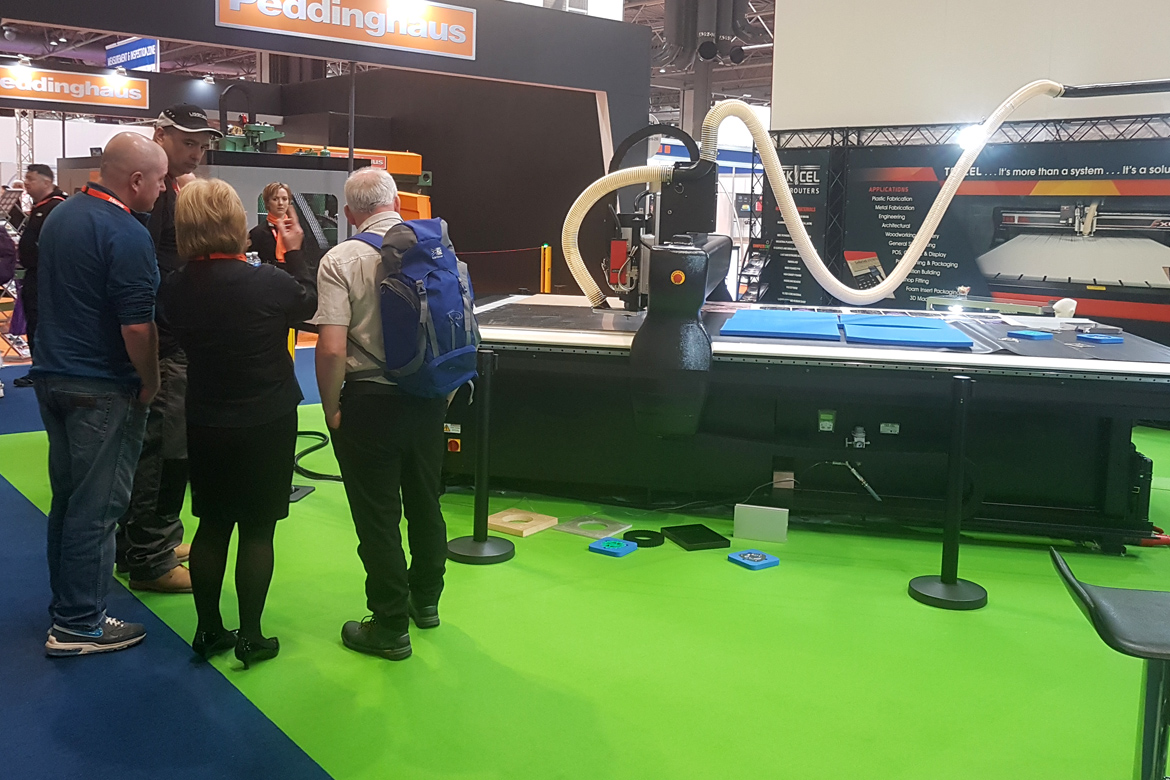
THE IMPORTANCE OF CHANGING CNC ROUTER COLLETS REGULARLY
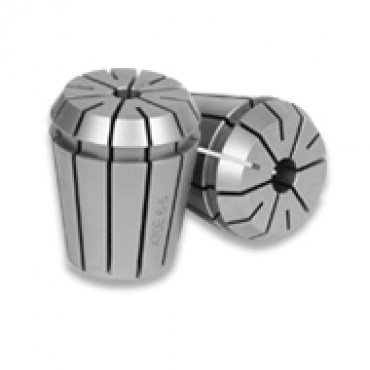
WITH YOU ALL THE WAY
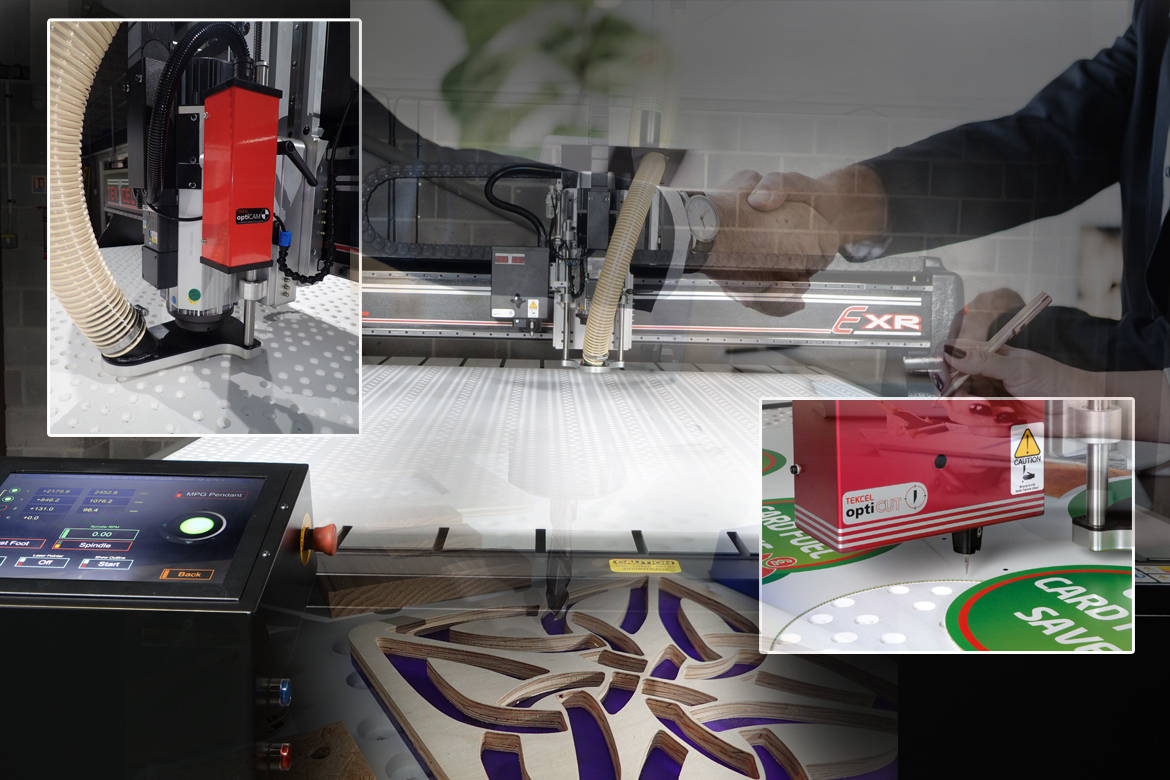